Visibility and automation: reducing disruption due to temperature excursions
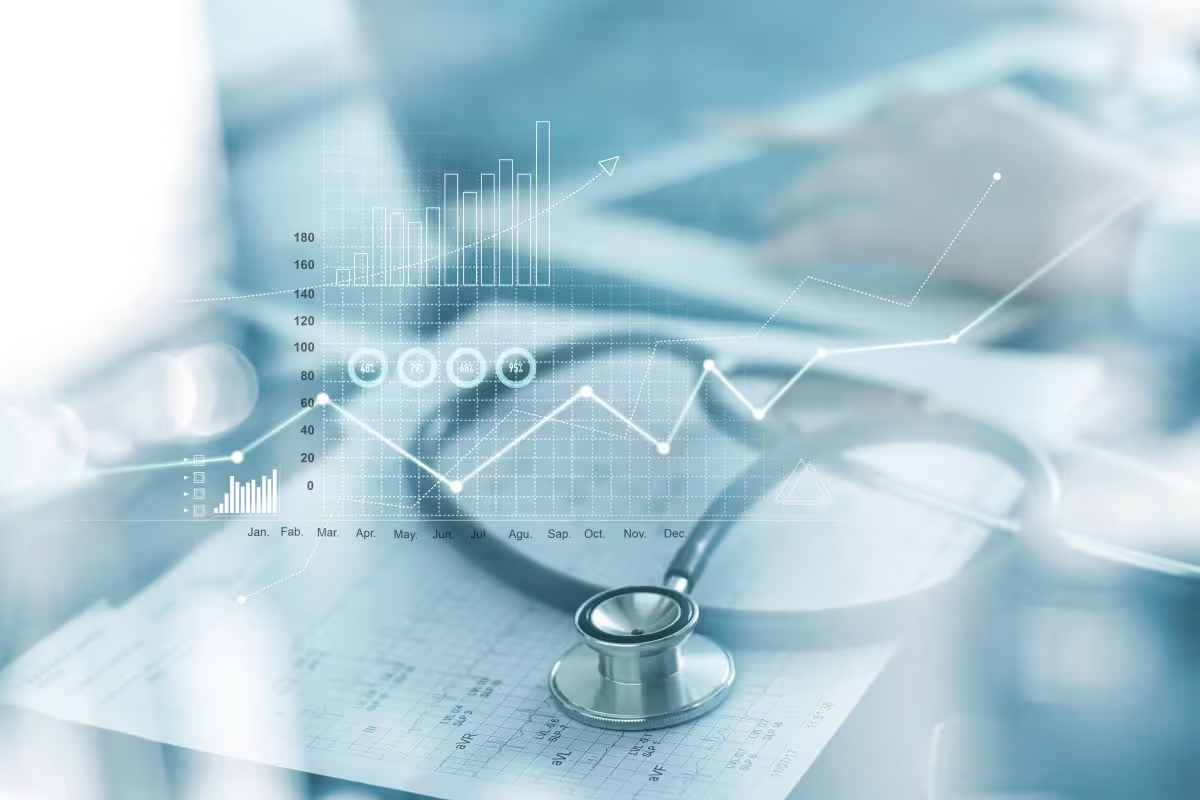
Visibility and Automation
For sponsors looking to improve operational efficiency, current industry practices for temperature monitoring create several potential sources of temperature excursion. The need to collect data manually for shipments, can lead to data gaps throughout the temperature monitoring process and additional site burden, taking up valuable time and introducing the risk of human error.
Digital solutions can remove these issues by providing supply chain professionals with an automated stream of accurate temperature data throughout the cold chain. In a clinical environment where every minute counts, there is considerable value in just reducing the time spent on temperature monitoring by clinical and sponsor staff. But there is even more value in being able to take preventative action quickly if problems do arise.
Here are some of the ways digital solutions can eliminate manual efforts, ensure safe dispensation of treatments, and enable seamless clinical operations.
Automation - Simplifying excursion processes
More than 90% of temperature excursions do not result in a deviation that requires treatments to be wasted. But with time-consuming manual interventions these still need to be investigated. Automating the process can lead to huge reductions in workload. While manual processes will usually prevent a patient being given a drug that has experienced a temperature deviation, automated evaluation of excursions present the same compliance while removing the workload from the study team and providing real-time decisions.
Visibility - Seeing the whole picture
Data gaps can mean temperature excursions are not detected until a shipment reaches its final destination. In turn, this can create delays in ordering replacement shipments, leading to wasted clinical time, frustrated trial participants and increased costs.
