Which way is the wind blowing?
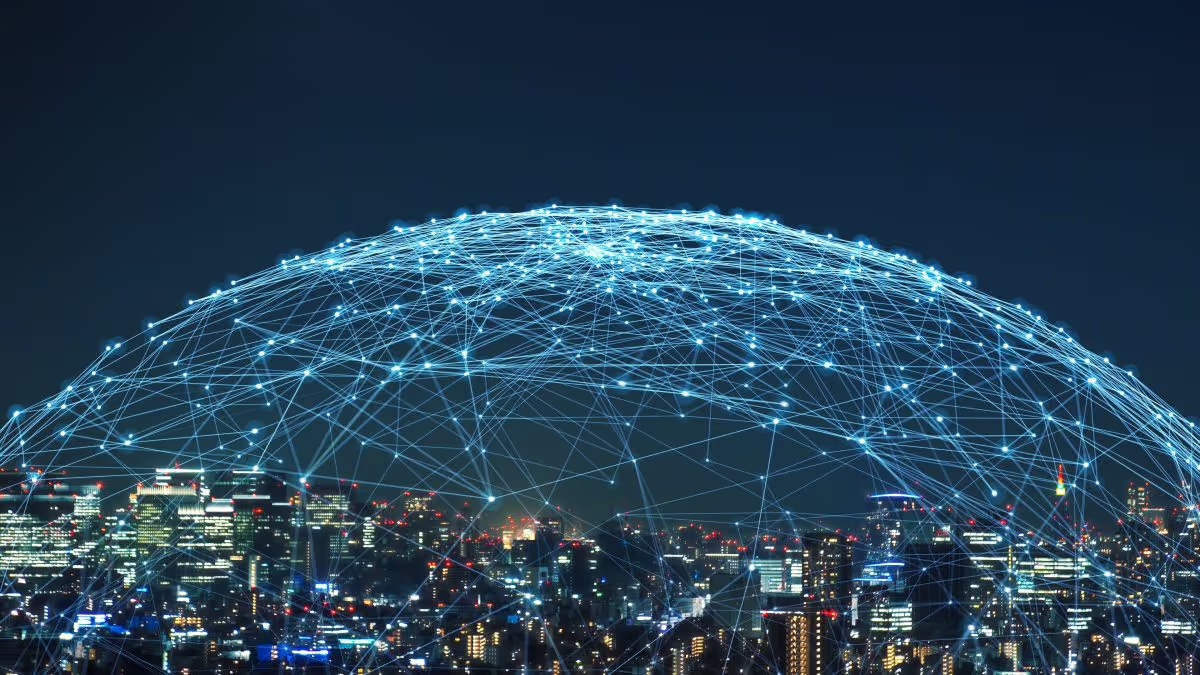
IoT on temperature monitoring
While the life science industry is celebrated for innovation in drug development, it is understandably conservative in its approach to early adoption of new technologies in areas such as logistics and distribution, where reliability and predictability of operations is critical.
Items such as temperature loggers continue to use hardware formats such as USB - universal, tried-and-tested and with relatively low failure rates. However, that reliability ceases to be a factor when users fail to upload the data to the system, causing gaps in the timeline which can lead to uncertainty of the shipping condition of the goods and ultimately questions on impact on patient safety, but also lack of data for insights that could improve supply chain efficiency. As an alternative, wireless technologies have come a very long way in a short time and their advantages in terms of efficiency, cost, and error-reduction now make them a compelling choice in many use cases.
Consider a typical example, where tracking of a pharma shipment is undertaken with a conventional logger. Upon the receipt of the shipment, a member of staff has to locate the logger, insert it into another device (typically a laptop, which might be in a different location) and manually upload the data. This physical process of uploading the data takes a significant amount of time per logger - multiply this by the number of shipments/packages and the hours add