Digital temperature monitoring solutions can provide visibility at every point of the process, giving clinical study teams notifications if an excursion occurs. This means they can begin managing the process of re-ordering, re-shipping, and re-scheduling immediately rather than hours or potentially days later, minimizing disruption and maximizing efficiency. This is especially important for direct-to-patient studies, where sponsors need to show that individual items were in a safe temperature range when they were delivered.
Reporting - Turning raw data into information
Having quick and easy access to baseline reporting with data presented in simple dashboards helps operators see data in a centrally organized way. This makes it much simpler for them to run the trial effectively and demonstrate its compliance, but also helps reduce the workload associated with the manual review process. Typically, a site will receive data on shipping or storage timeframes, but the data sets are not connected to one another. These connection points have to be created manually. Digital systems automate this process of data review and aggregation, presenting teams with the data they want in a format that is easy to digest. Whereas detecting, logging and dealing with an excursion that did not result in a deviation could take hours or days with attritional manual process, through digital systems the event is recorded, and operators notified within seconds.
.jpeg)
Integration - Seamless exchange of data between clinical systems
Digital solutions also offer another important benefit: flexibility. Traditional temperature monitoring methods do not offer operators much choice in how it is performed. Digital solutions on the other hand, can be adapted and tailored to fit the needs of specific operators or clinical environments and integrated with their IRT seamlessly. They also offer interpretability with other systems, breaking down silos and allowing the seamless exchange of data. Working closely with clients, we have been able to show the enormous benefits customized solutions can deliver for operators. By using data that originates from one source and flows through several other systems without the need for manual intervention, the workload of teams is reduced even further. Most importantly, the risk of dispensing unsafe treatments in greatly reduced because of the automated quarantine in the IRT.
Our solution can establish whether a temperature deviation has occurred and notify users within seconds, helping to reduce failed patient visits and dropouts. Almost instantly, operators can see exactly how delays will impact the other steps in their trial, so that they can make more informed decisions to mitigate any impacts.
You can find out more about how digital solutions are taking the average excursion management process from days to seconds and reducing site burden by listening to our cold chain distribution webinar. Watch on-demand today:
You may also be interested in
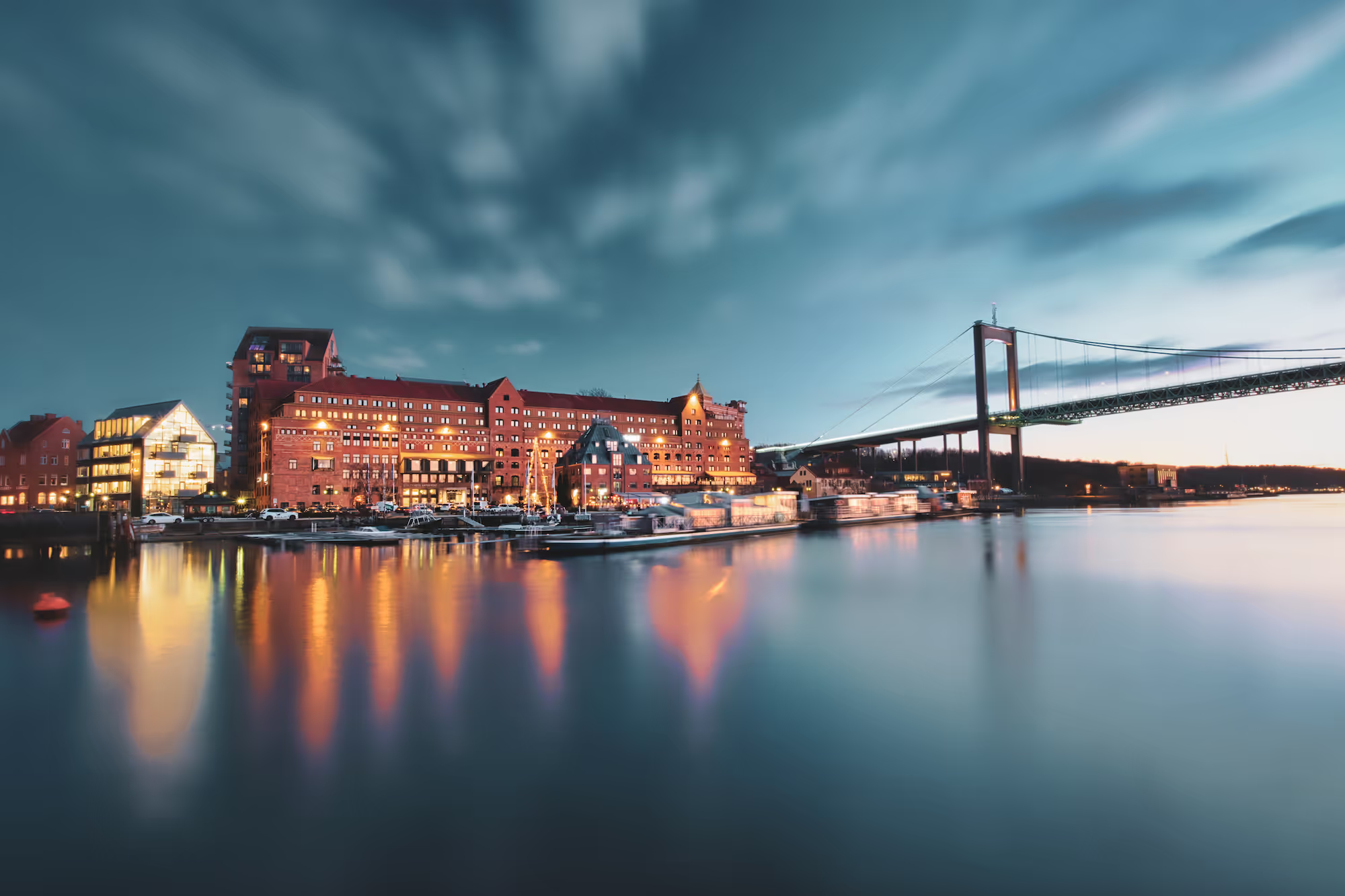
TSS User Forum 2023
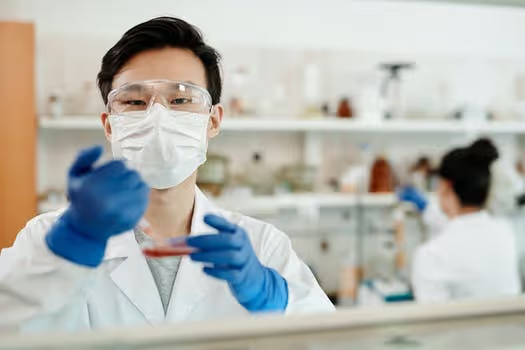
On-demand webinar: Excursion Management – From days to seconds
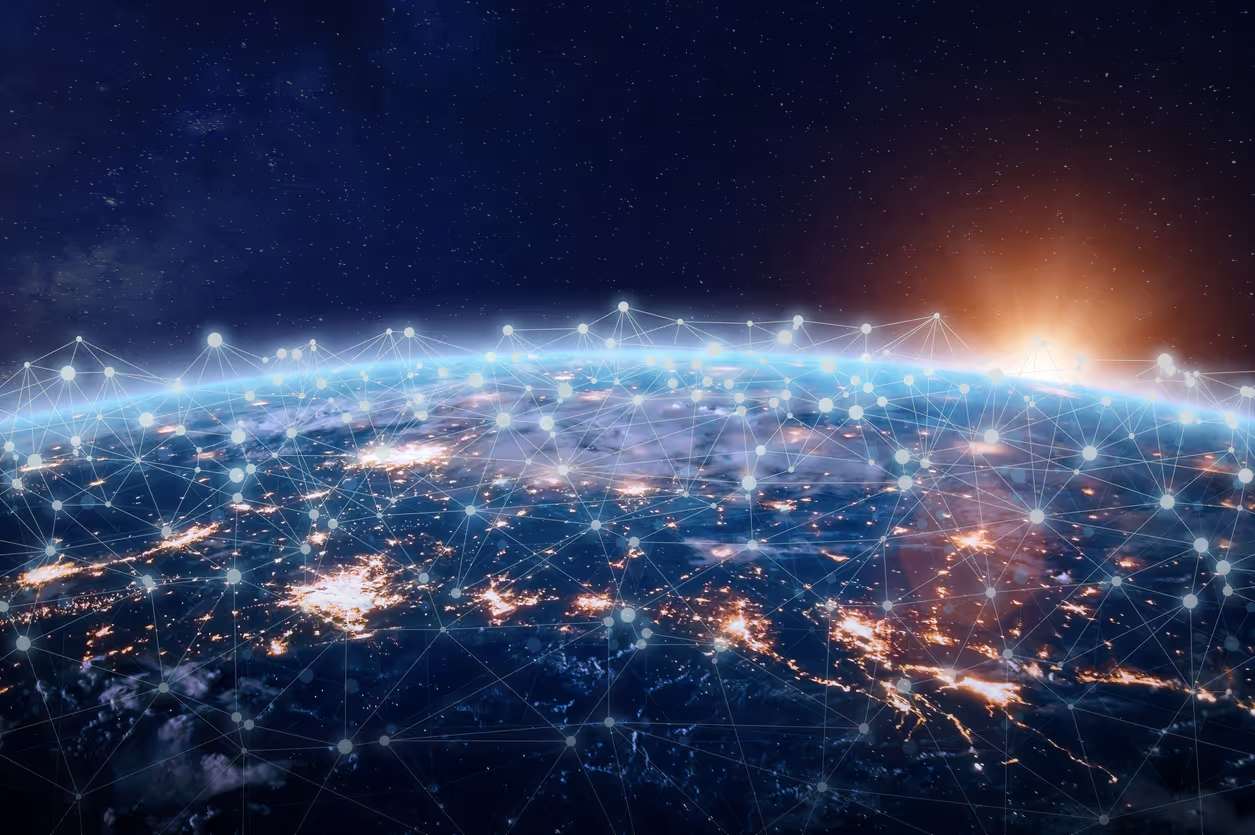
White paper: the future, today - the next generation of temperature monitoring
You may also be interested in
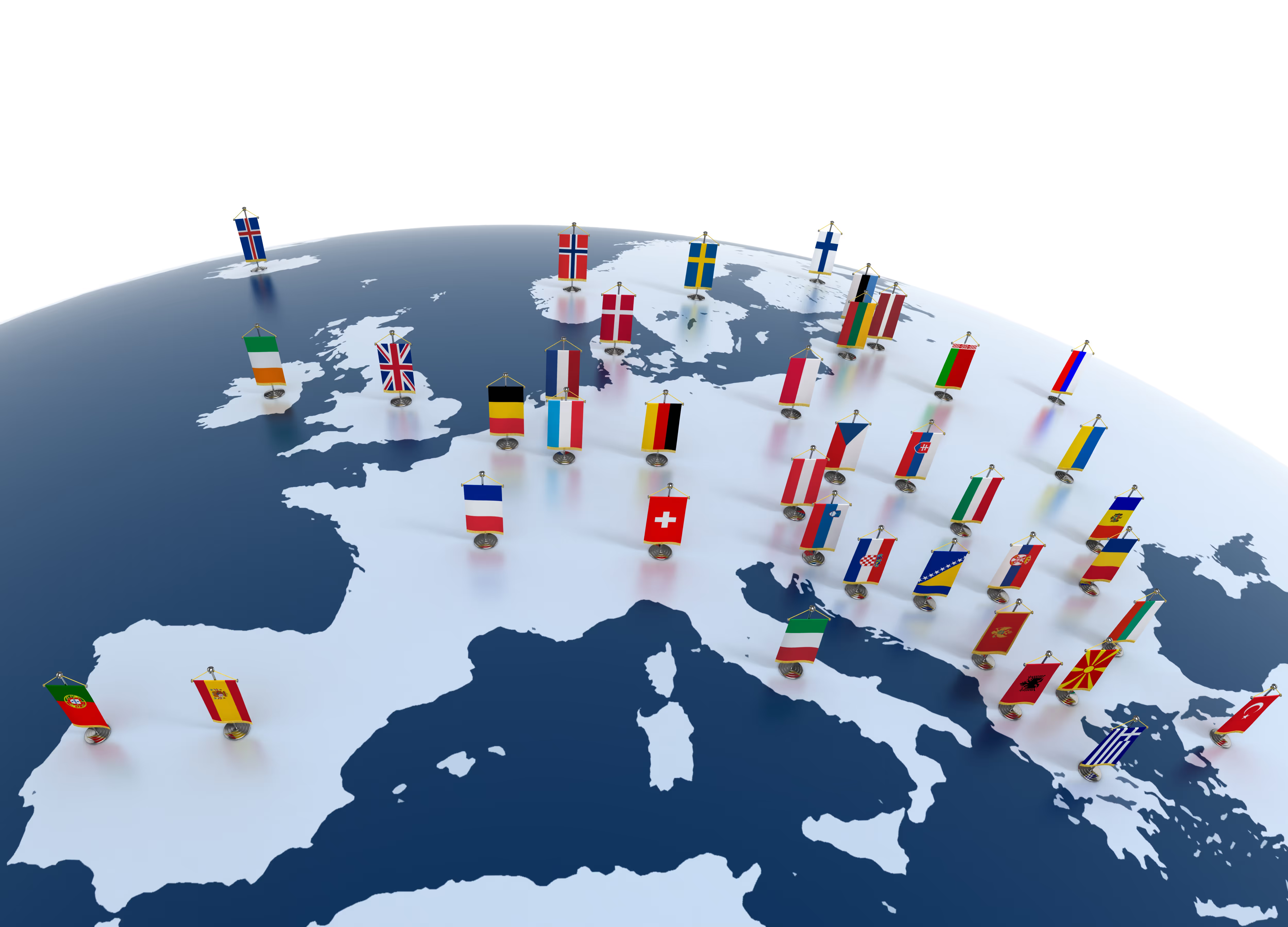
Join Us at LogiPharma Europe 2025
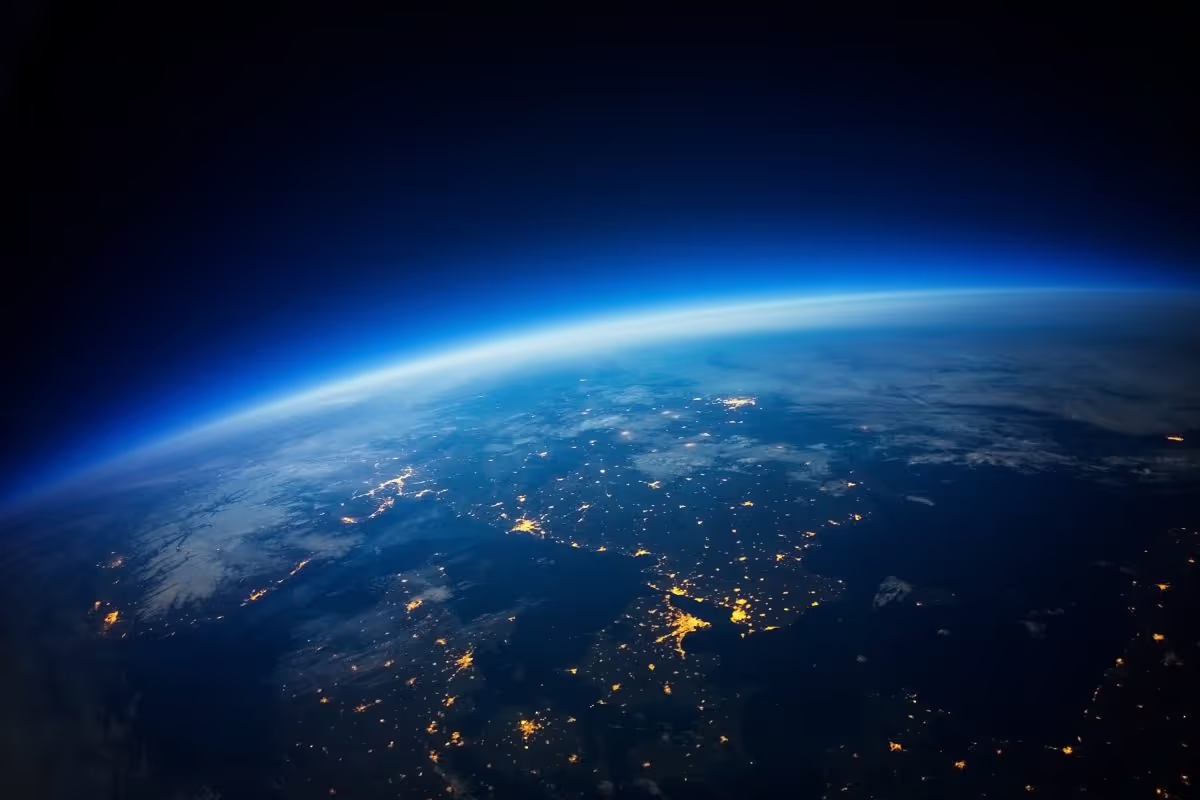
TSS launches innovative Bluetooth powered temperature monitoring solutions
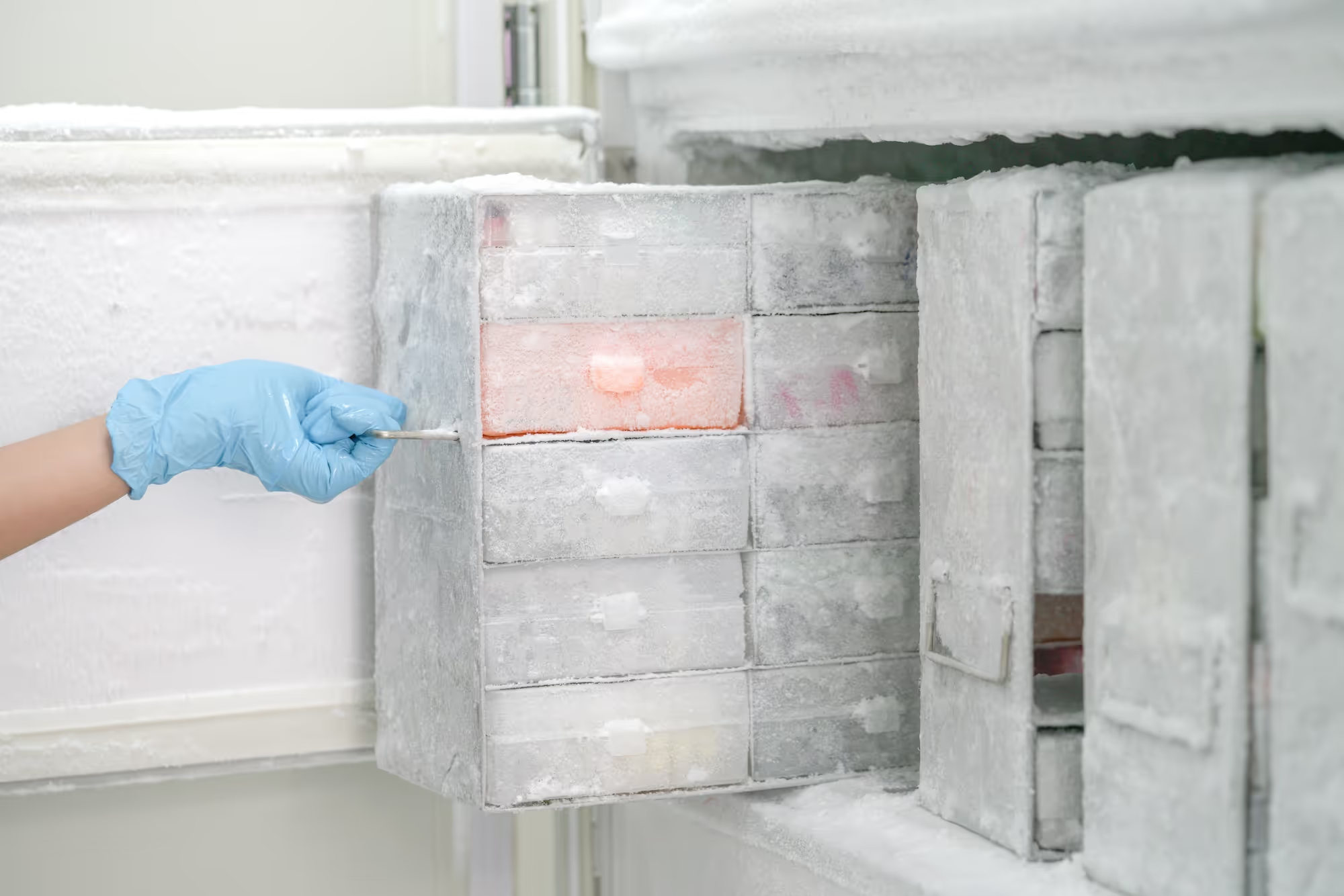
Achieving FDA and EMA Compliance in Temperature Monitoring
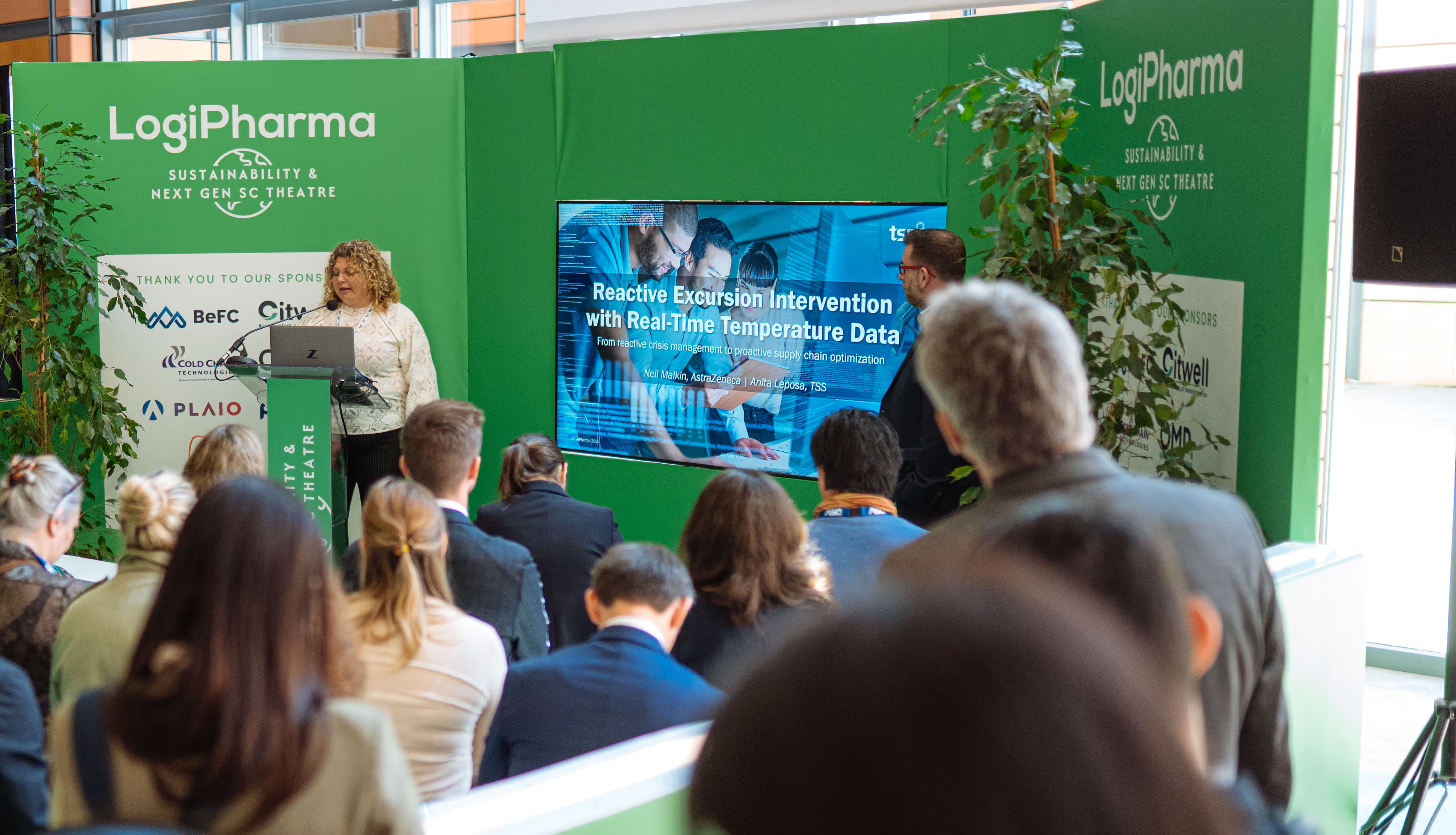
Proactive Temperature Management: The Key to a More Resilient Pharma Supply Chain
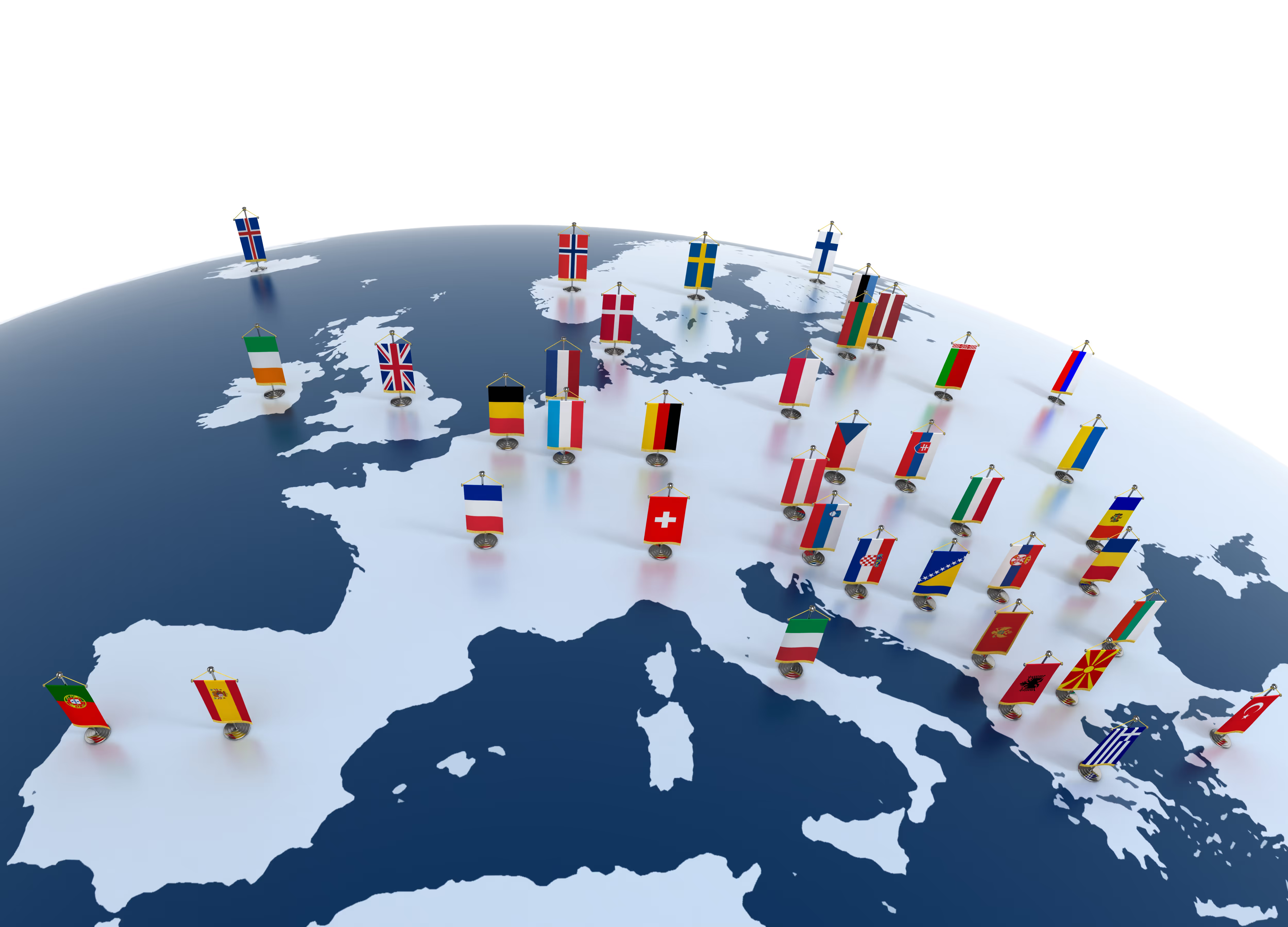
Join Us at LogiPharma Europe 2025
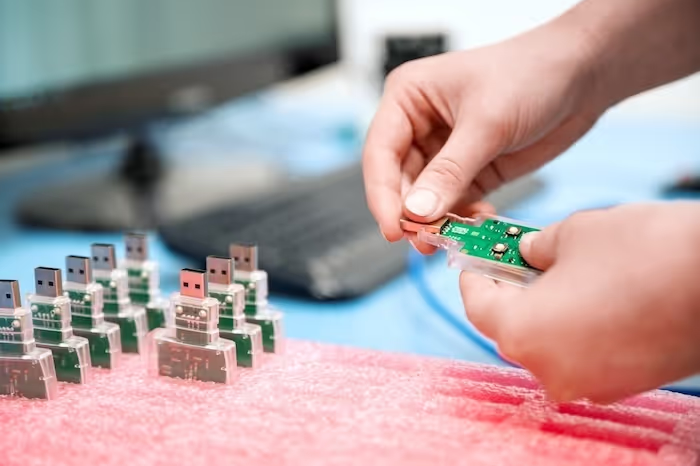
TSS Receives CDP SME Climate Score 'SME B' for Strong Climate Actions
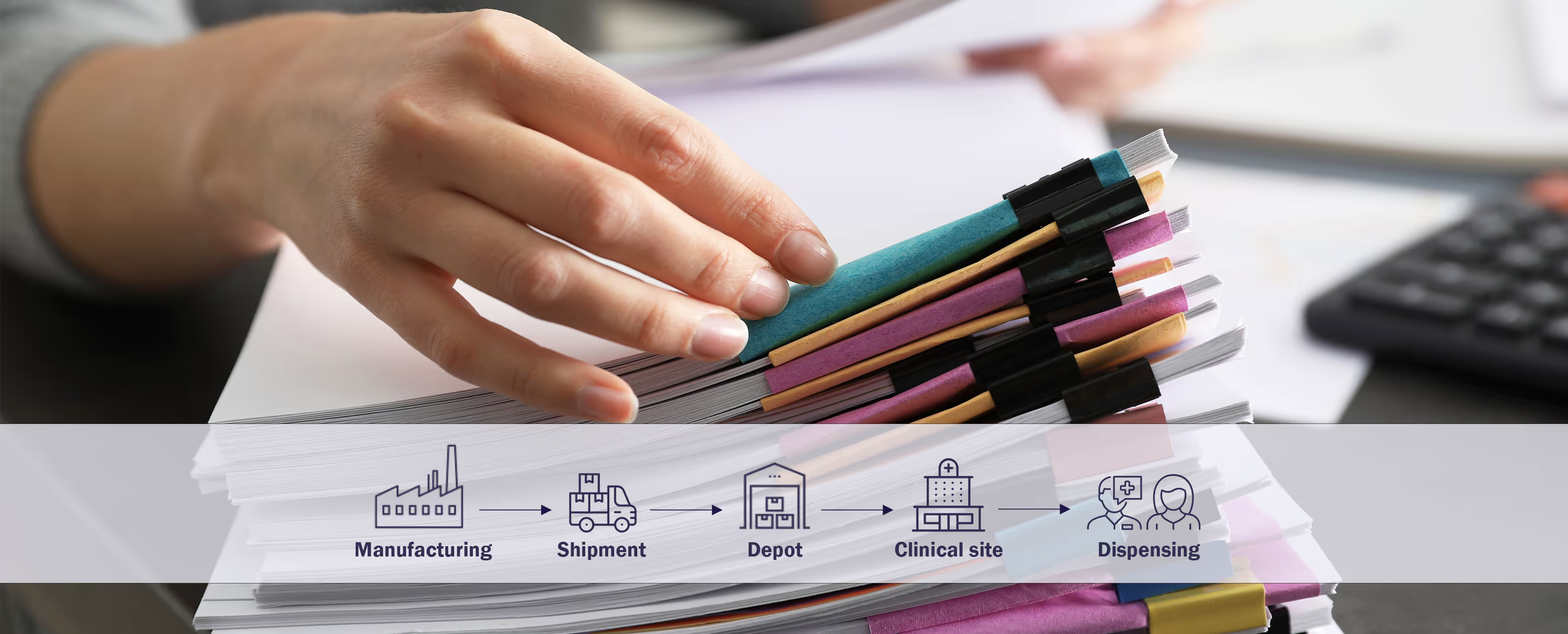
Future-Proofing Clinical Trials: How Sponsors Can Up-Scale Through Automation
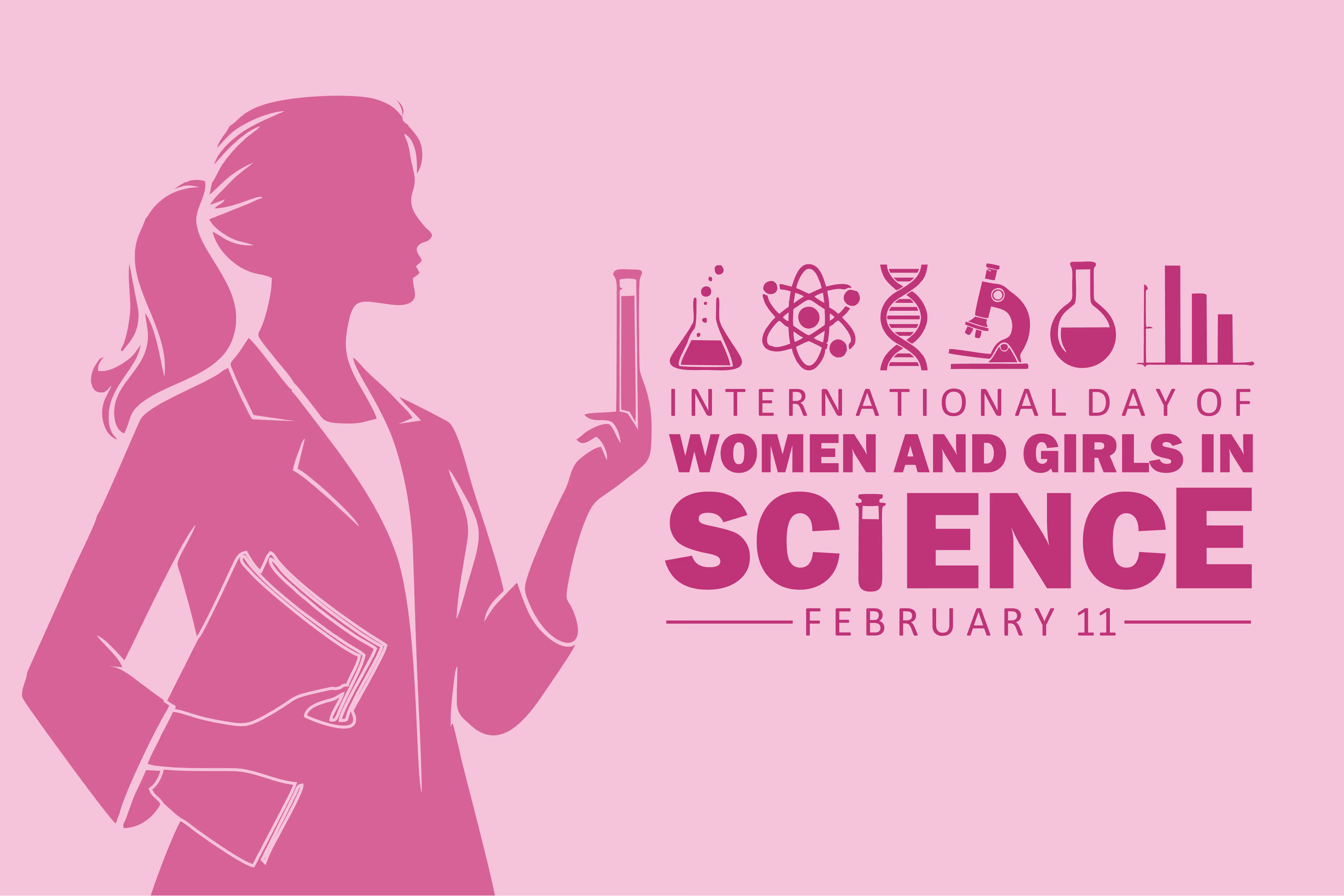
Celebrating Women in Tech
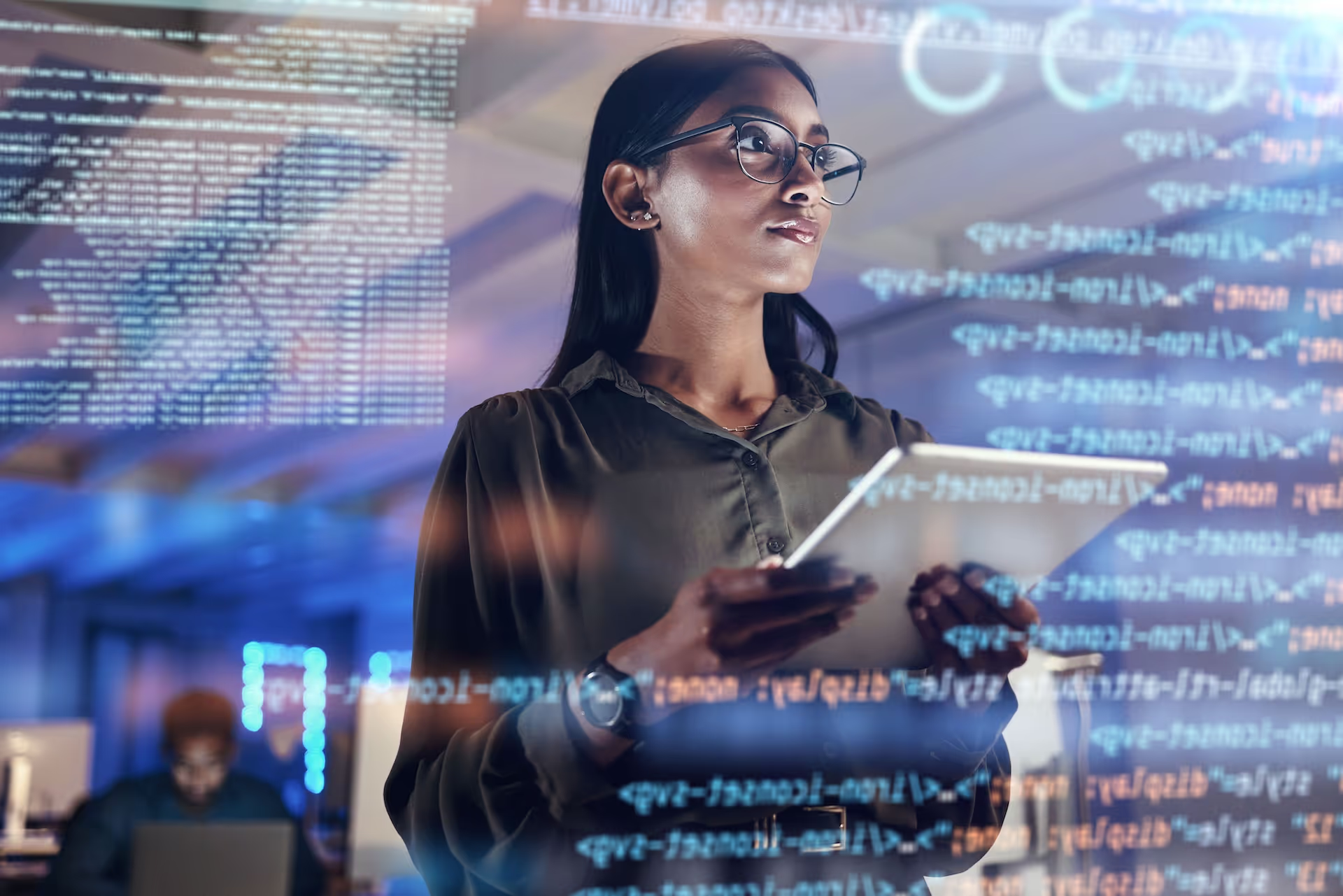
Clinical Trial Supply Europe Event 2025
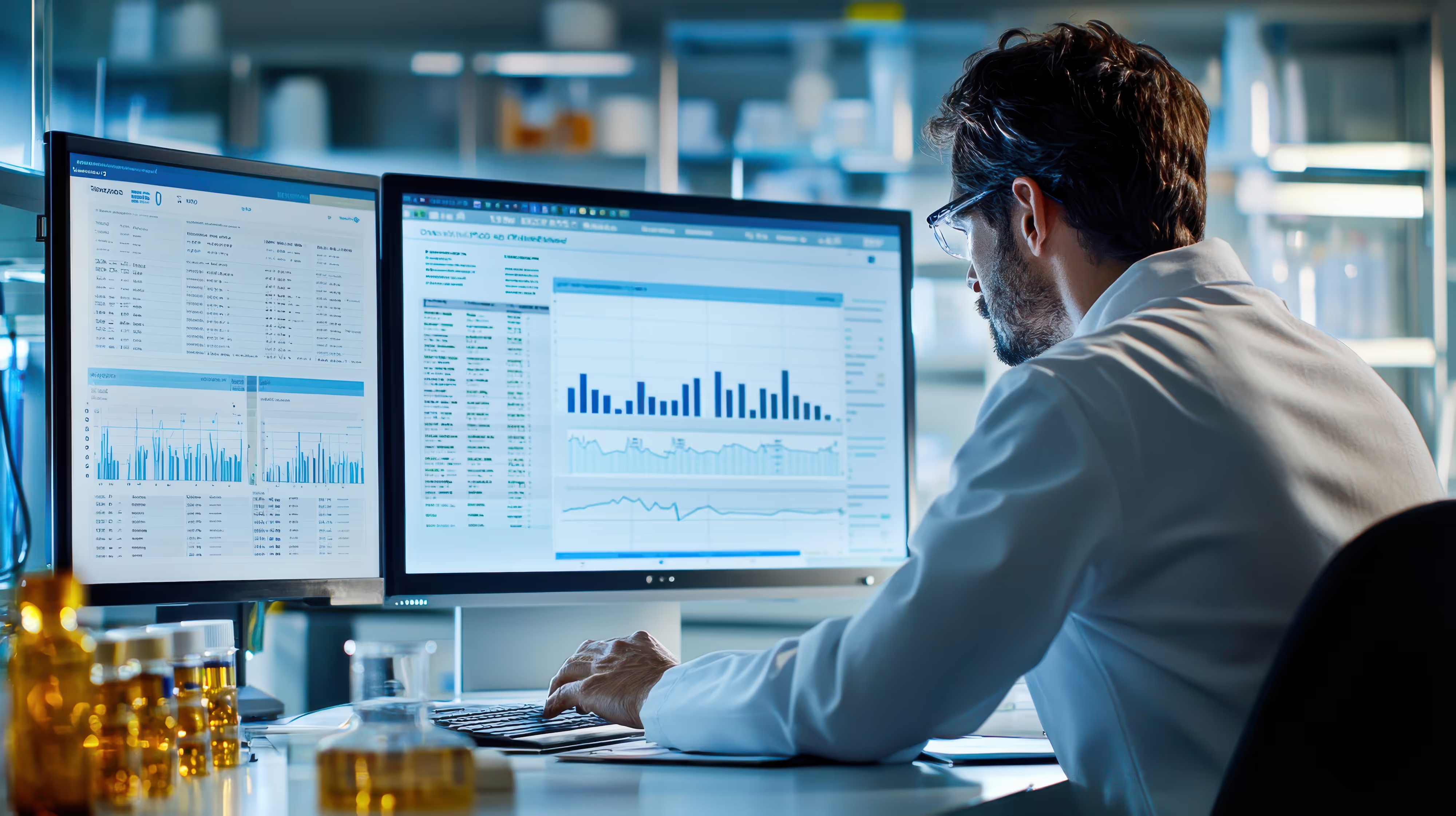
Sustainable Temperature Management: A Key to Greener Clinical Trials
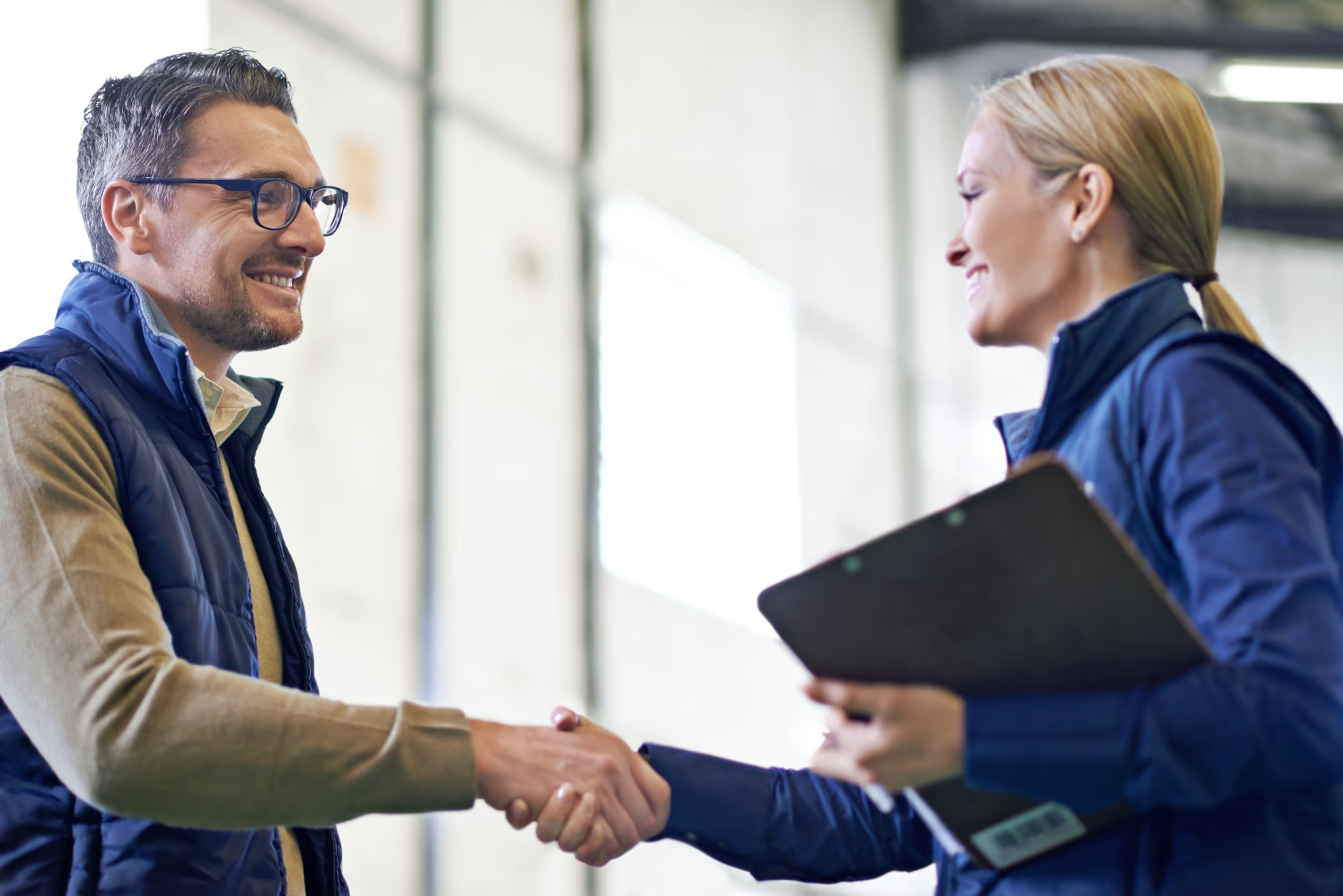
10 Common Mistakes to Avoid During Customer Onboarding
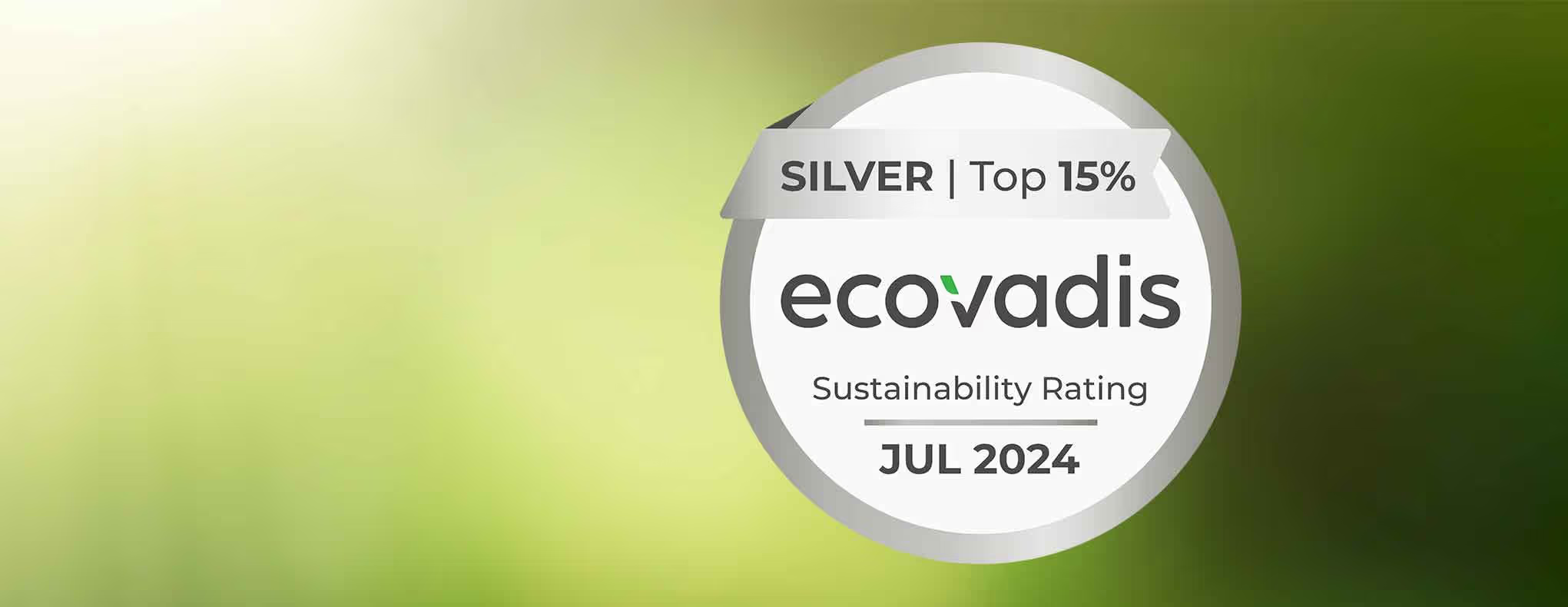
TSS Keeps EcoVadis Silver Medal Despite Tougher Standards in 2024
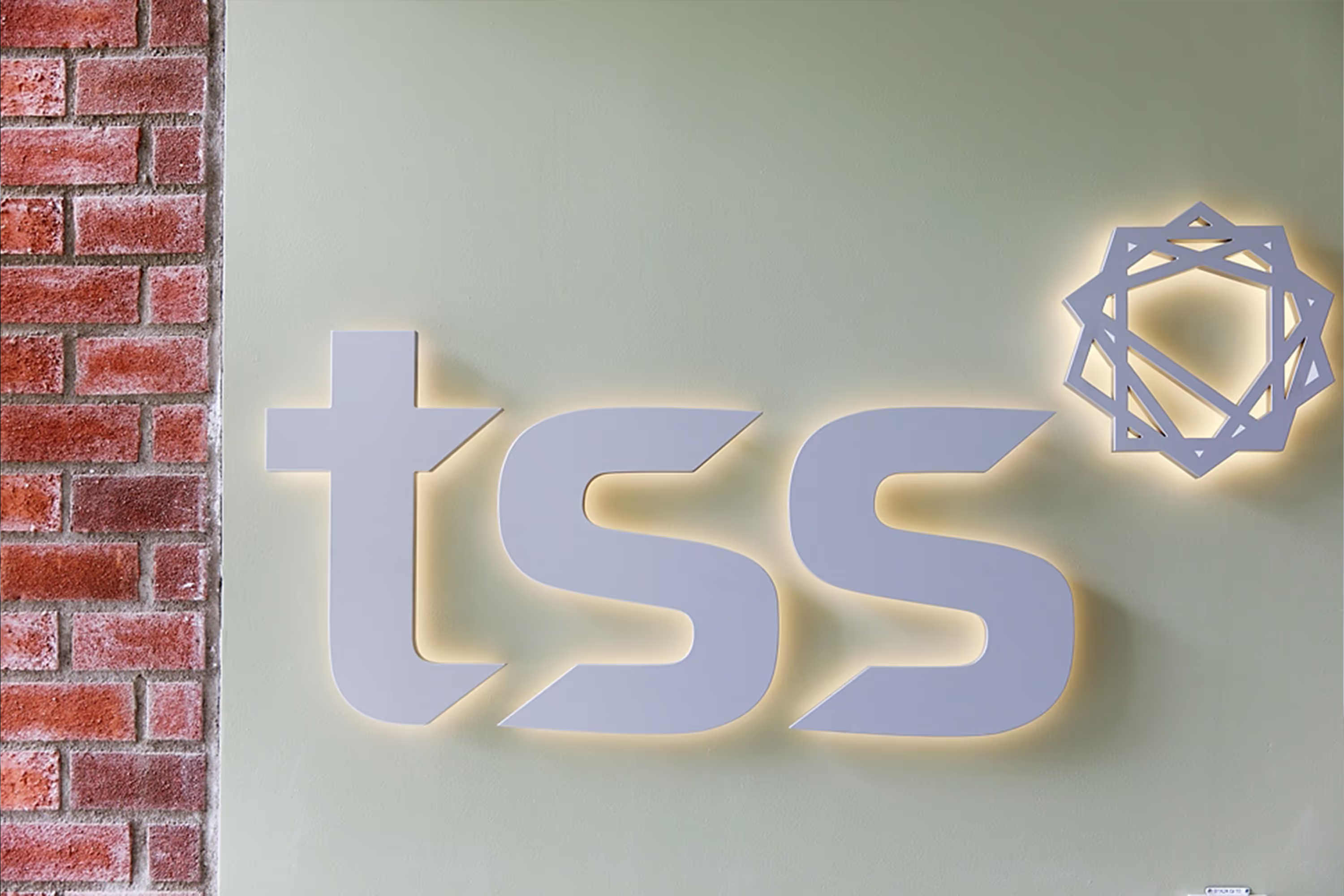