up. In addition, any system that relies on manual intervention has a greater potential for human error. People get distracted, can be insufficiently trained on a system, or be reliant on 3rd party software and hardware to transfer the data itself. Consider also that wireless systems allow for information such as temperature excursions to be automatically uploaded at key points in-transit, rather than just upon arrival at the ultimate destination - by which time there may be little that can be done.
While there are situations where a conventional logger is absolutely fit for purpose, it’s definitely the case that a wireless, automated solution has particular benefits; automated, reliable excursion reporting can contribute to reducing the costly waste of spoilt shipments, as well as eliminating delays in reporting while awaiting user intervention upon arrival.
.jpeg)
So, of the most commonly used wireless protocols available, which is best? Kjell Runngren, Product Manager at TSS explains the options and their pros and cons:
“At first glance, when we look at RFID (Radio Frequency ID), we see many advantages.. It’s a trusted technology which is low cost, reliable, low power and has existed as a tried and tested standard for years. However, the need for specific, proprietary hardware scanners makes it an inflexible choice and not a global viable option.
At the other end of the spectrum, cellular/GPS logging allows for real-time, continuous tracking of high-value shipments which, in some cases, can be invaluable. However, the vast majority of shipments don’t need real time - just an update at critical points where processes for intervention can be established along the supply chain. On the downside, cellular trackers are power-hungry, often a more expensive solution, and have regulatory restrictions when it comes to air travel and won´t last through longer missions or when stuck at customs for long time (they are, after all, mini-mobile phones).
So that leaves Bluetooth. The most recent version (BLE, or Bluetooth Low Energy) is a quantum leap forward, building upon the reliability of previous generations but adding increased range and minimal power consumption. In addition, it is almost universally compatible, and the infrastructure is globally available. Every laptop, desktop, tablet or phone of the last decade will almost certainly come shipped with Bluetooth as standard.”
The upside is simple. Automated, no-touch tracking and upload to the cloud of key shipment data, such as temperature logs and location, with low cost, high reliability, and no need for expensive hardware or specialized personnel training.
Traditional monitoring equipment has served - and continues to serve - the industry well, but in a large number of cases it might well be time to cut the cord.
You may also be interested in
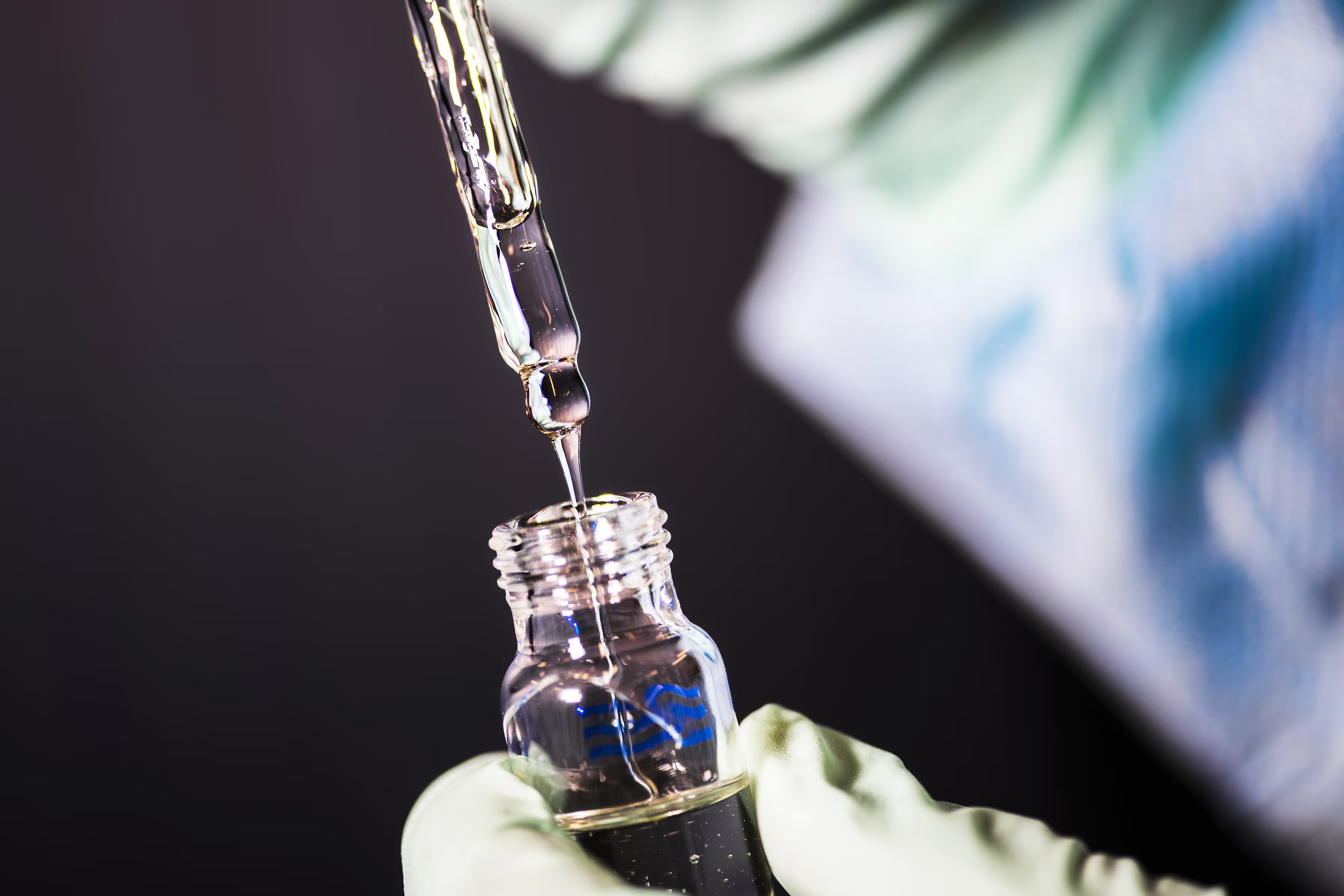
Making the pharma industry future-proof through supply chain digitalization
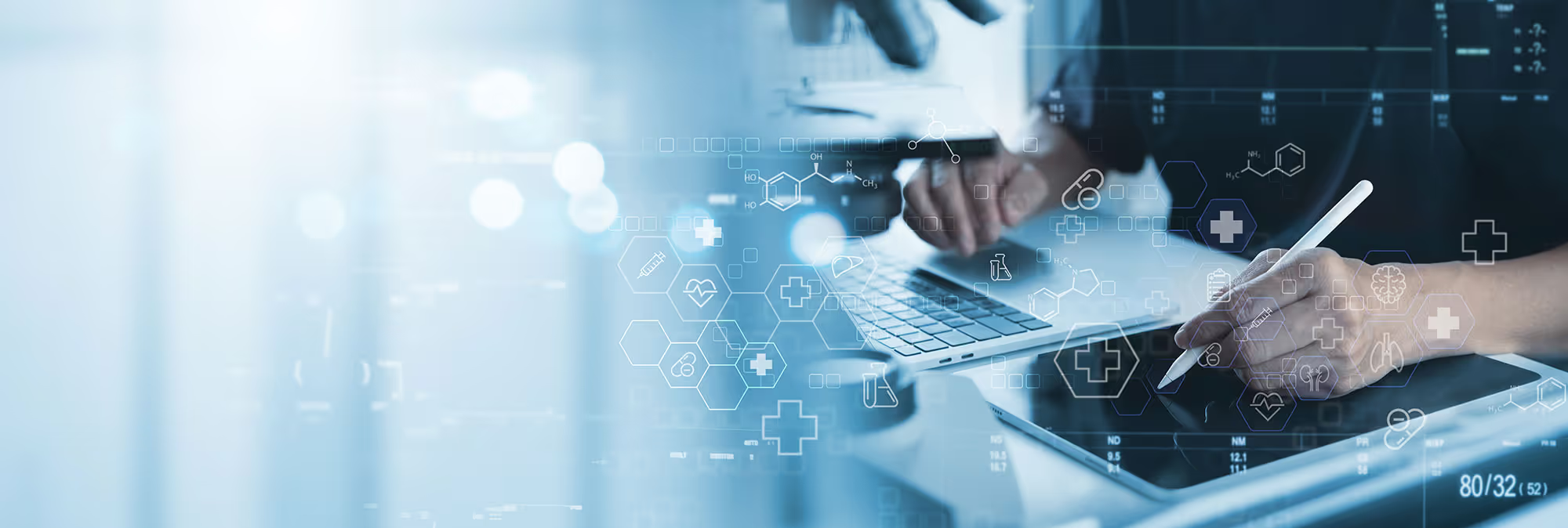
How can maturity in temperature management move your decision process from days to seconds?