Change in the Management of TSS
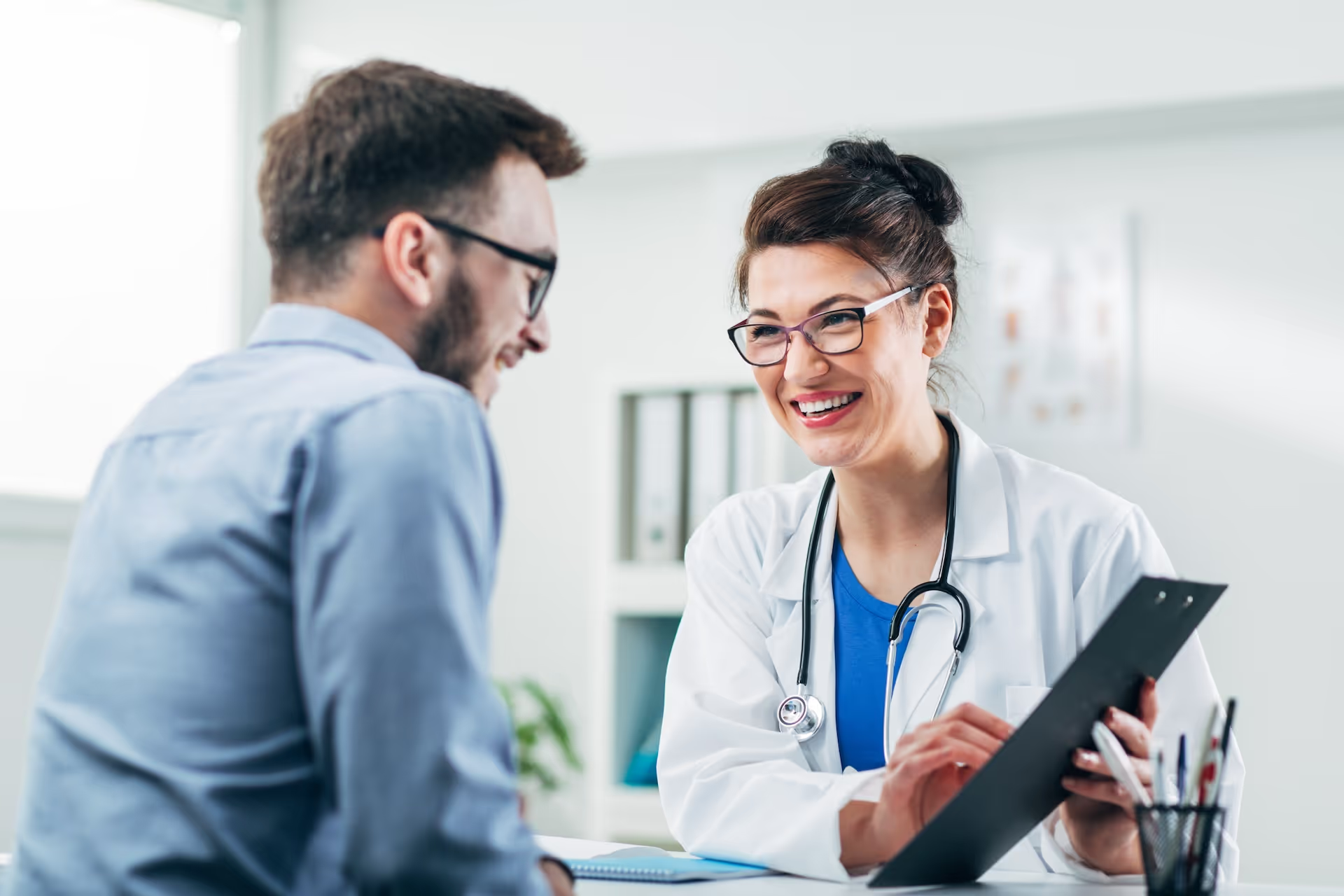
How to Scale Up Your Clinical Trials
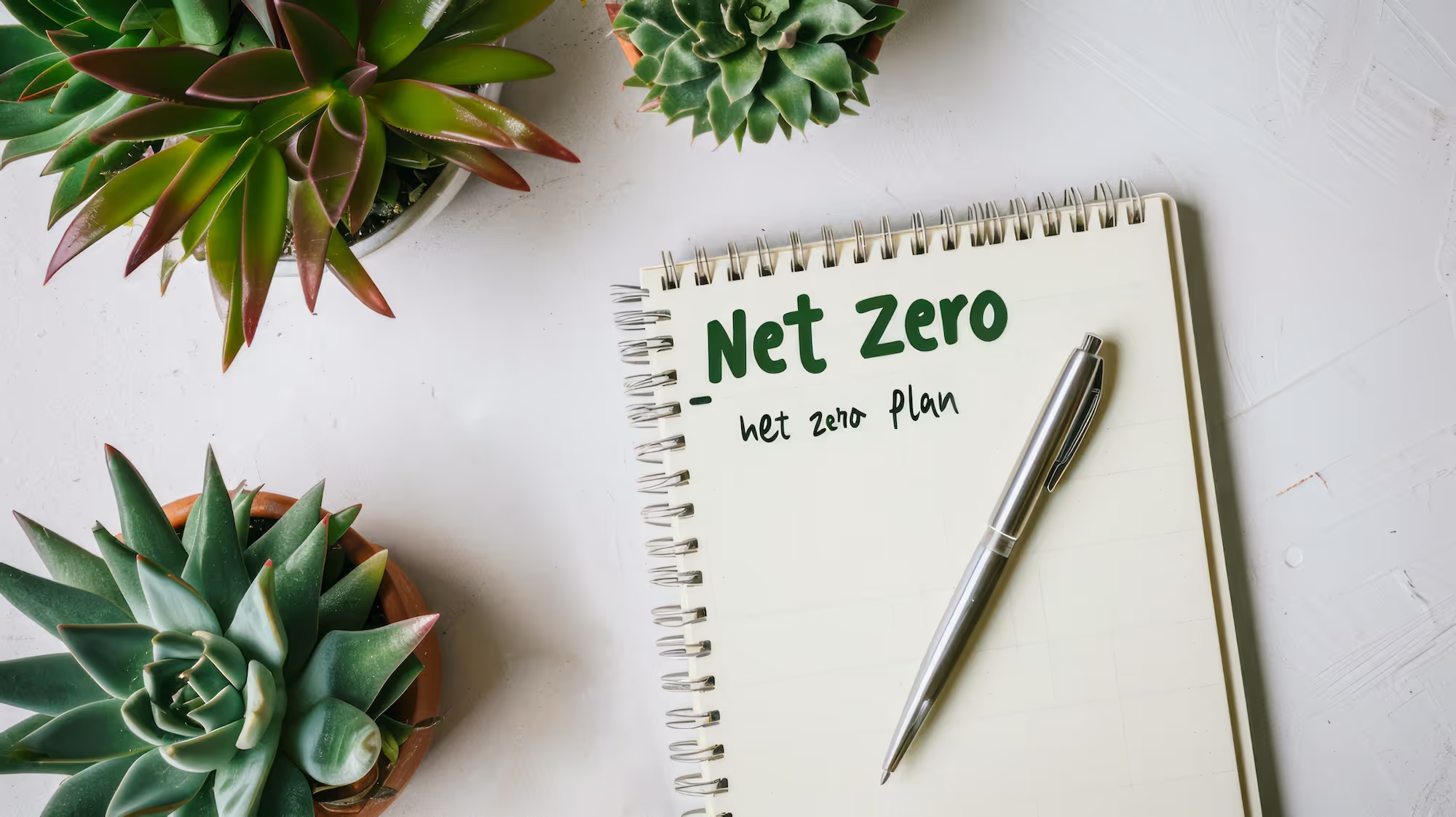
10 Steps to Navigating Sustainability in the Pharma Supply Chain
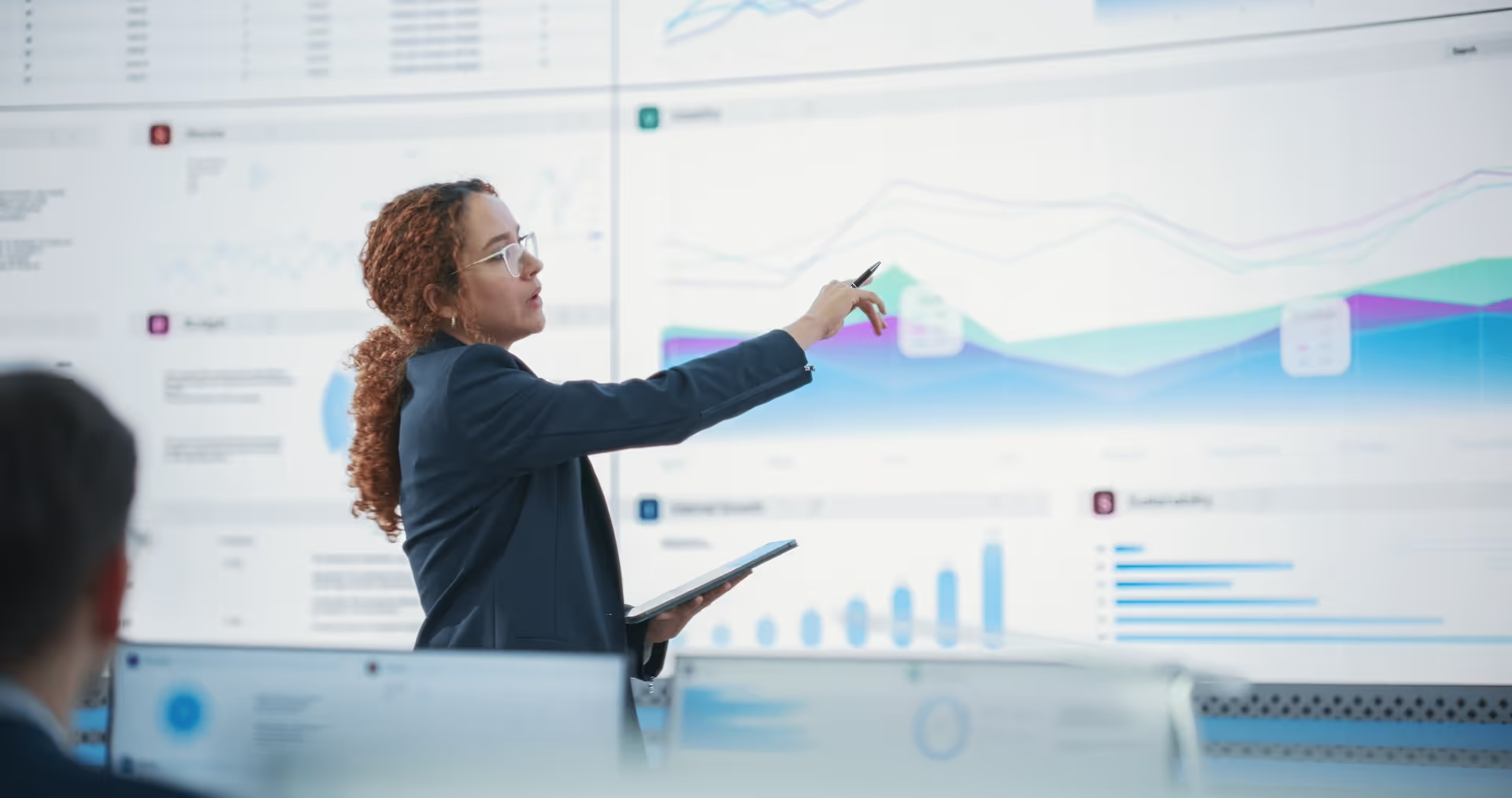
Balancing Cost and Quality in the Pharmaceutical Supply Chain: A Quick Guide
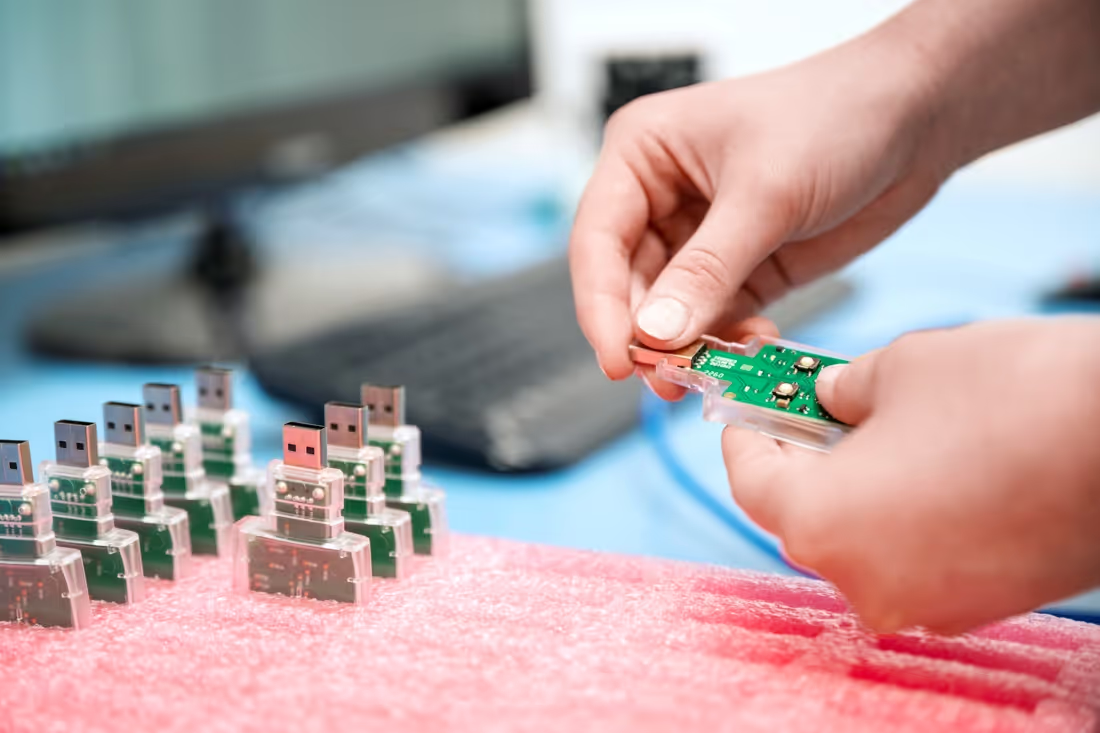
TSS Celebrates WTISD 2024: Embracing Innovation, Digitalisation, and Sustainability
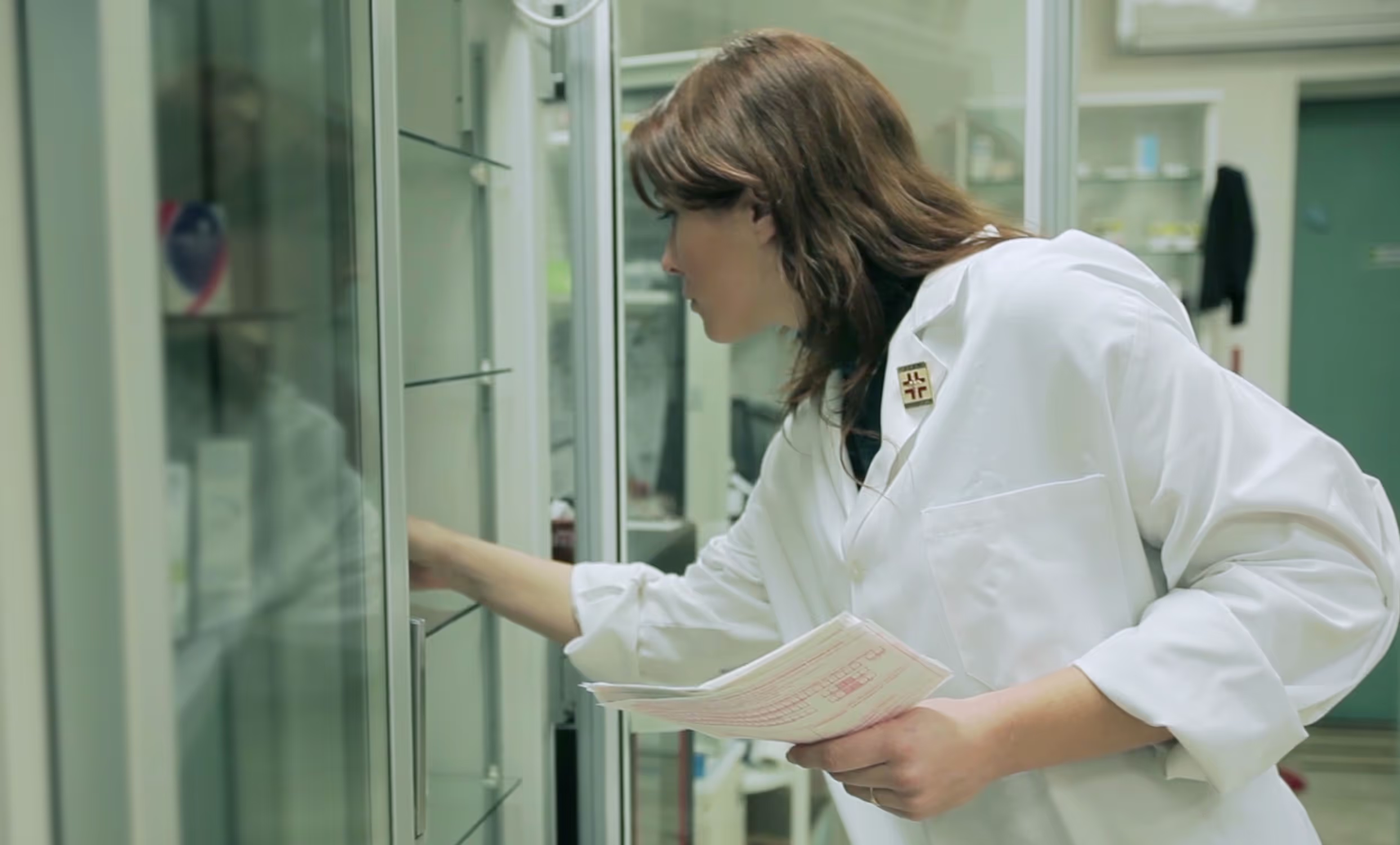
Enhancing Product Quality and Compliance at Clinical Sites
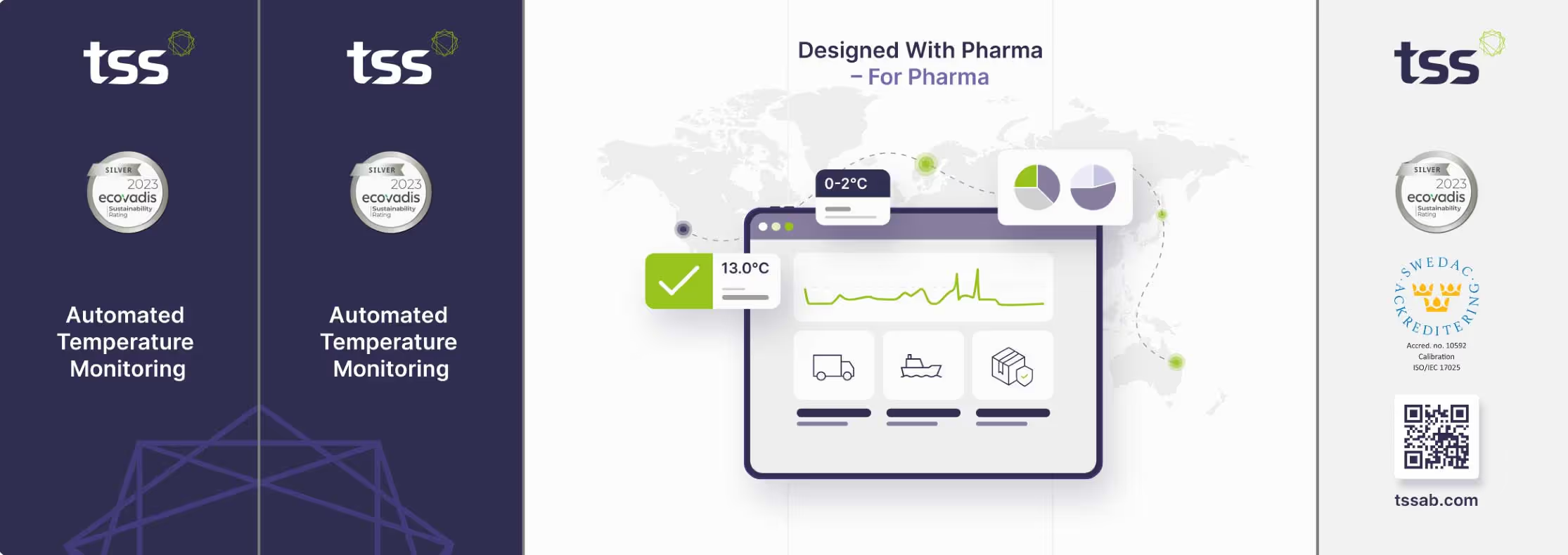
LogiPharma Lyon 2024
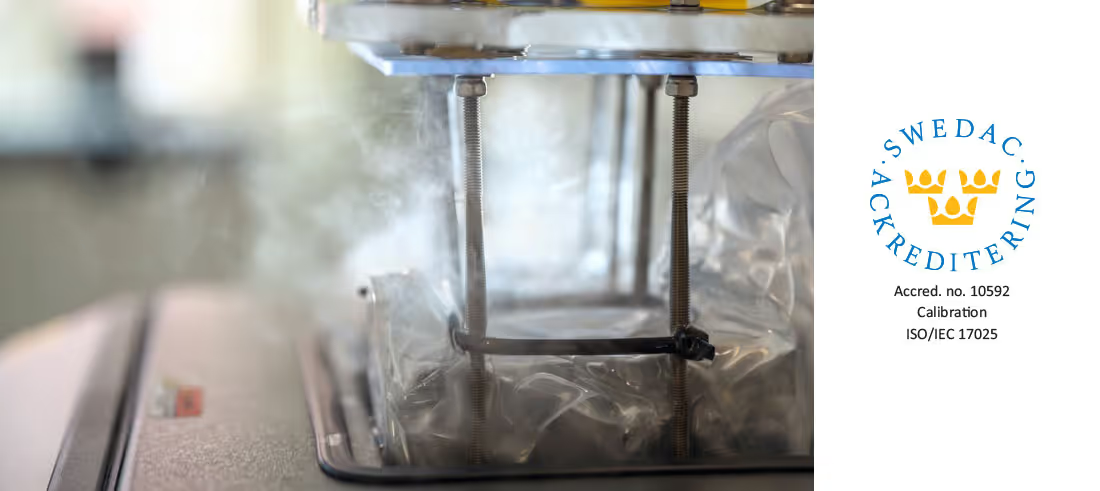
TSS Achieves Coveted ISO/IEC 17025 Calibration Accreditation
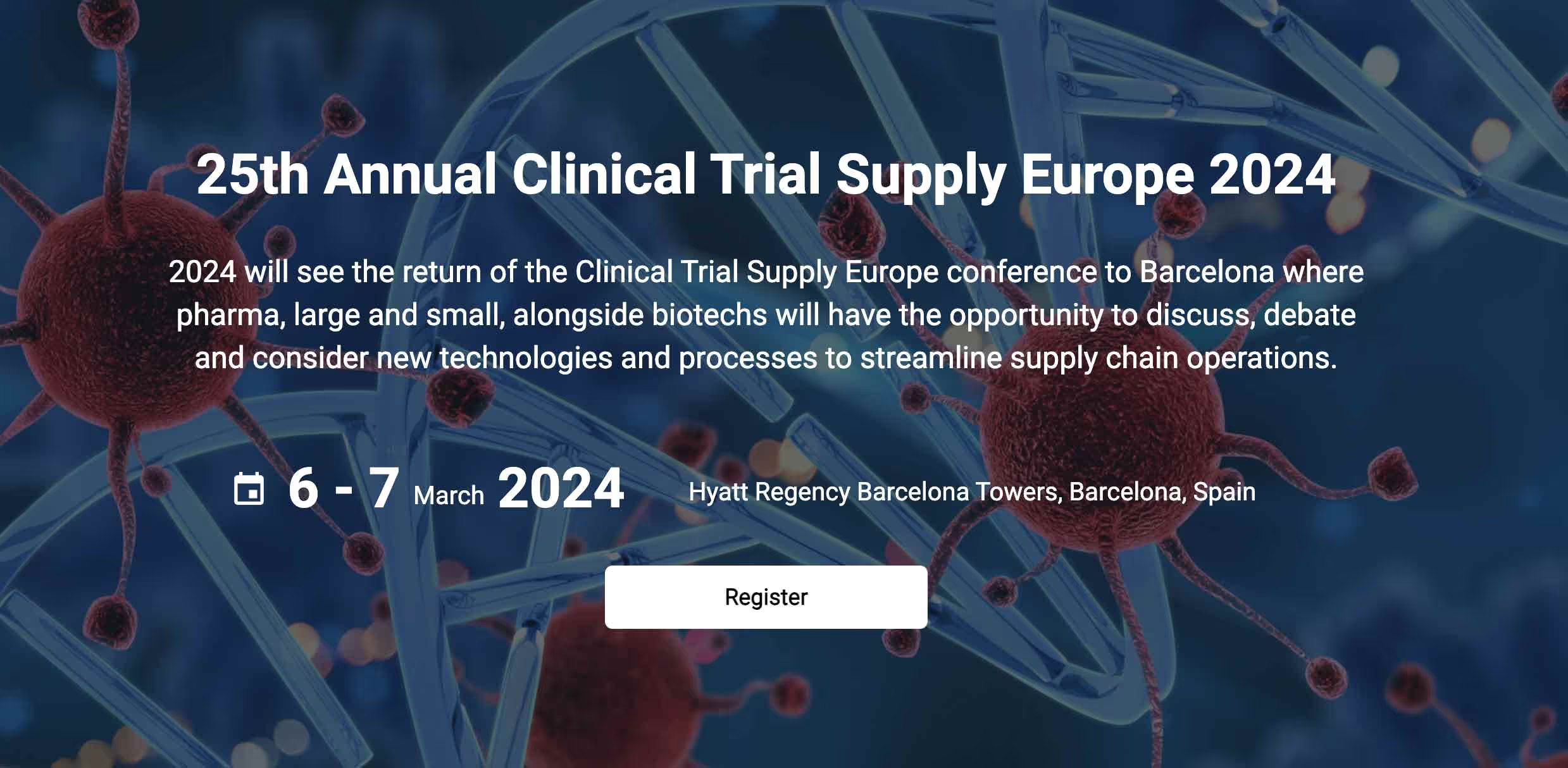
Join us at Clinical Trial Supply Europe 2024 in Barcelona
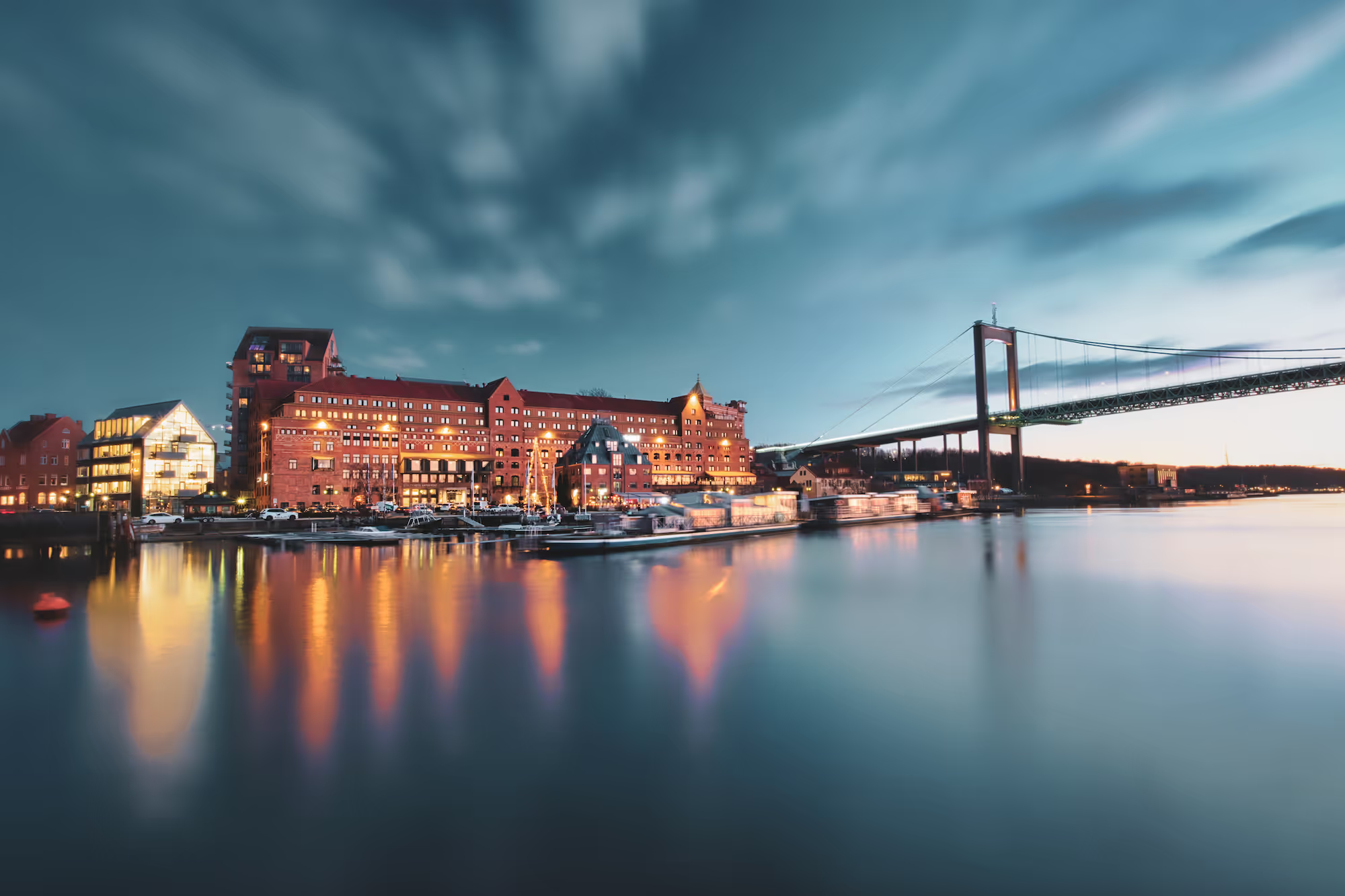
TSS User Forum 2023
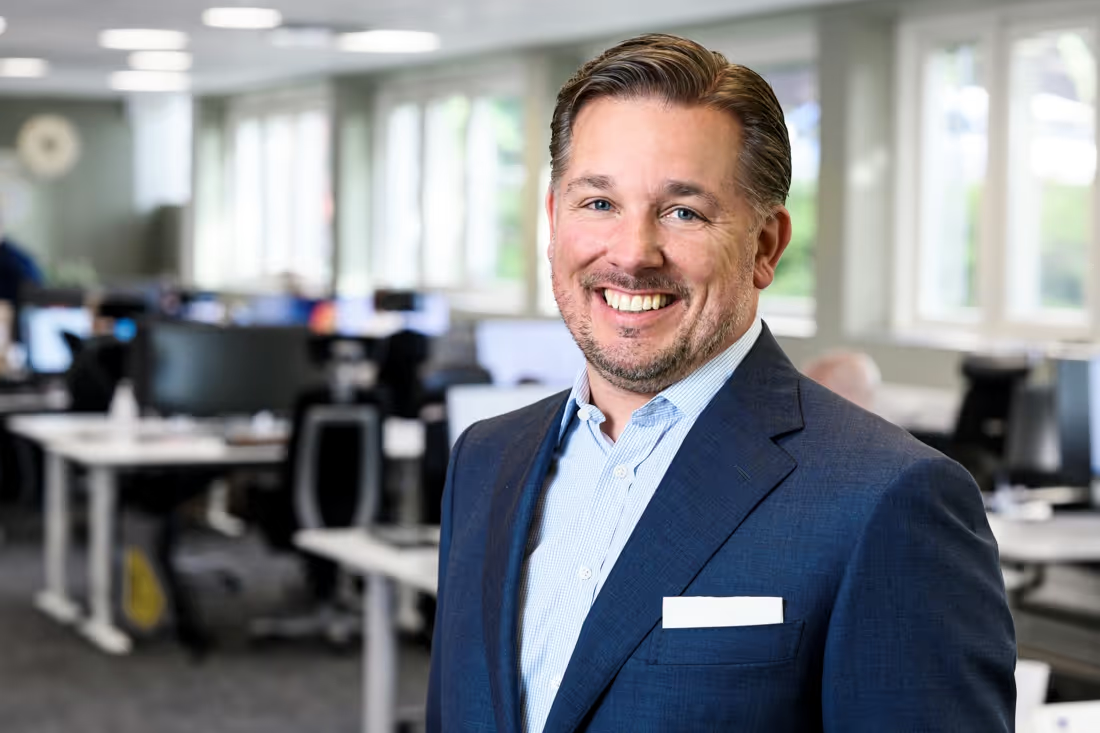
TSS Welcomes Gustaf Rasin as New Chief Operations Officer
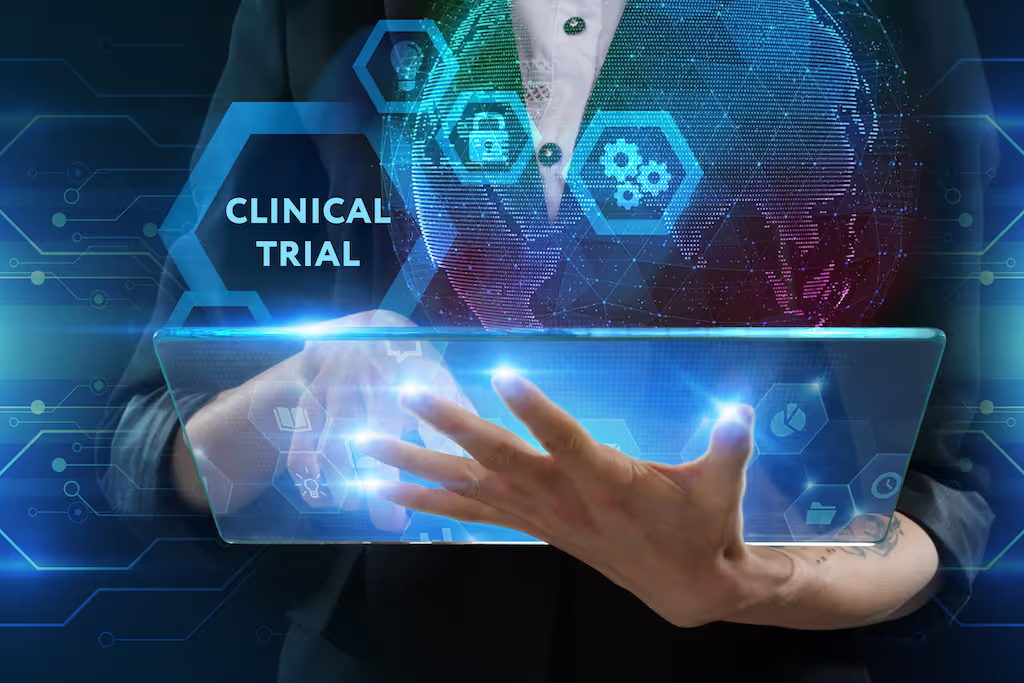
NECSO Cambridge 2023
.avif)
TSS Welcomes Thomas Lindén as New Chief Technology Officer
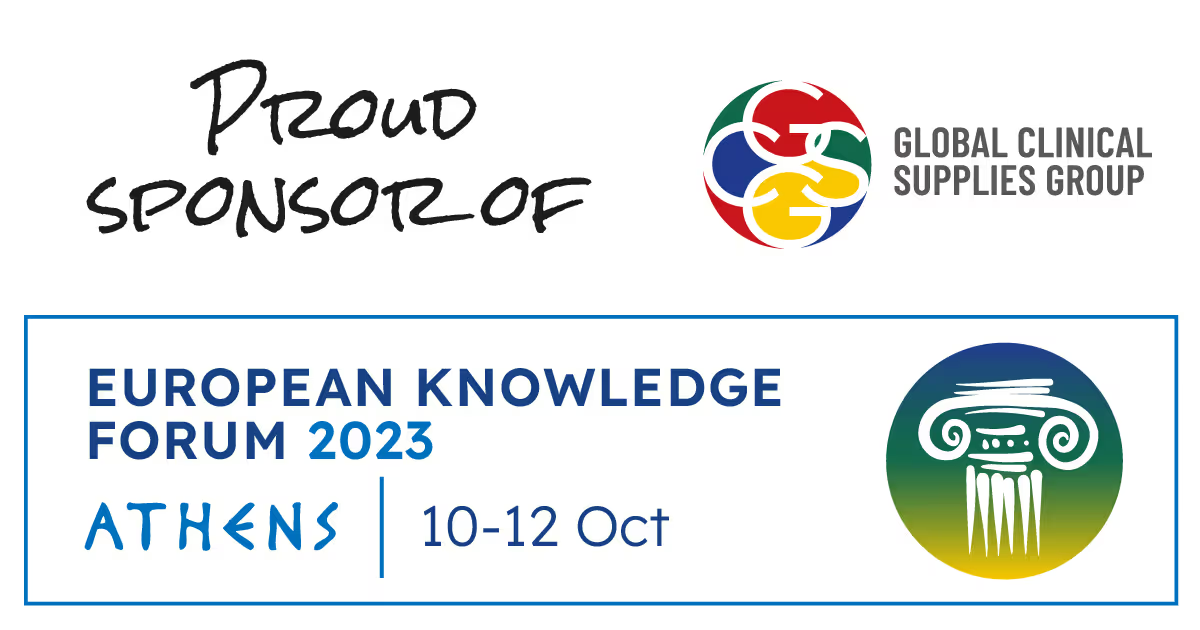
GCSG Athens 2023 Vendor Showcase Hosted by TSS
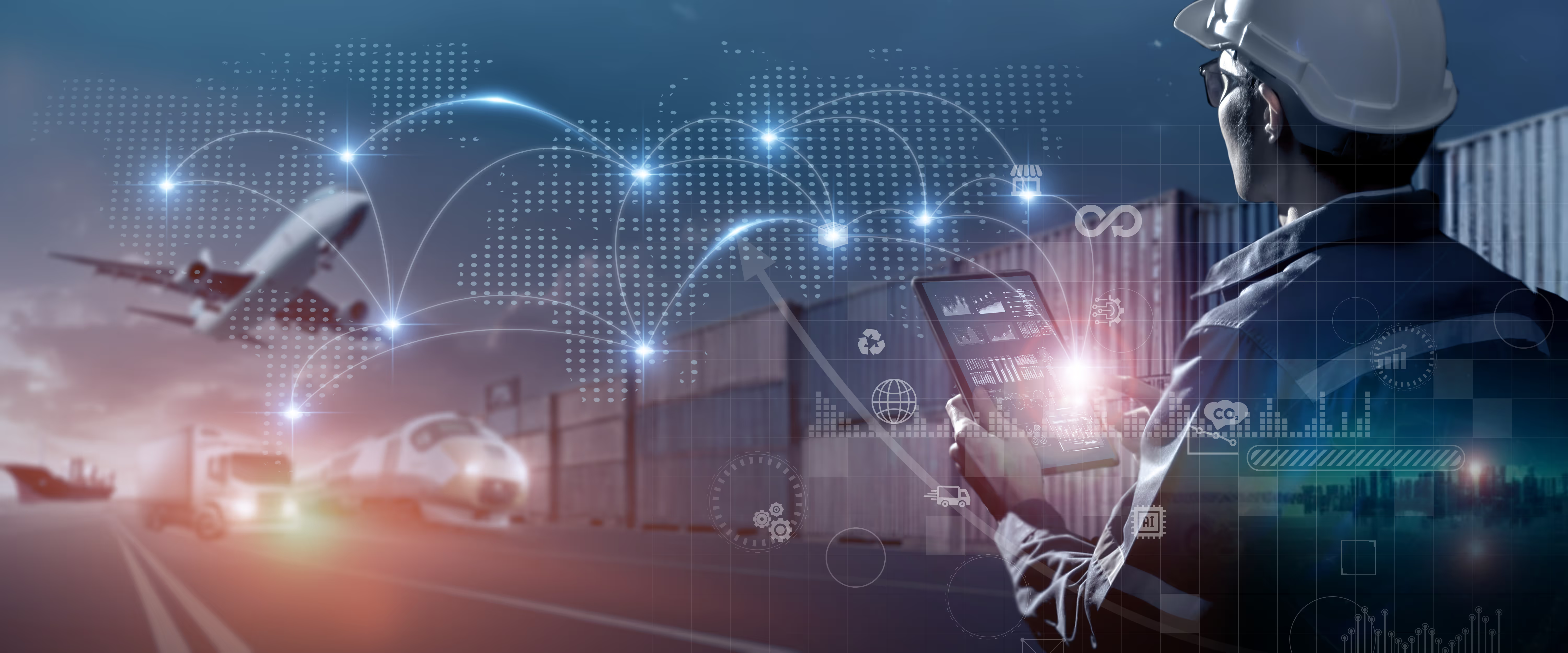
How GSK Pharma in UAE optimized the supply chain through automatization
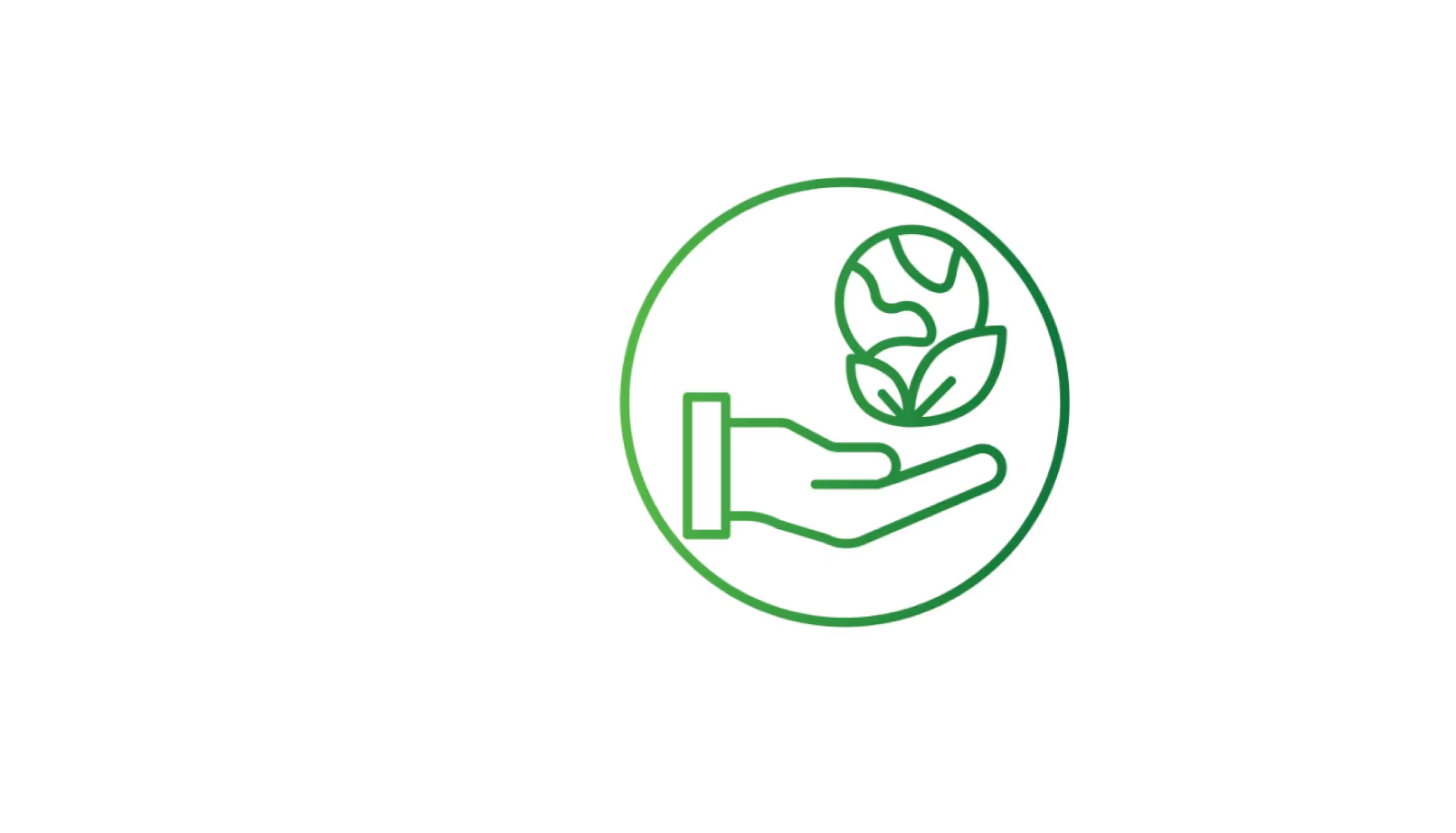
Cooperation with Swedish Innovation Authority and University to Optimize Sustainability Procedures
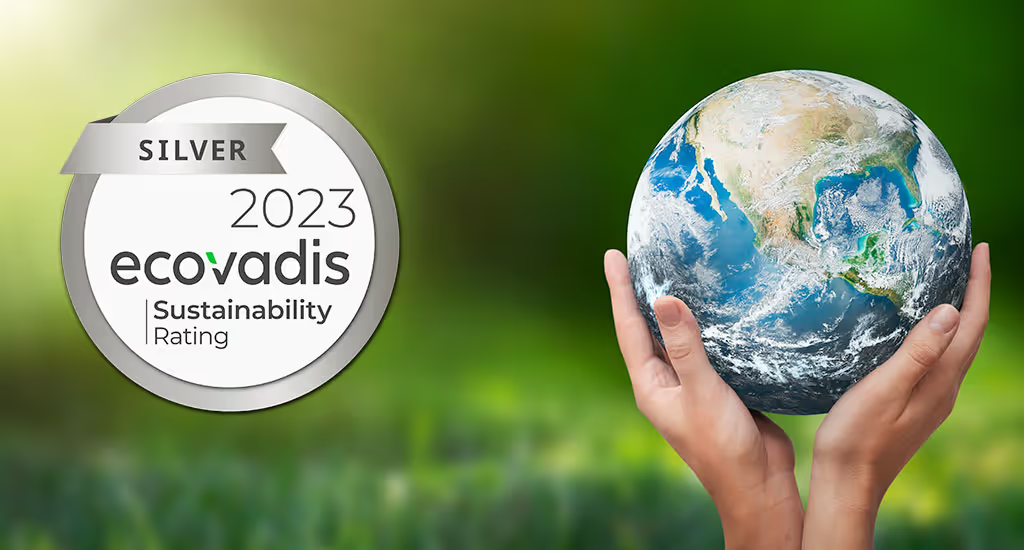
TSS Achieves EcoVadis Silver Medal for Advanced Sustainability Performance
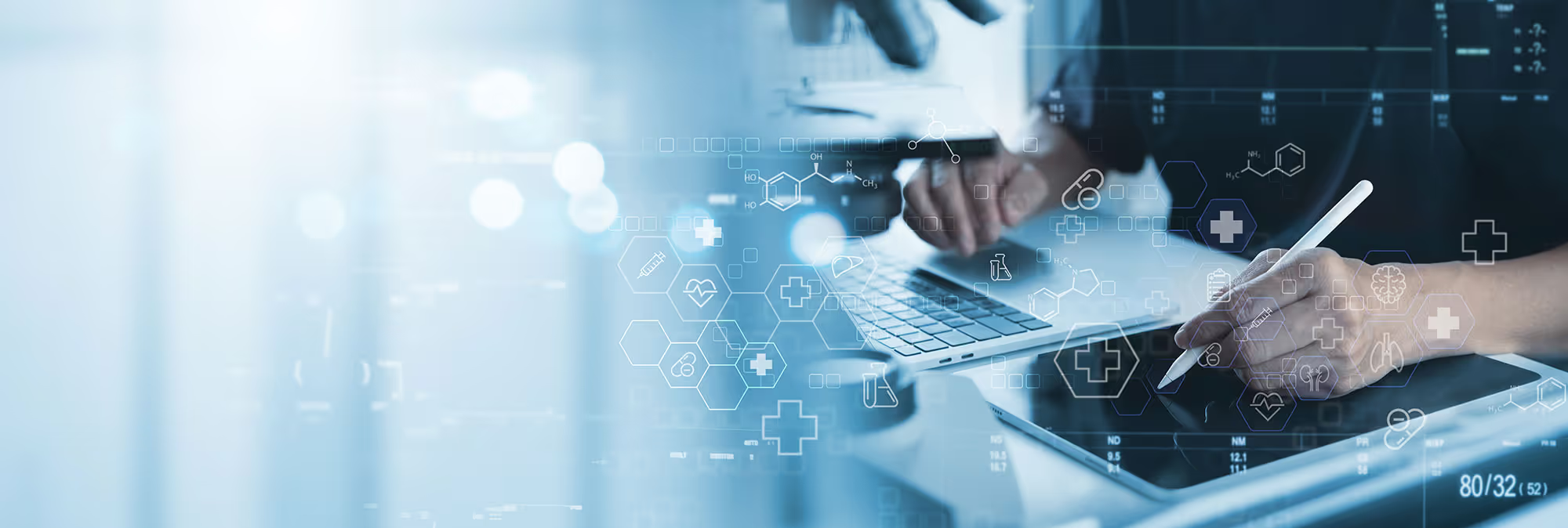
How can maturity in temperature management move your decision process from days to seconds?
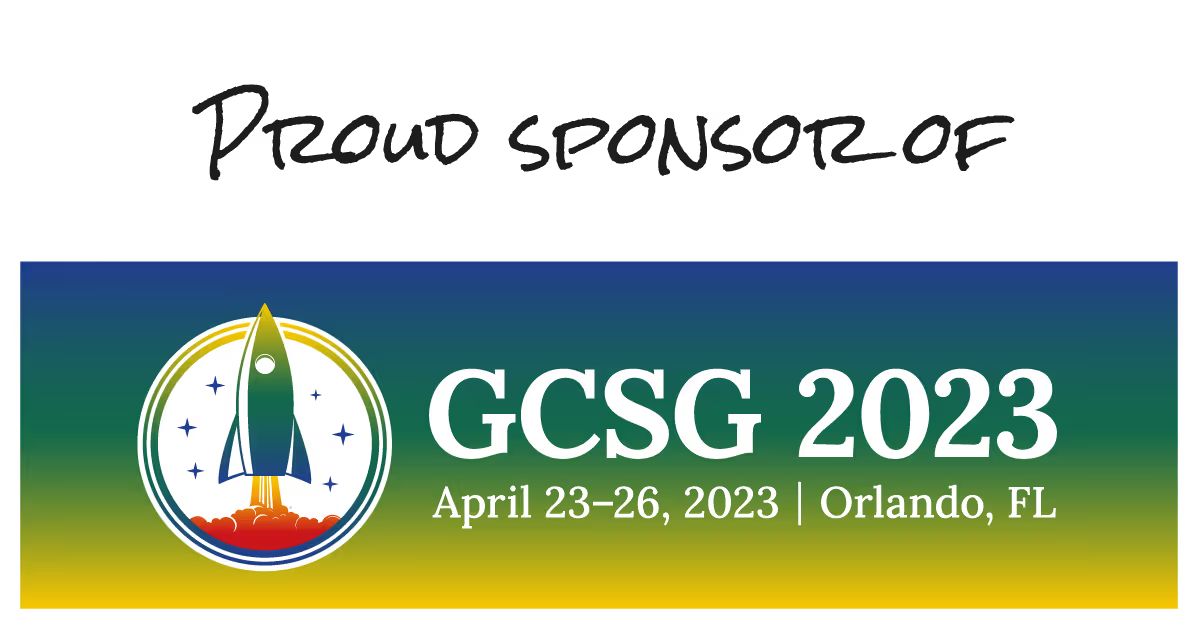
GCSG 2023 US Conference
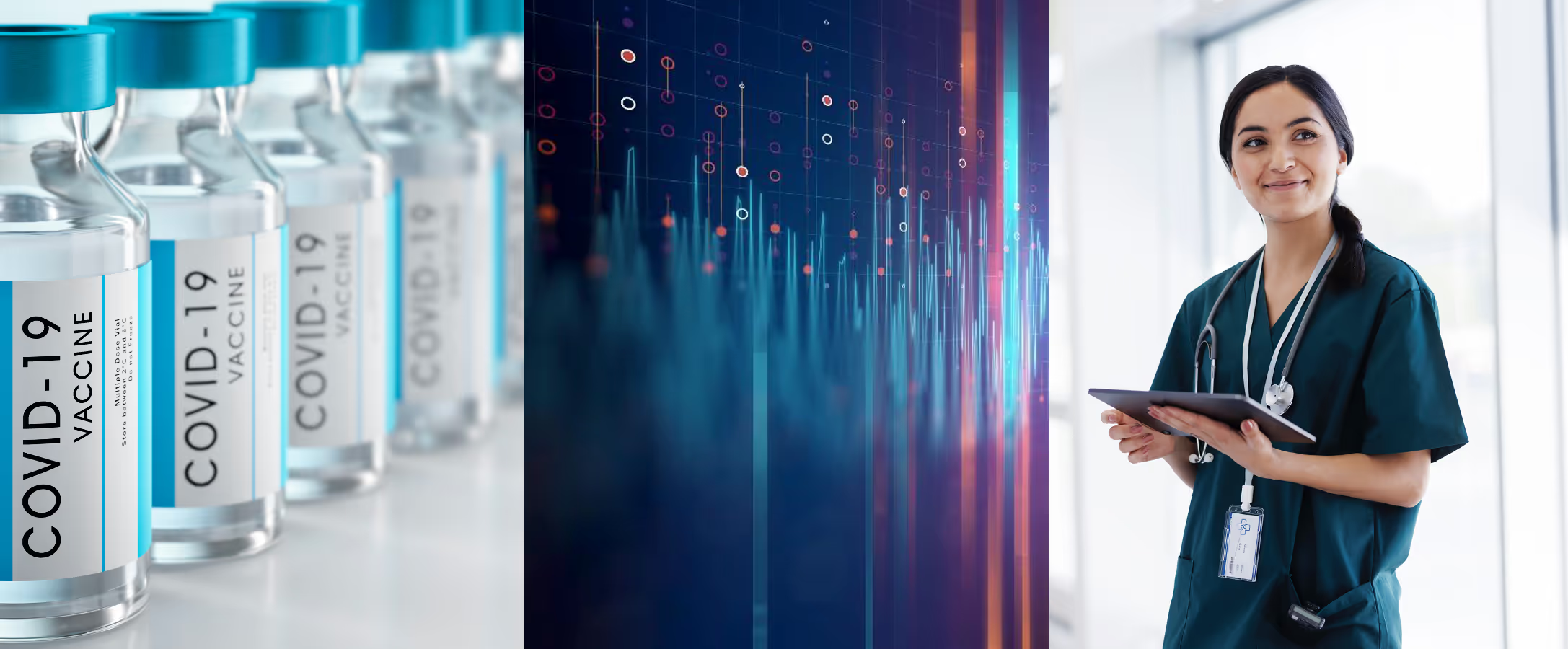
3 steps to accelerate Decentralized trials & Release to patients
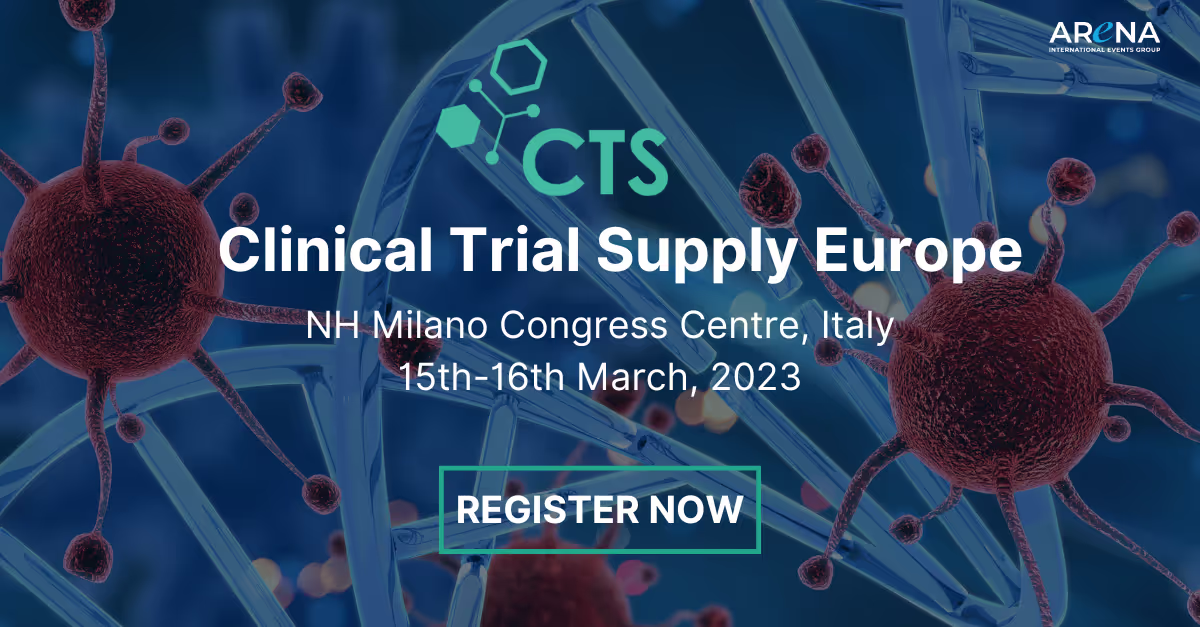
Join us at Clinical Trial Supply Europe 2023
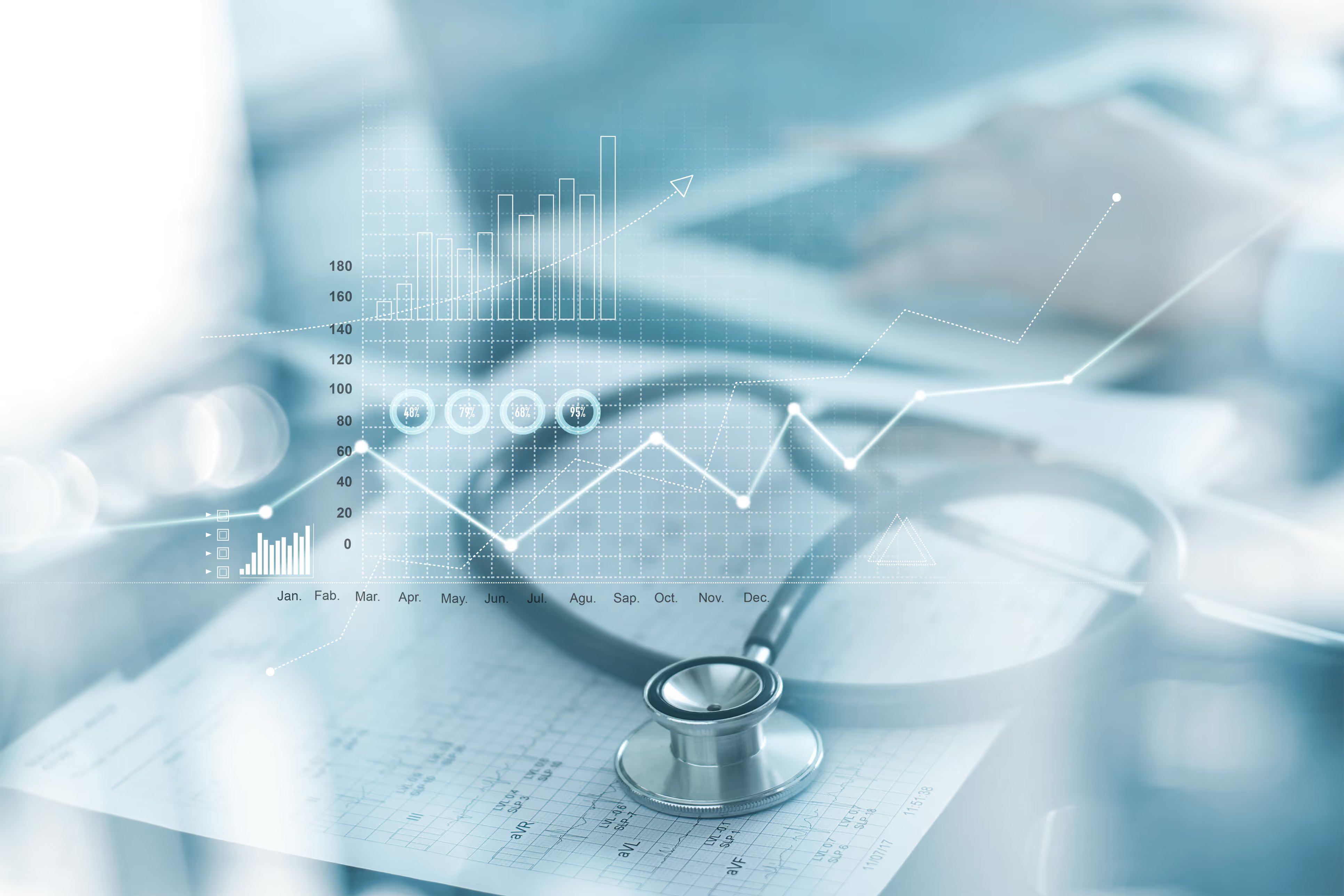
We are back at Clinical Trial Supply East Coast
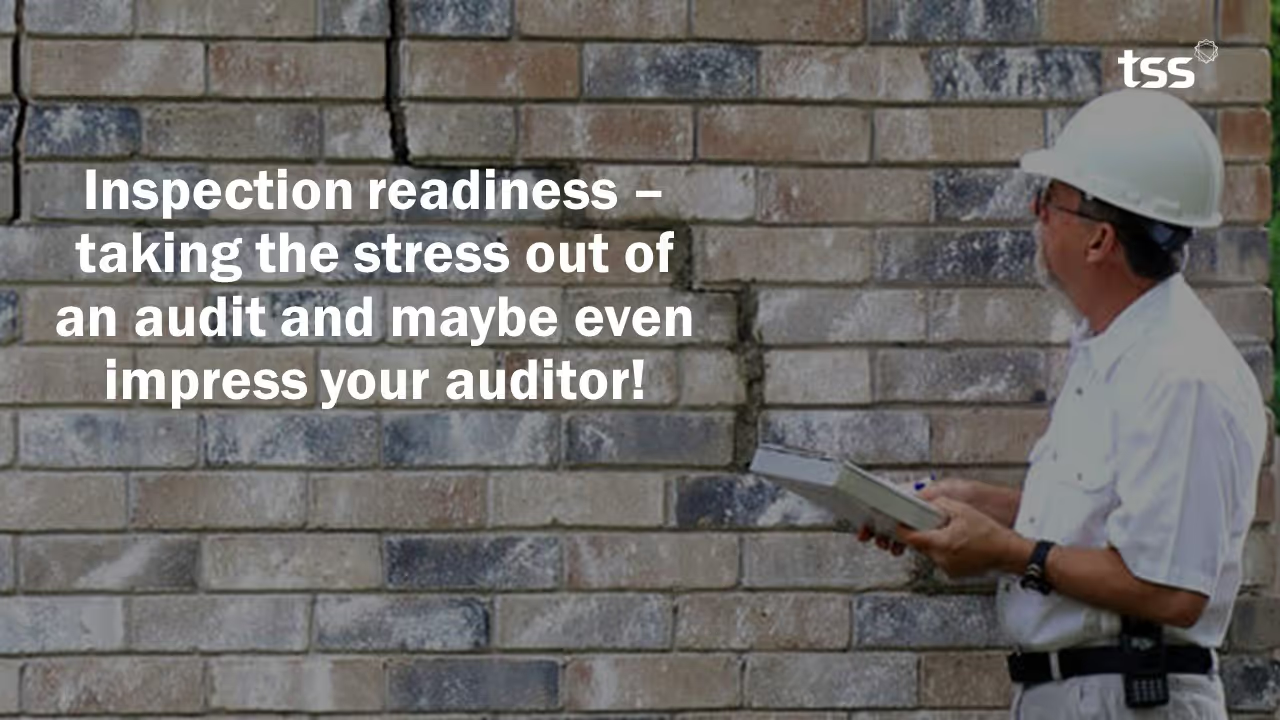
The GCSG 2022 European Knowledge Forum is coming up, and we will be there.