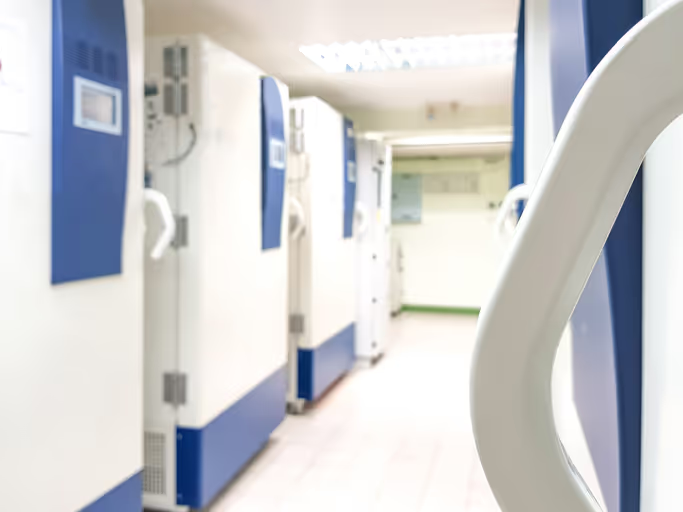
4 things to know about TSS new BLE data loggers
You may also be interested in
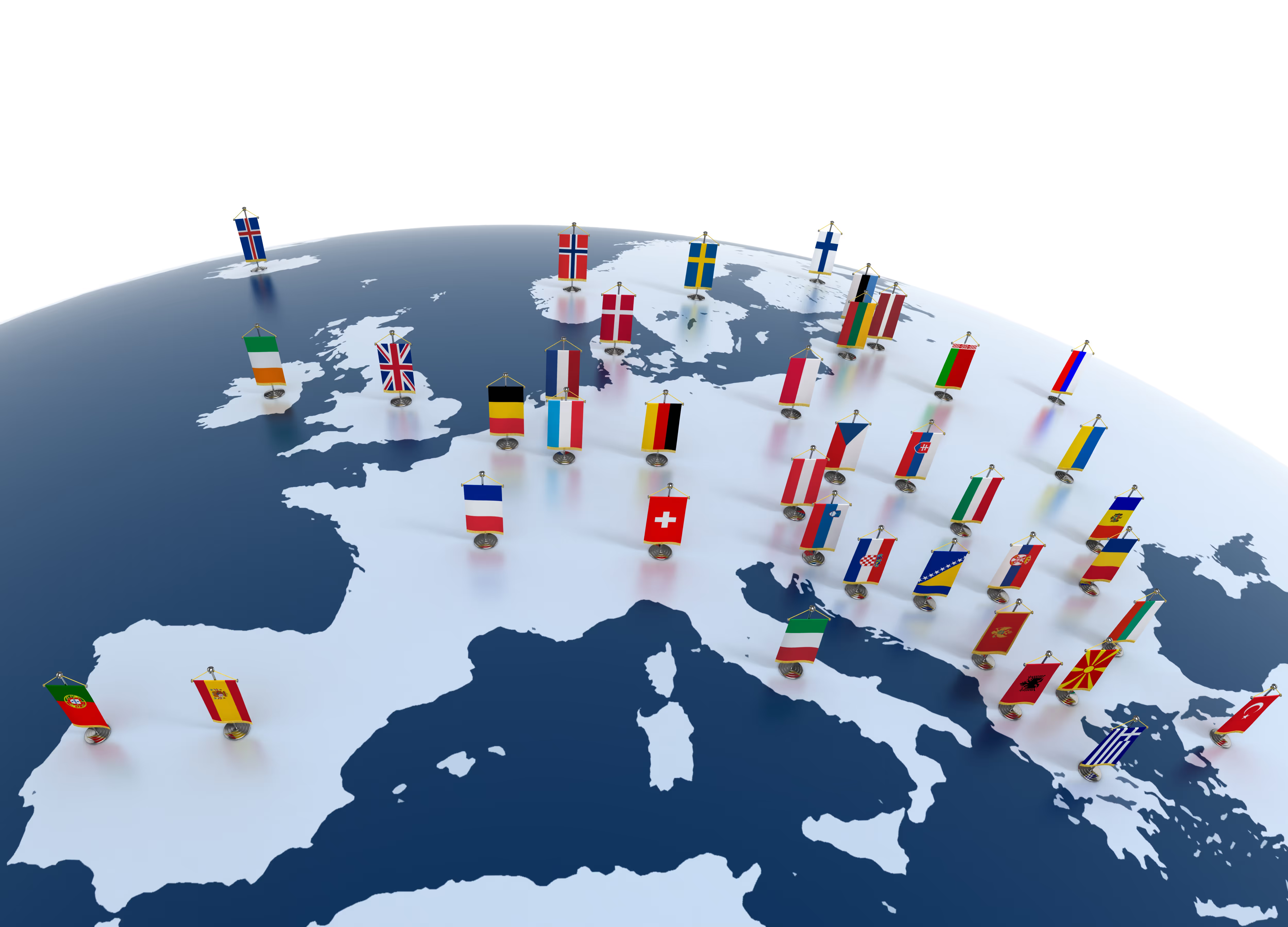
Join Us at LogiPharma Europe 2025
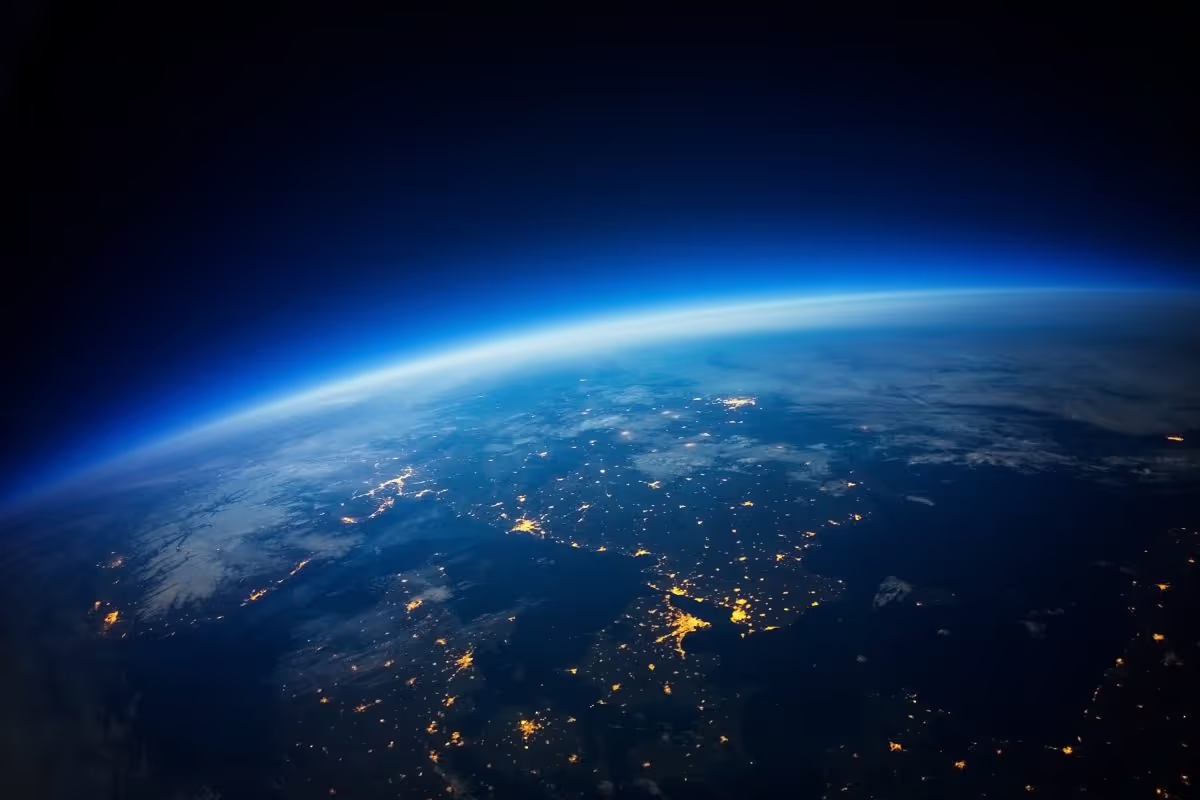
TSS launches innovative Bluetooth powered temperature monitoring solutions
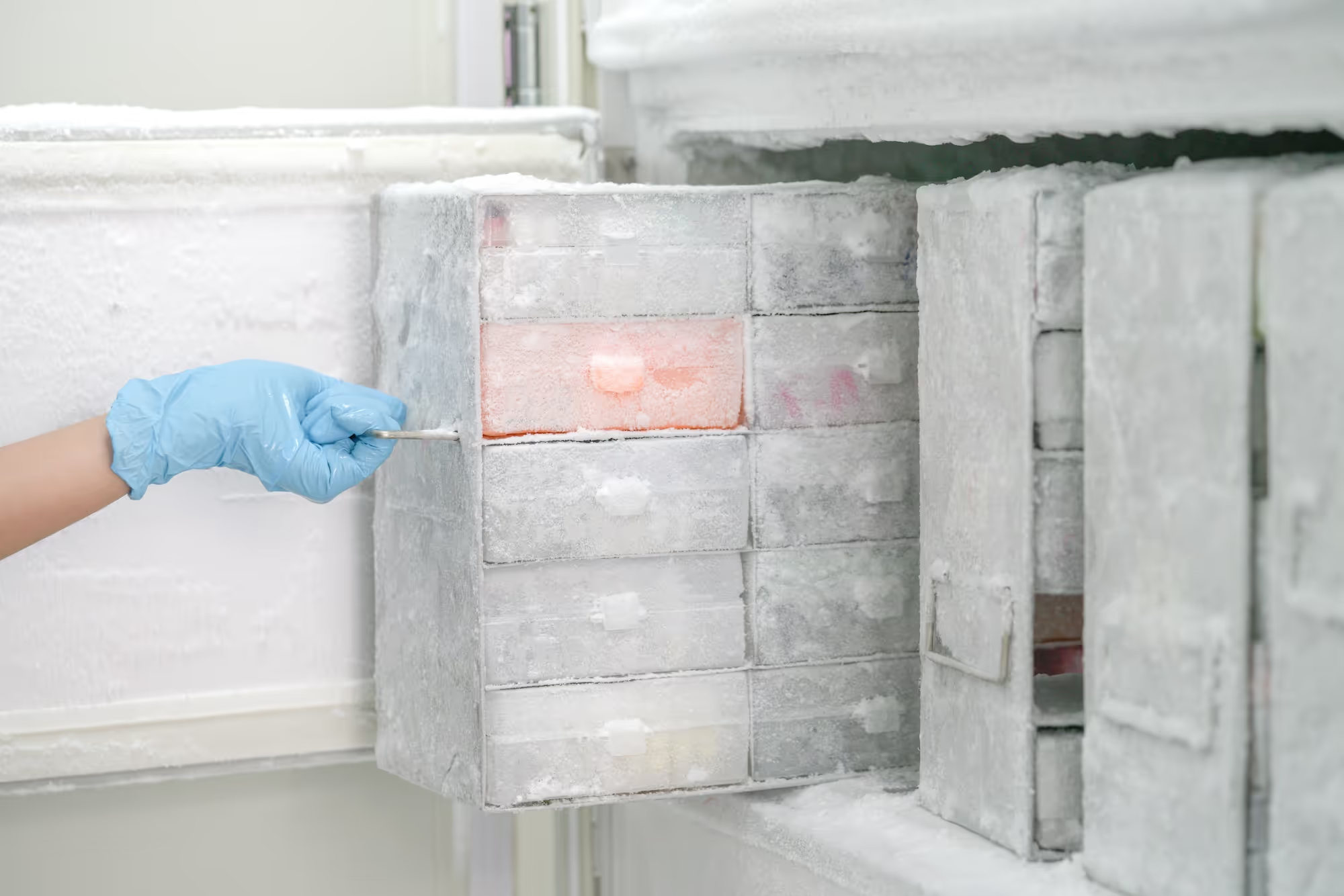
Achieving FDA and EMA Compliance in Temperature Monitoring
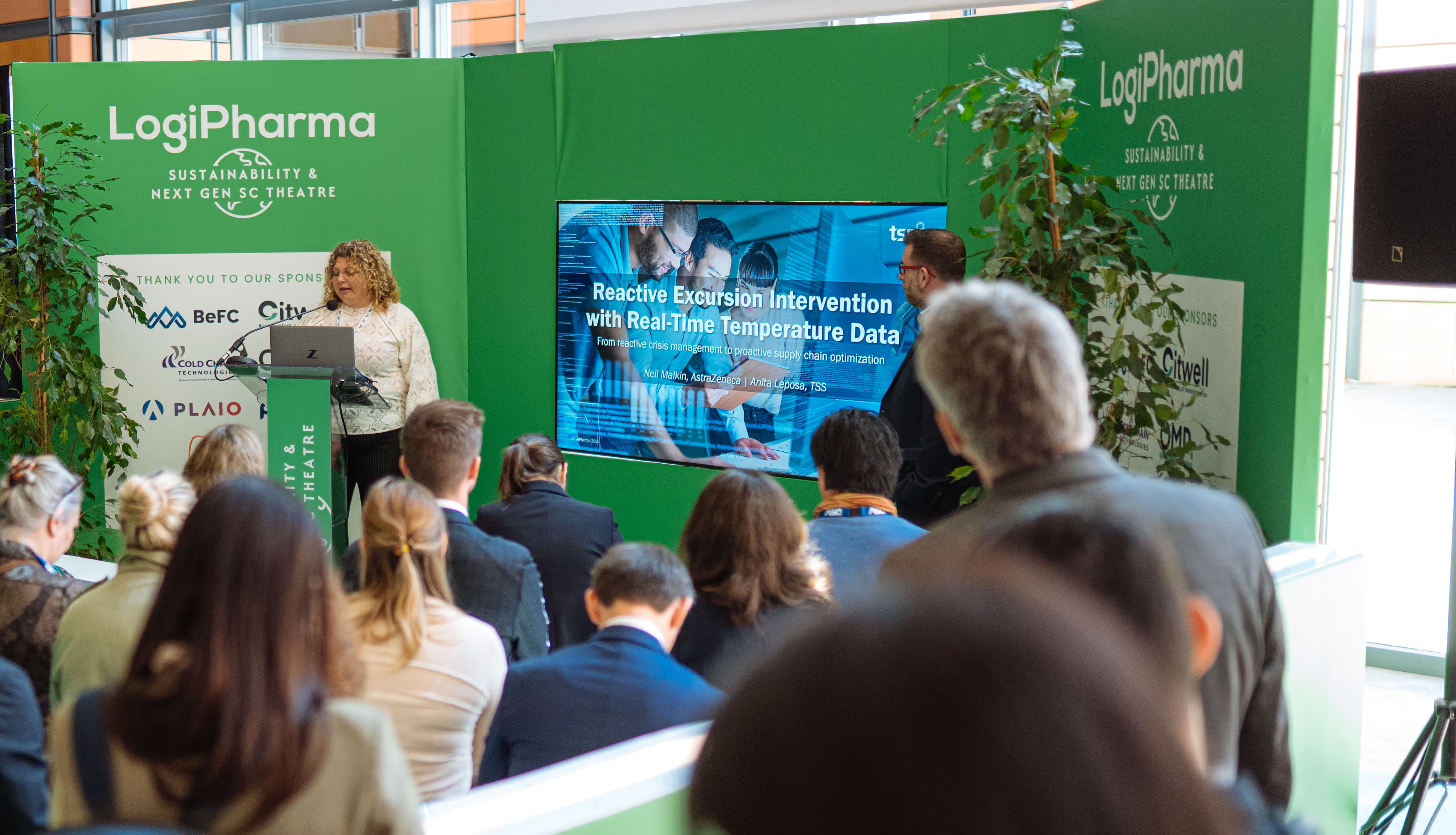
Proactive Temperature Management: The Key to a More Resilient Pharma Supply Chain
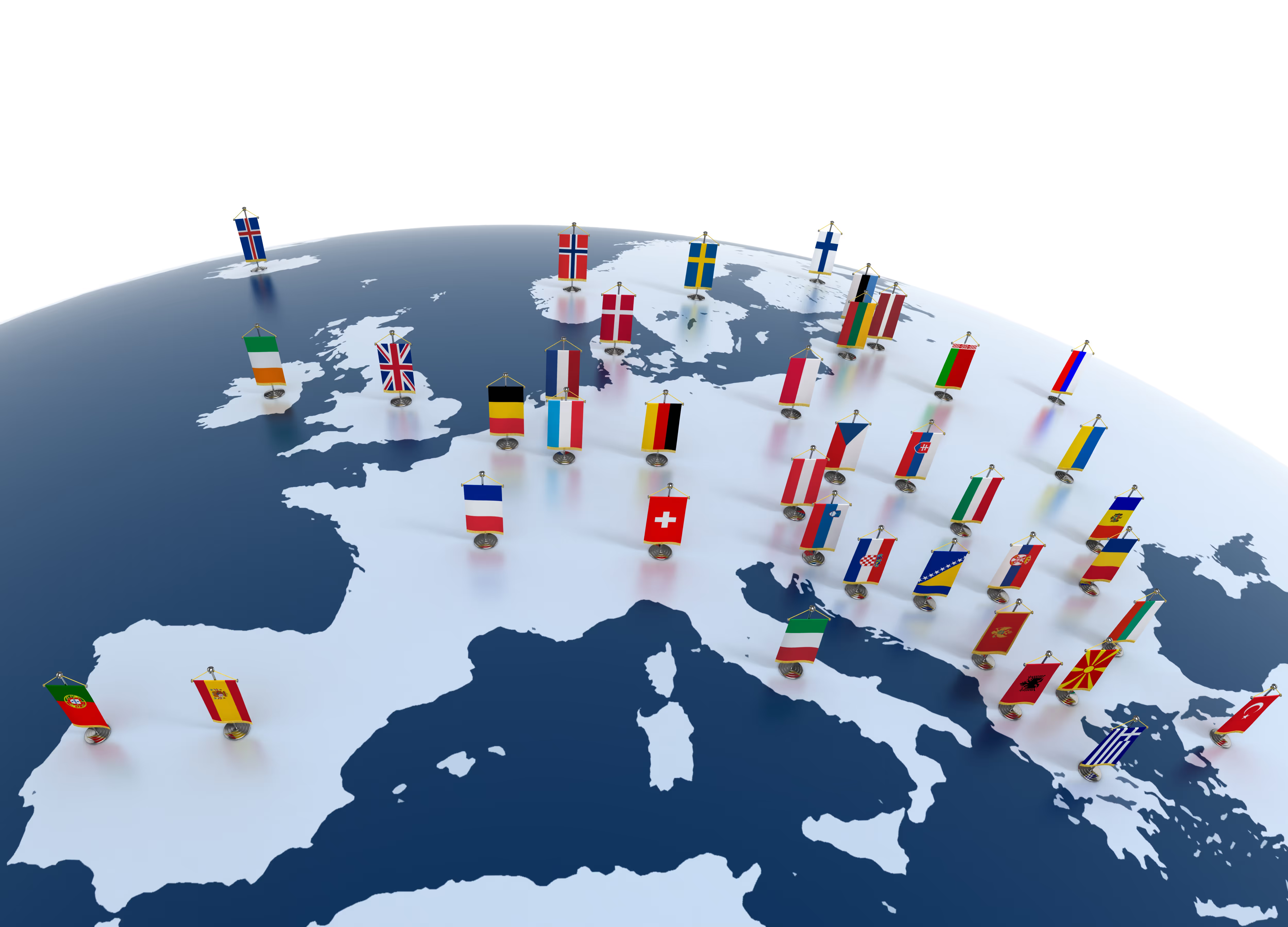
Join Us at LogiPharma Europe 2025
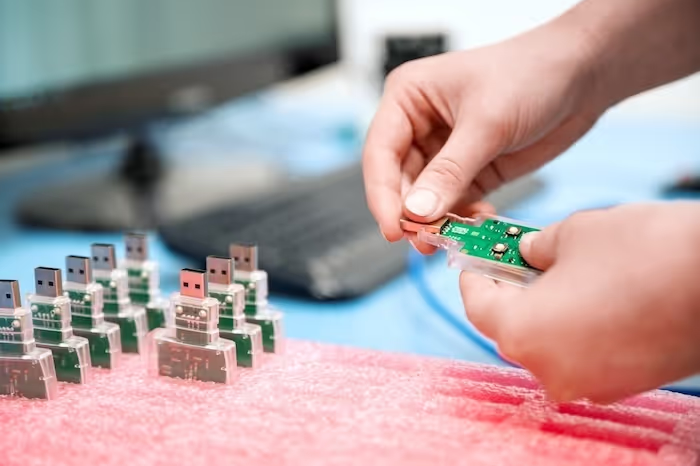
TSS Receives CDP SME Climate Score 'SME B' for Strong Climate Actions
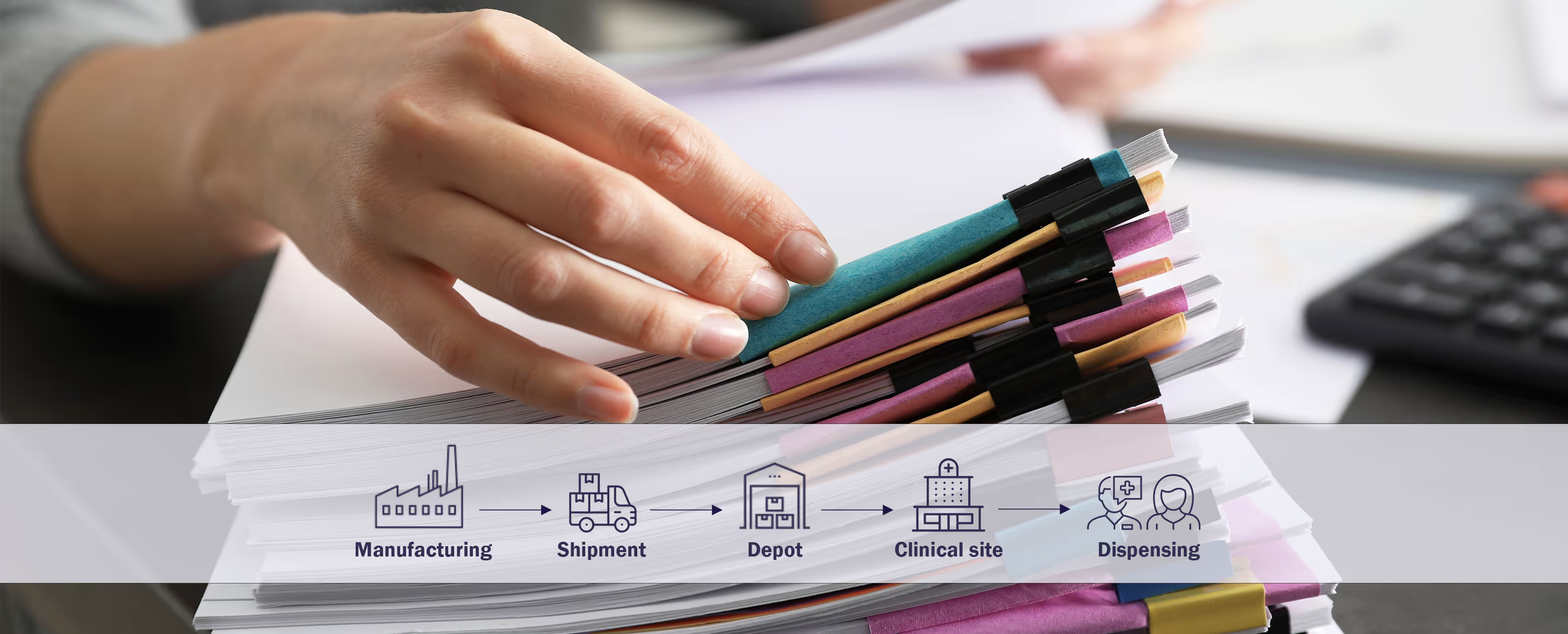
Future-Proofing Clinical Trials: How Sponsors Can Up-Scale Through Automation
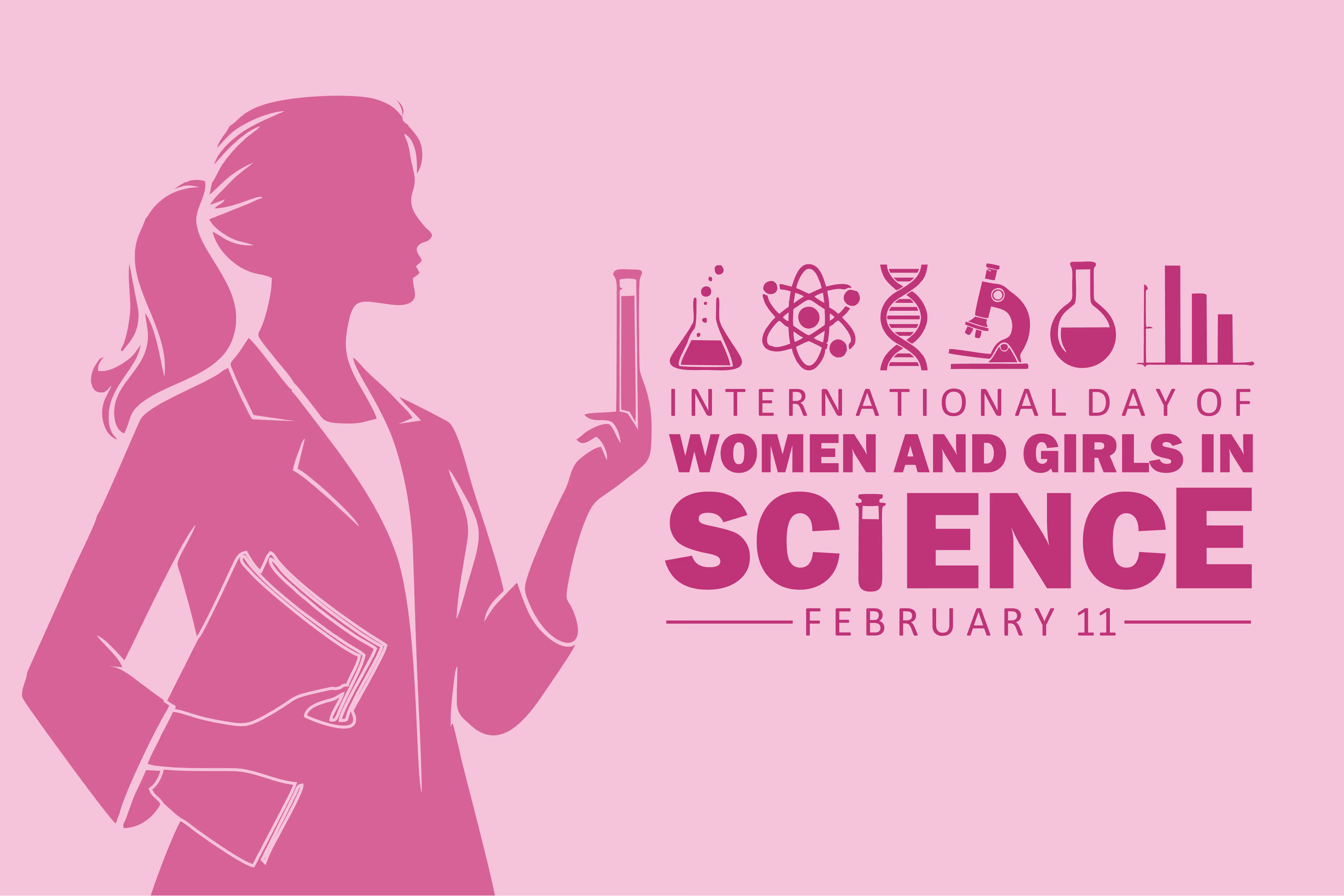
Celebrating Women in Tech
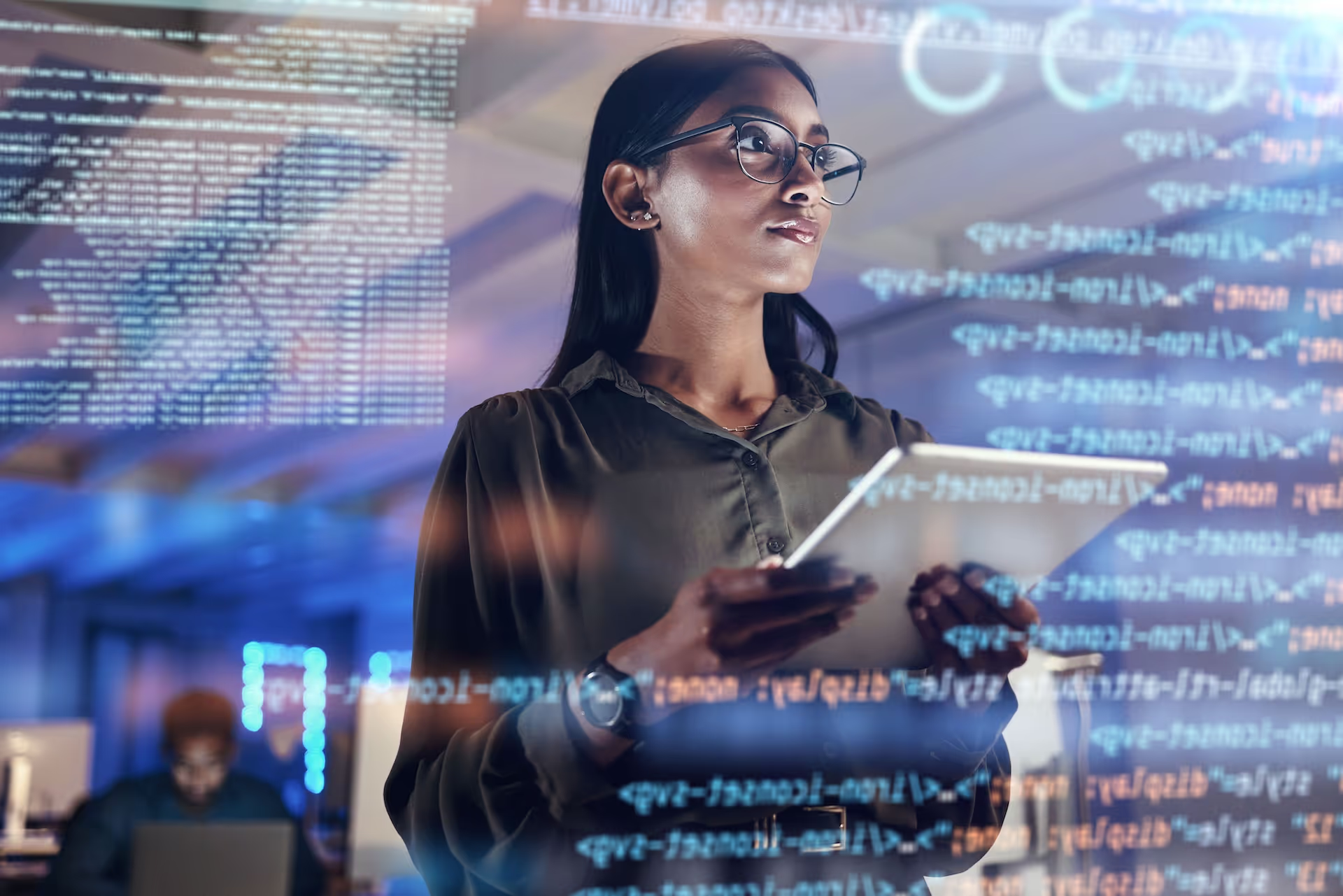
Clinical Trial Supply Europe Event 2025
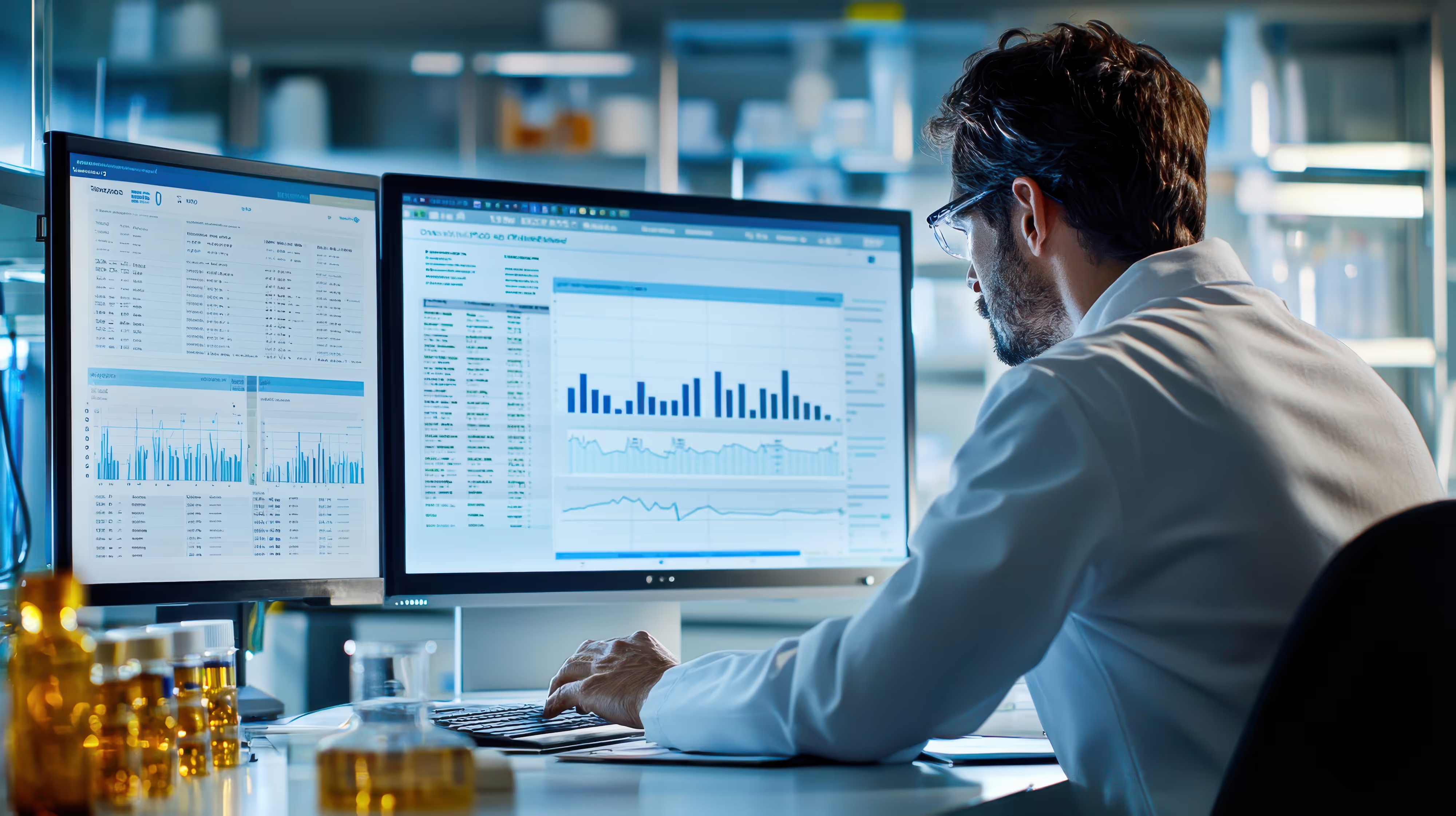
Sustainable Temperature Management: A Key to Greener Clinical Trials
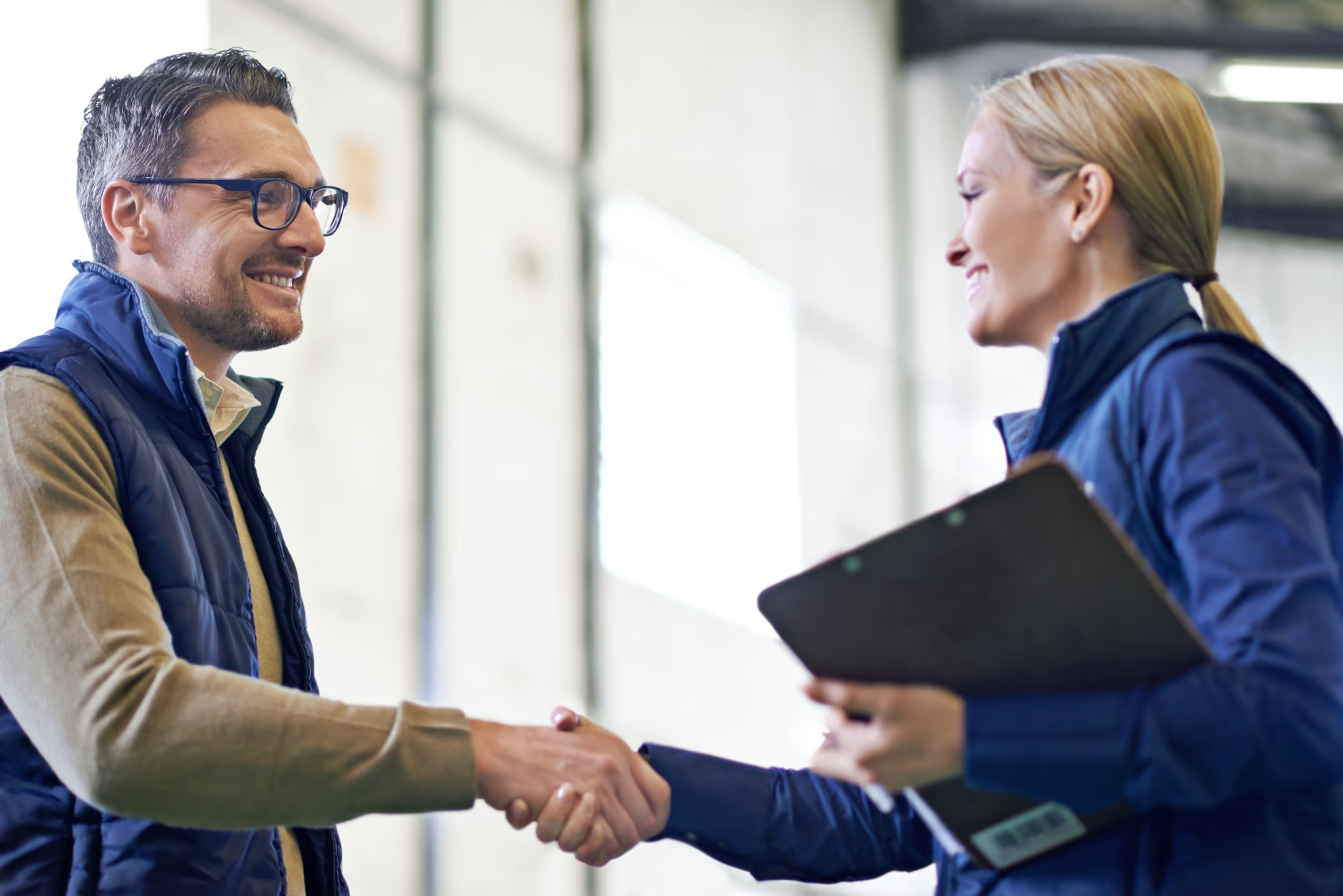
10 Common Mistakes to Avoid During Customer Onboarding
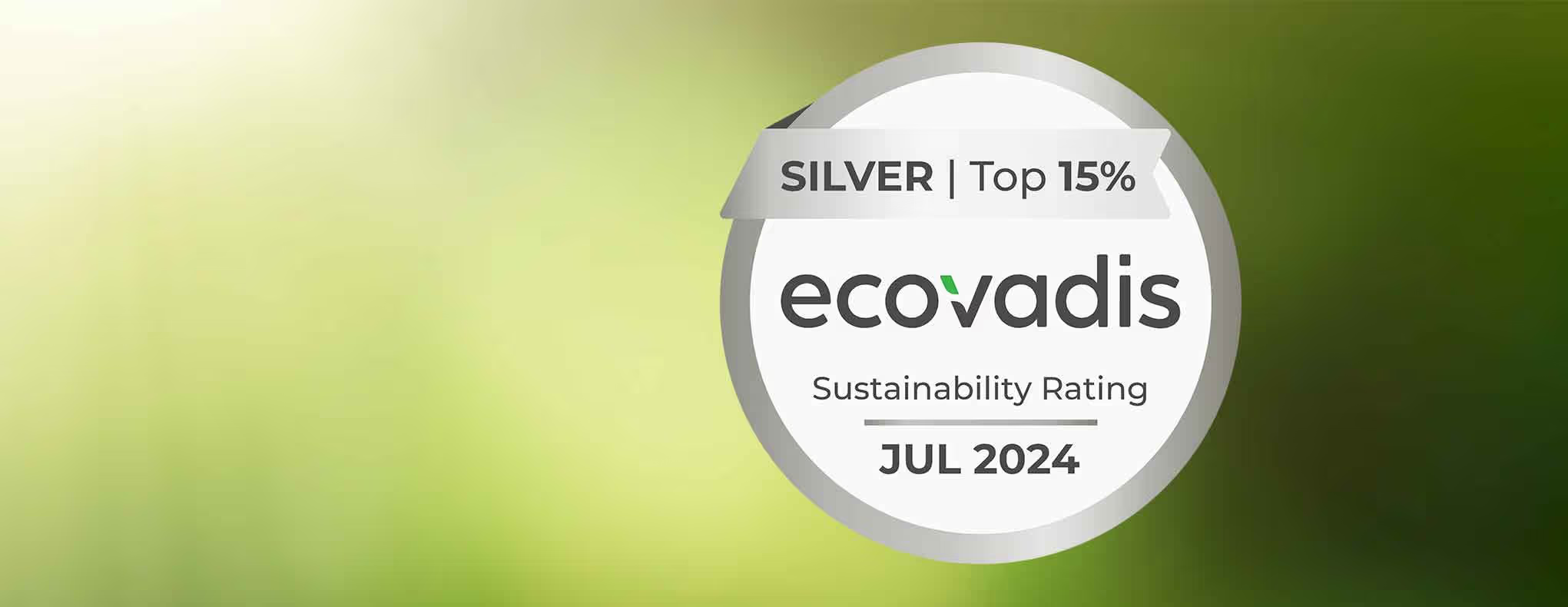
TSS Keeps EcoVadis Silver Medal Despite Tougher Standards in 2024
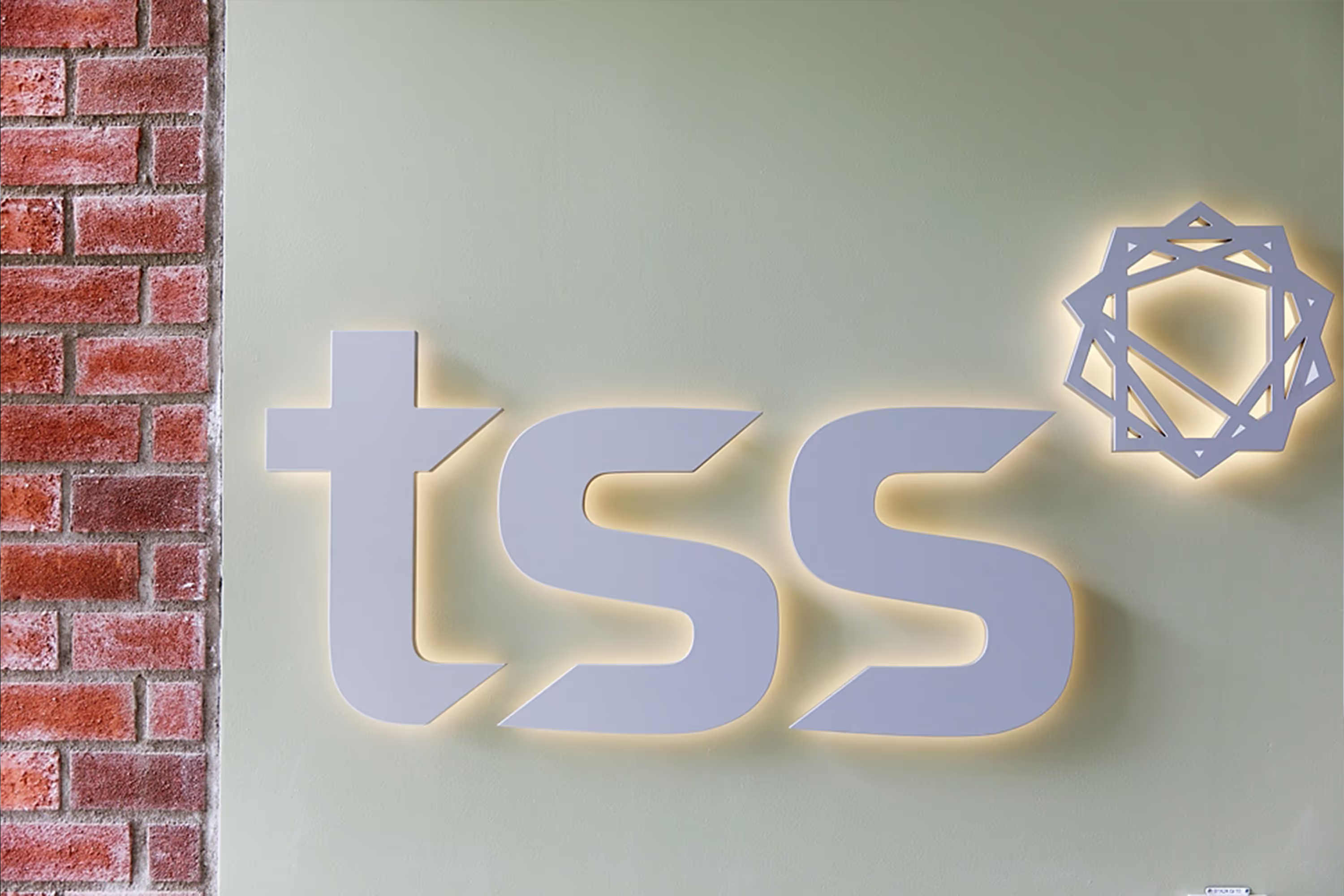
Change in the Management of TSS
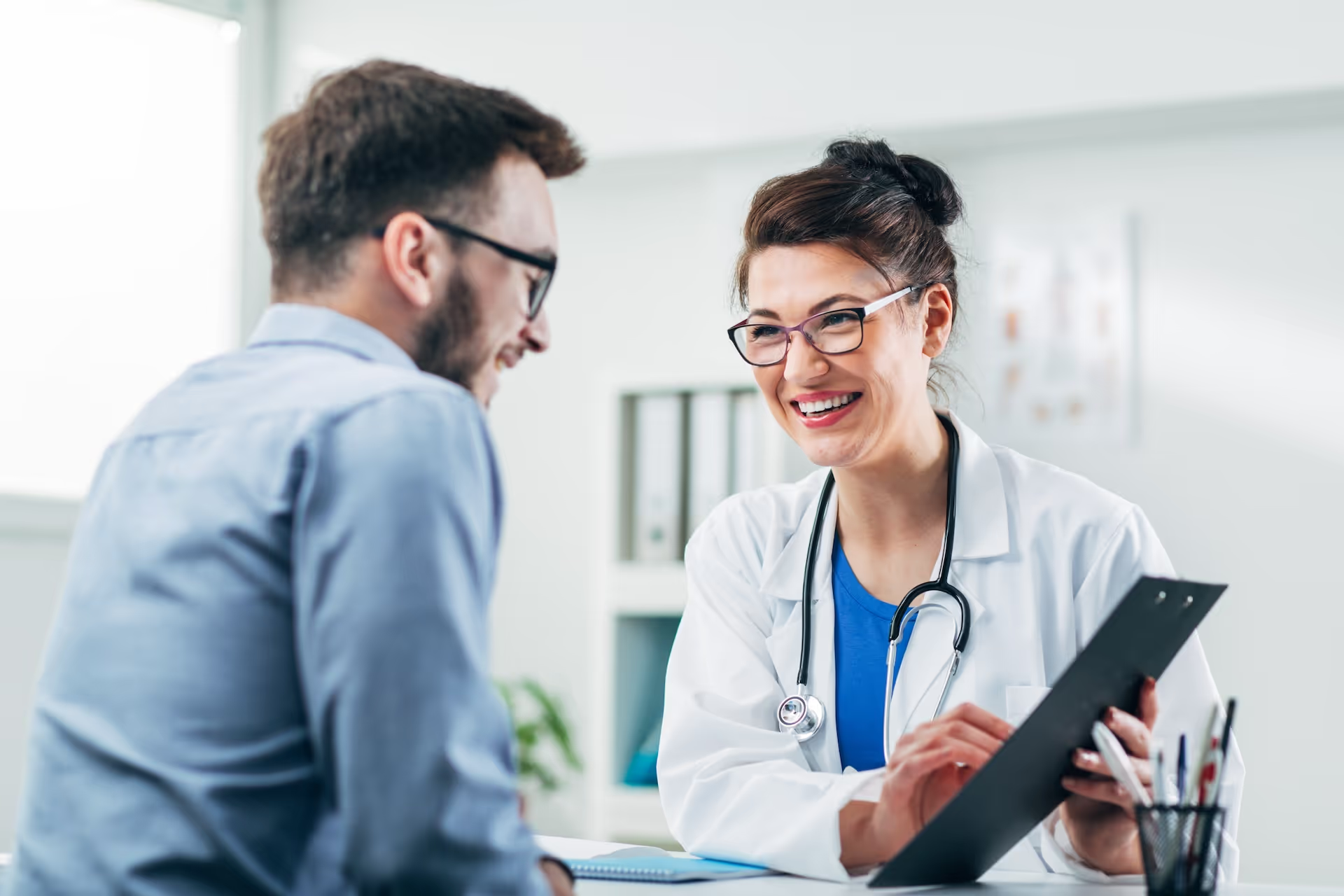
How to Scale Up Your Clinical Trials
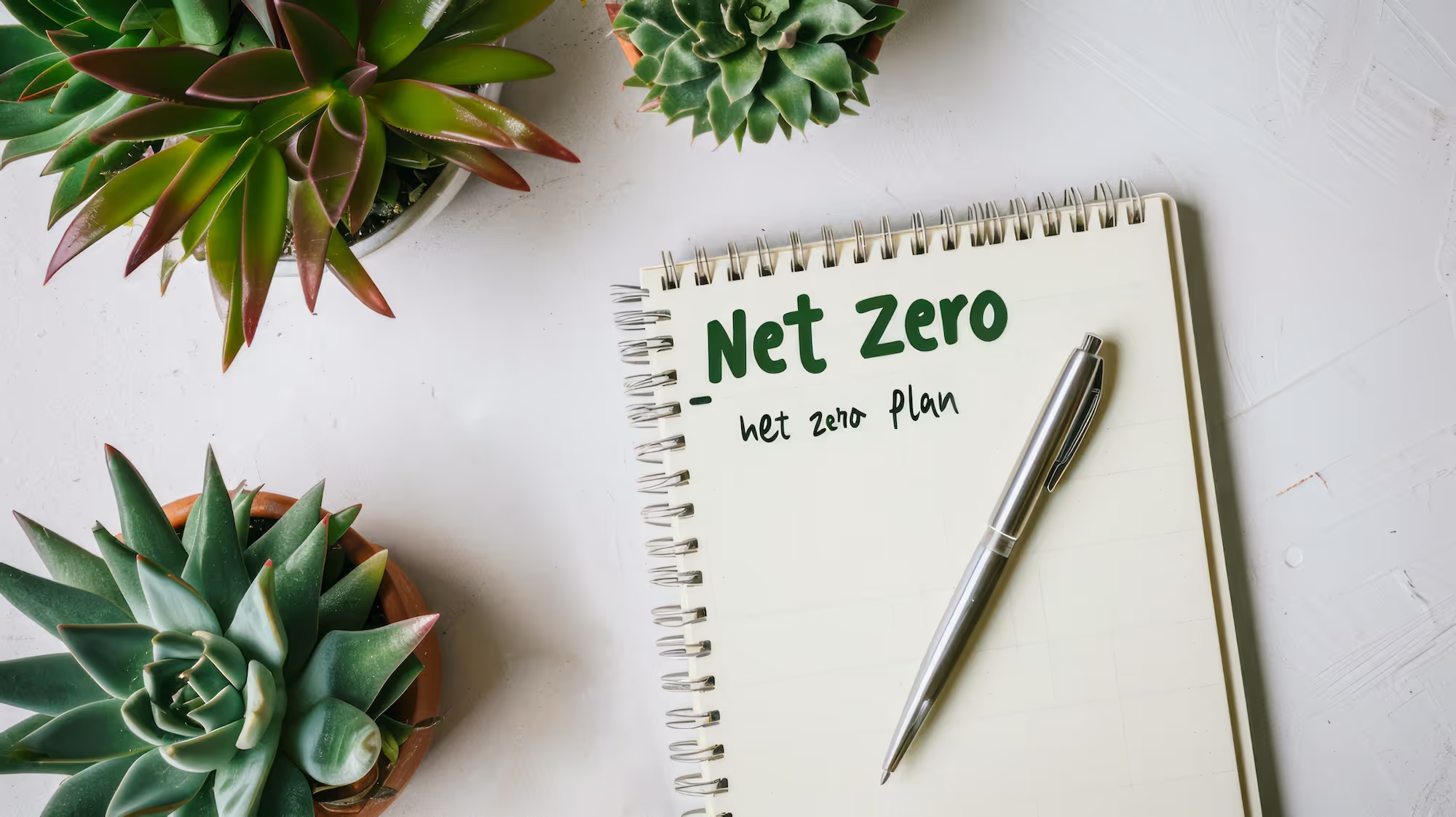