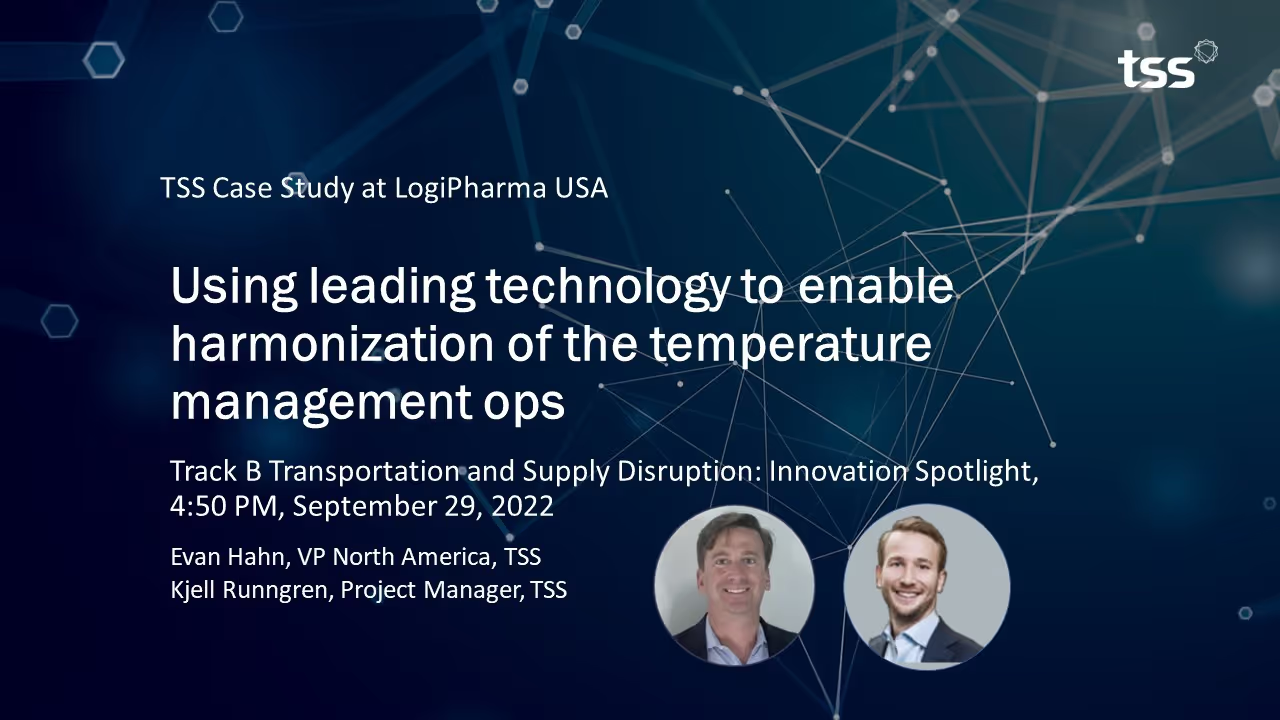
Meet us at Logipharma US in Boston on September 29th-30th
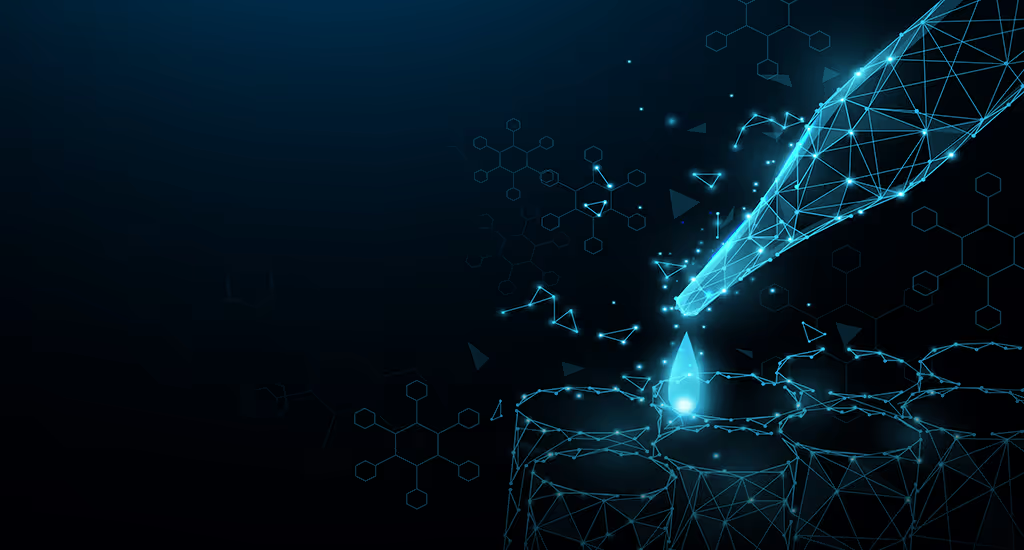
Boost value in clinical trial management with two-way integrations
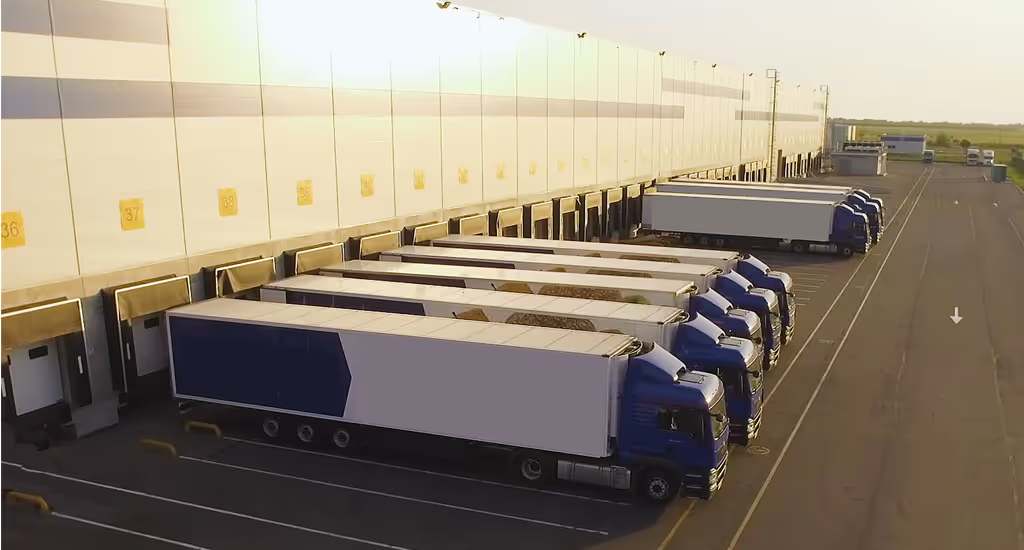
Achieving pharma supply chain excellence through integrations
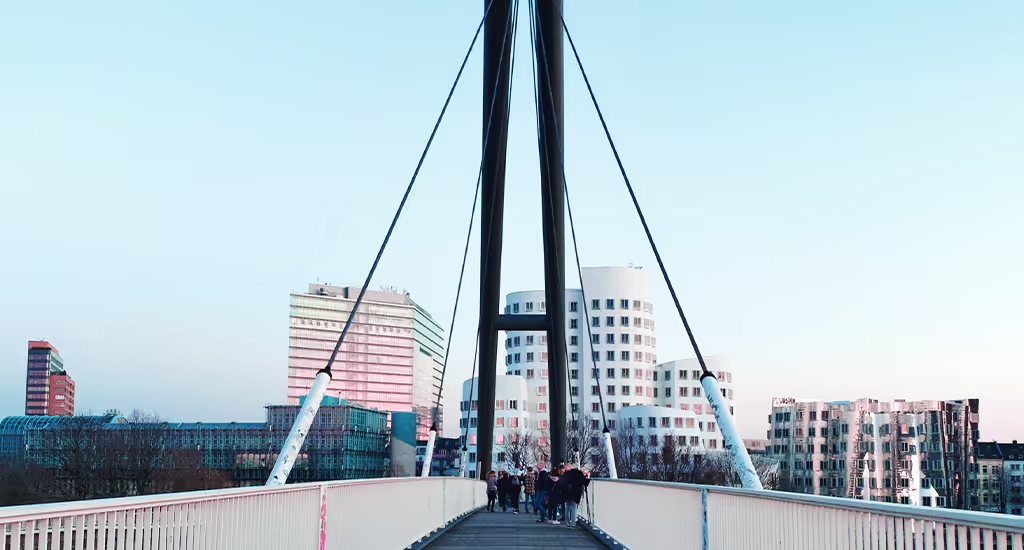
Join us at Temperature Control & Logistics in Düsseldorf

Meet our people: Quality Engineer, Akanksha Sharma
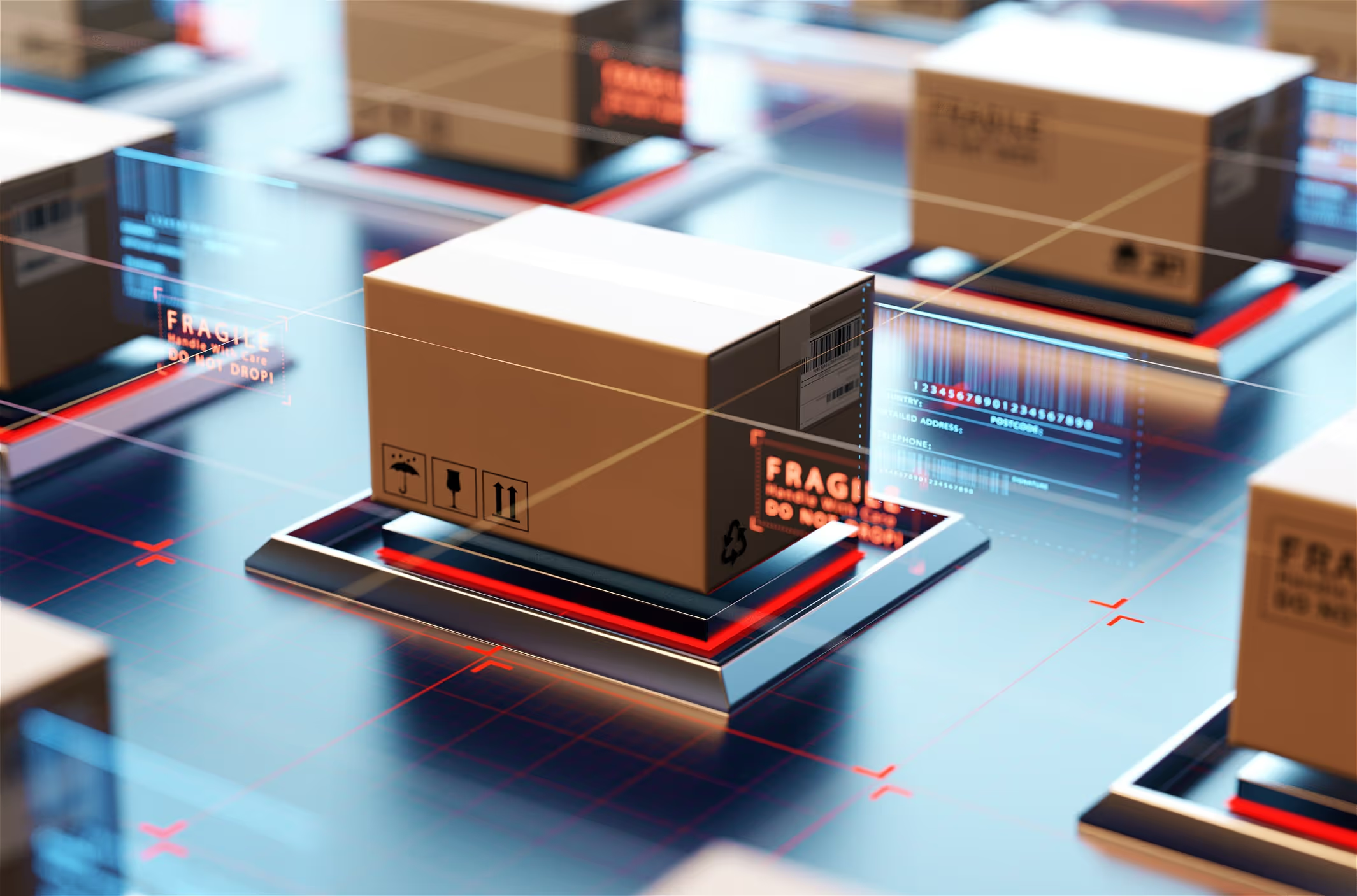
Is your supply chain ready for a digital transformation?
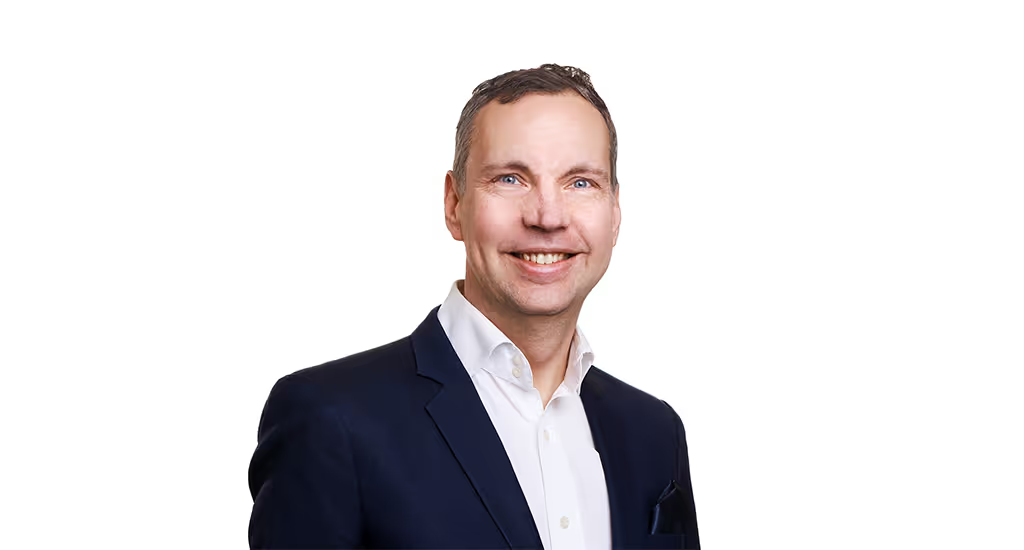
Q&A with Claes Kalderén: Our European Sales Manager
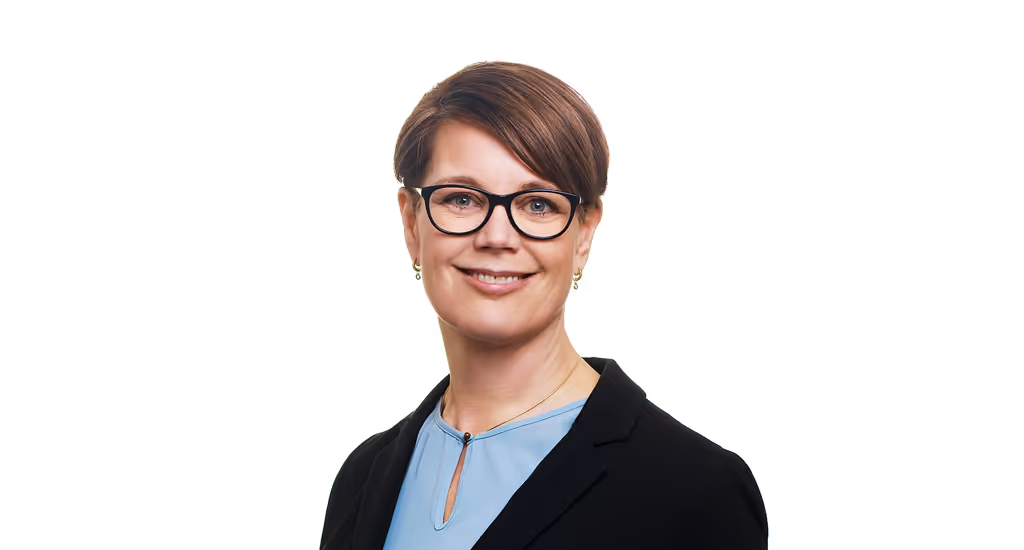
Meet Johanna Eriksson, Chief Product Officer at TSS
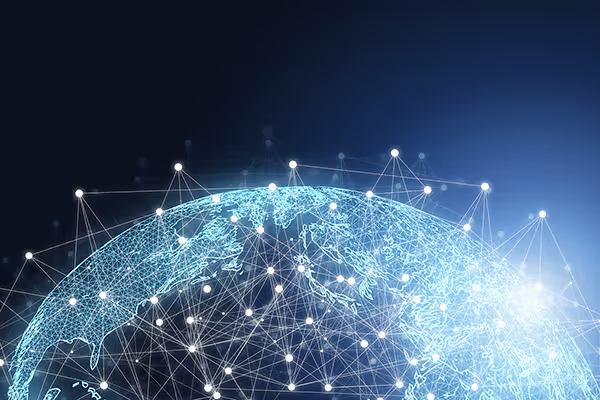
On-demand webinar: Maximize value with 2-way integrations in Clinical Trial Management
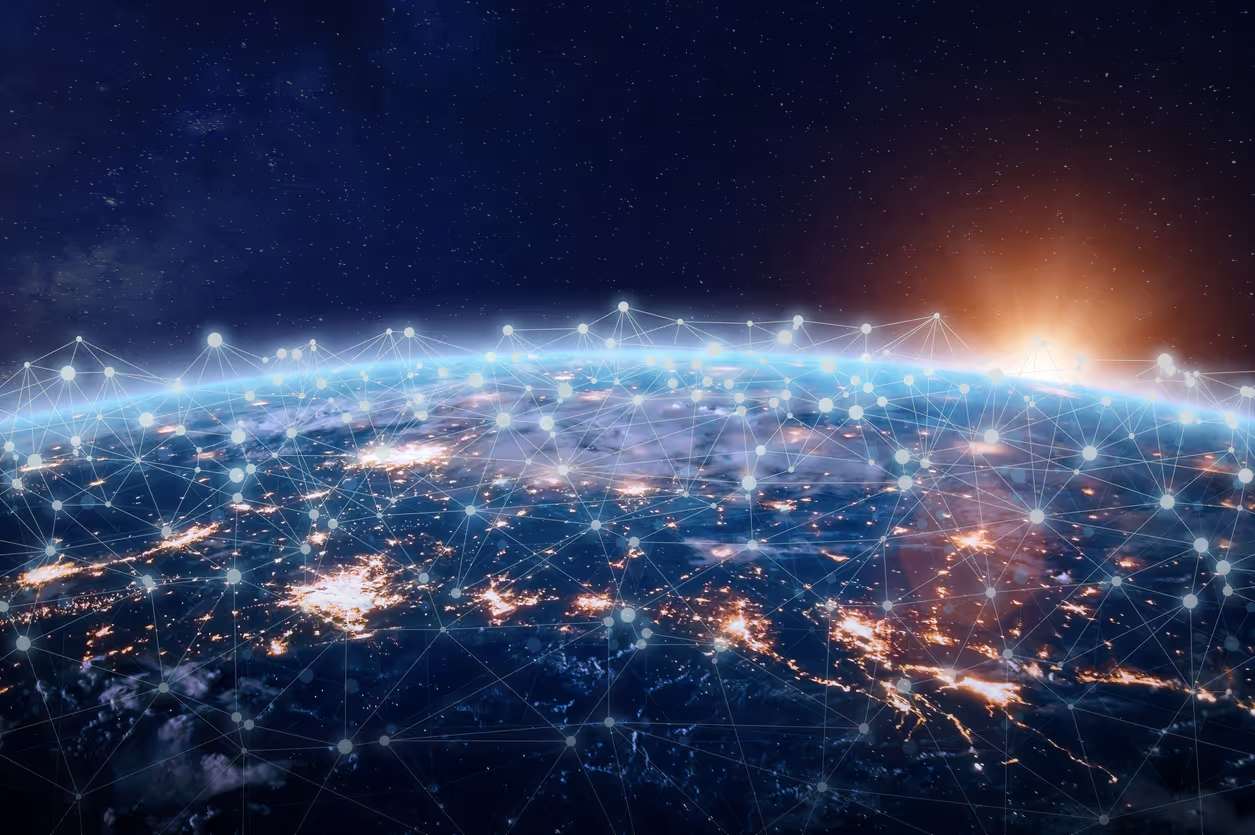
White paper: the future, today - the next generation of temperature monitoring
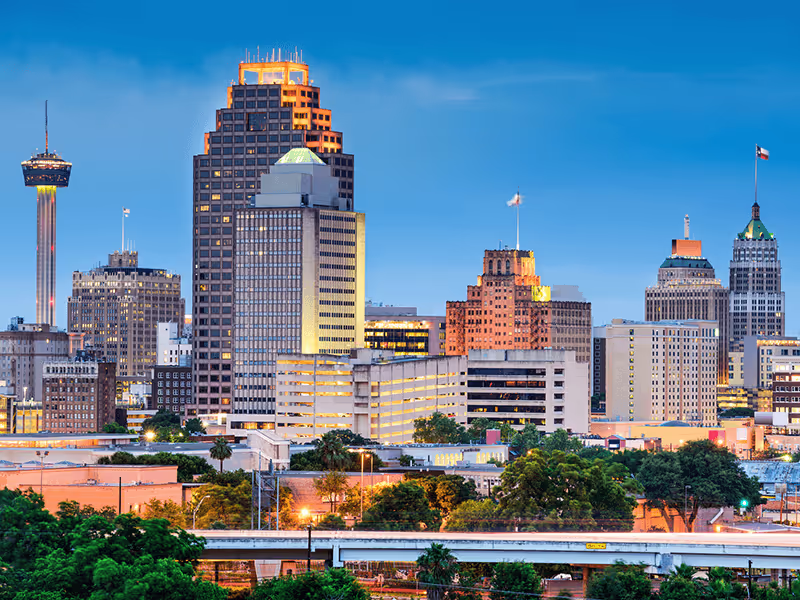
Join us at GCSC US 2022
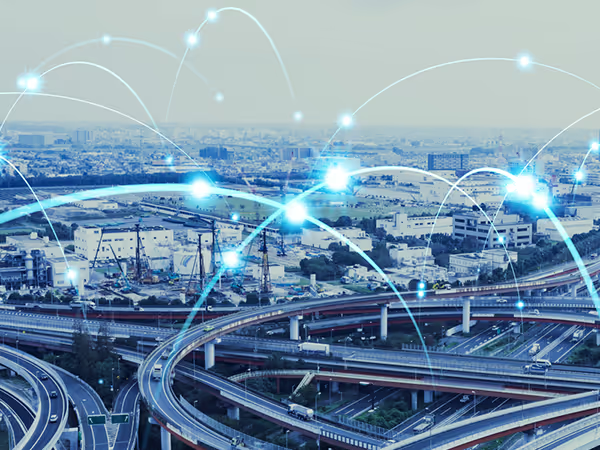
Guide: The road to digital success in temperature monitoring
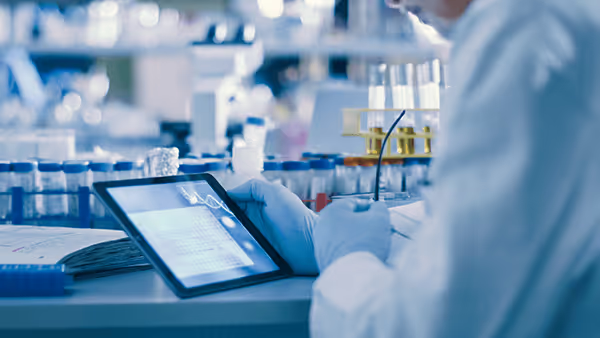
On-demand webinar: New approaches to automating temperature management in clinical trials
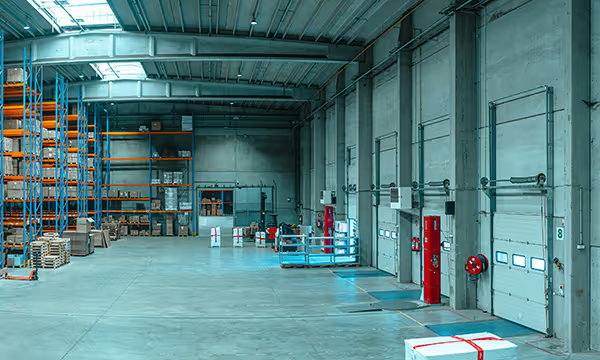
End-to-end visibility is the key to creating more efficient, cost-effective, and sustainable pharmaceutical supply chains
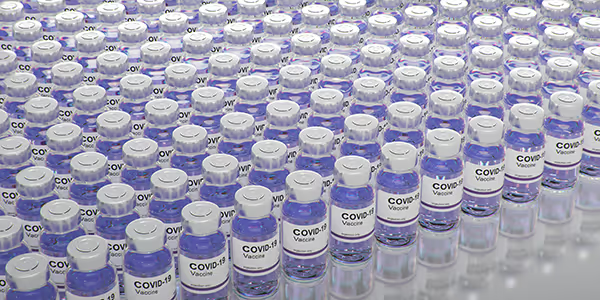
White paper: The next step to automating clinical trials
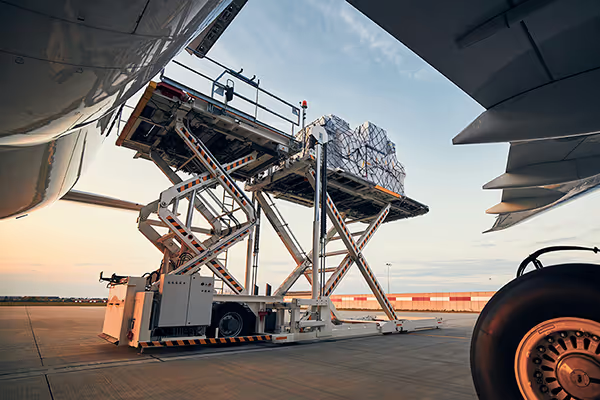