10 Steps to Navigating Sustainability in the Pharma Supply Chain
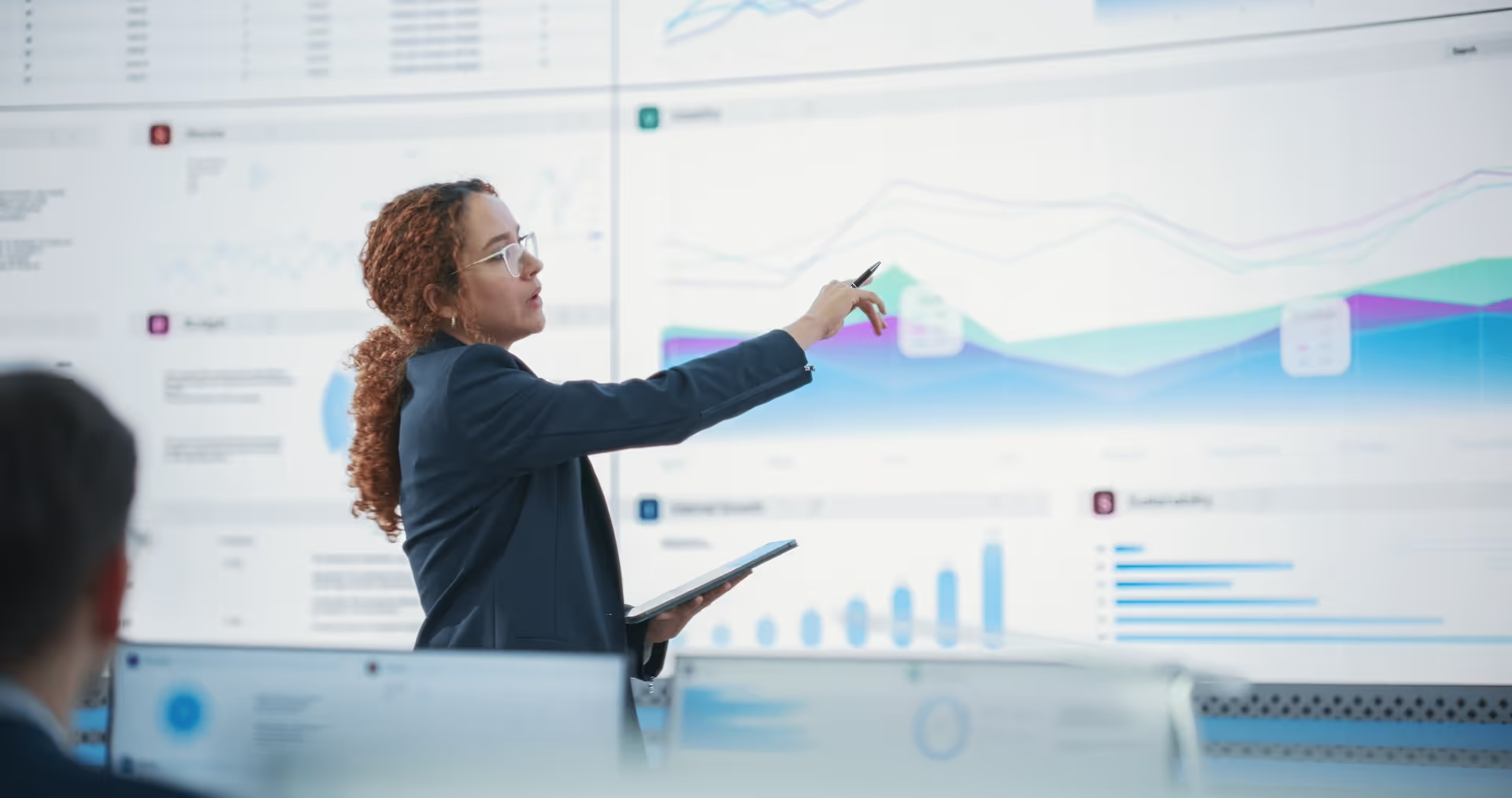
Balancing Cost and Quality in the Pharmaceutical Supply Chain: A Quick Guide
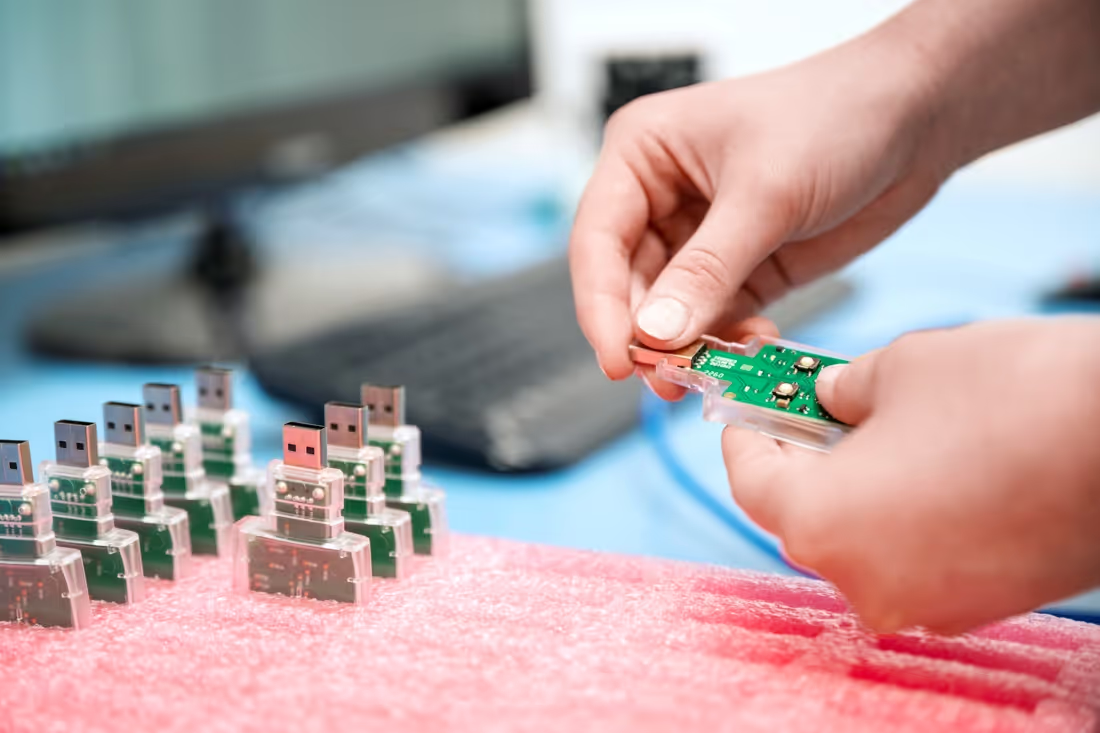
TSS Celebrates WTISD 2024: Embracing Innovation, Digitalisation, and Sustainability
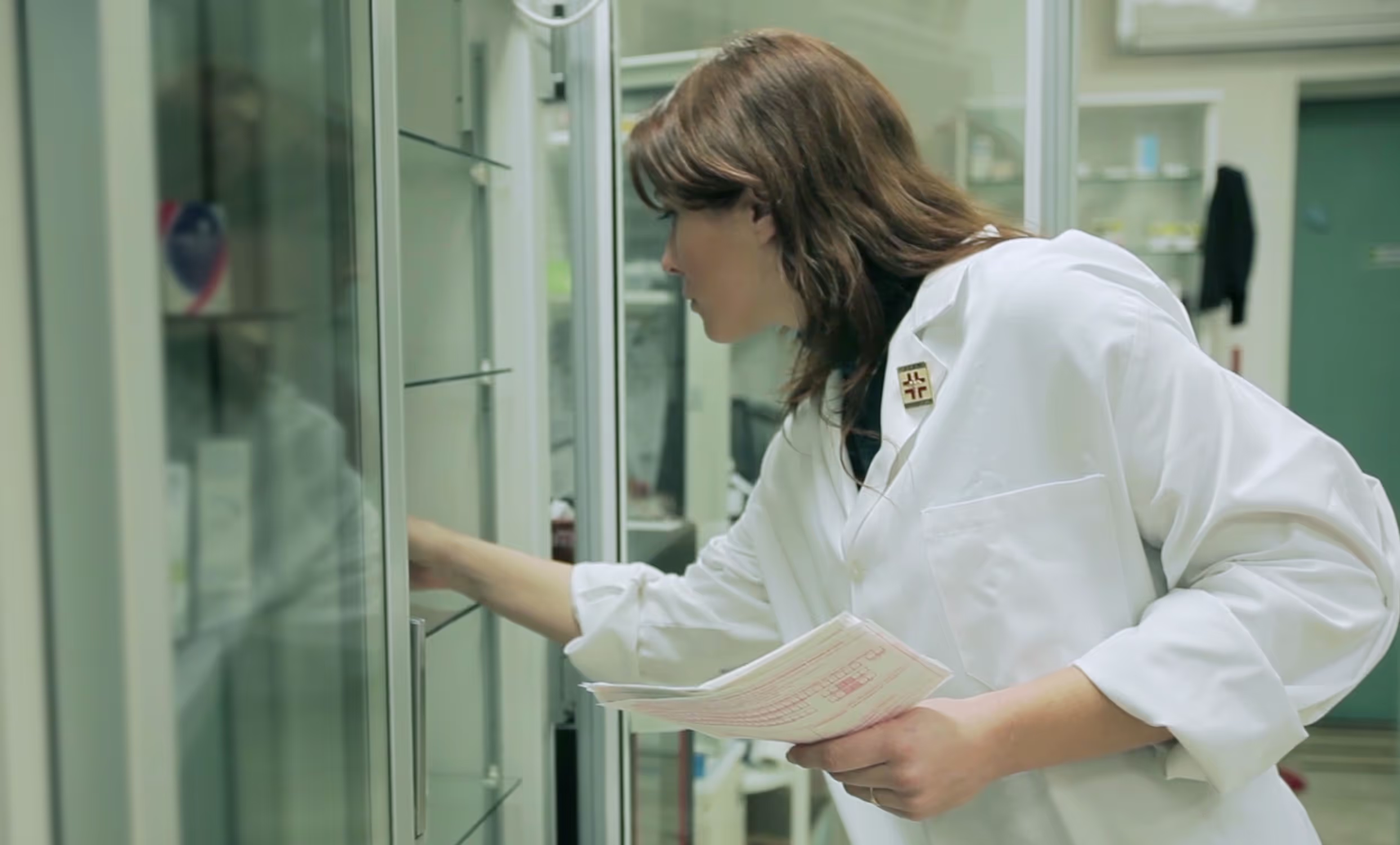
Enhancing Product Quality and Compliance at Clinical Sites
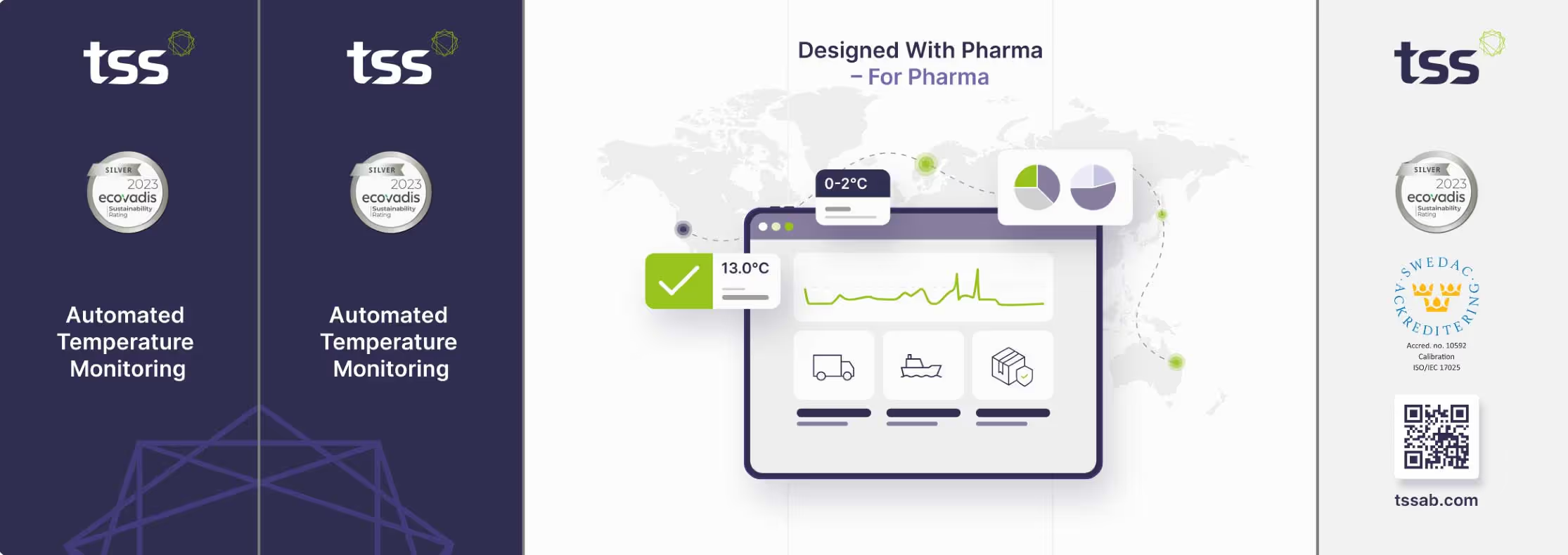
LogiPharma Lyon 2024
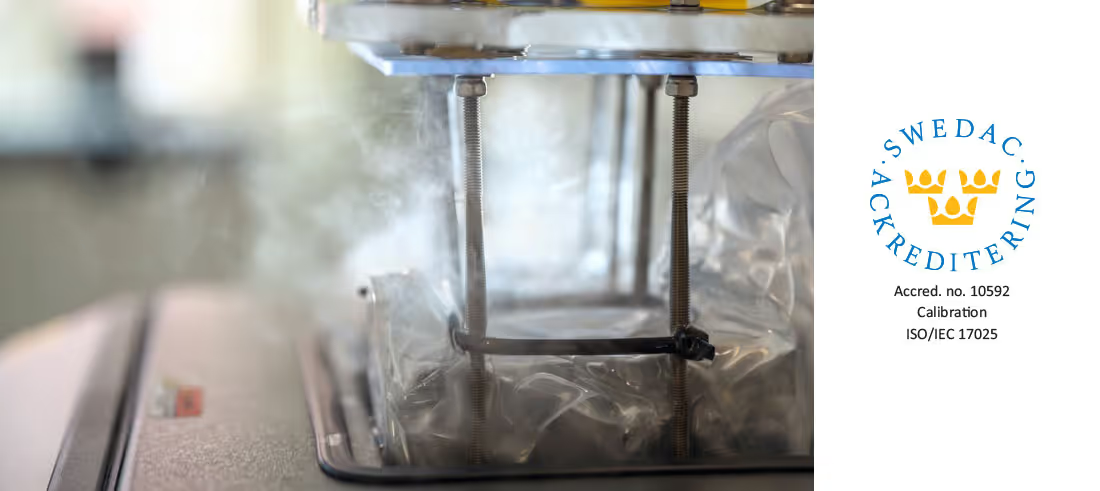
TSS Achieves Coveted ISO/IEC 17025 Calibration Accreditation
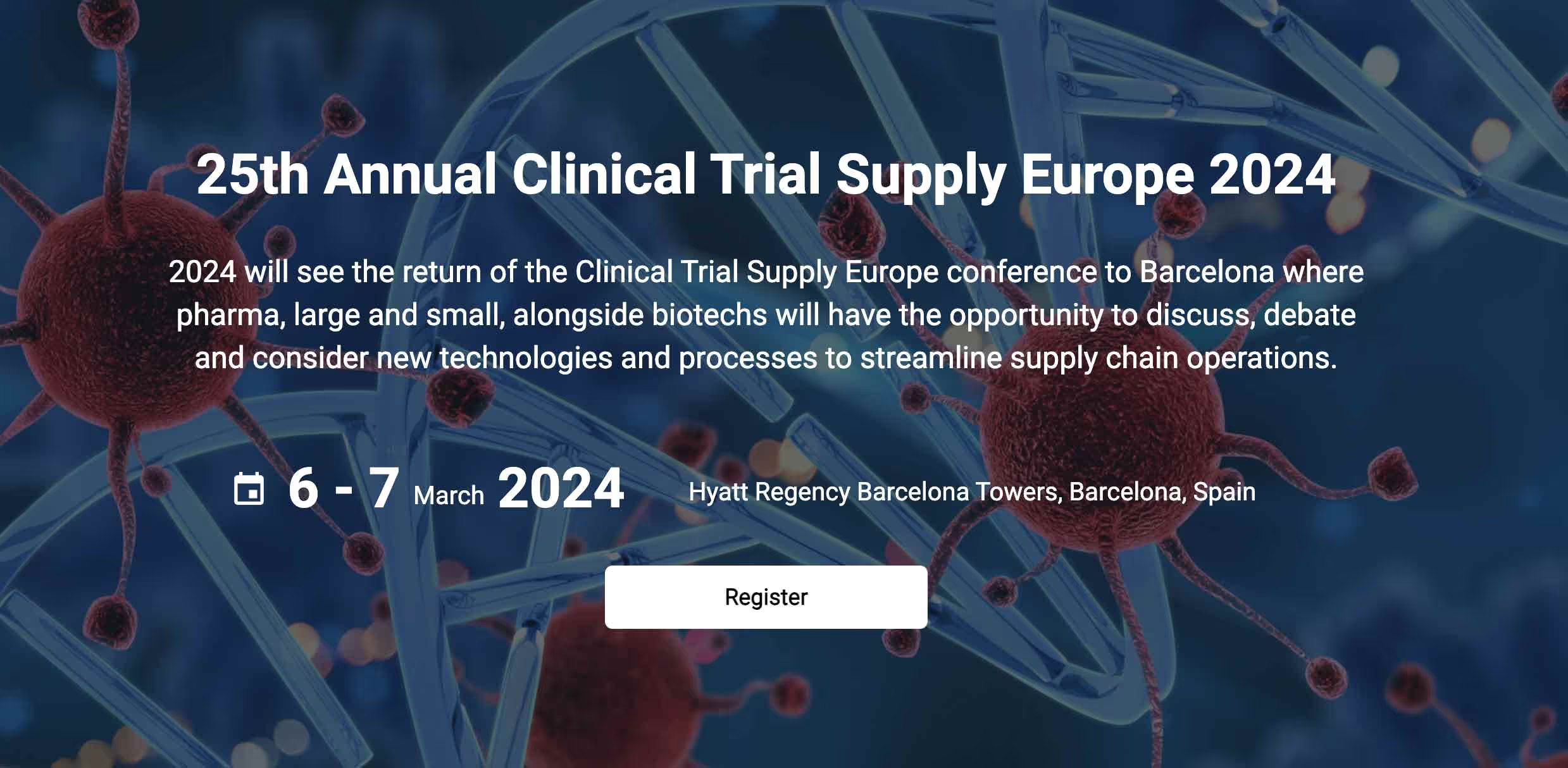
Join us at Clinical Trial Supply Europe 2024 in Barcelona
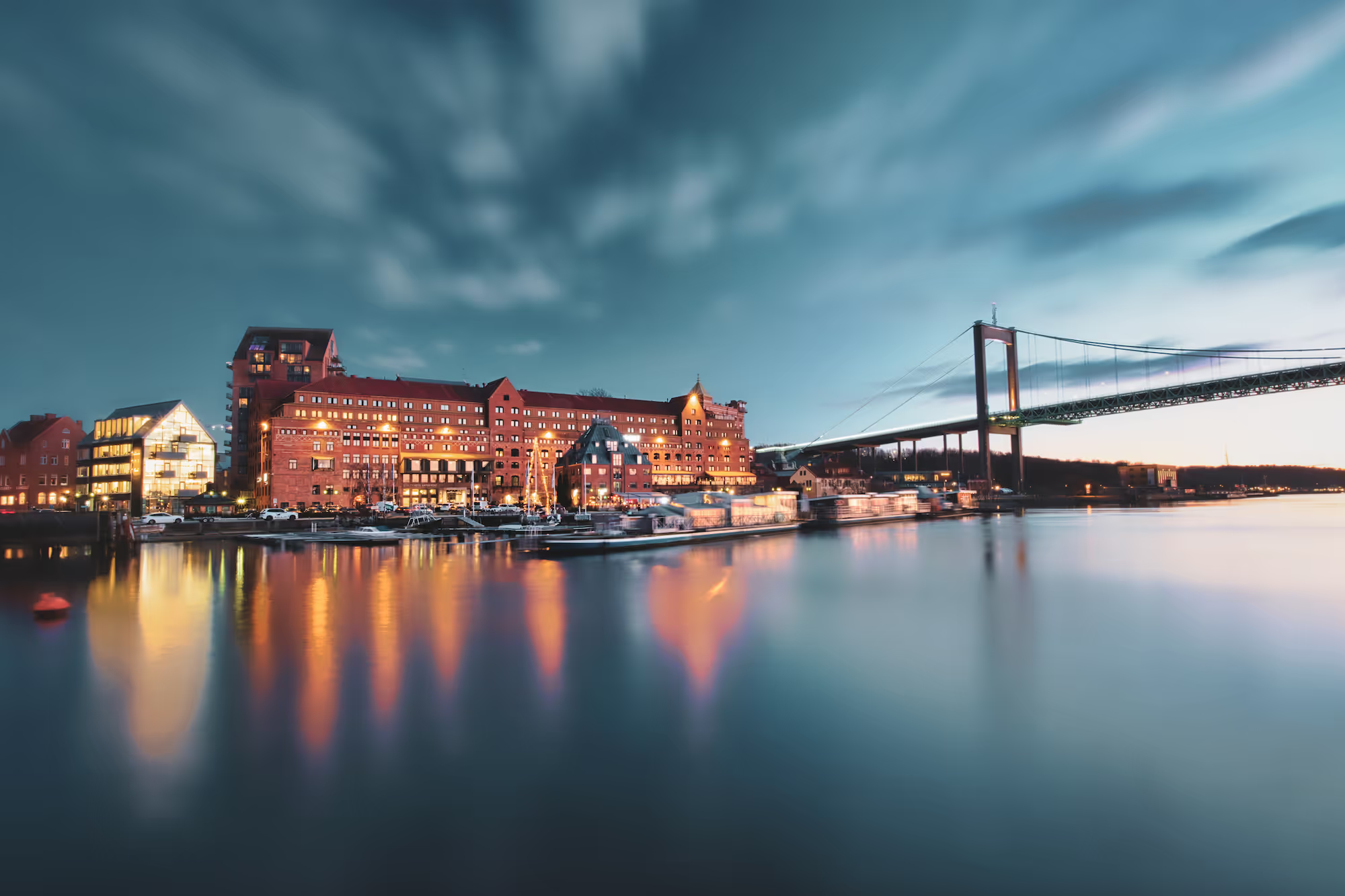
TSS User Forum 2023
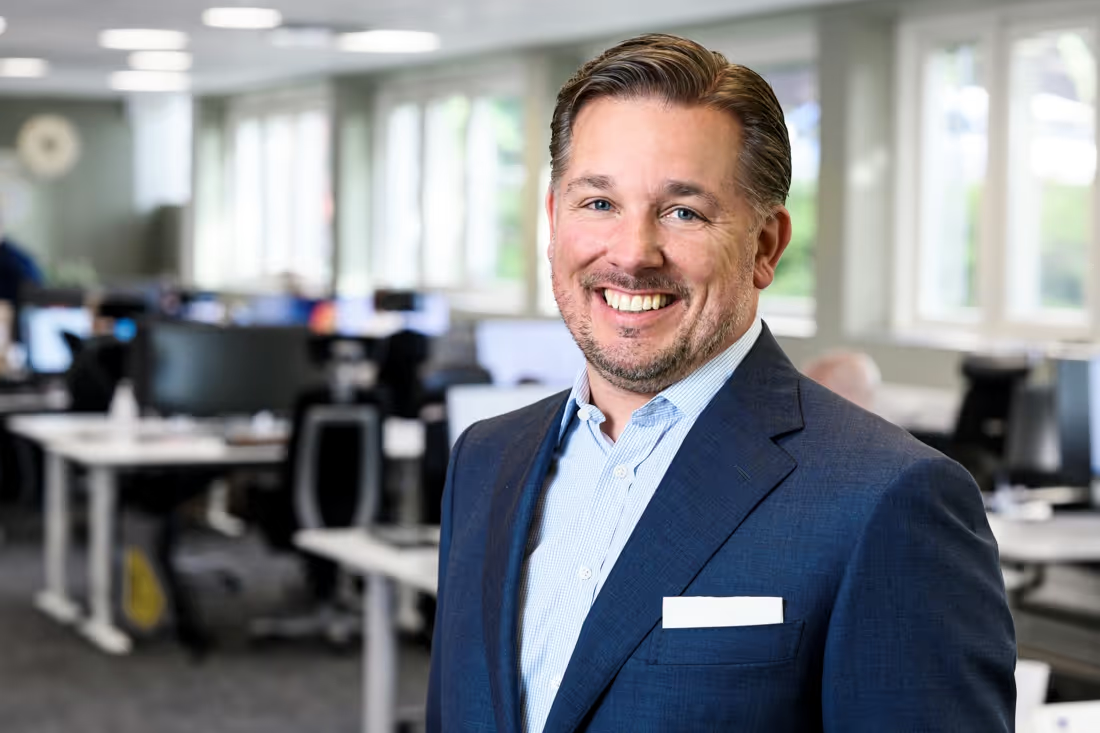
TSS Welcomes Gustaf Rasin as New Chief Operations Officer
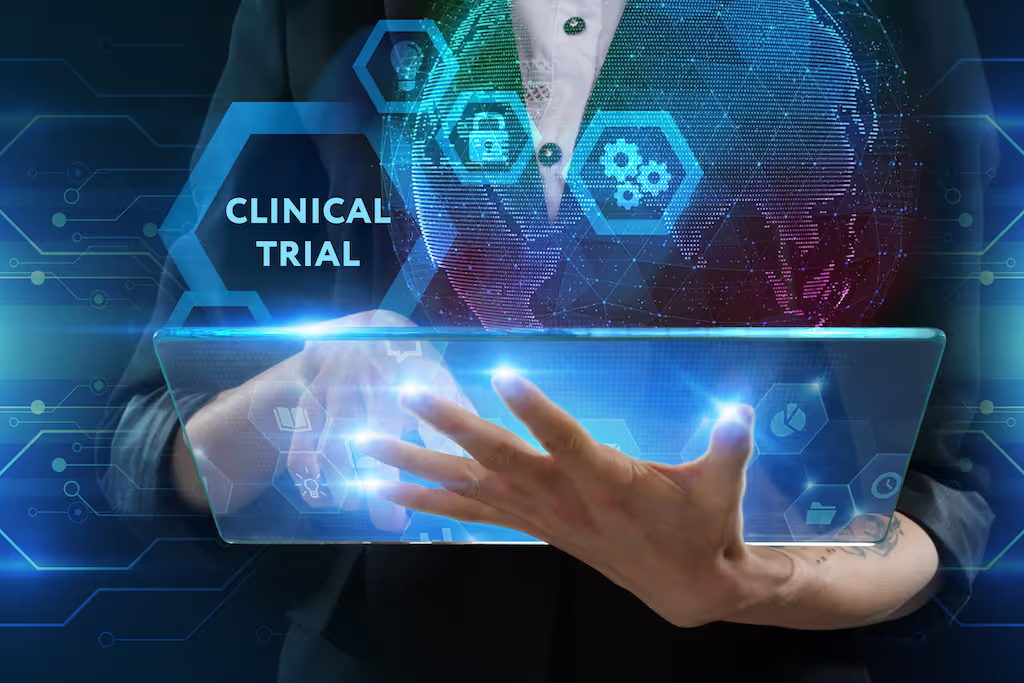
NECSO Cambridge 2023
.avif)
TSS Welcomes Thomas Lindén as New Chief Technology Officer
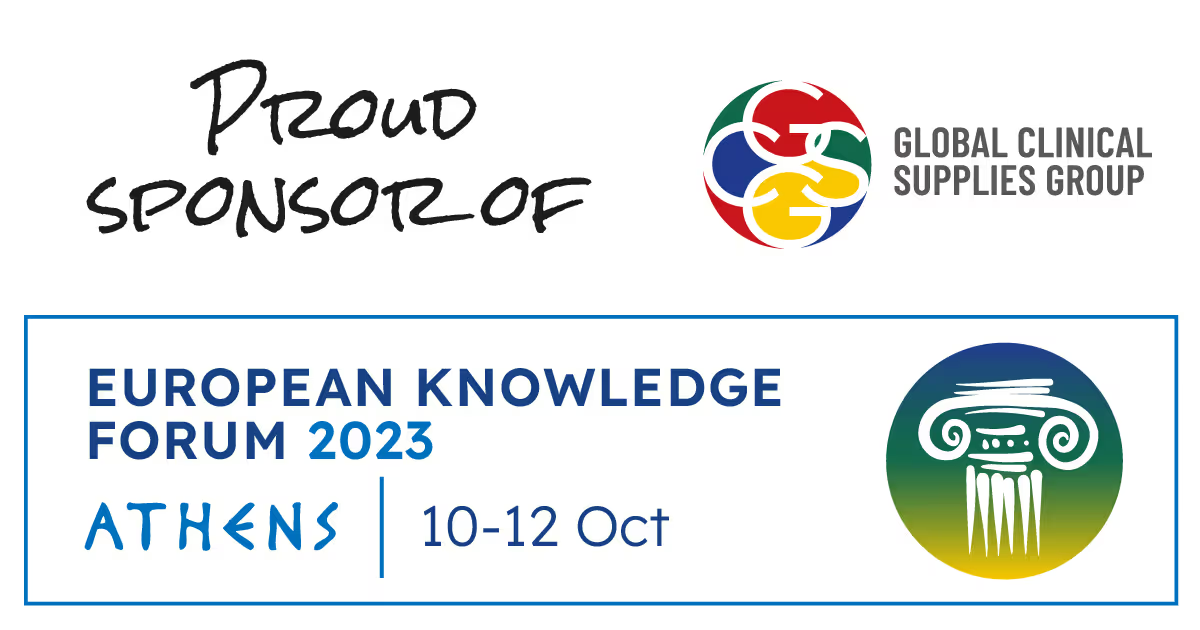
GCSG Athens 2023 Vendor Showcase Hosted by TSS
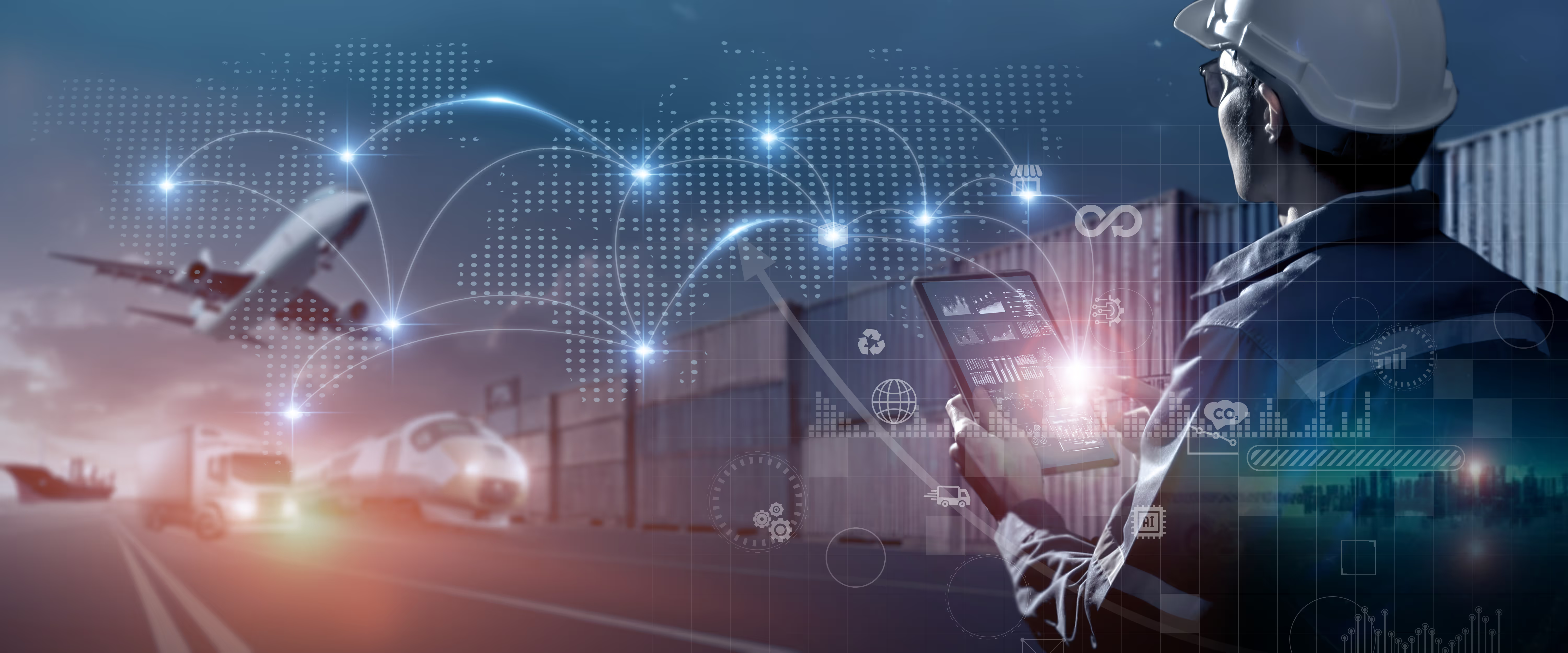
How GSK Pharma in UAE optimized the supply chain through automatization
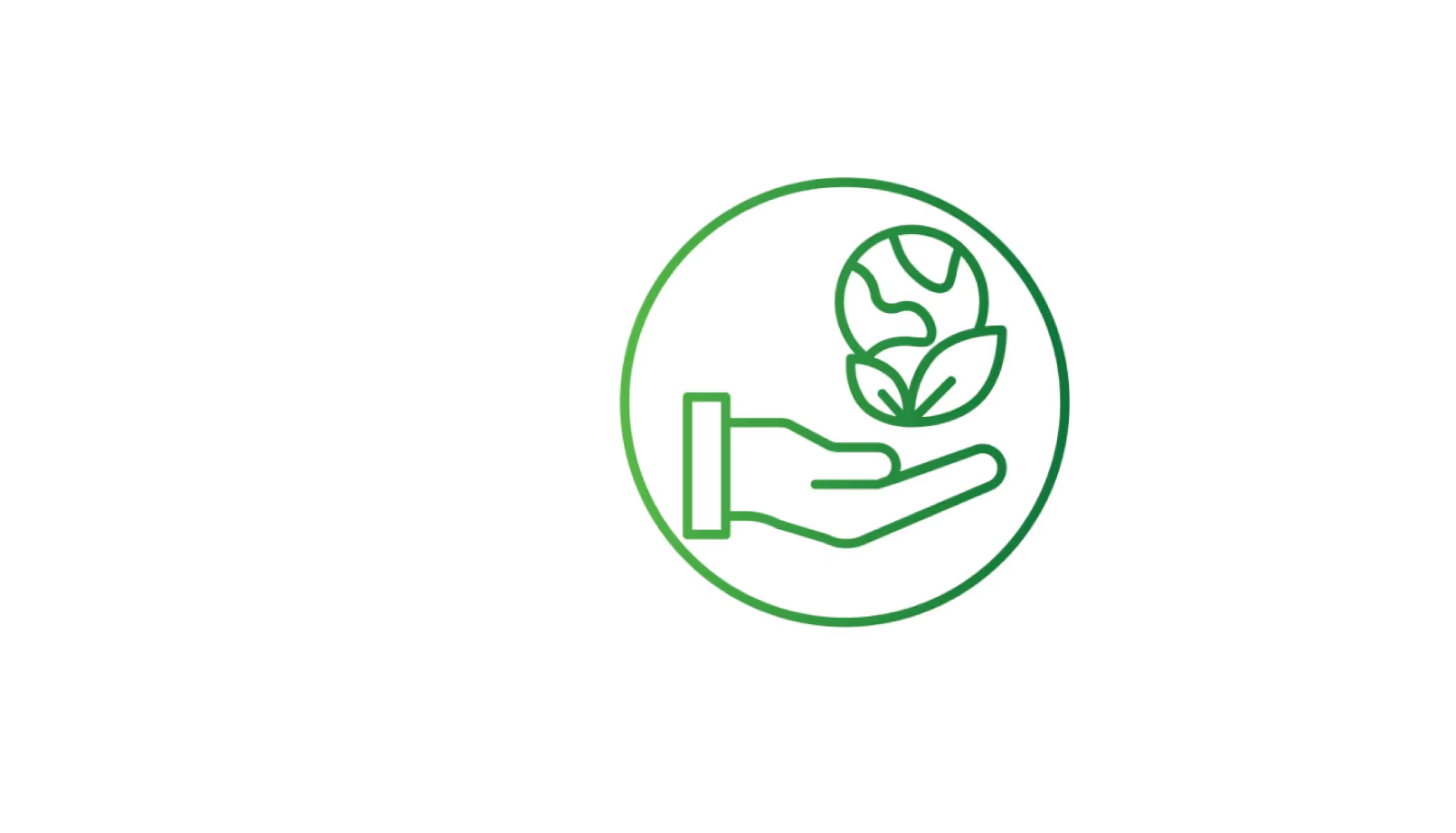
Cooperation with Swedish Innovation Authority and University to Optimize Sustainability Procedures
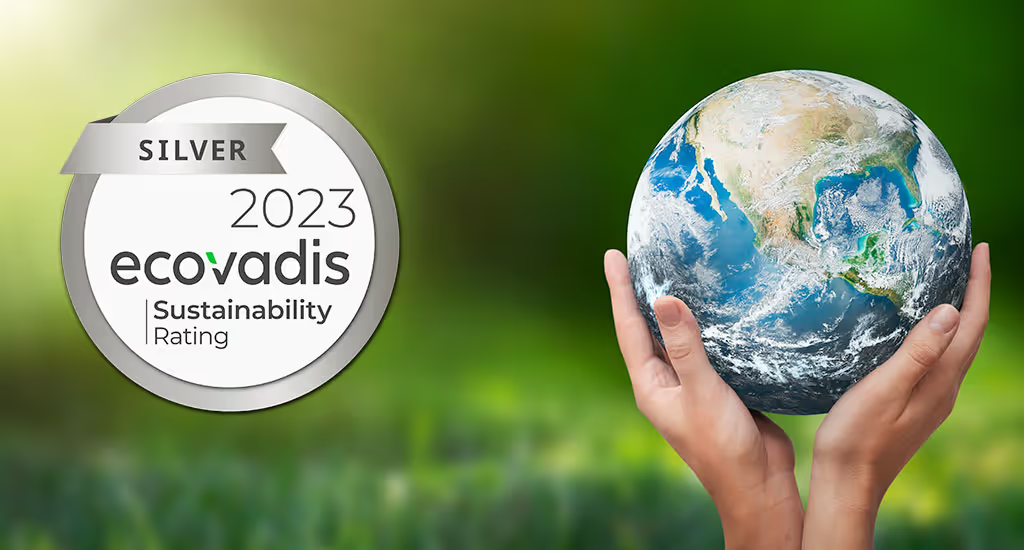
TSS Achieves EcoVadis Silver Medal for Advanced Sustainability Performance
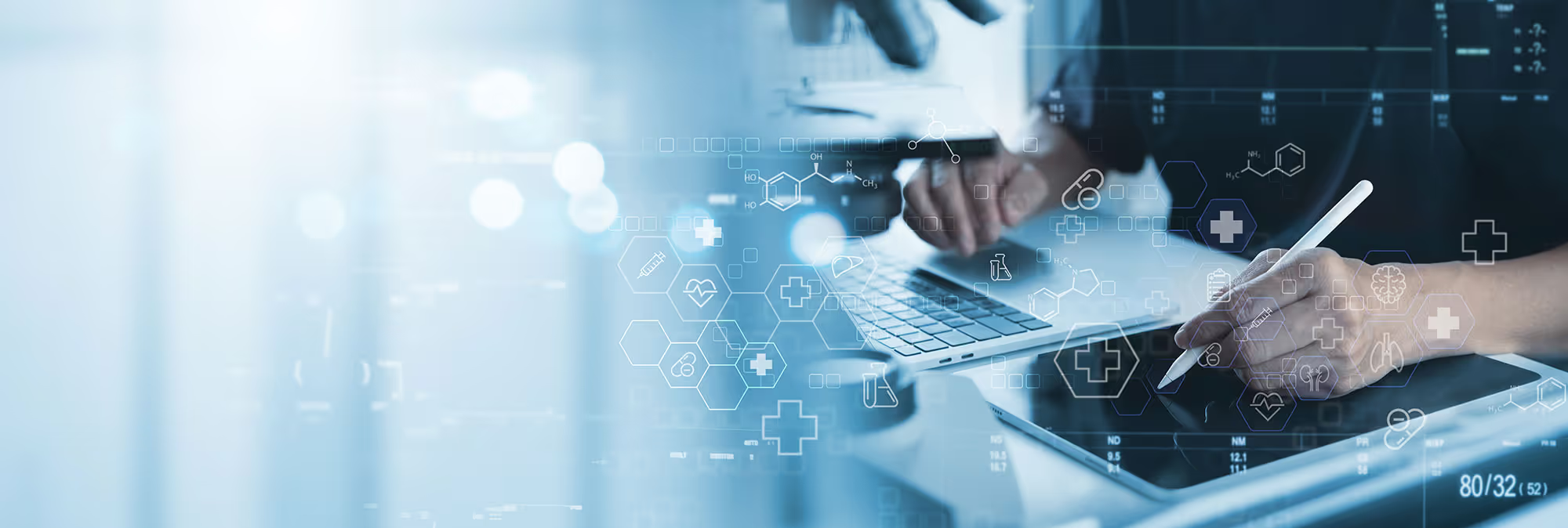
How can maturity in temperature management move your decision process from days to seconds?
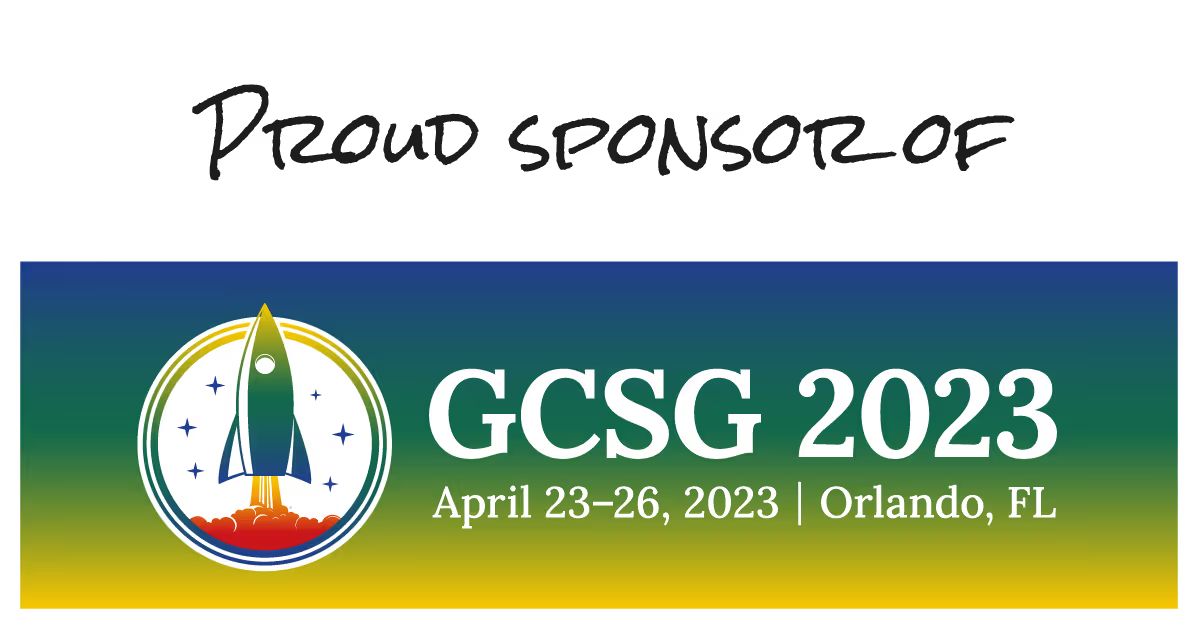
GCSG 2023 US Conference
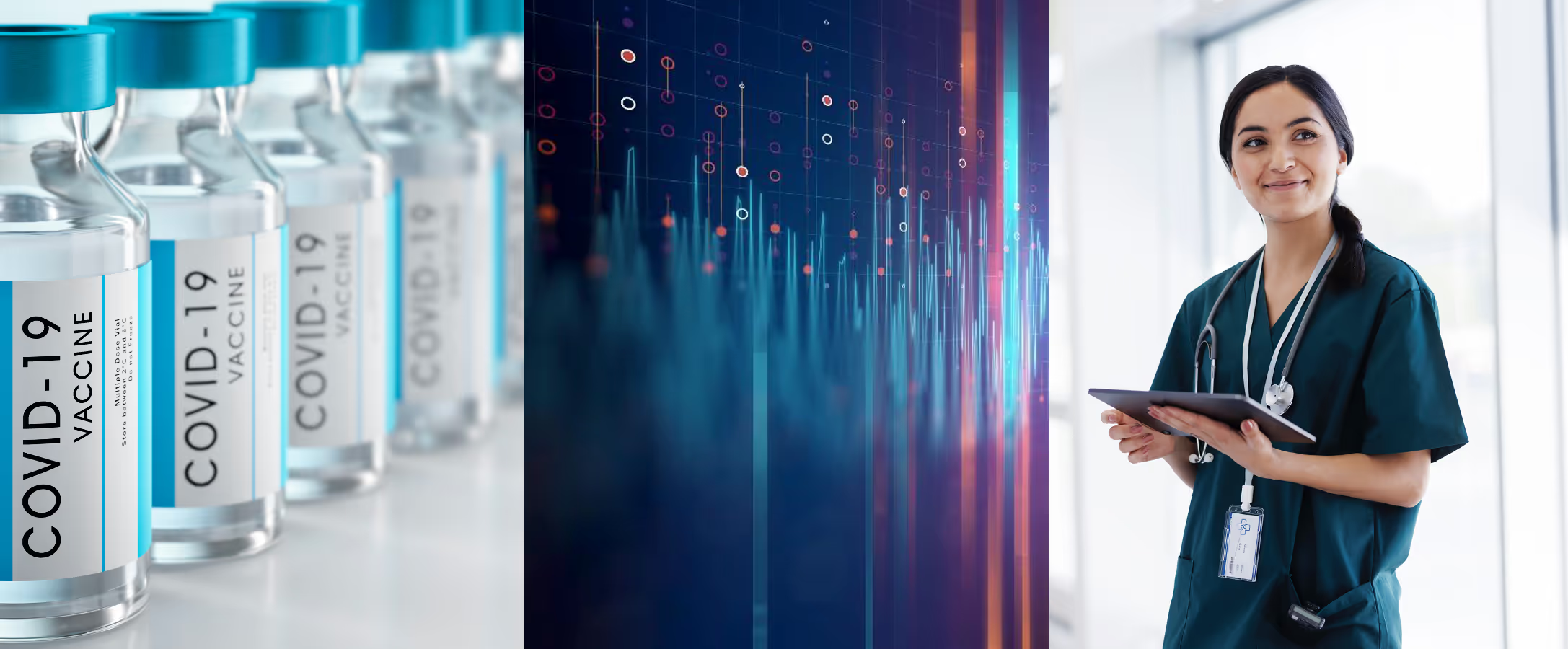
3 steps to accelerate Decentralized trials & Release to patients
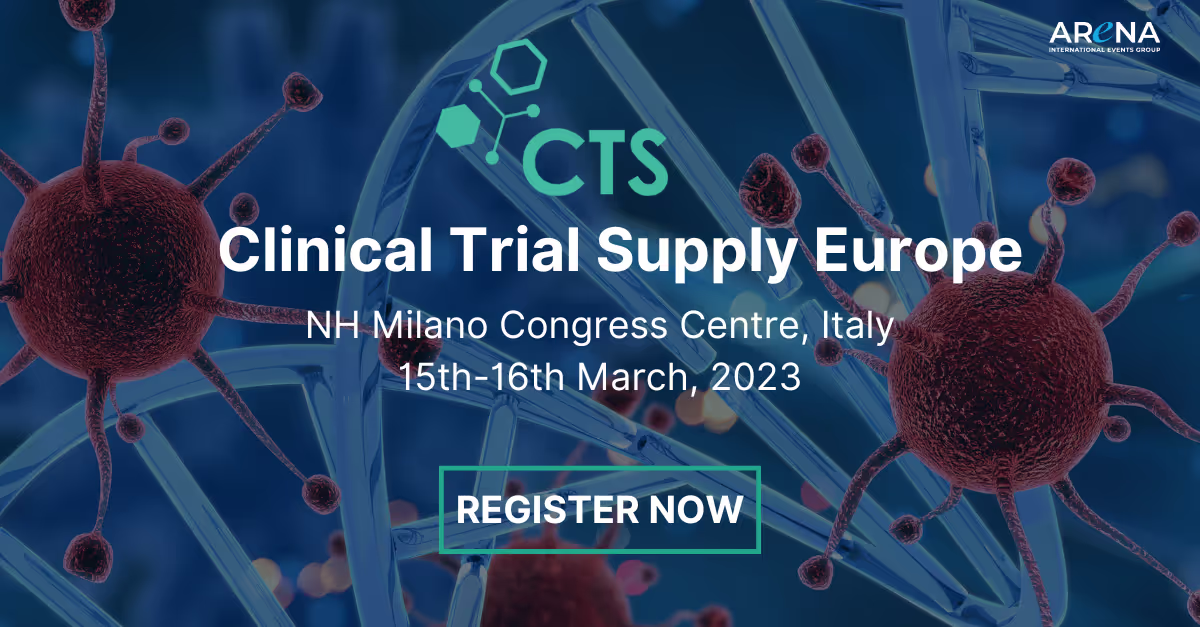
Join us at Clinical Trial Supply Europe 2023
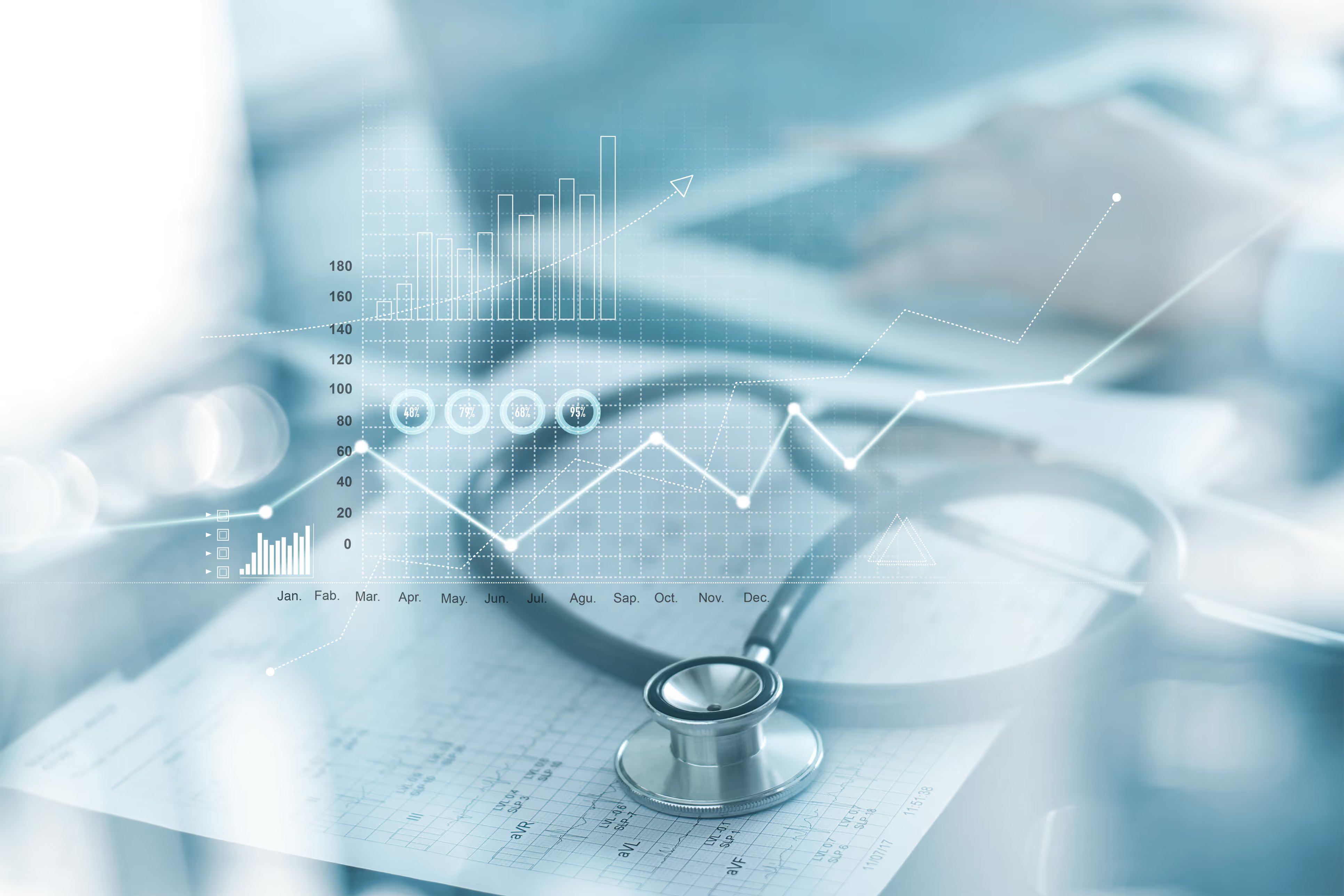
We are back at Clinical Trial Supply East Coast
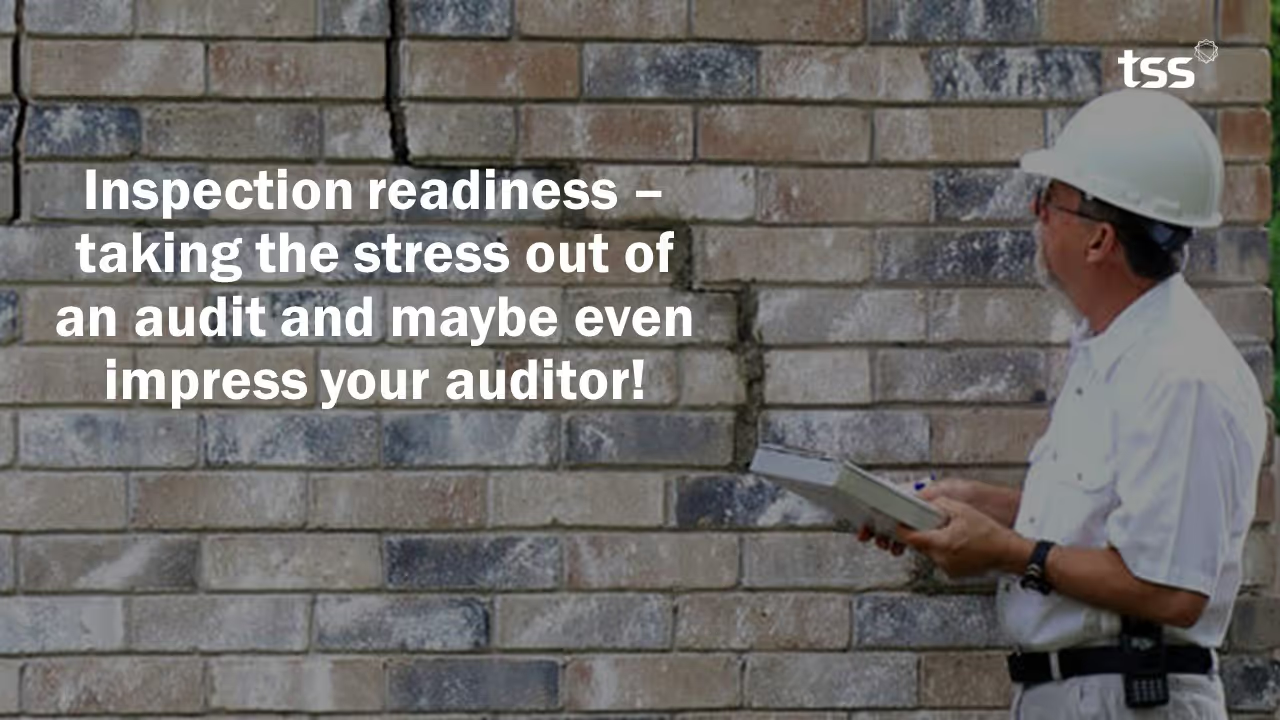
The GCSG 2022 European Knowledge Forum is coming up, and we will be there.
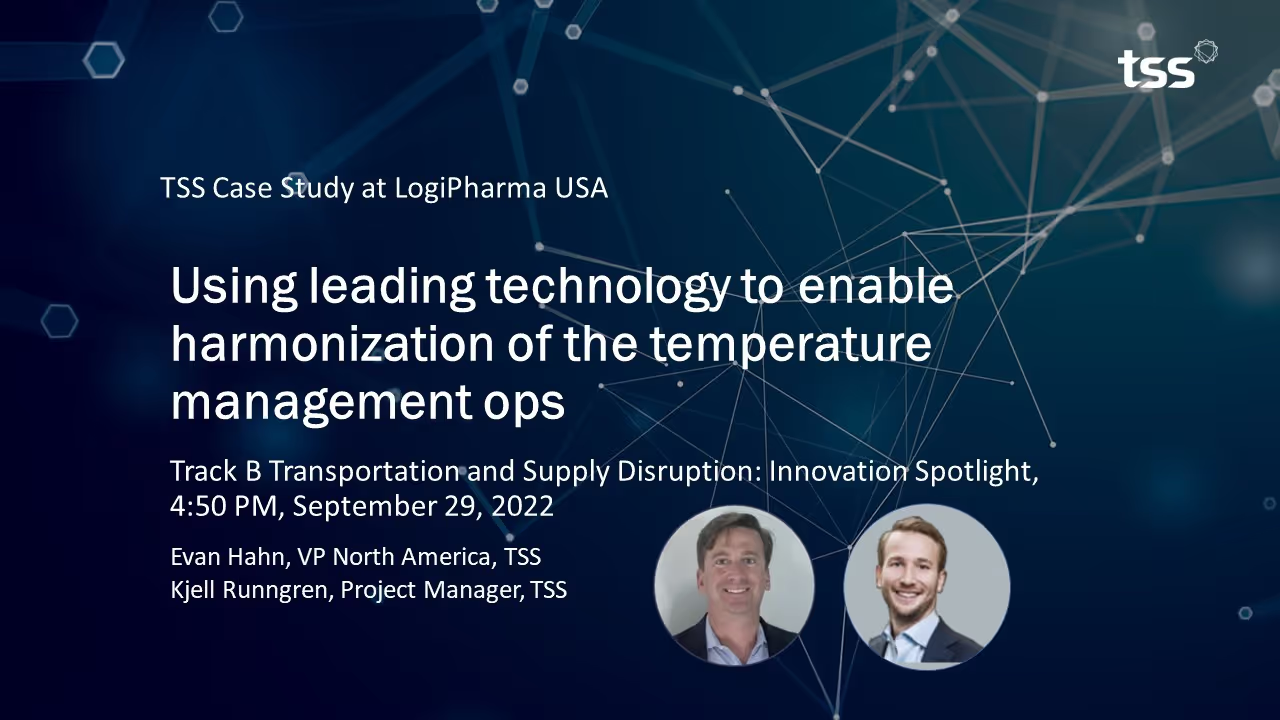
Meet us at Logipharma US in Boston on September 29th-30th
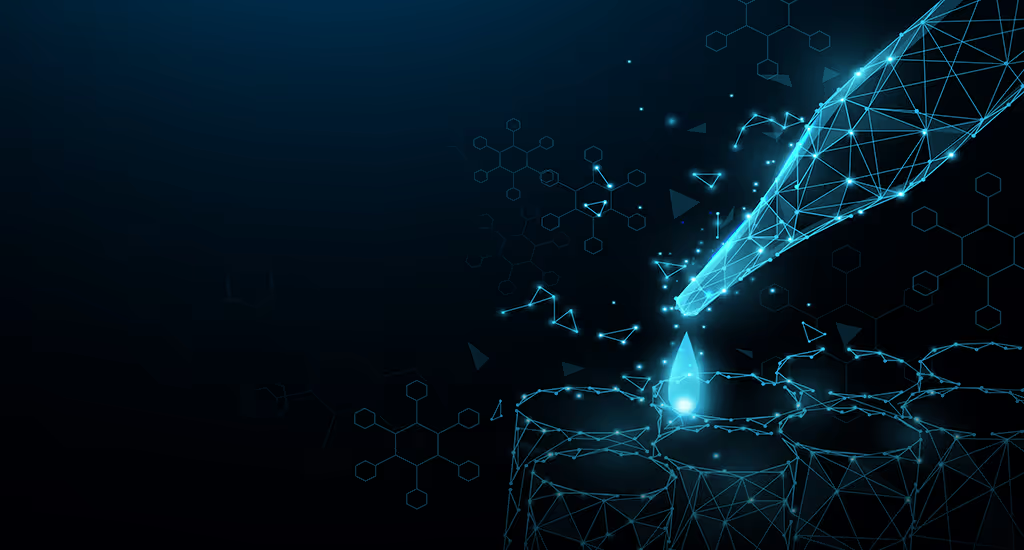
Boost value in clinical trial management with two-way integrations
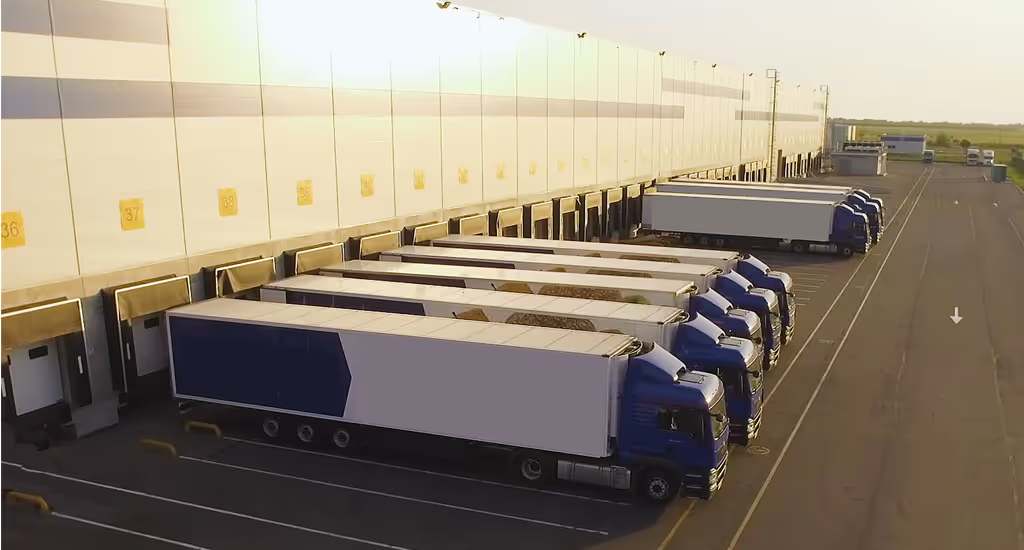
Achieving pharma supply chain excellence through integrations
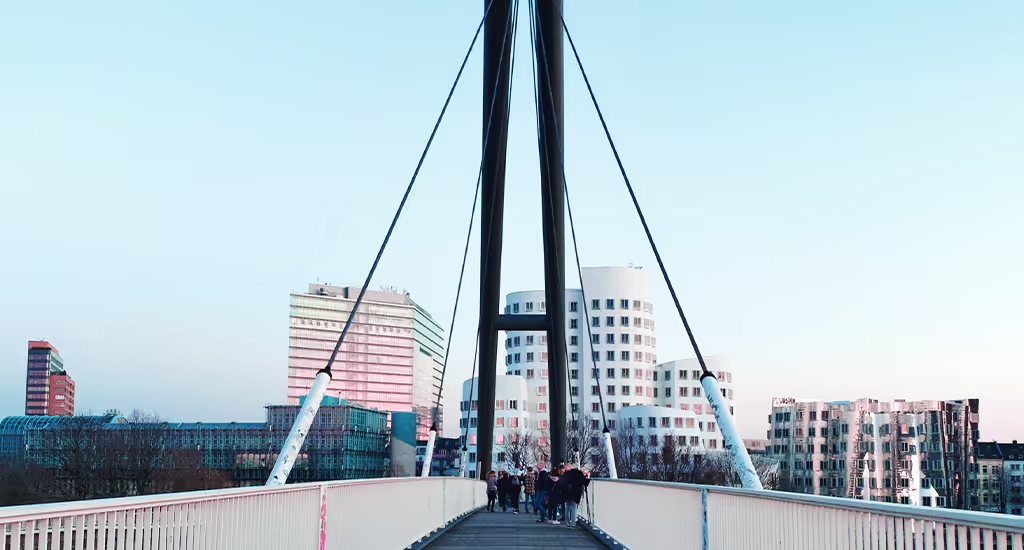
Join us at Temperature Control & Logistics in Düsseldorf

Meet our people: Quality Engineer, Akanksha Sharma
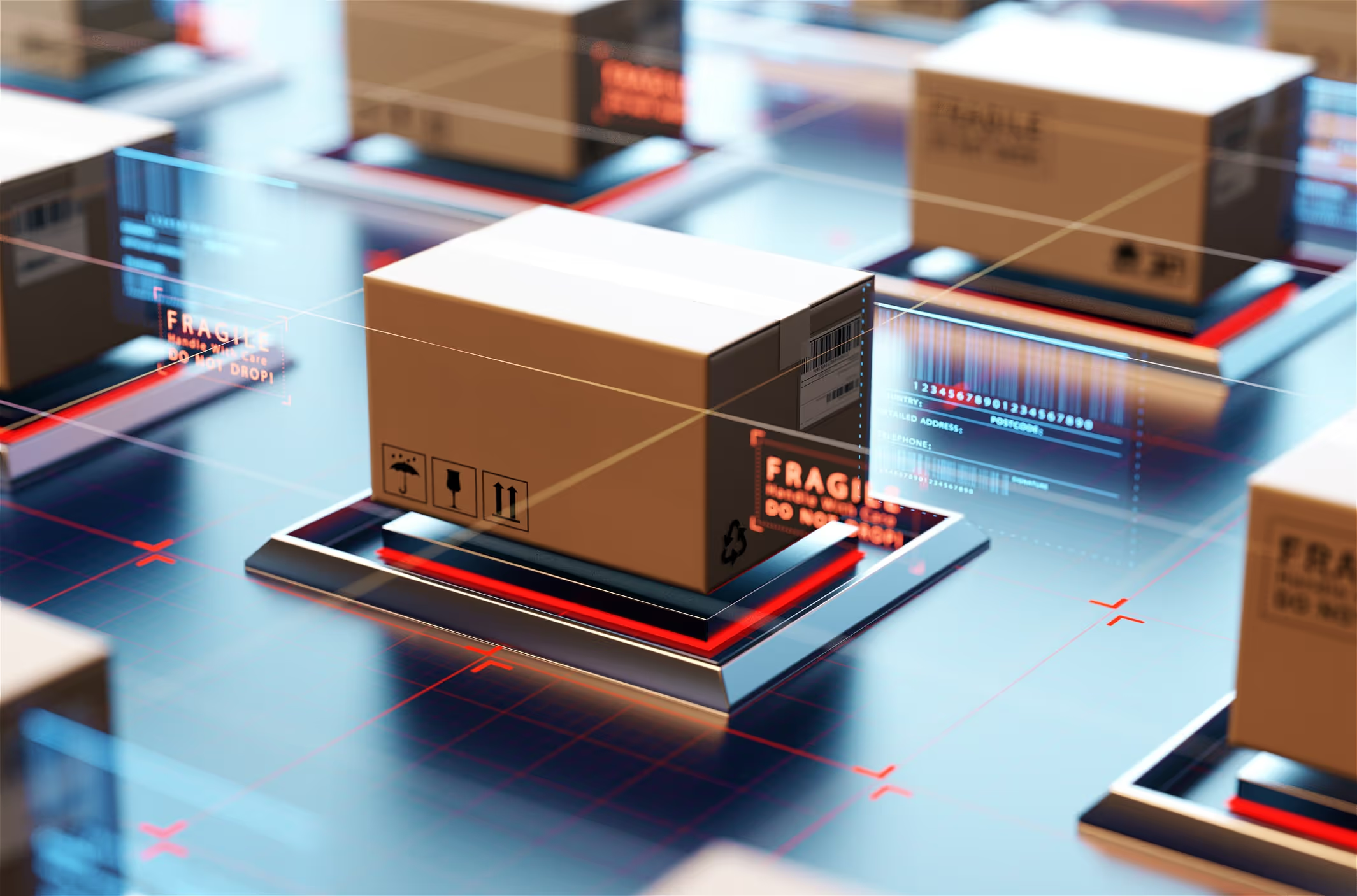
Is your supply chain ready for a digital transformation?