Getting the full value out of your supply chain temperature data
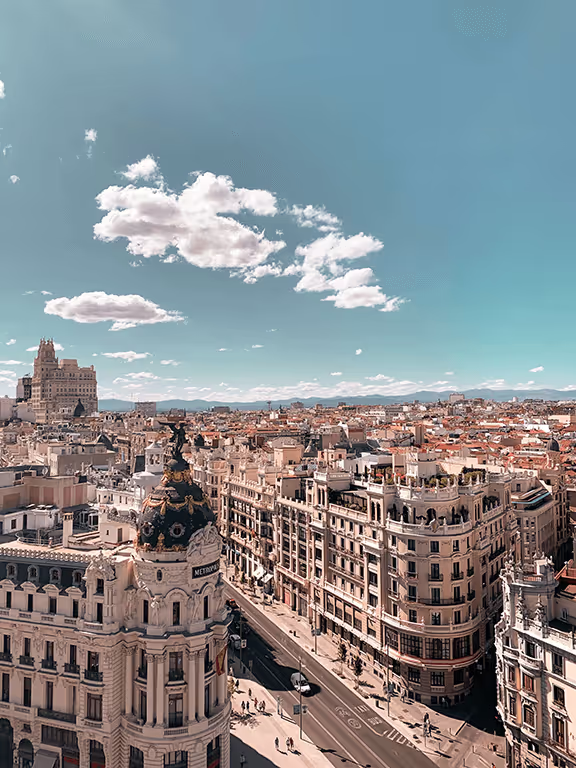
Join us at Clinical Trial Supply Europe 2022
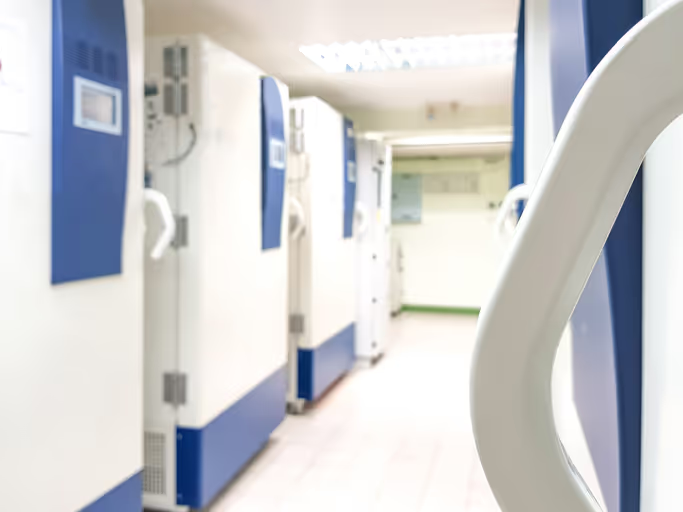
4 things to know about TSS new BLE data loggers
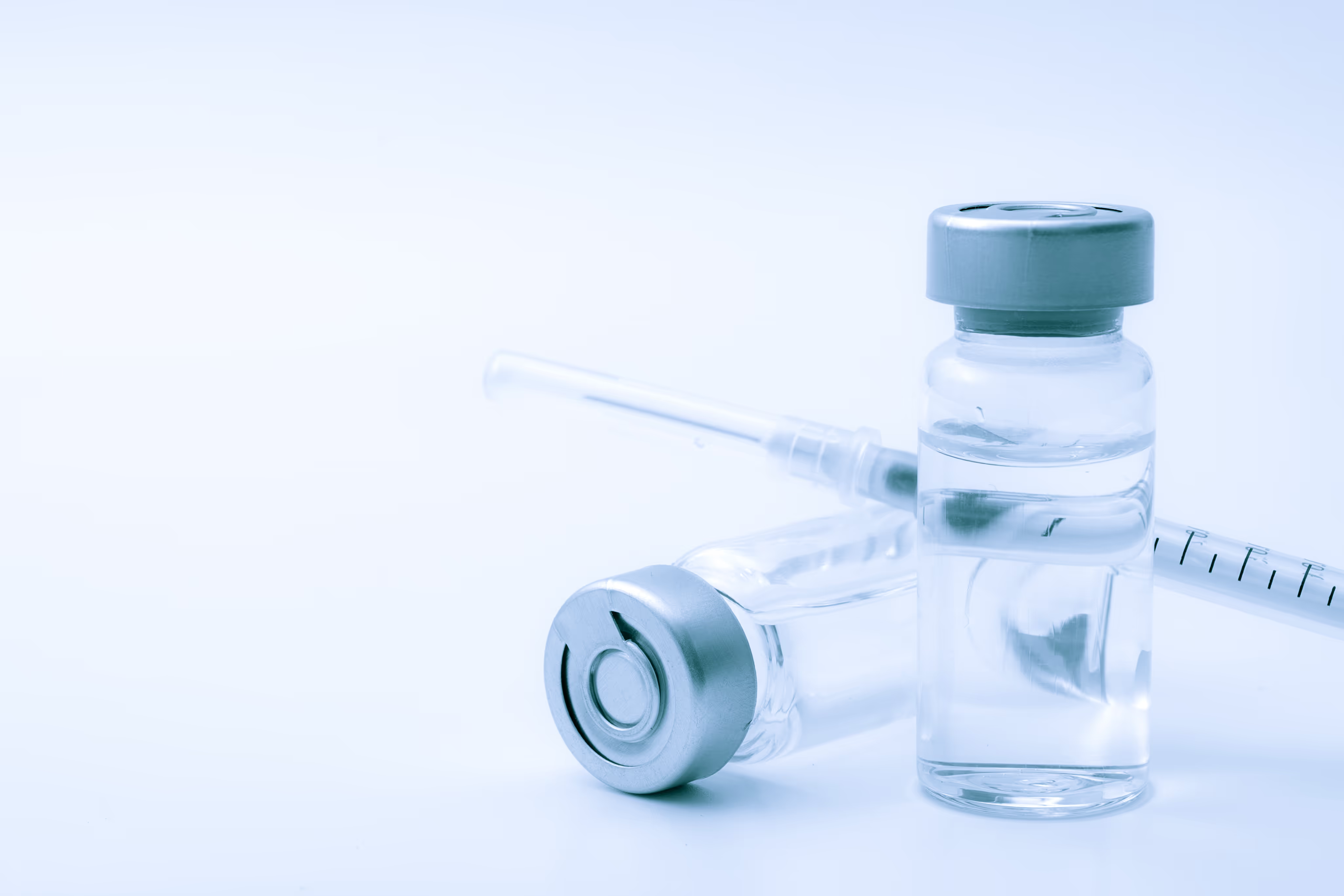
The year in review: TSS’s most-read blog articles of 2021
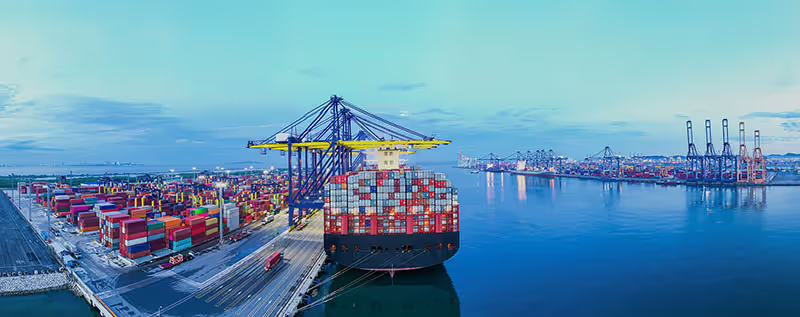
Logipharma report: A fast-track learning exercise in pharma supply chain innovation
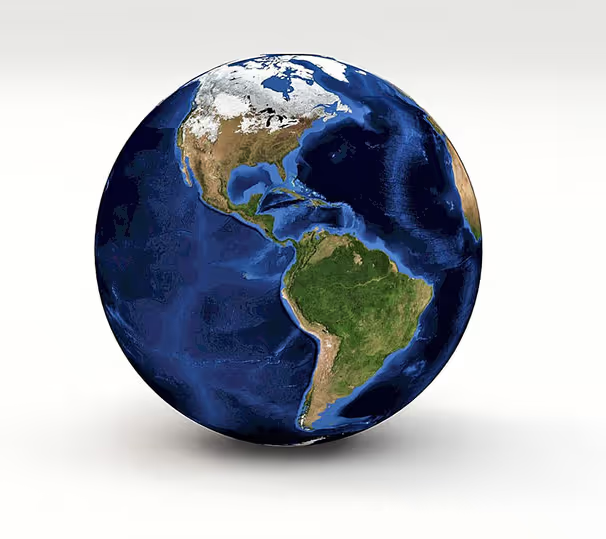
Temperature management – from local to global
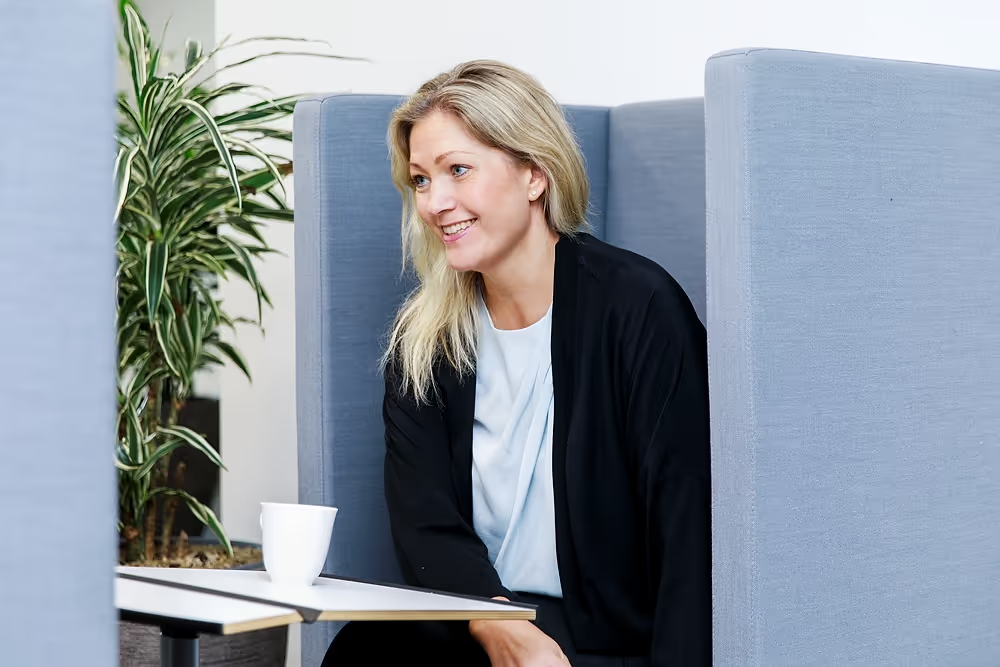
Meet Nina Nilsson, Chief Revenue Officer at TSS
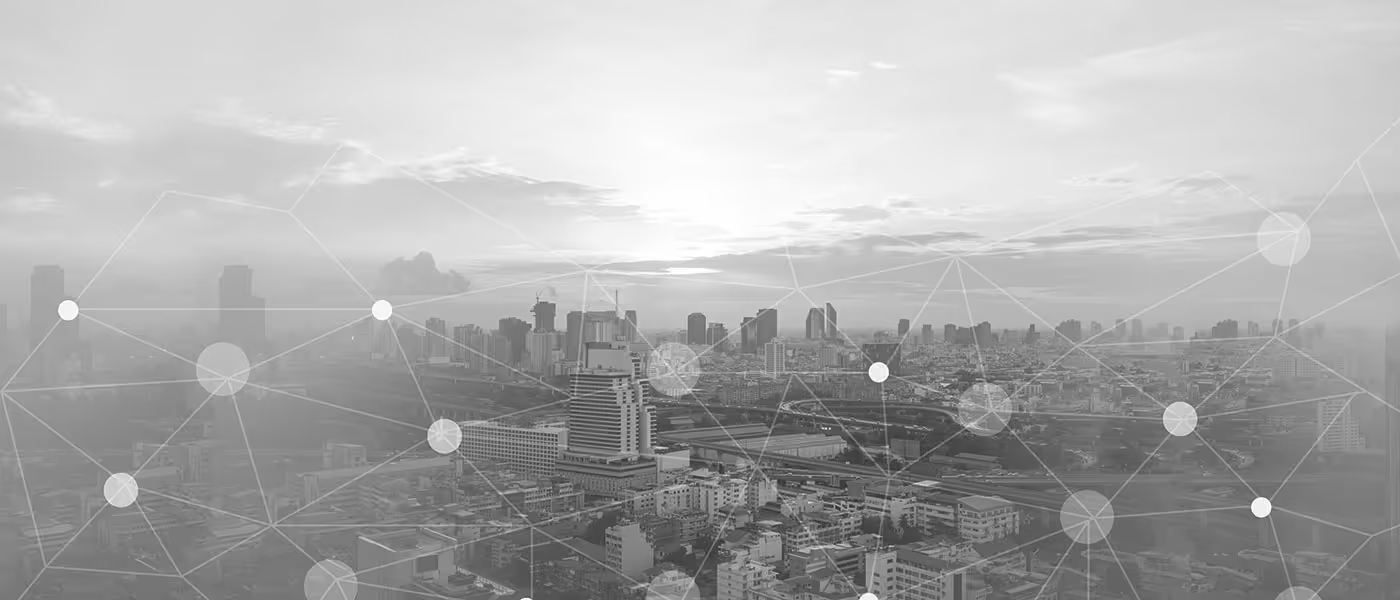
The Buyer’s guide to real-time temperature monitoring
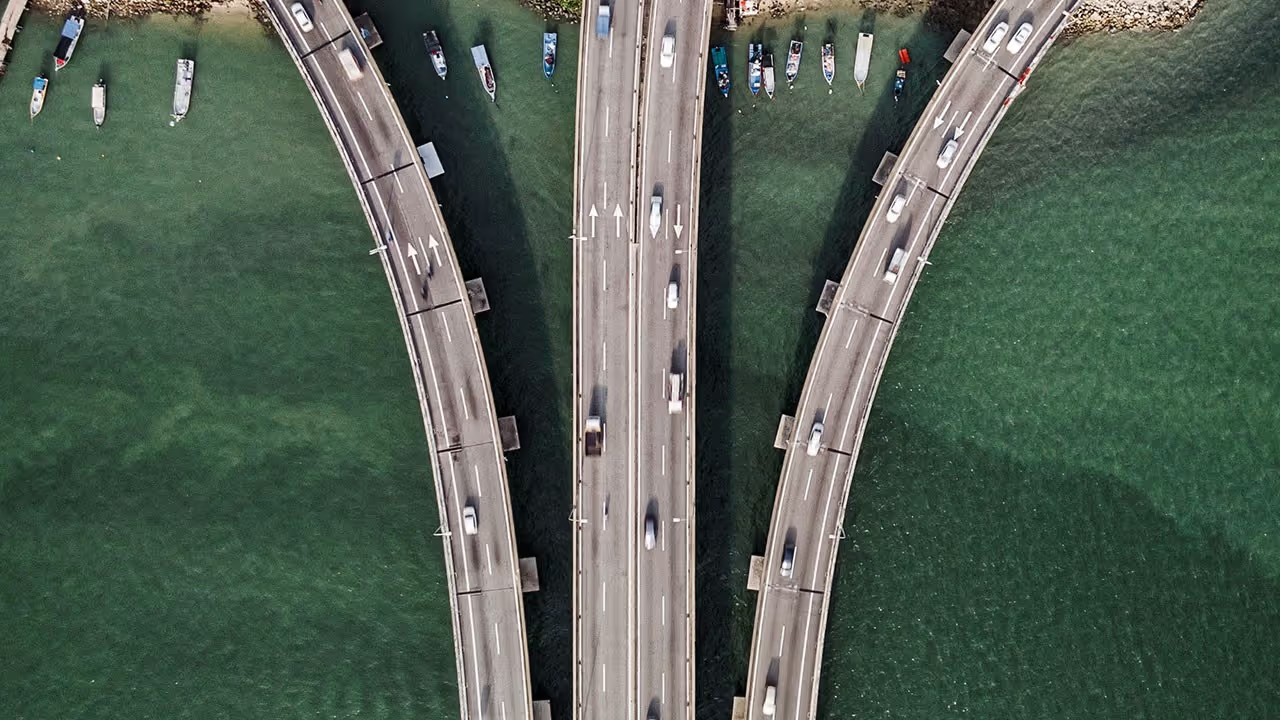
Increasing visibility with a proactive supply chain
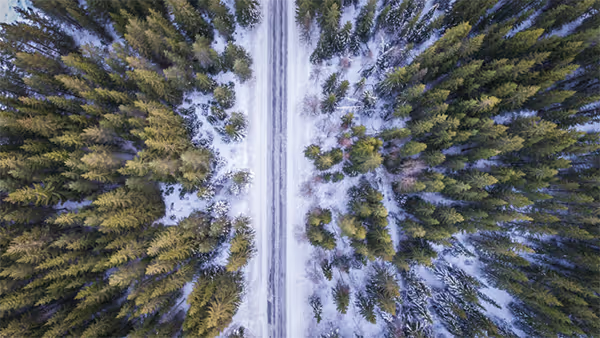
On-demand webinar: Master your supply chain with end-to-end visibility
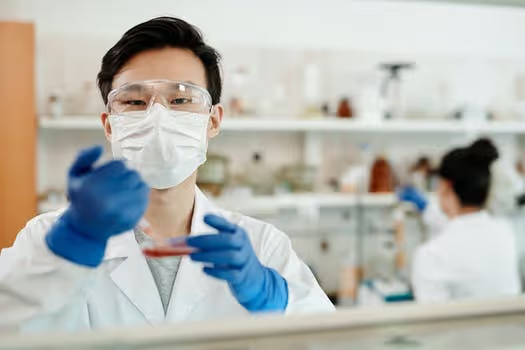
On-demand webinar: Excursion Management – From days to seconds
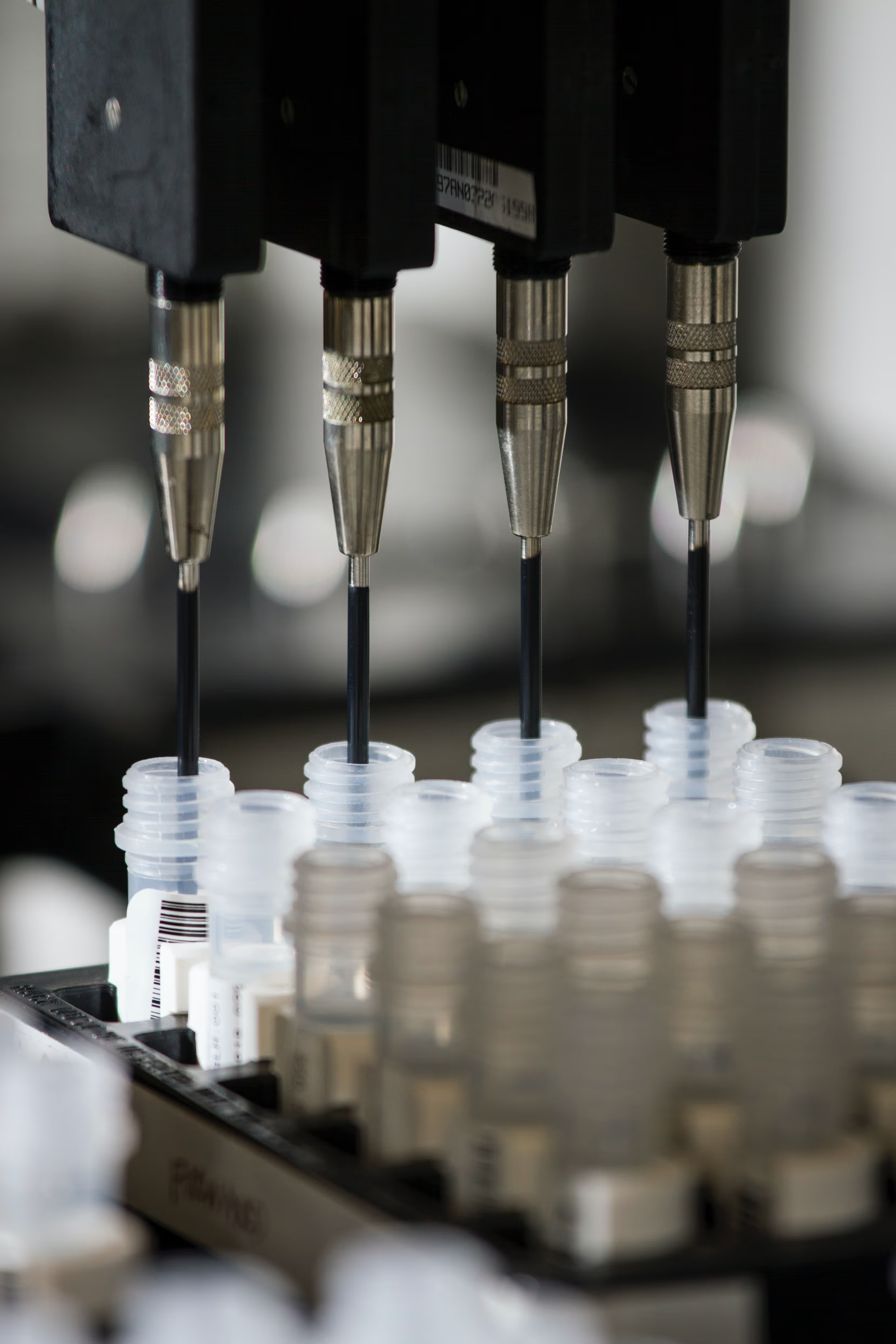
Turn days into seconds at clinical sites worldwide
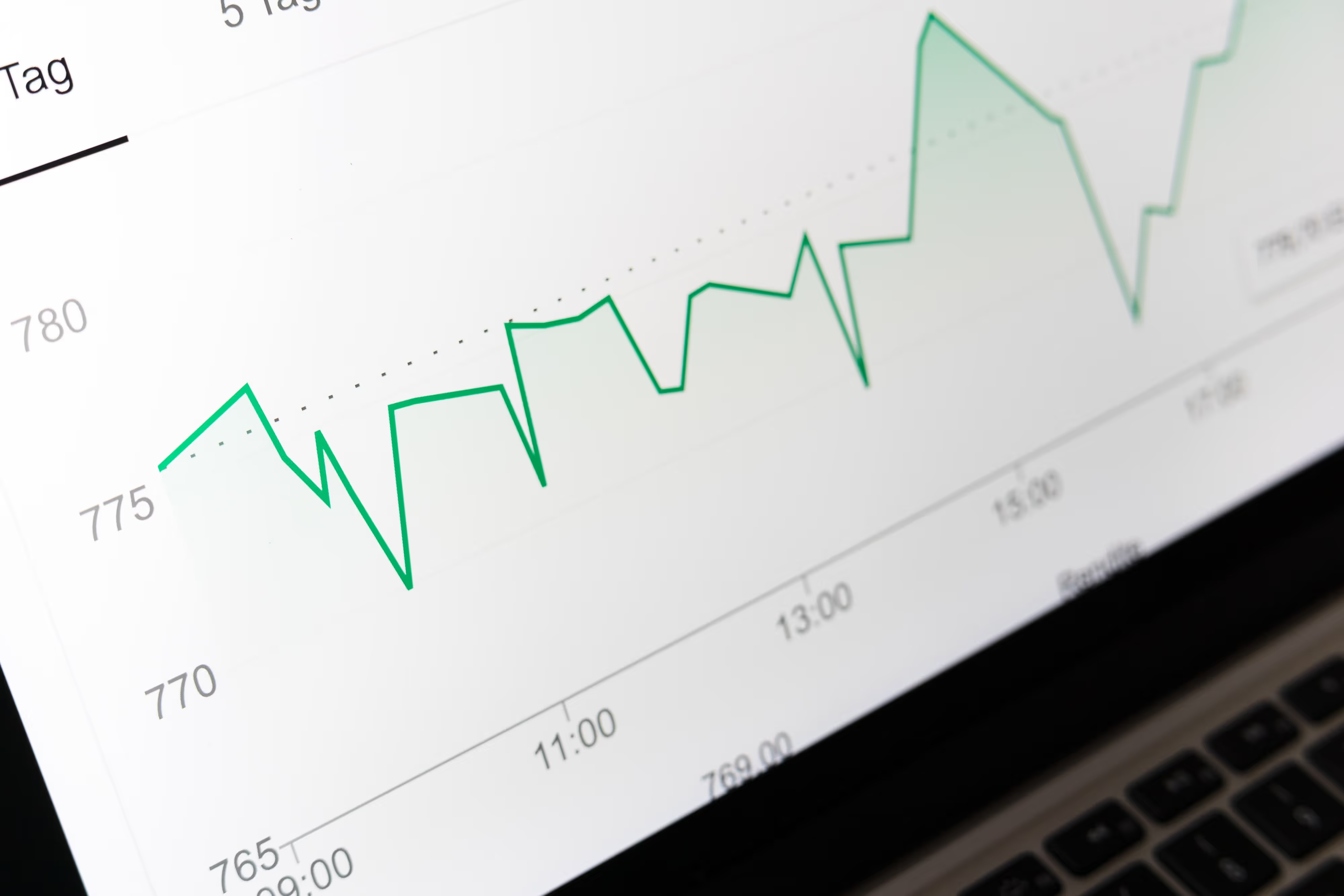
On-demand webinar: Digitalization and its impact on the pharma supply chain
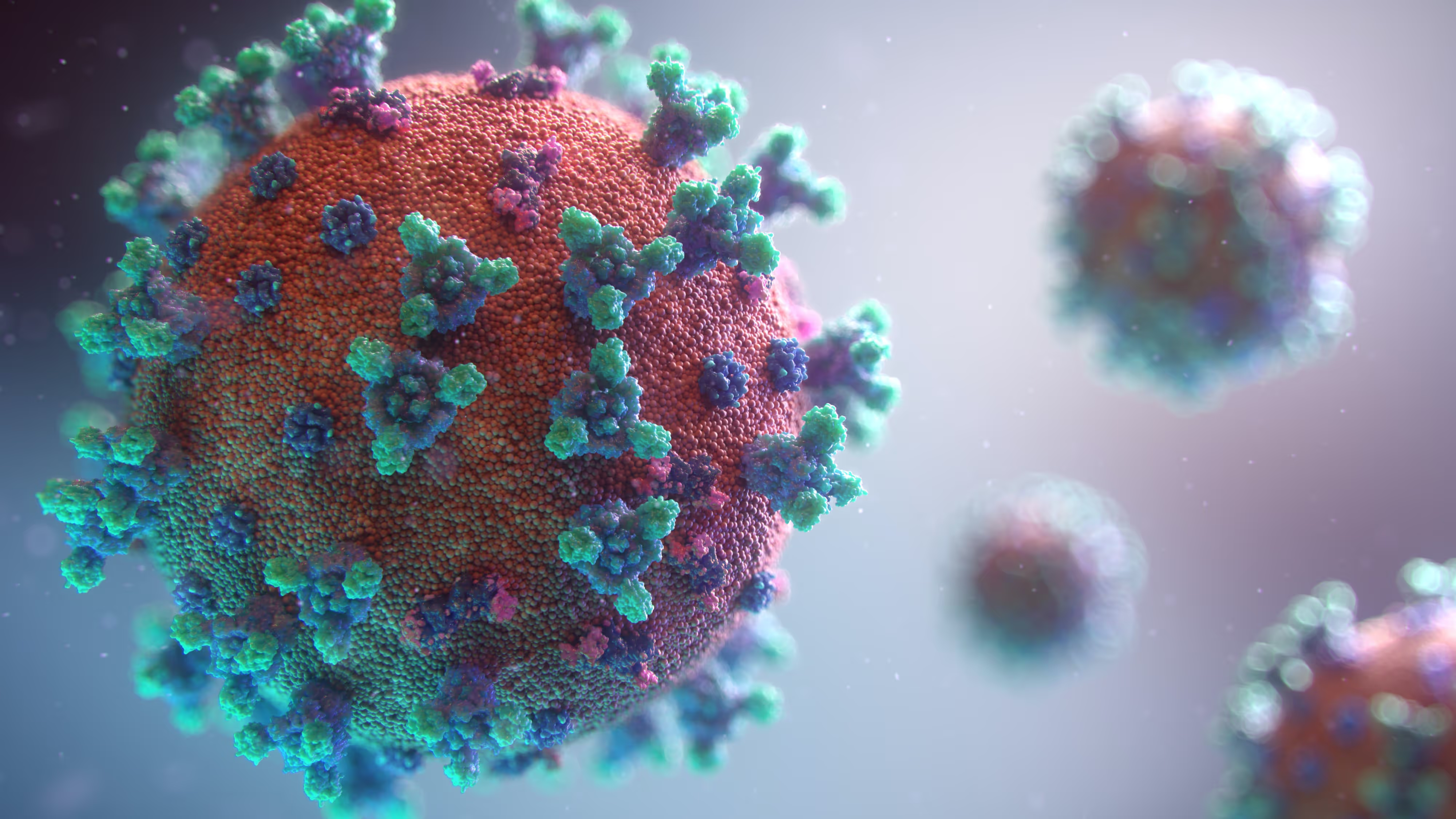
Covid-19 situation
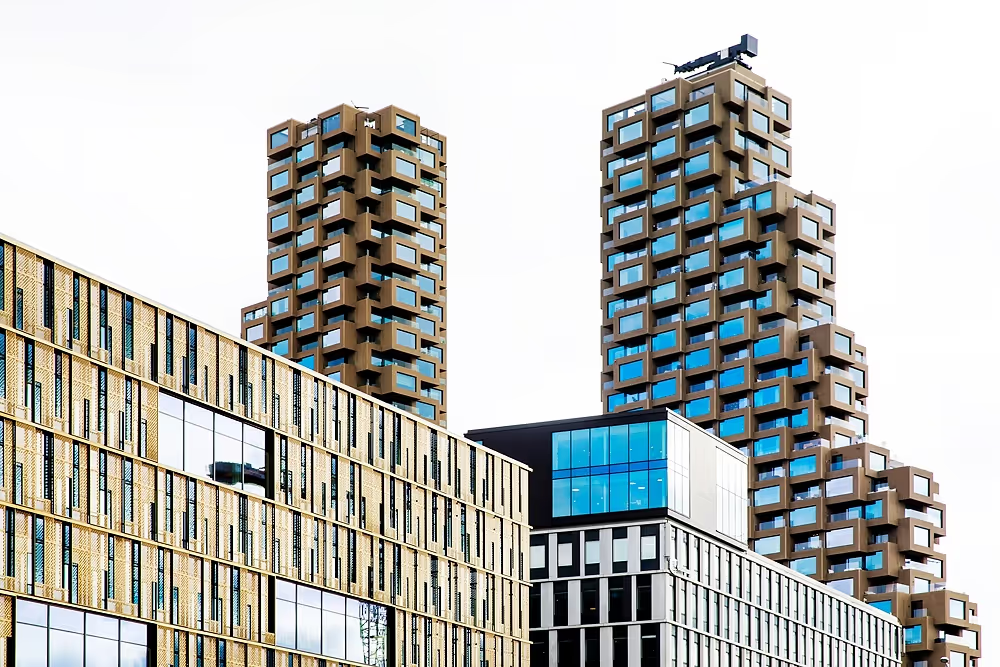
Innovation flourishes when different perspectives meet
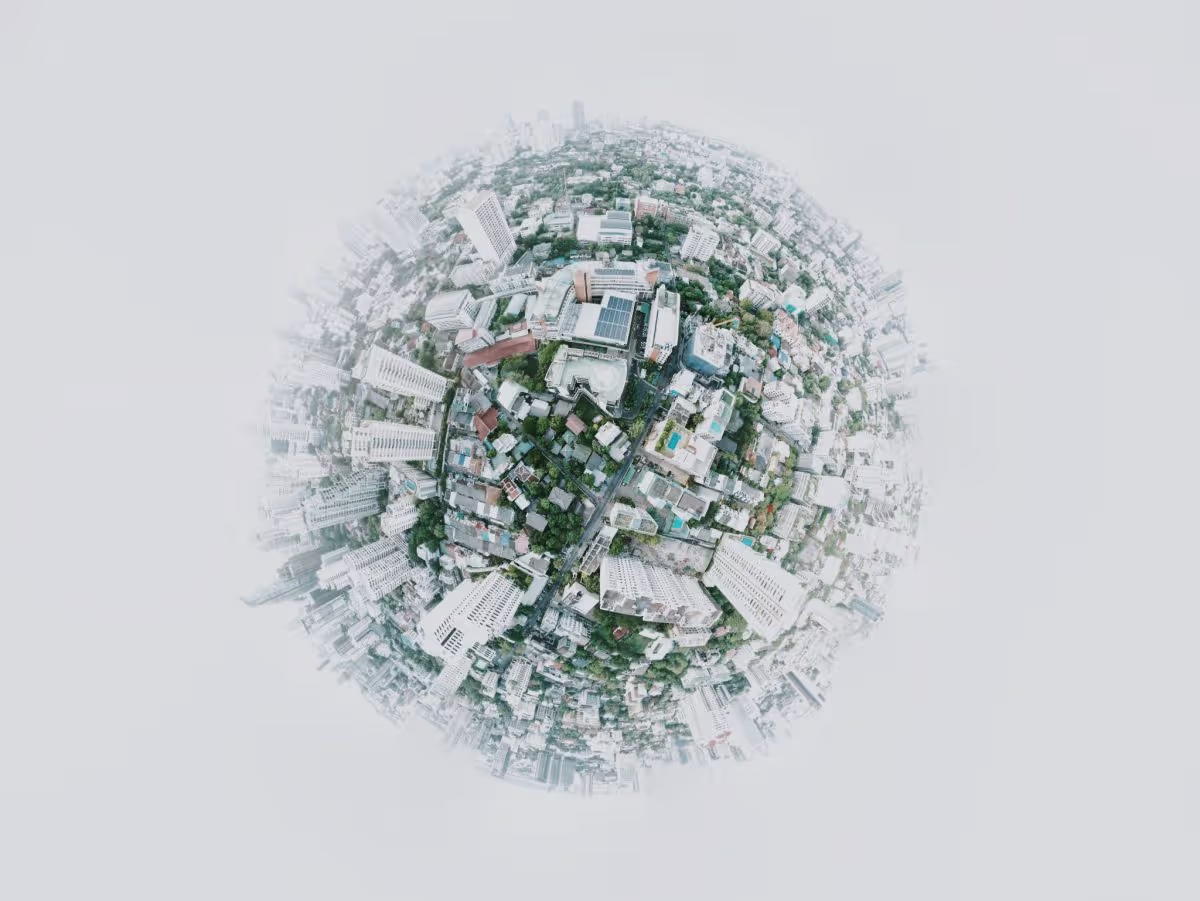
Exploring the solution to a global question
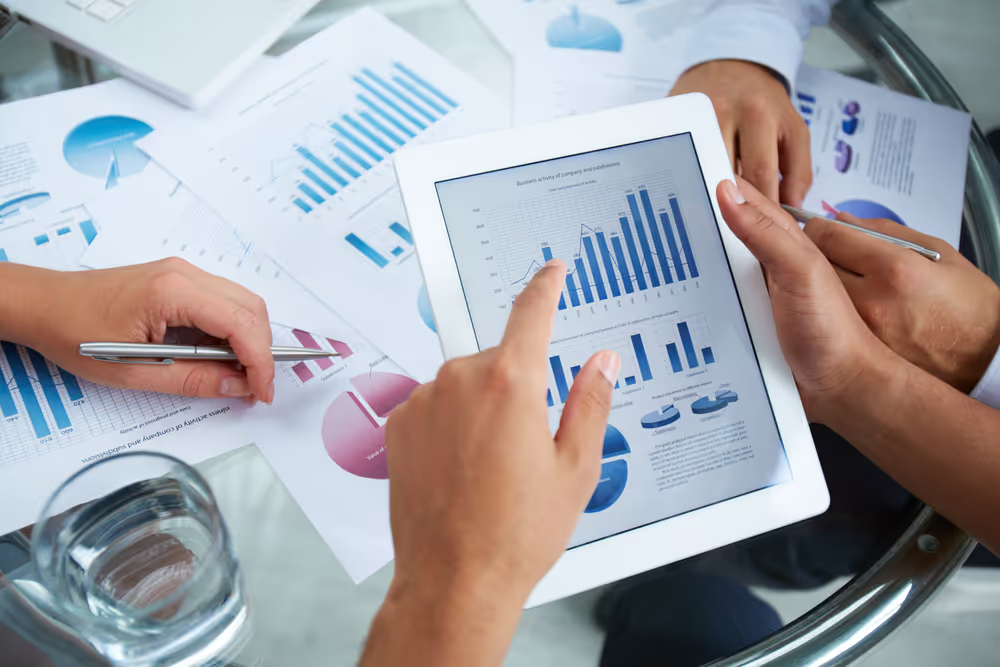
How live access to GxP data support supply chain best practices?
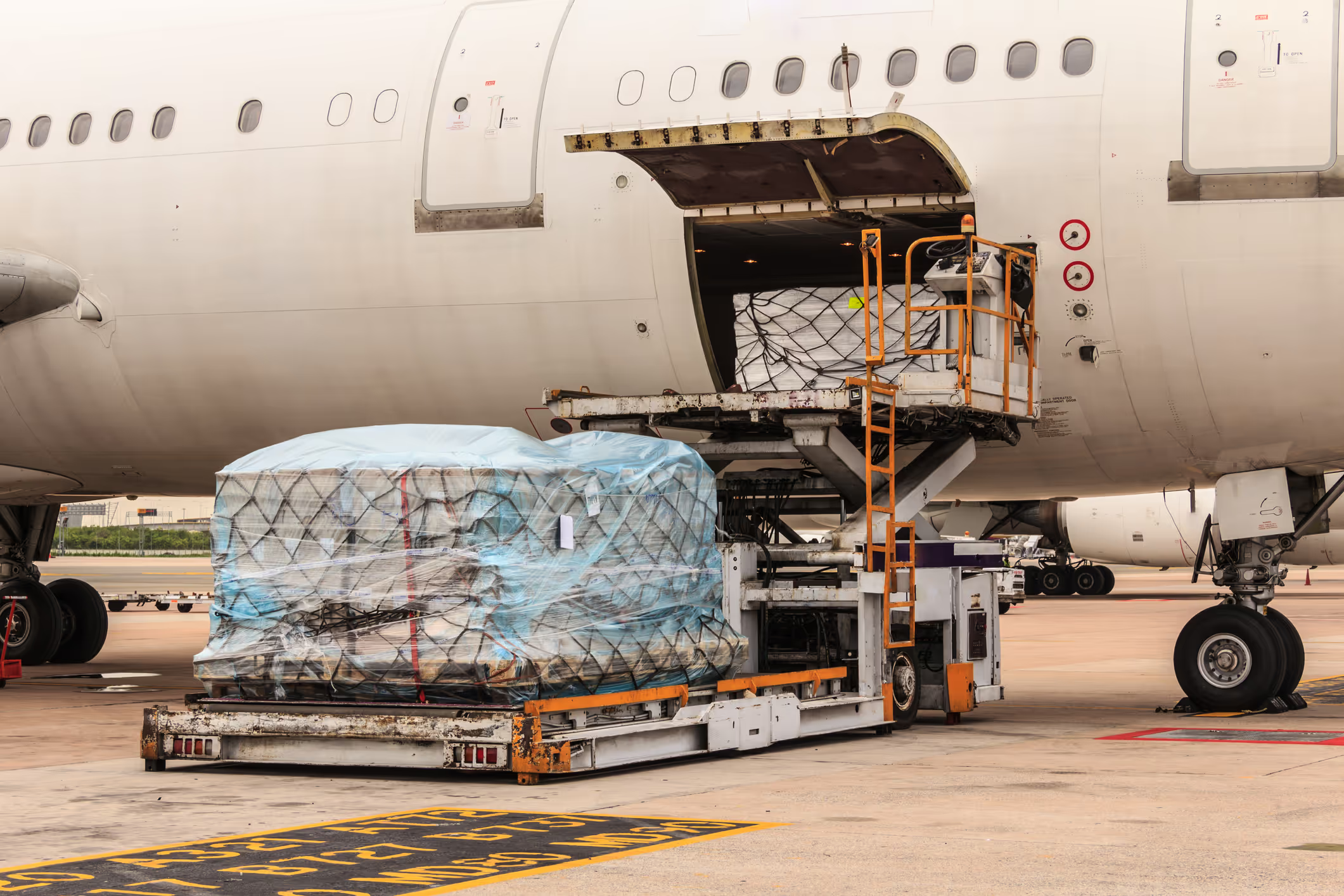
On time and in full, when it matters most
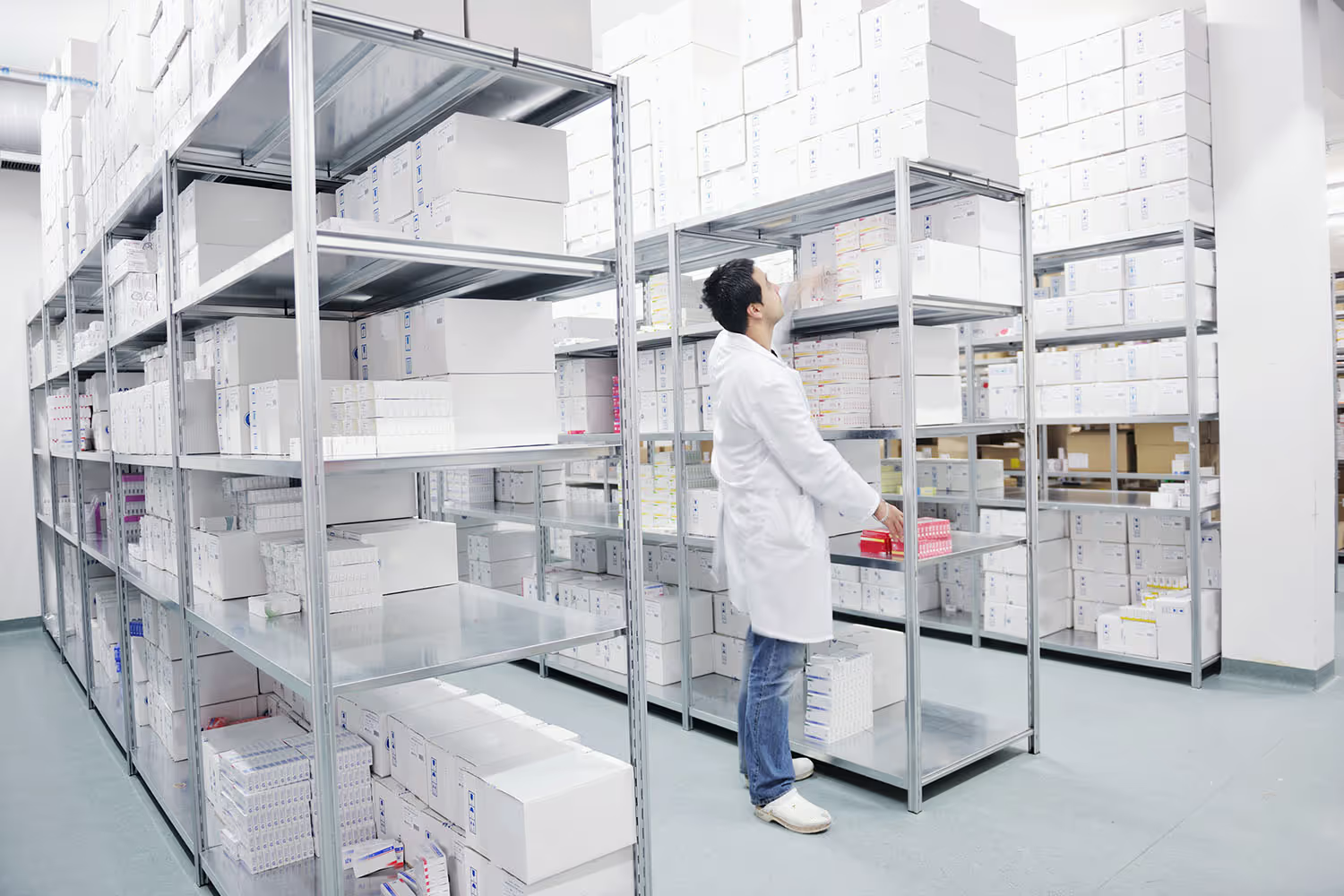
5 benefits of adopting digital temperature monitoring solutions
.avif)
Reducing excursion evaluation time from days to seconds
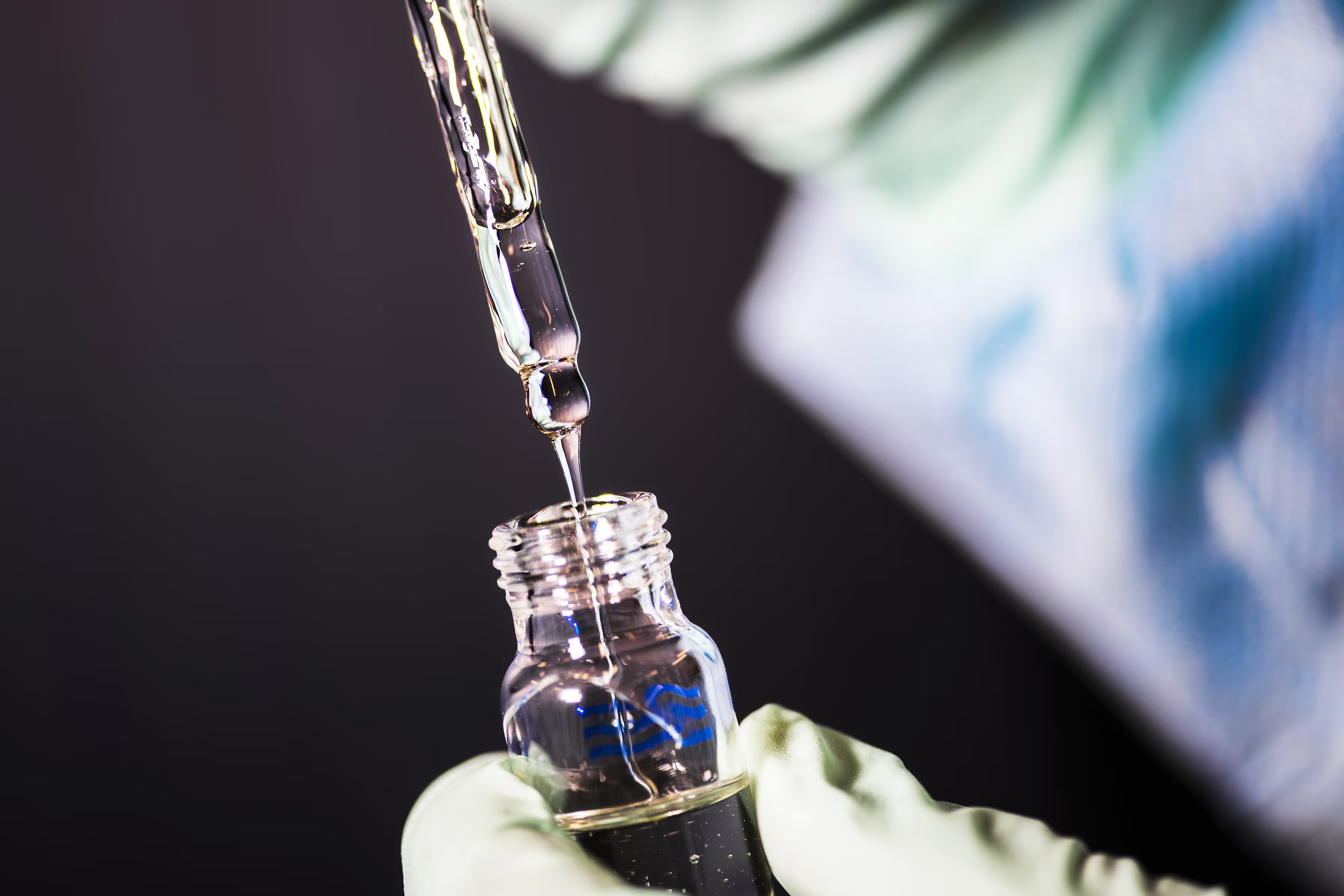
Making the pharma industry future-proof through supply chain digitalization
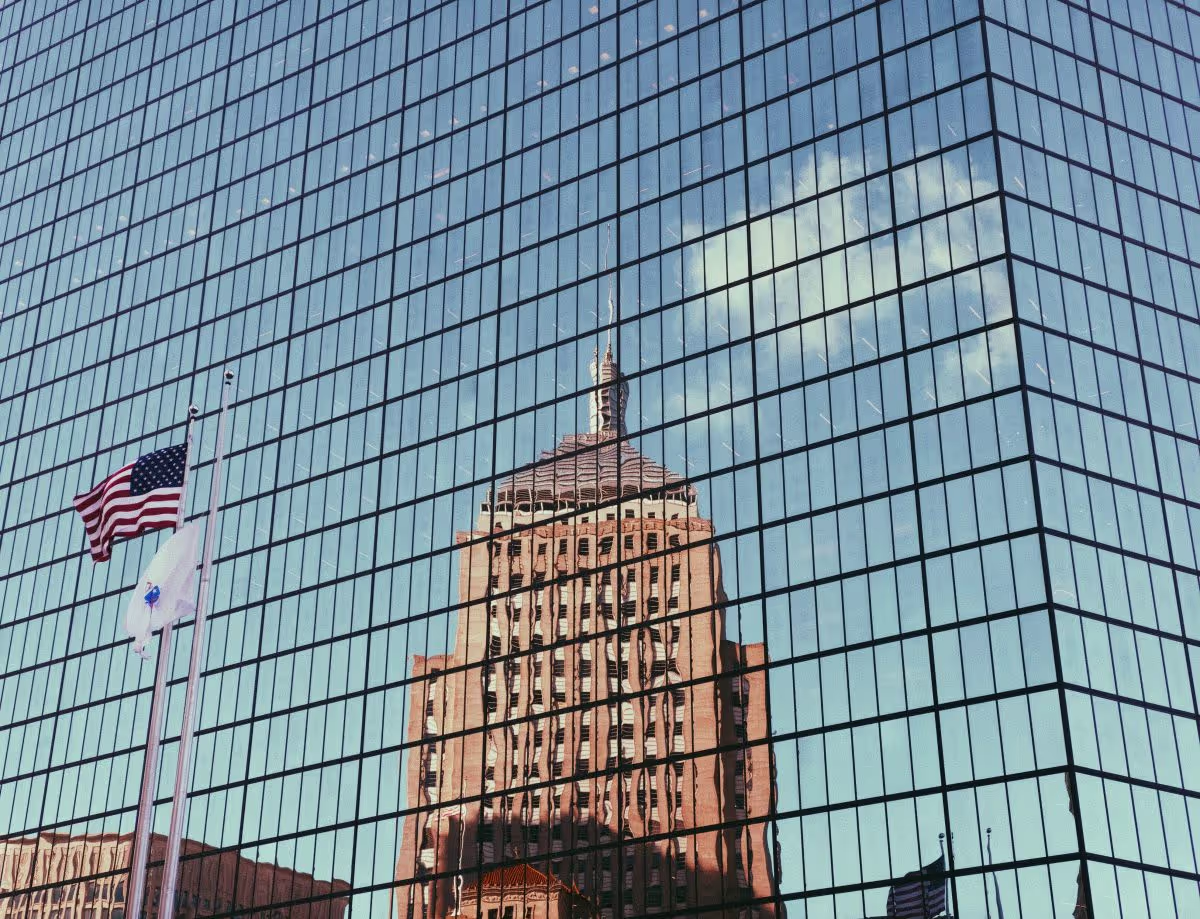
New opportunities on the horizon as TSS expands US operations
.avif)
On-demand webinar: A unified approach to clinical supply temperature management
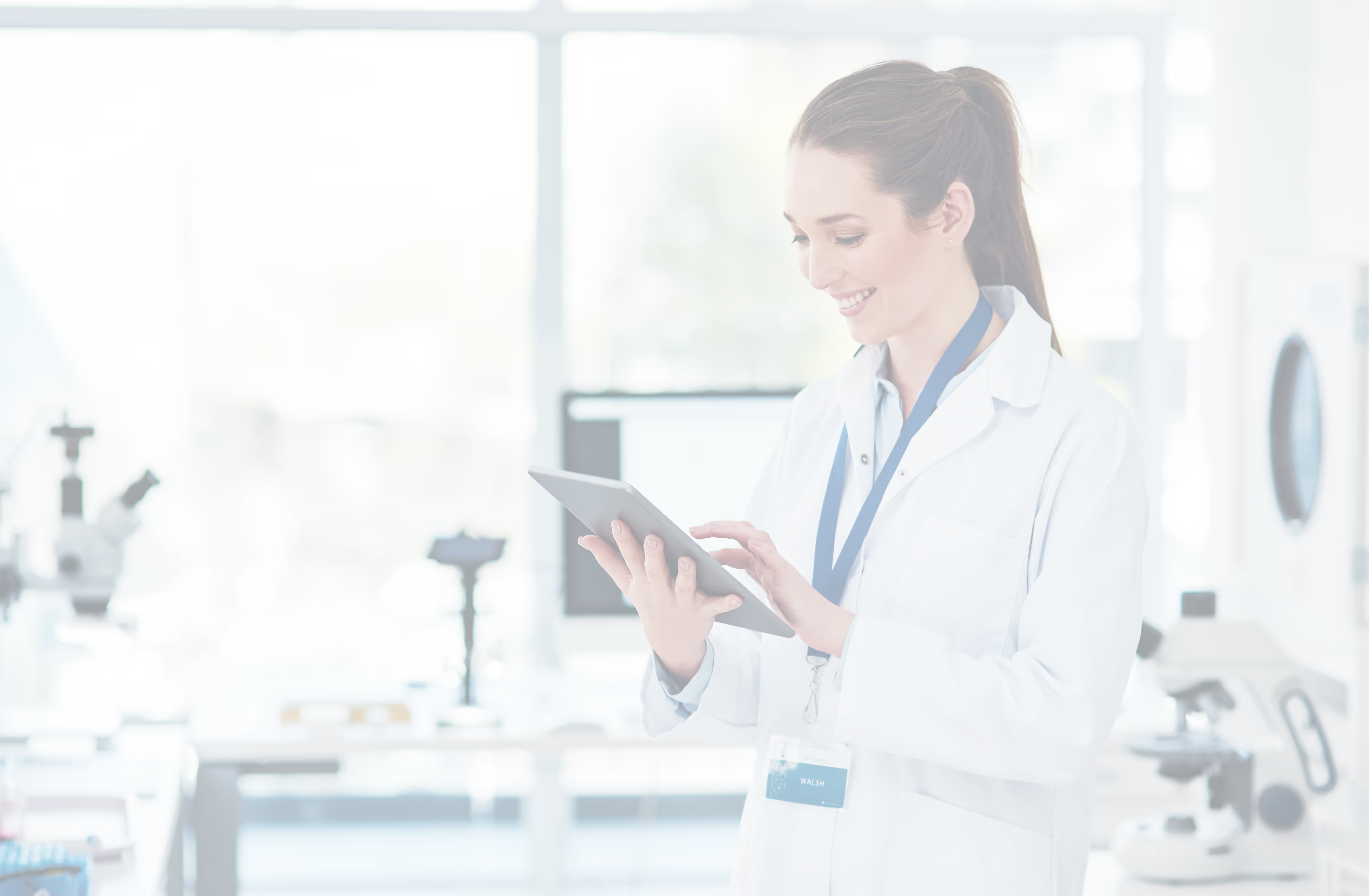
TSS Clinical Trials Digitalization User Forum 2021
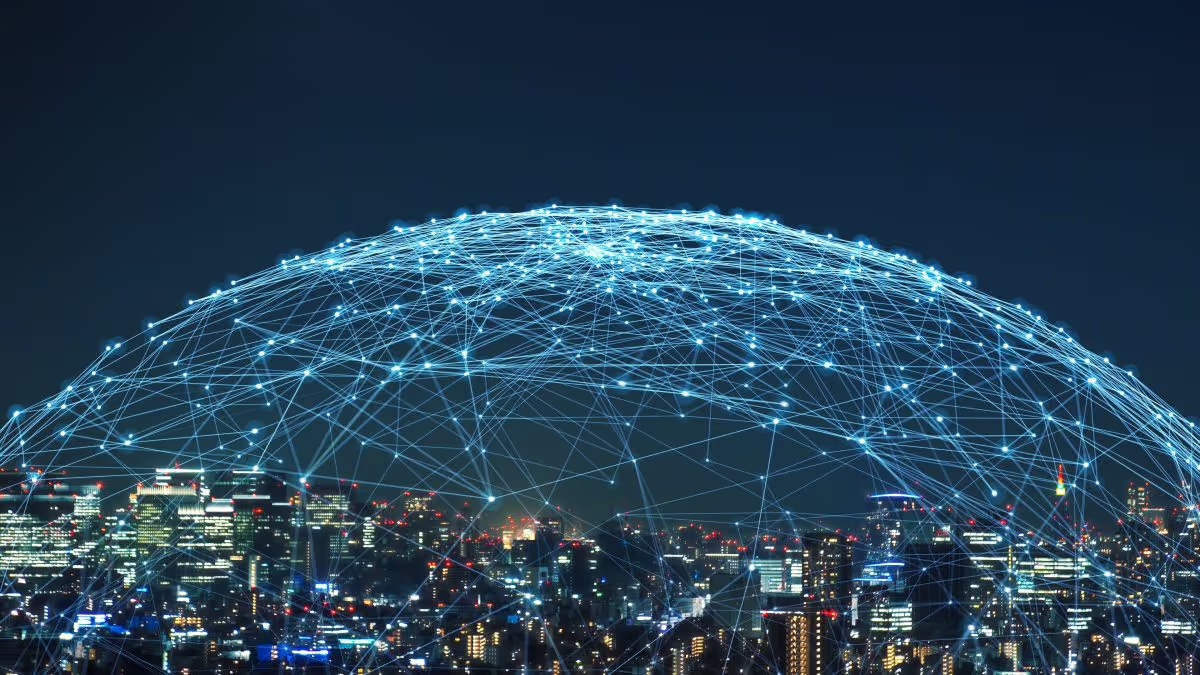
Which way is the wind blowing? The implications of cloud-based IoT on temperature monitoring in the life science supply chain
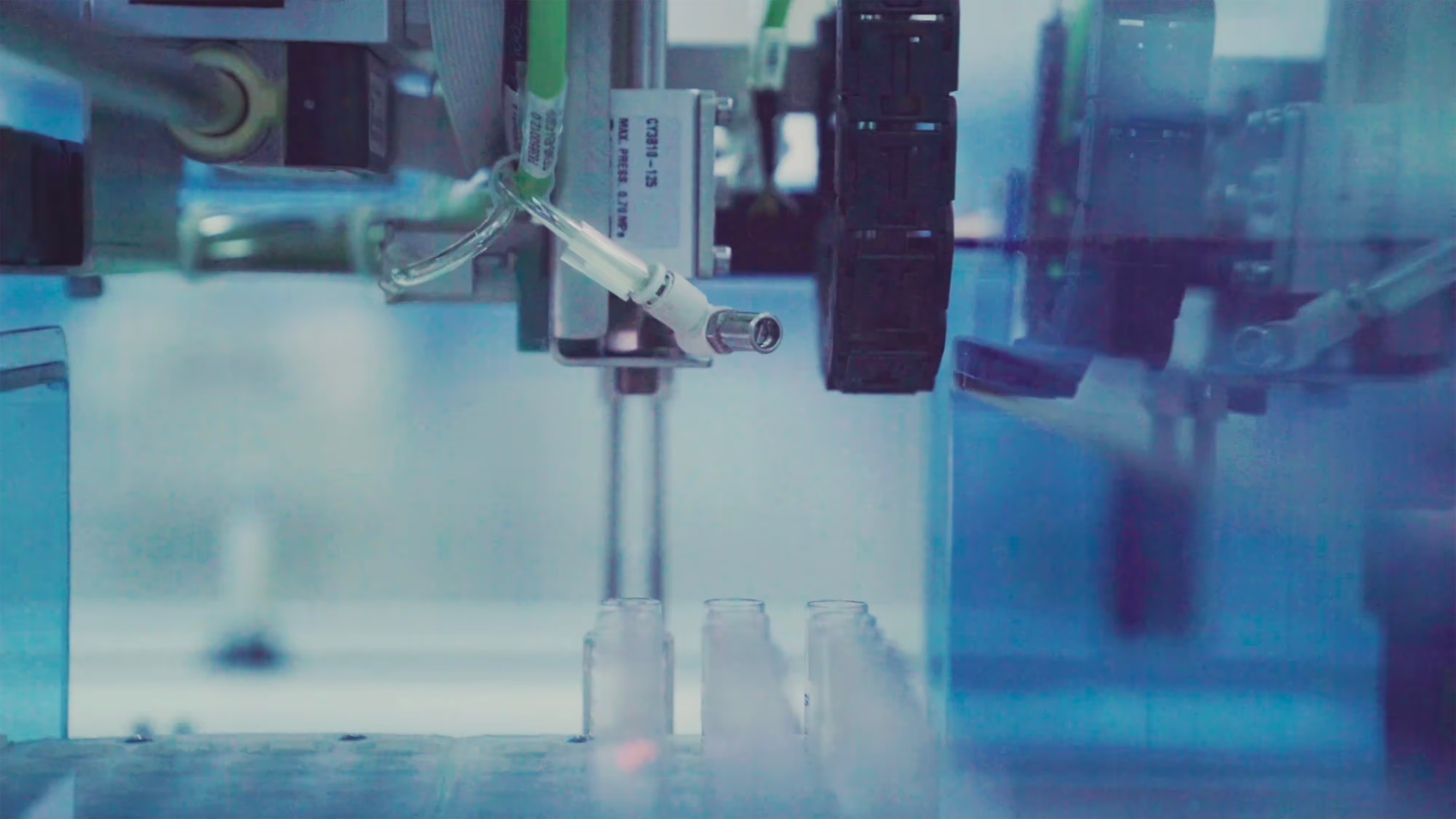
On-demand webinar: Monitoring multiple products with one temperature data logger
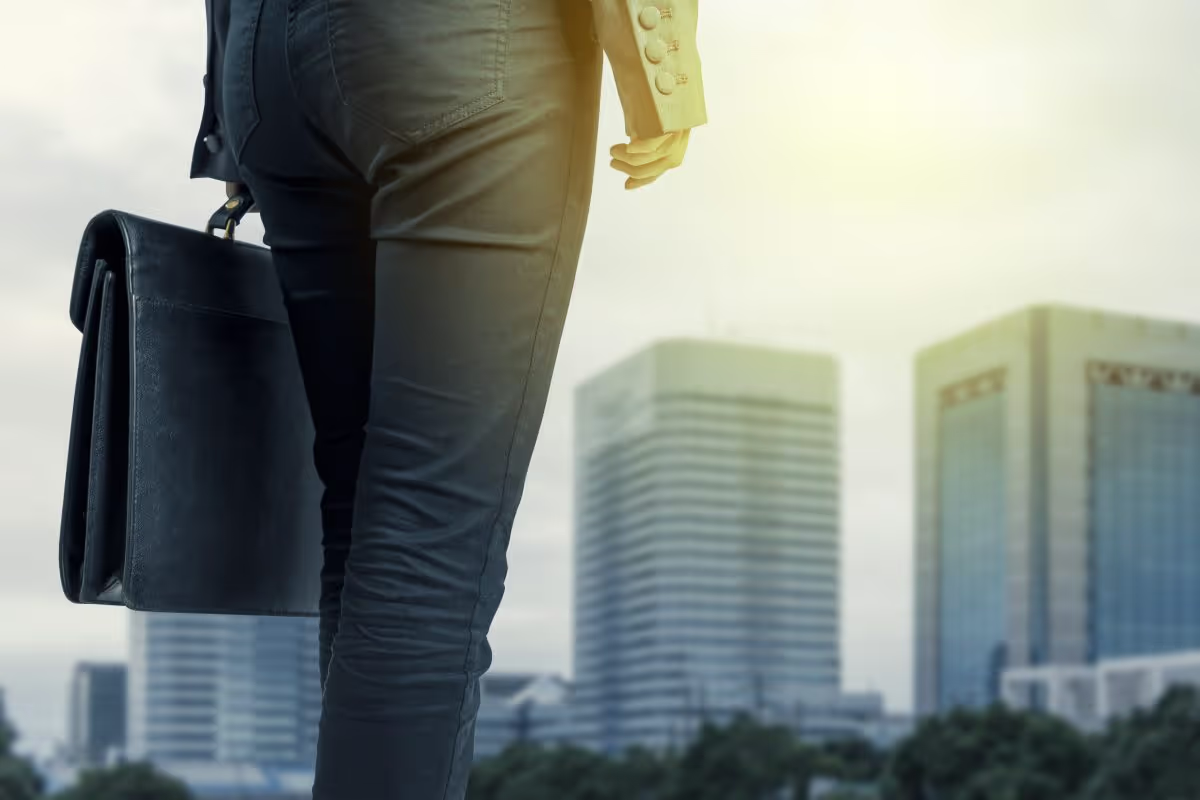
Women in executive positions: making a difference with International Women’s Day
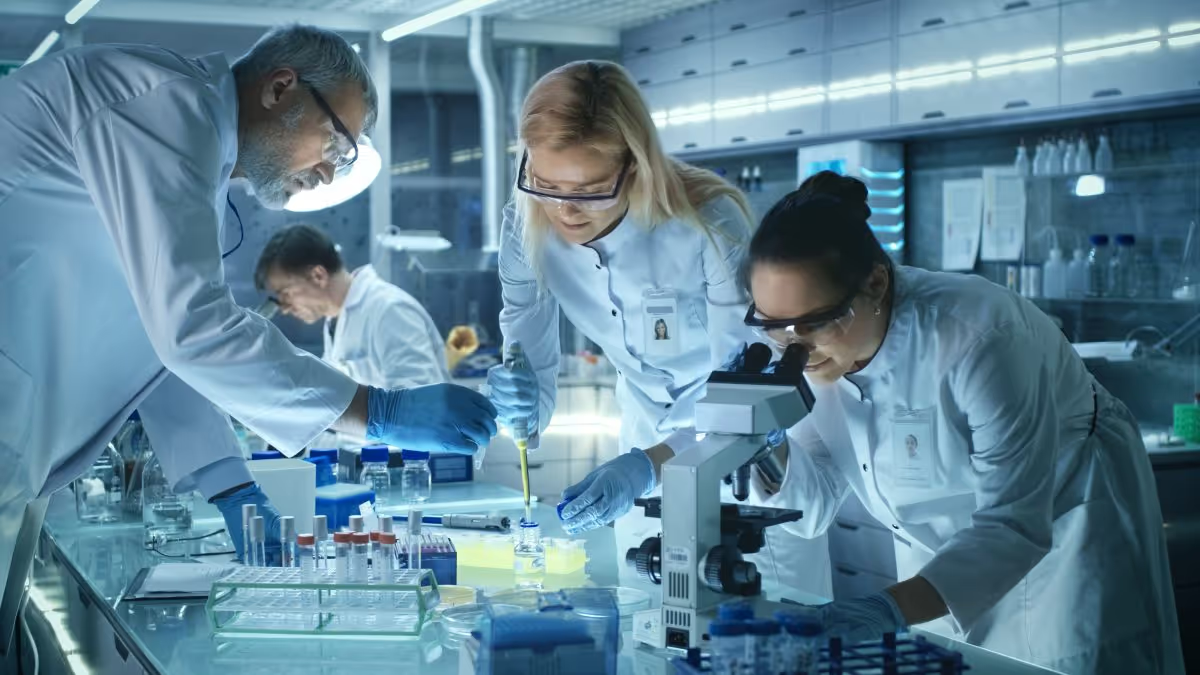