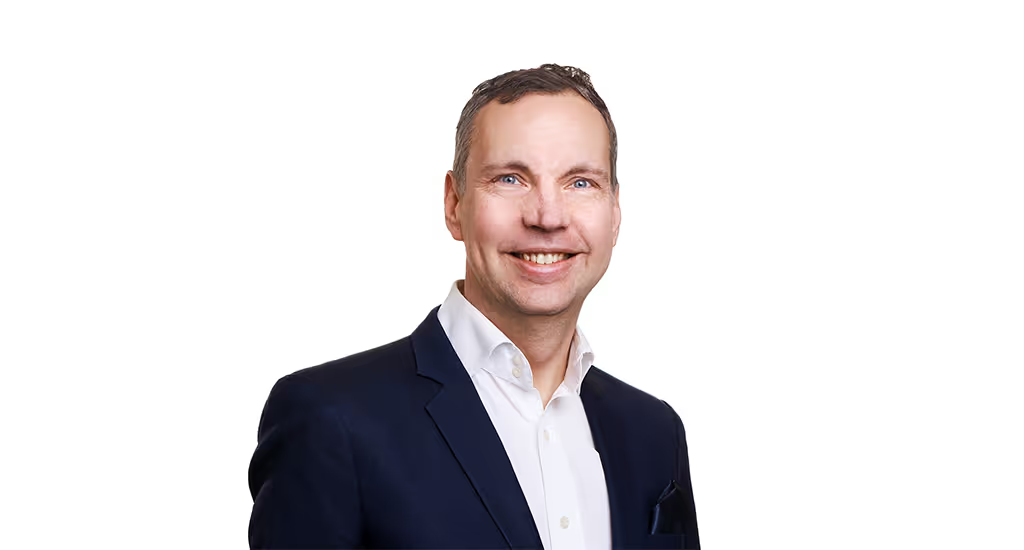
Q&A with Claes Kalderén: Our European Sales Manager
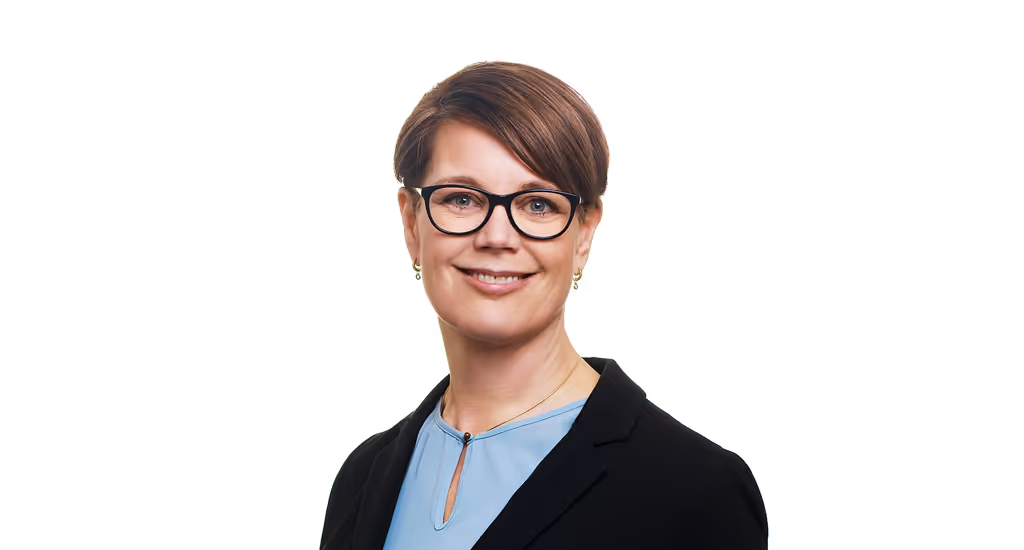
Meet Johanna Eriksson, Chief Product Officer at TSS
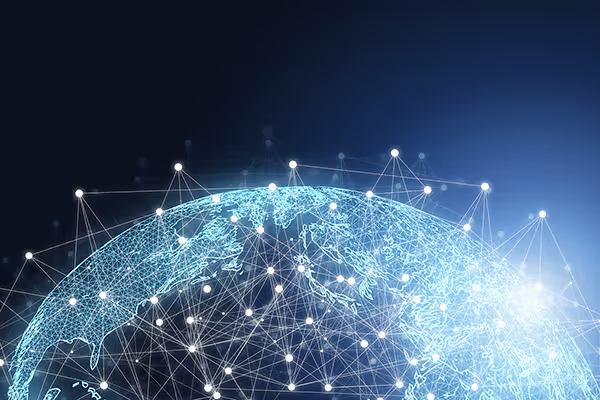
On-demand webinar: Maximize value with 2-way integrations in Clinical Trial Management
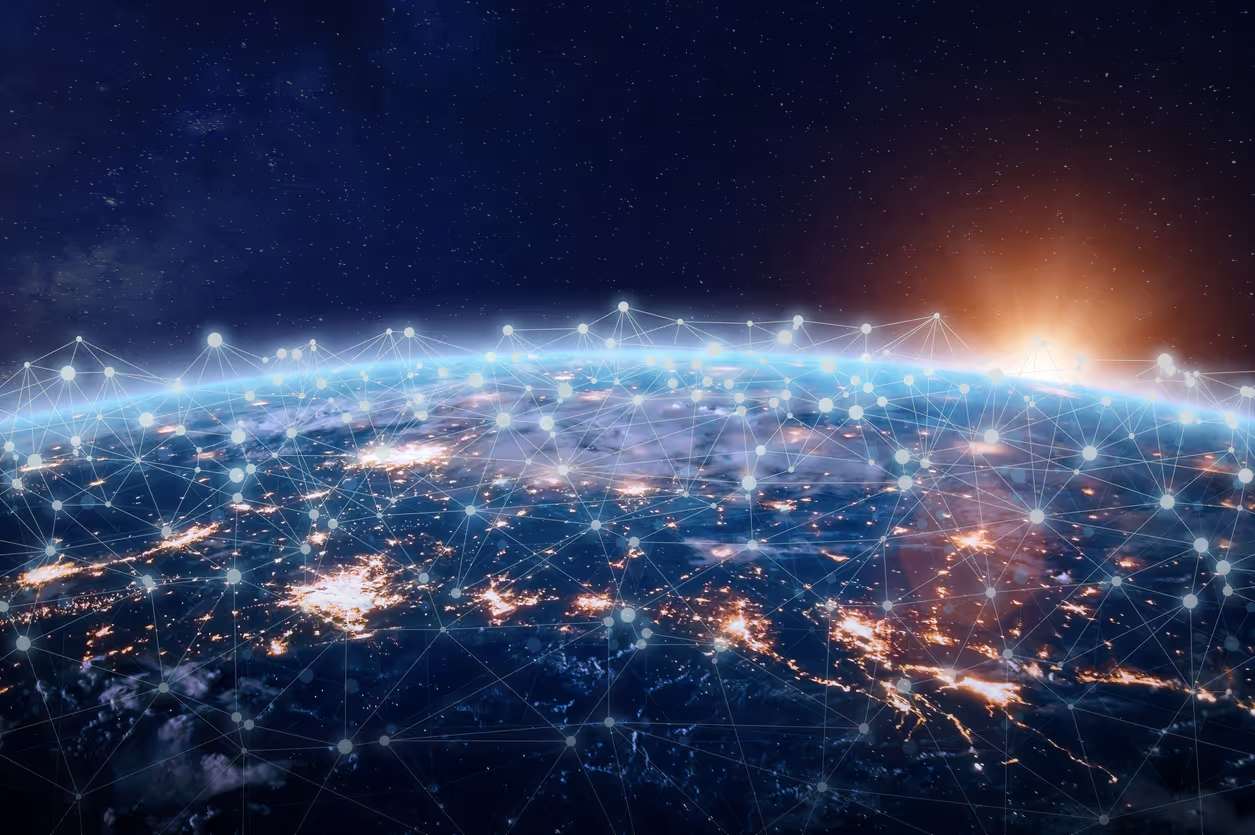
White paper: the future, today - the next generation of temperature monitoring
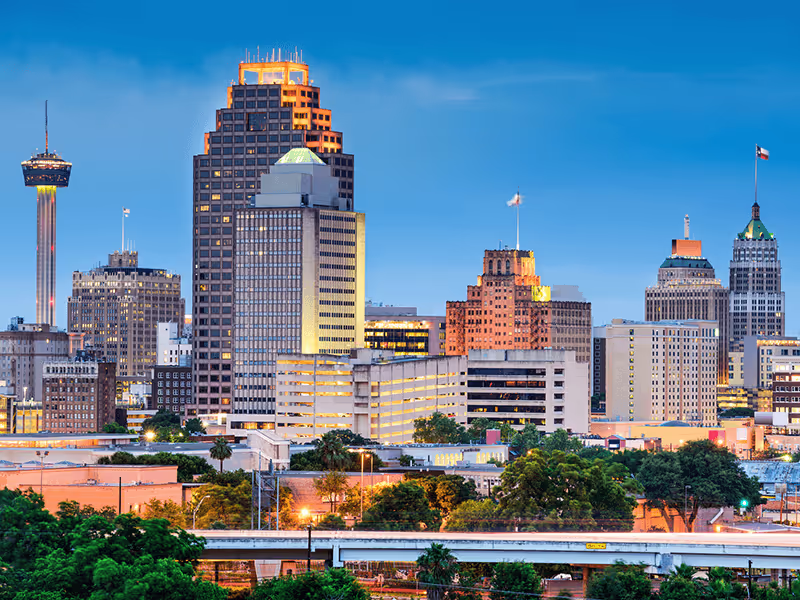
Join us at GCSC US 2022
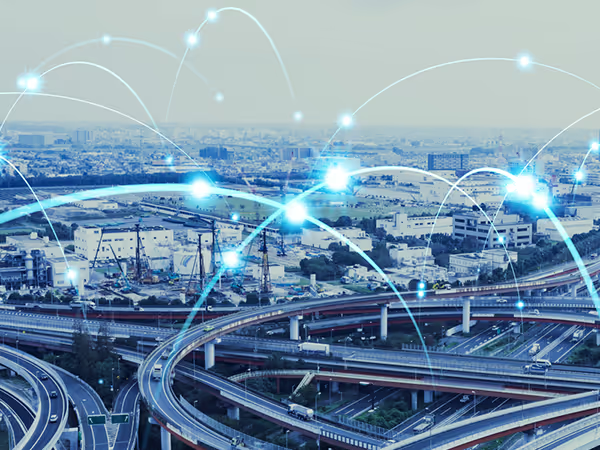
Guide: The road to digital success in temperature monitoring
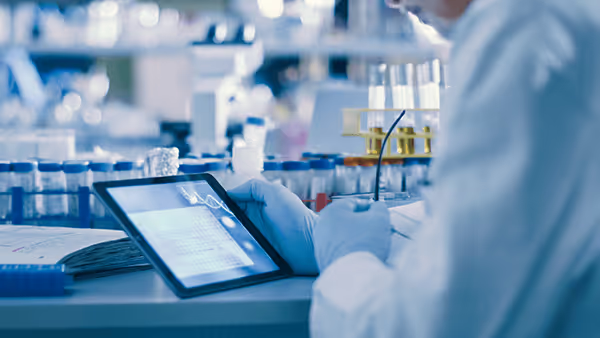
On-demand webinar: New approaches to automating temperature management in clinical trials
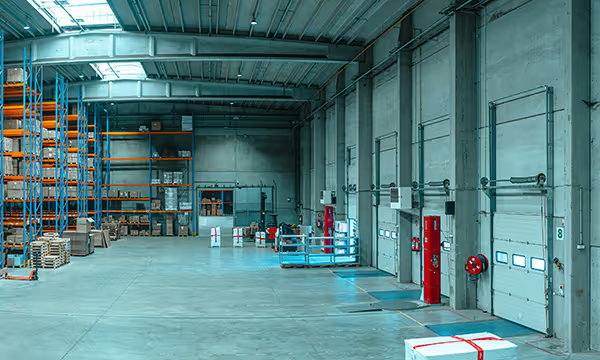
End-to-end visibility is the key to creating more efficient, cost-effective, and sustainable pharmaceutical supply chains
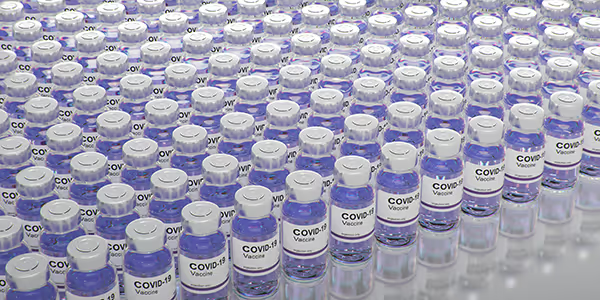
White paper: The next step to automating clinical trials
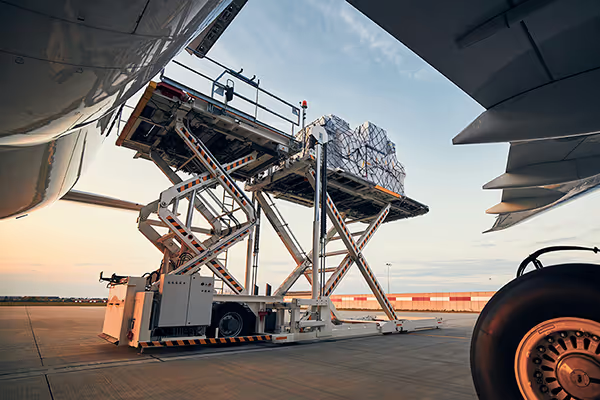
Getting the full value out of your supply chain temperature data
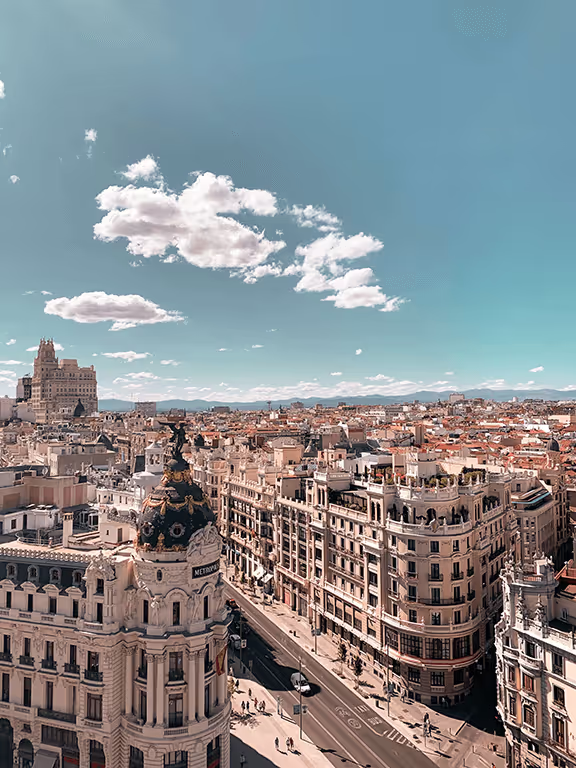