Automation is making temperature excursion management simpler and more efficient for clinical sites
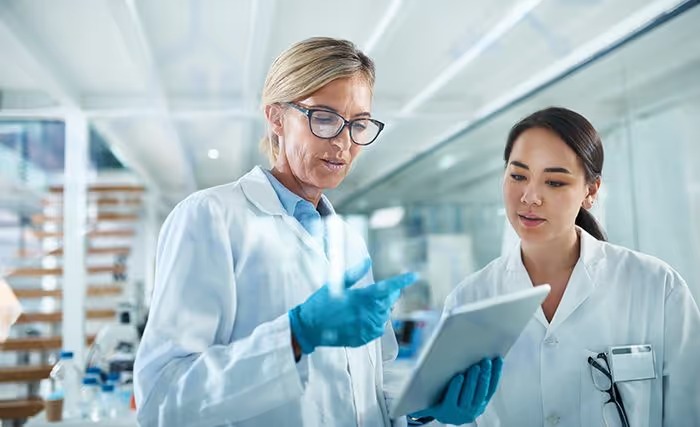
Mind the gap: the real-world impact of data gaps in clinical trials
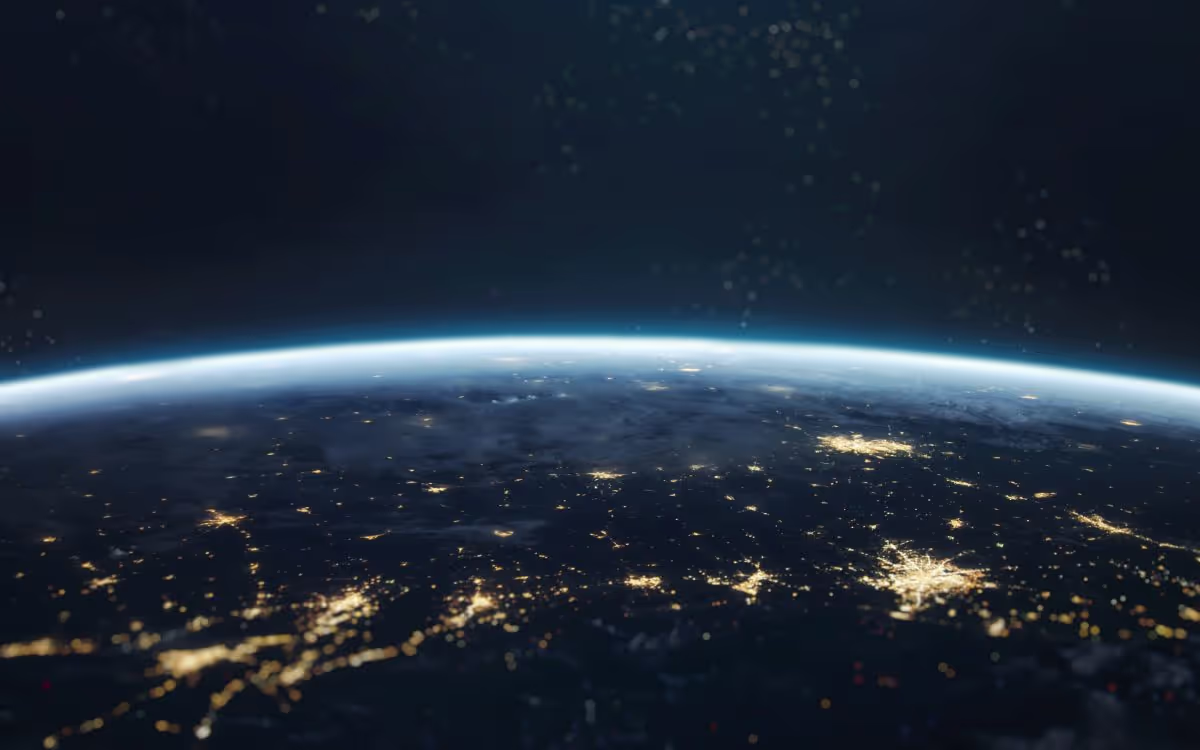
On-demand webinar: Introducing BLE technology for temperature monitoring
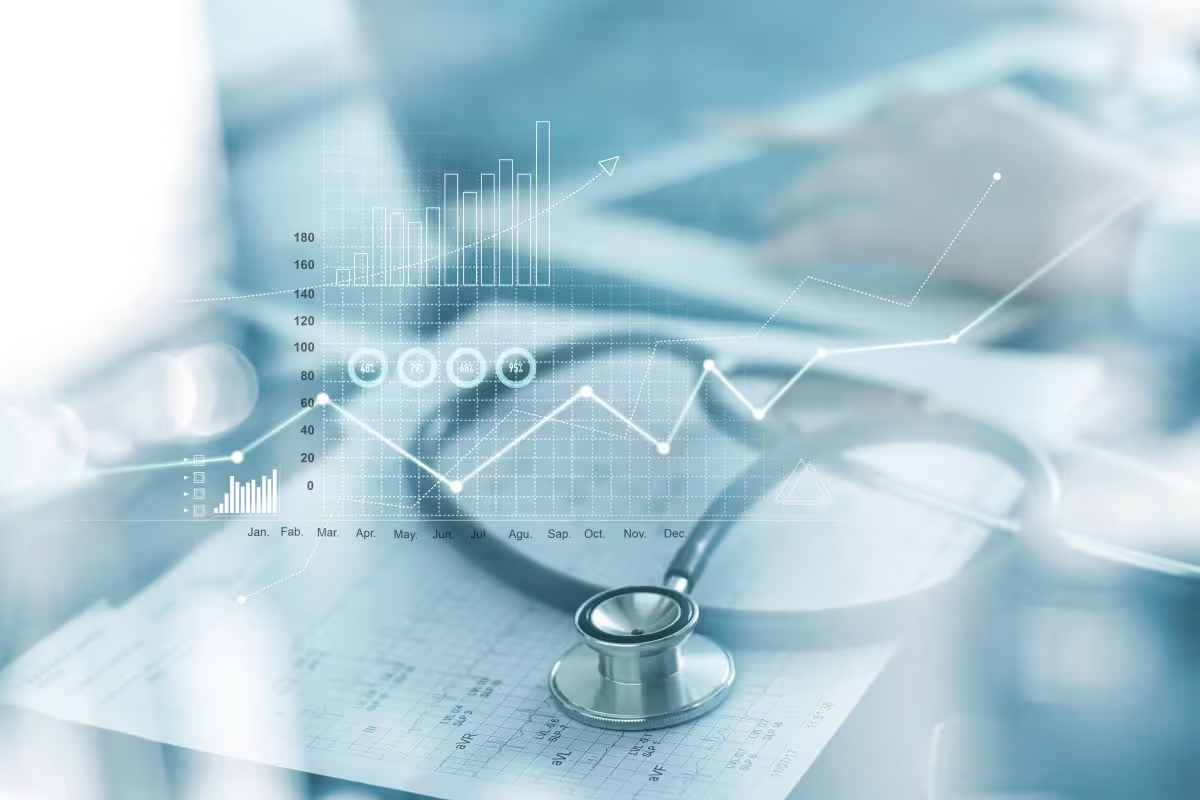
Visibility and automation: reducing disruption due to temperature excursions
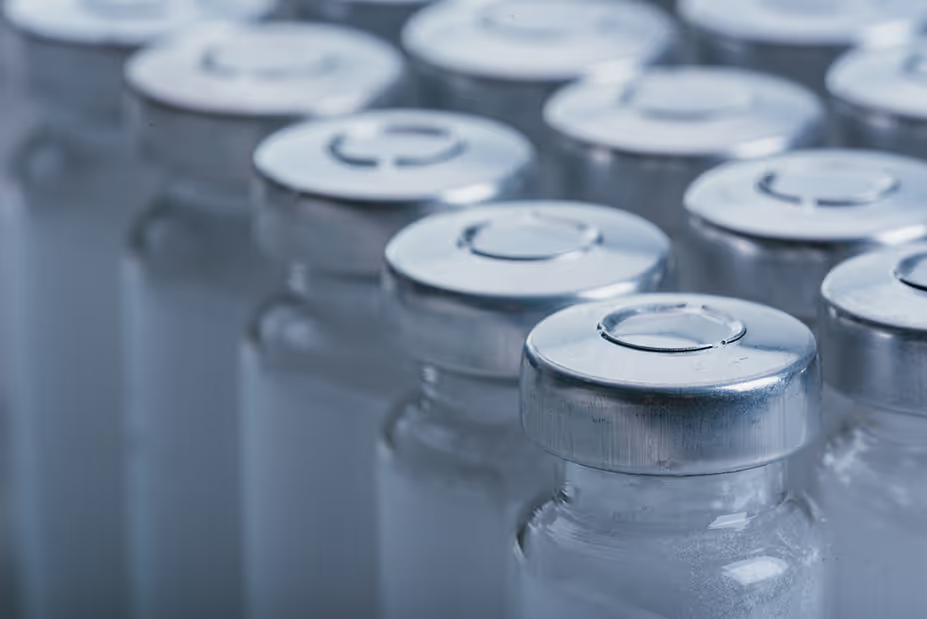
On-demand webinar: Automating the clinical supply chain

Three approaches for automating clinical supply chains
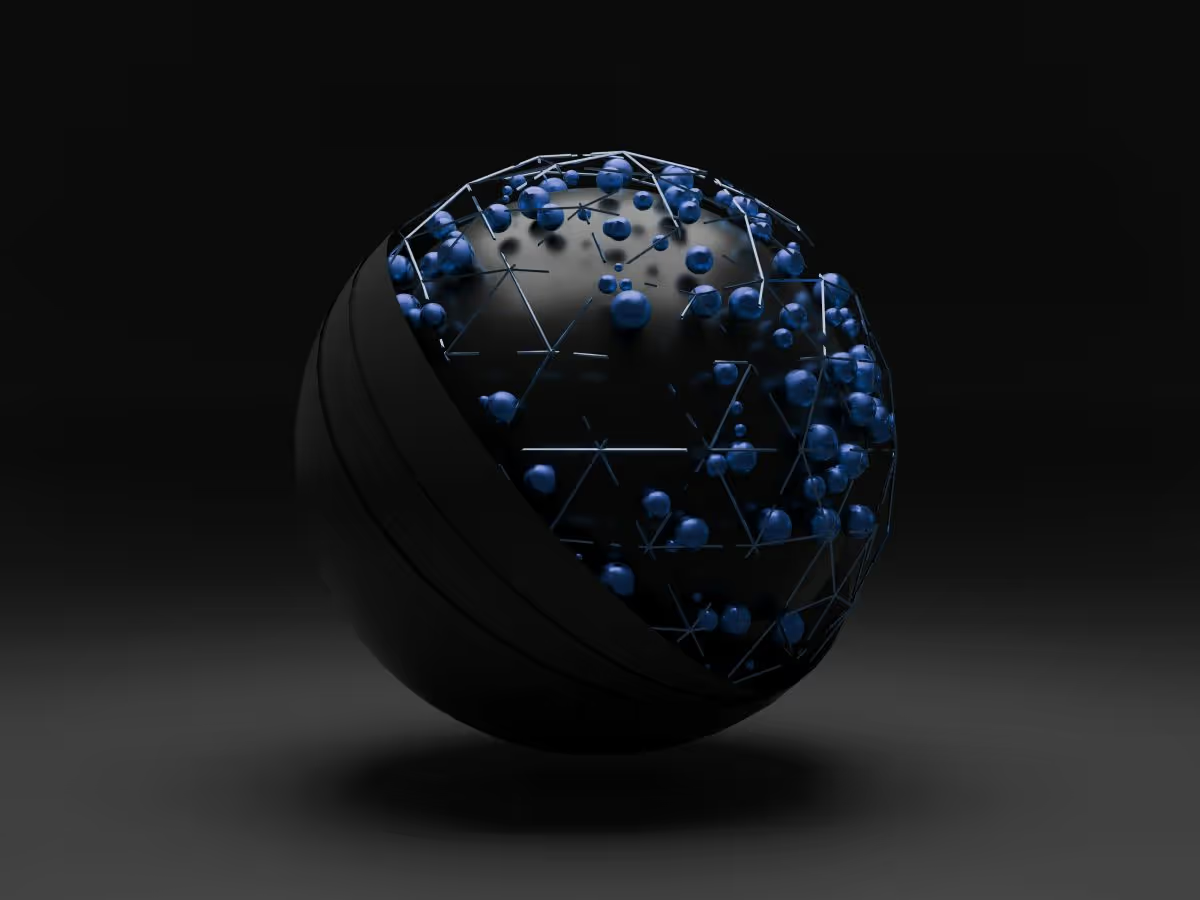
Data-driven supply chains: improving your excursion rate and temperature performance in 5 steps
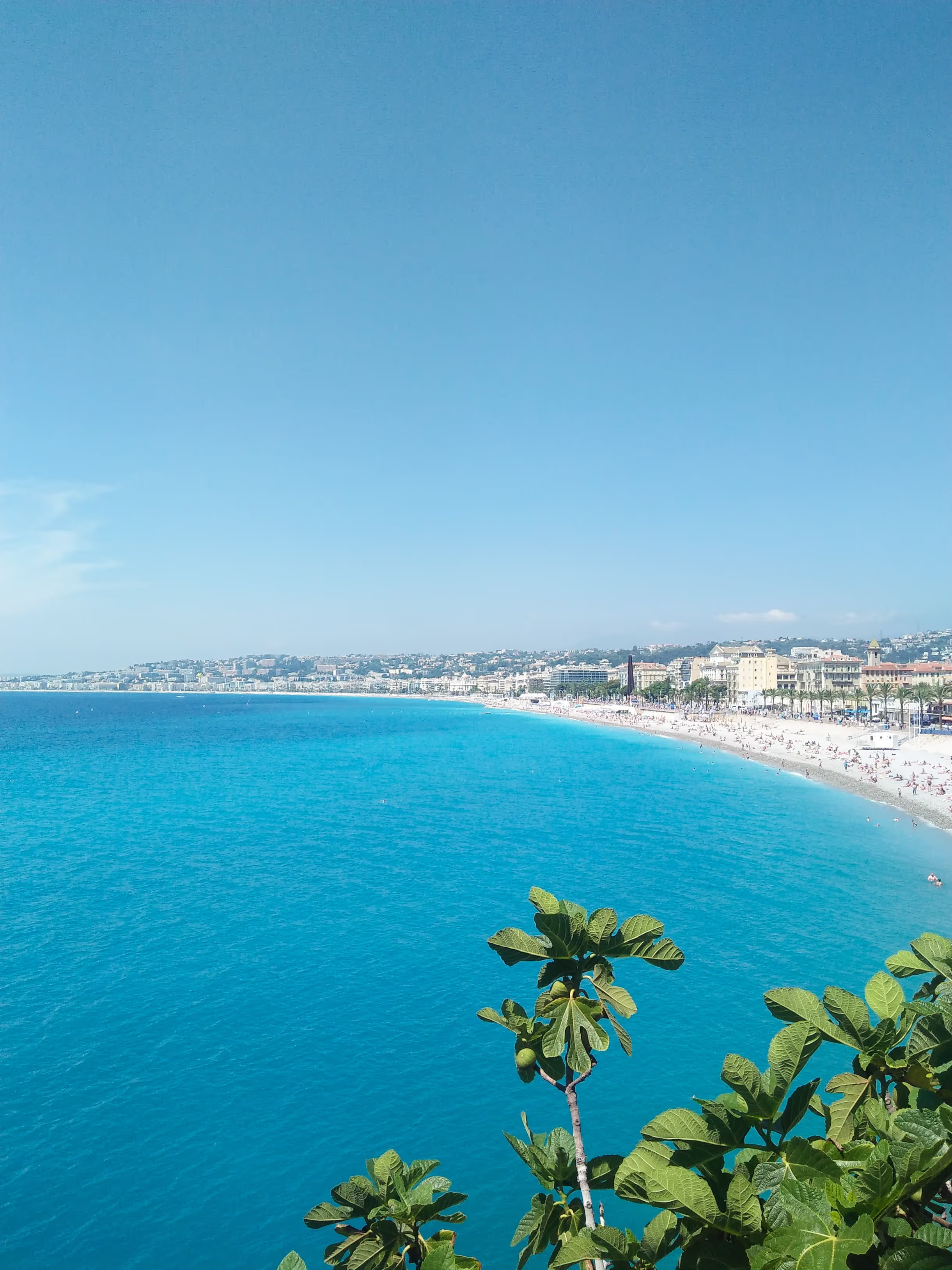
We’re attending LogiPharma 2022
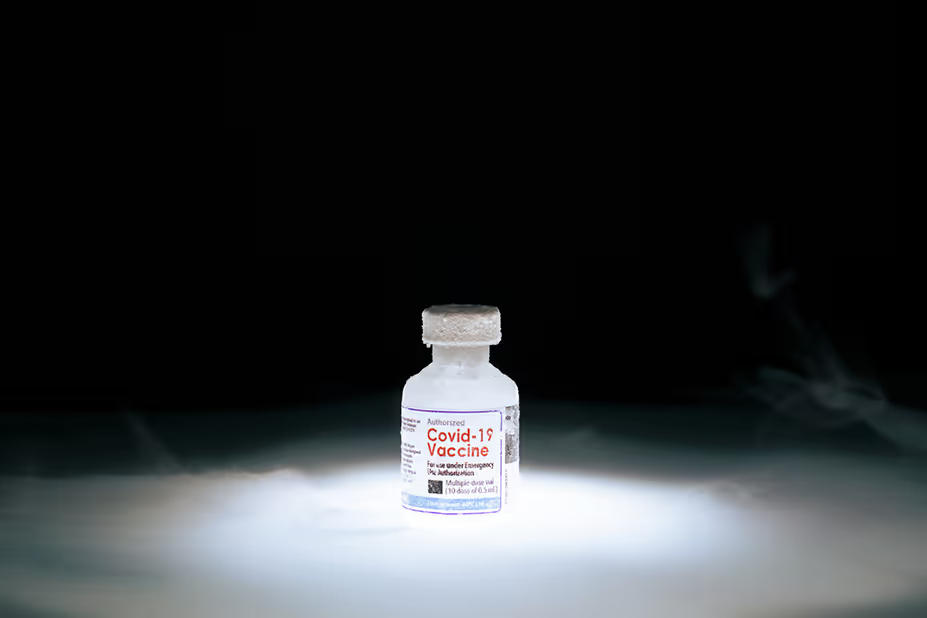
Could automating temperature excursion management hold the key to improving clinical supply processes?
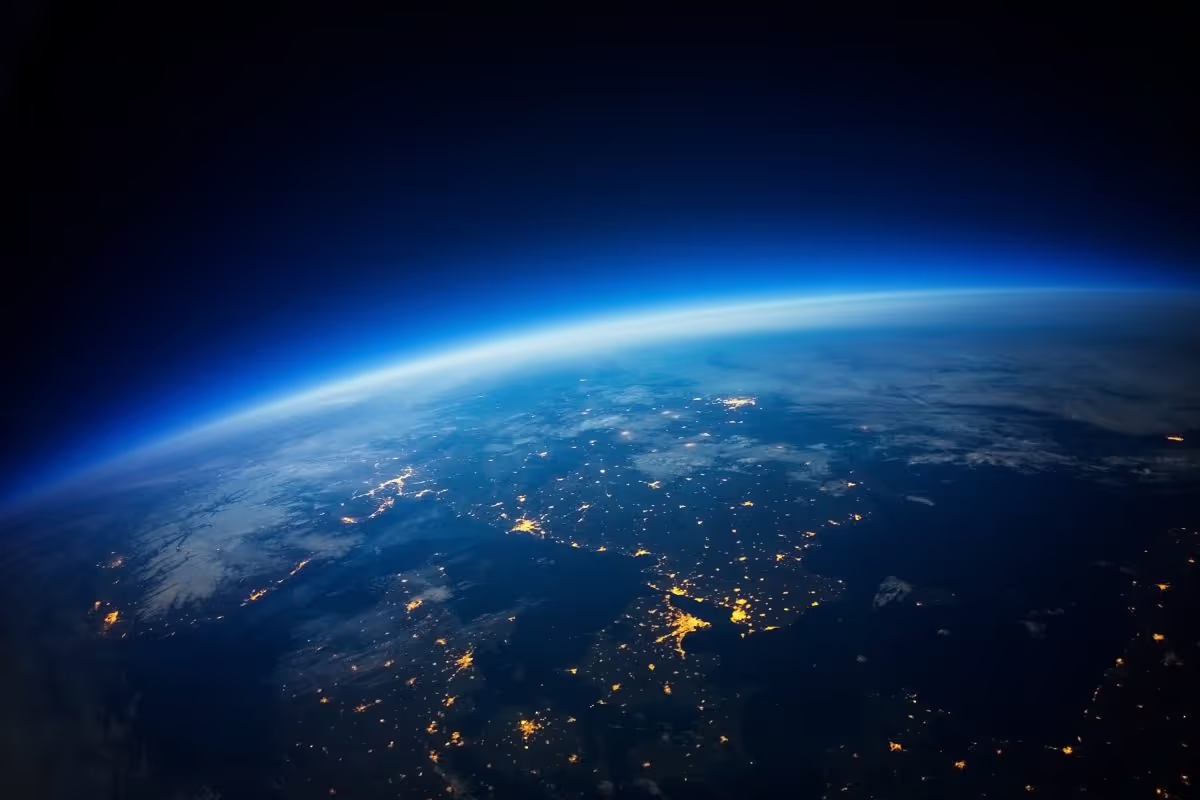
TSS launches innovative Bluetooth powered temperature monitoring solutions
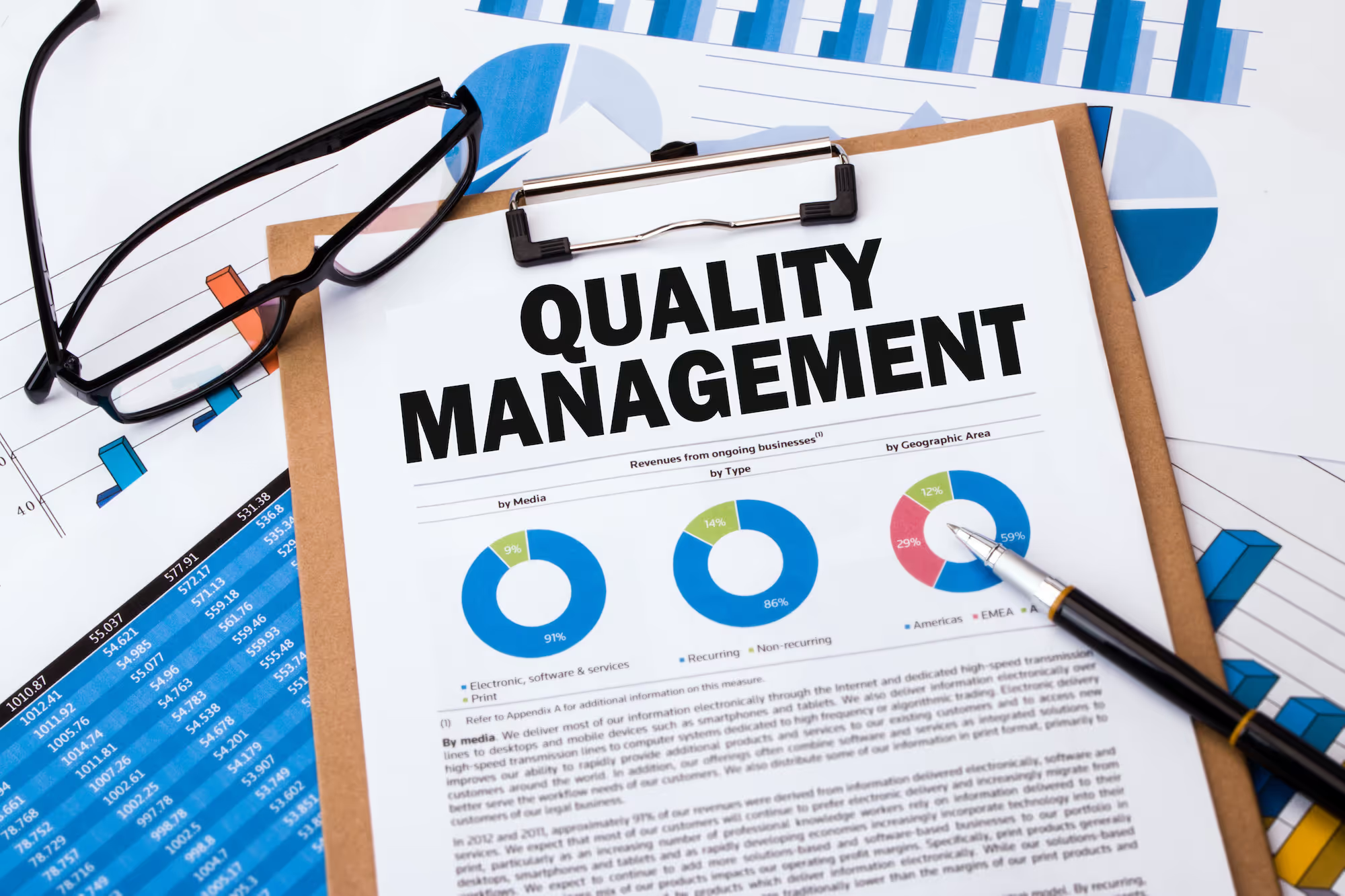
What is Quality?
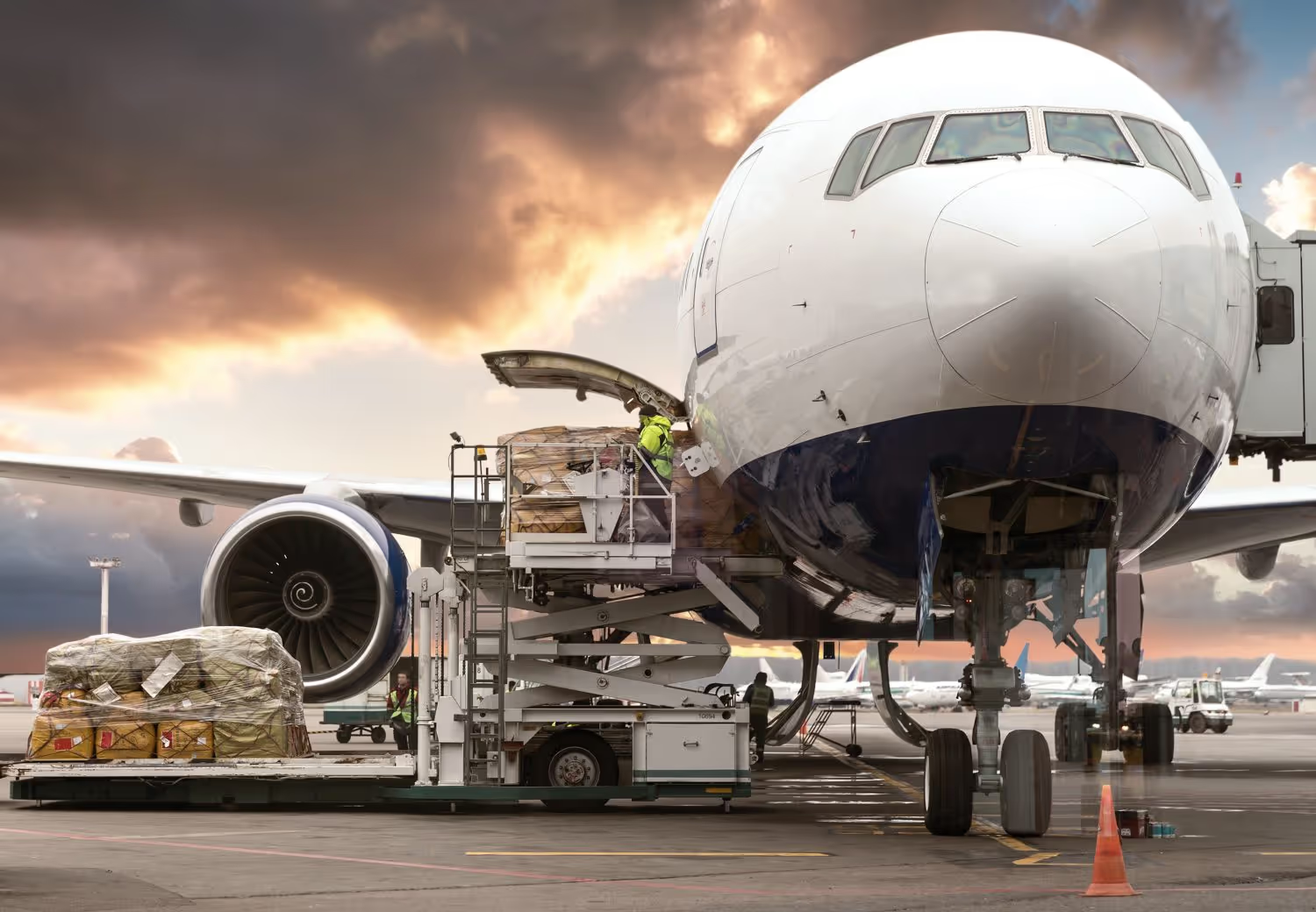