Join us at Clinical Trial Supply Europe 2022
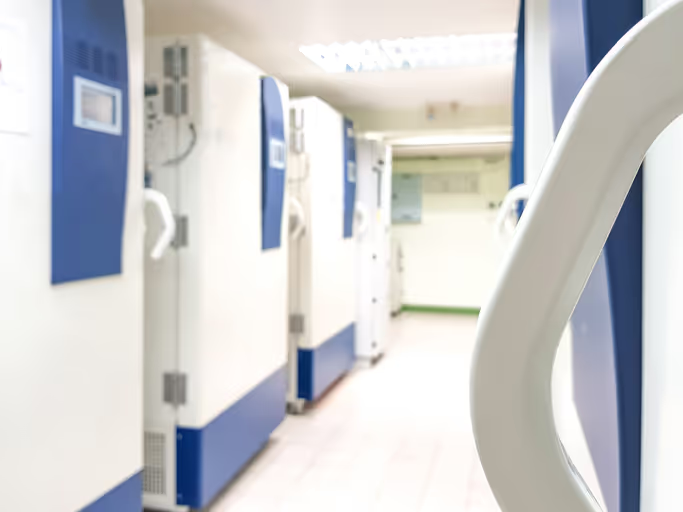
4 things to know about TSS new BLE data loggers
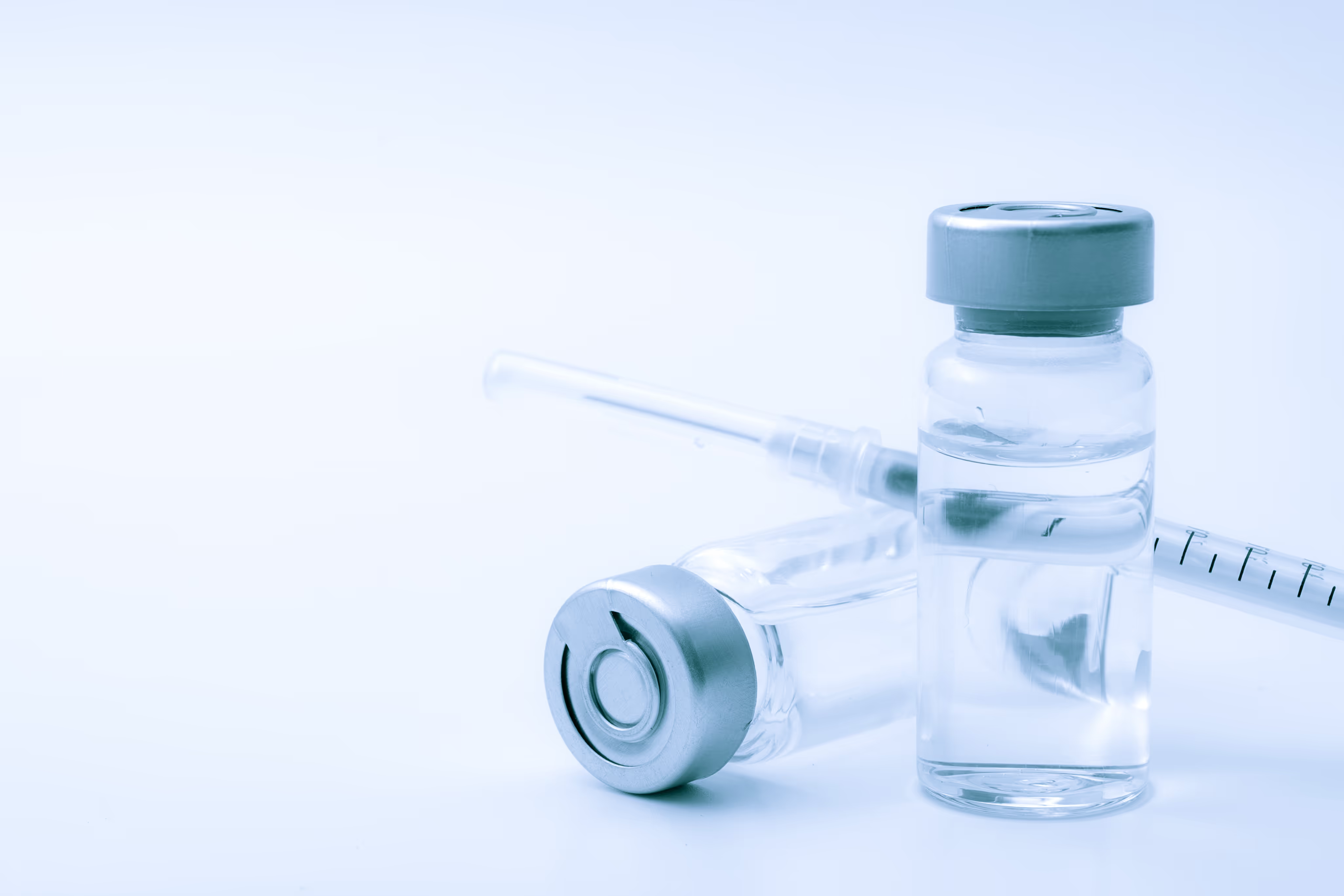
The year in review: TSS’s most-read blog articles of 2021
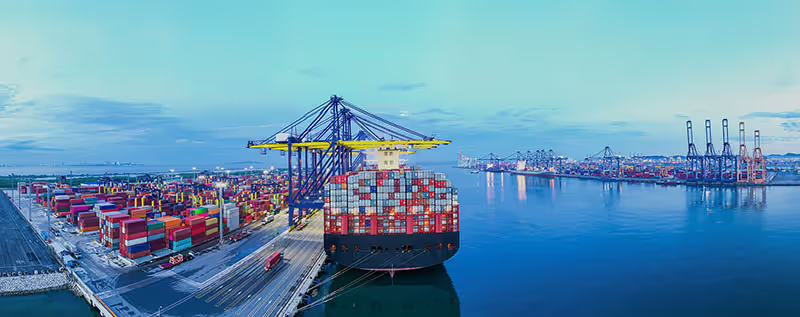
Logipharma report: A fast-track learning exercise in pharma supply chain innovation
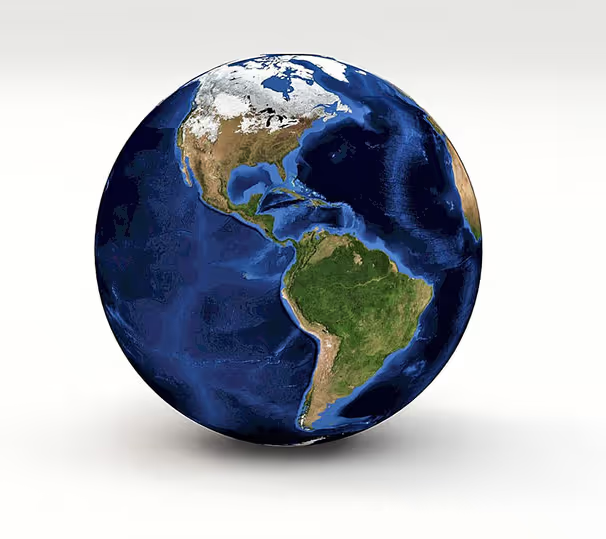
Temperature management – from local to global
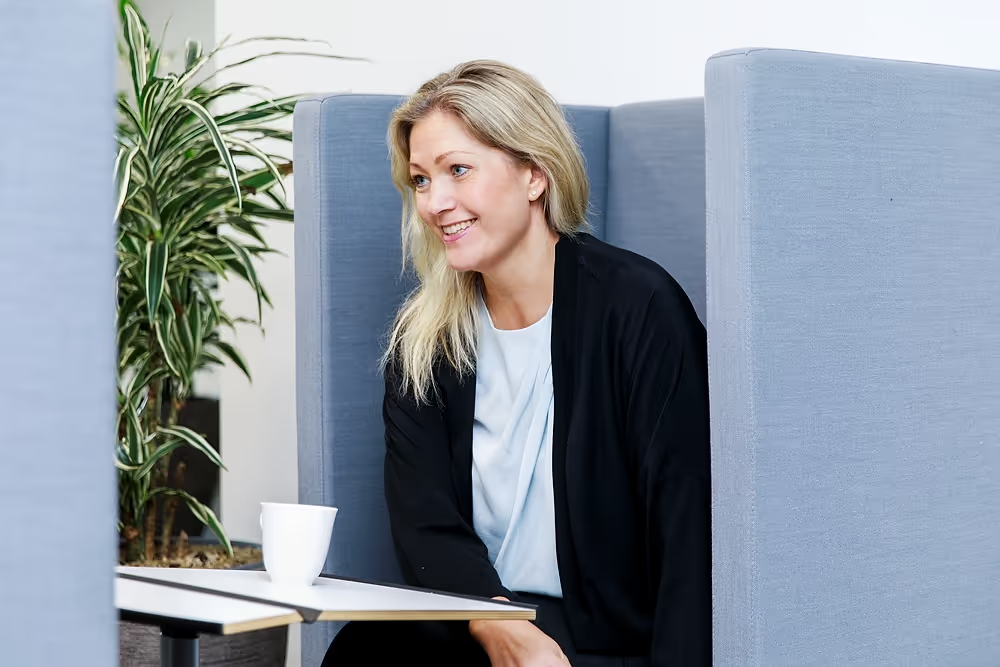
Meet Nina Nilsson, Chief Revenue Officer at TSS
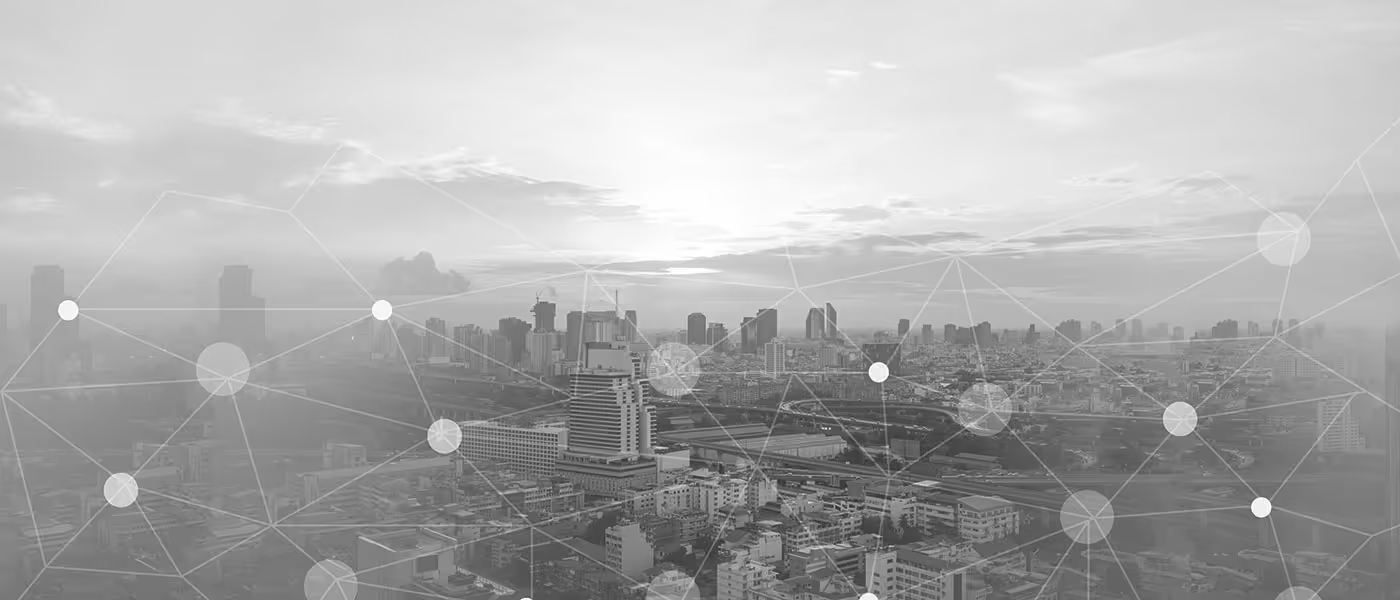
The Buyer’s guide to real-time temperature monitoring
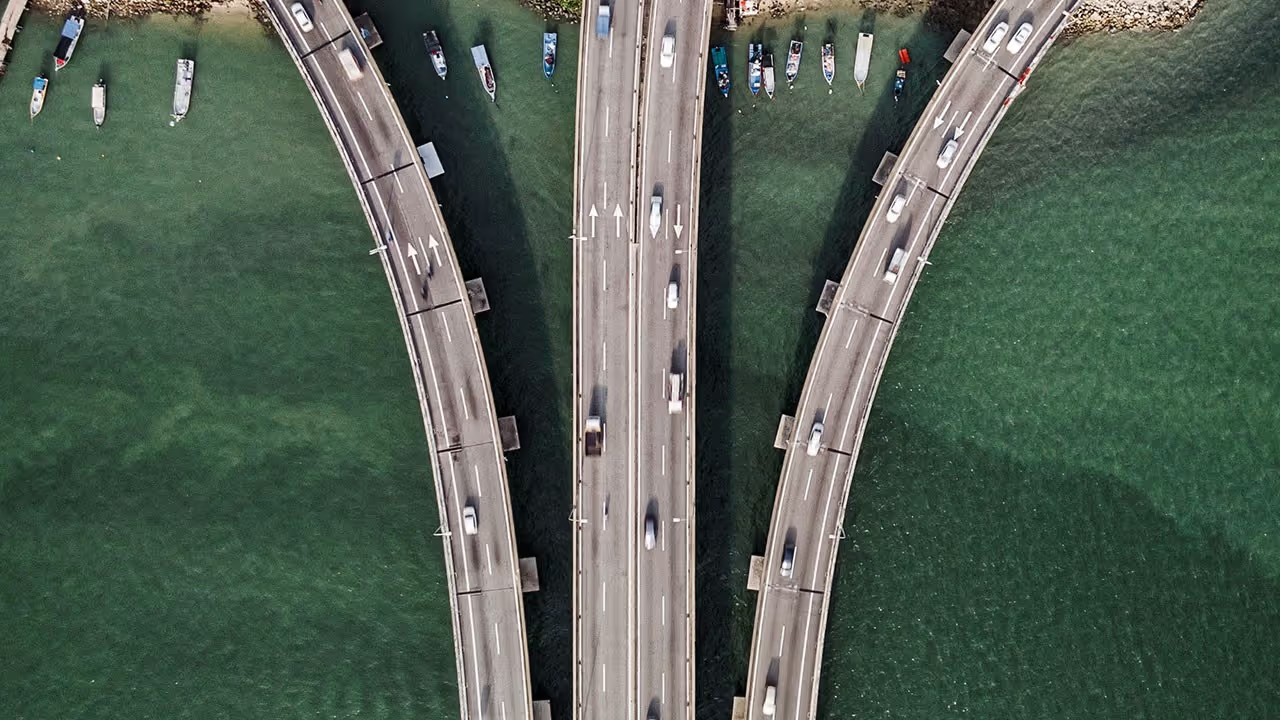
Increasing visibility with a proactive supply chain
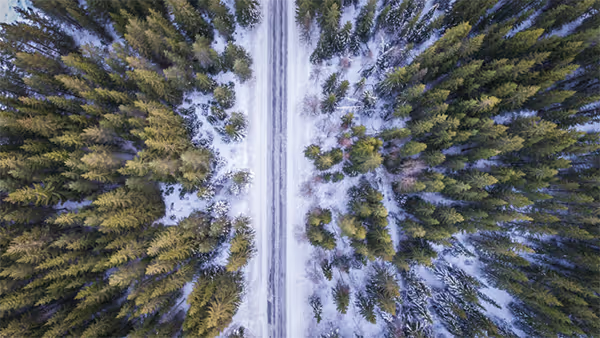
On-demand webinar: Master your supply chain with end-to-end visibility
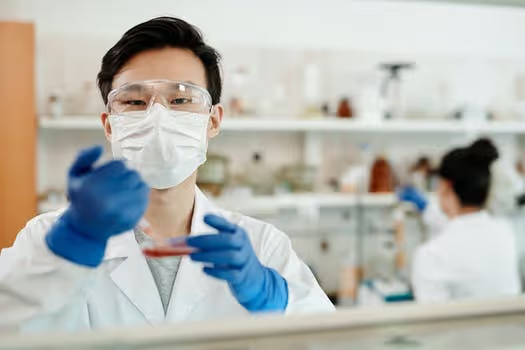
On-demand webinar: Excursion Management – From days to seconds
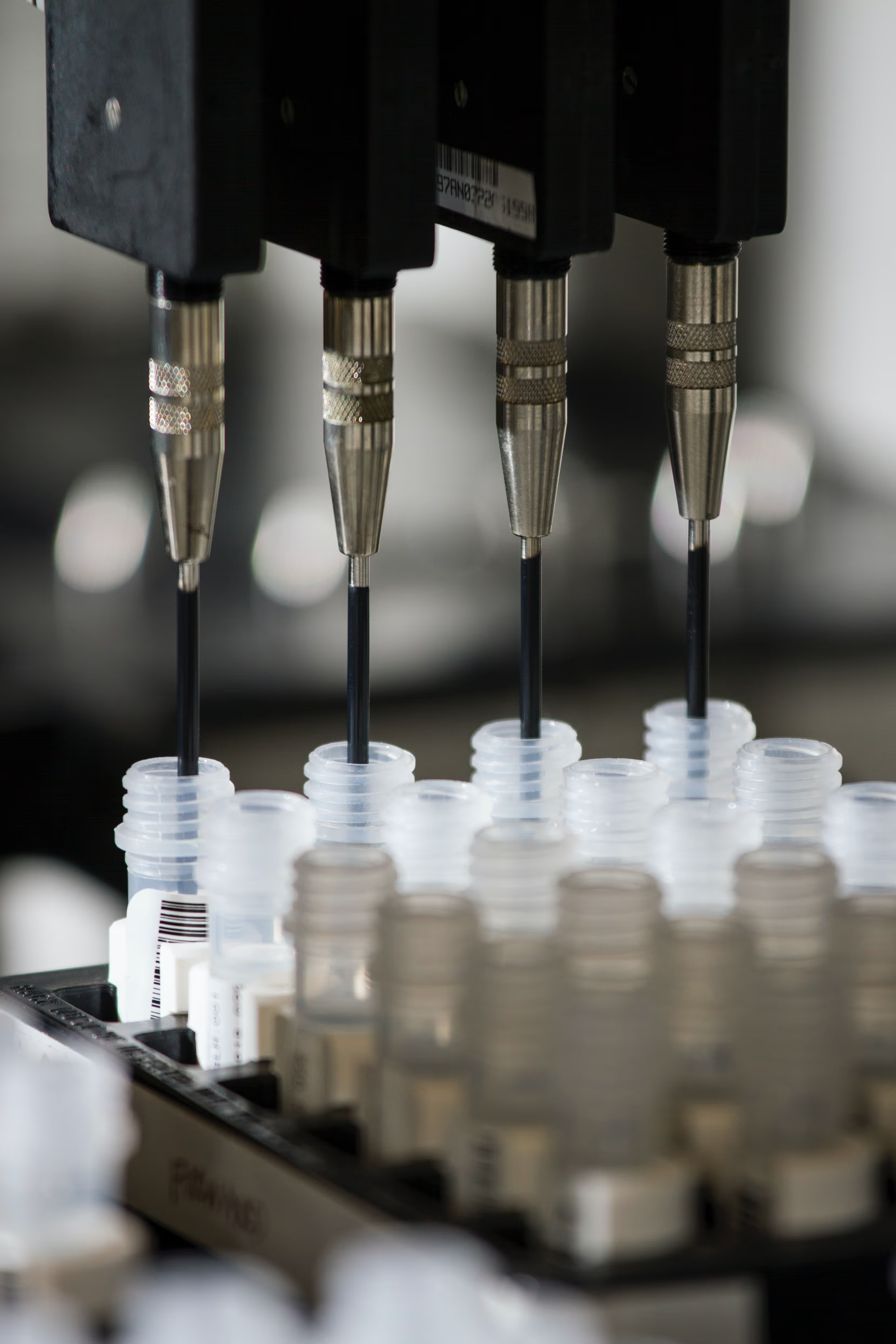
Turn days into seconds at clinical sites worldwide
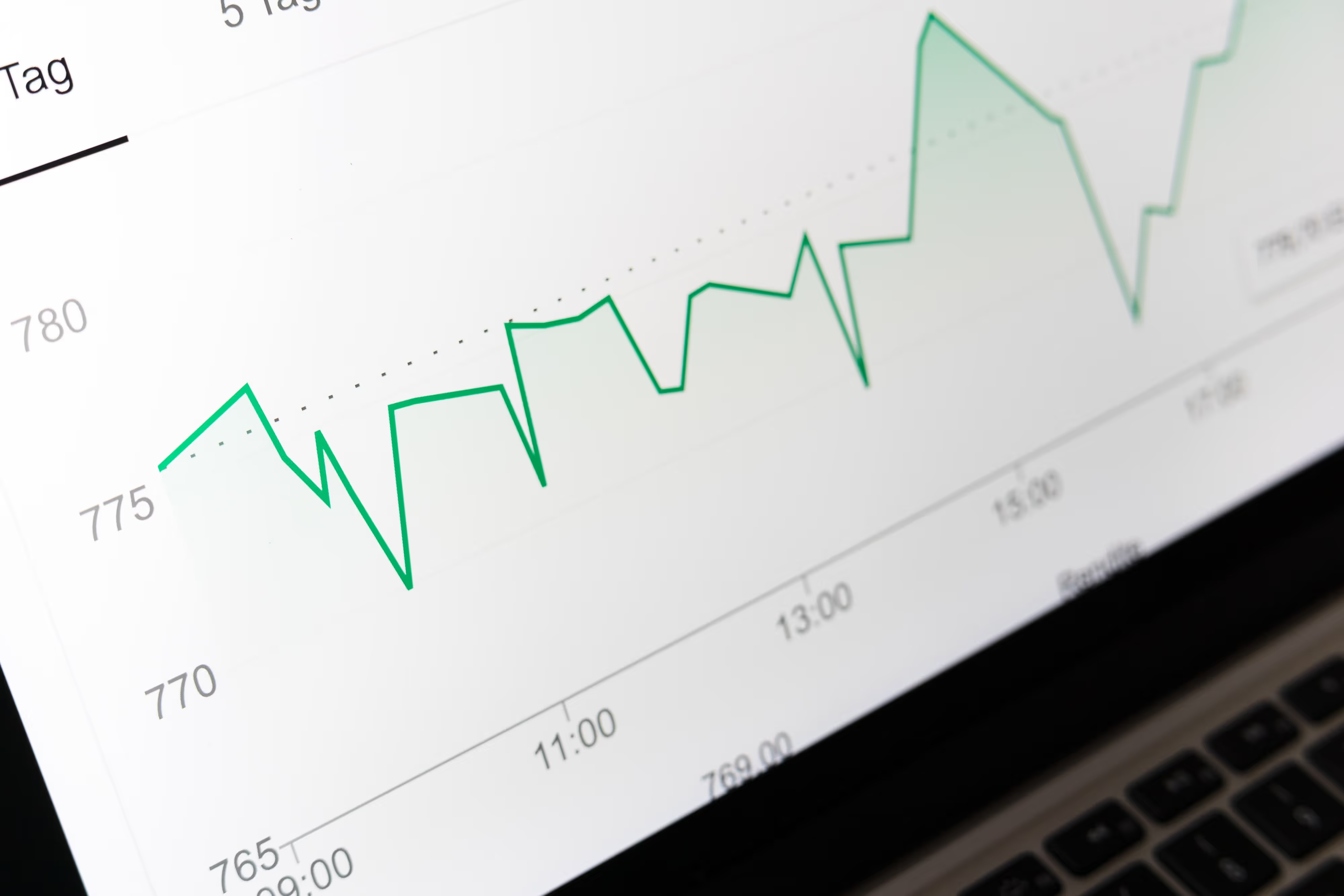
On-demand webinar: Digitalization and its impact on the pharma supply chain
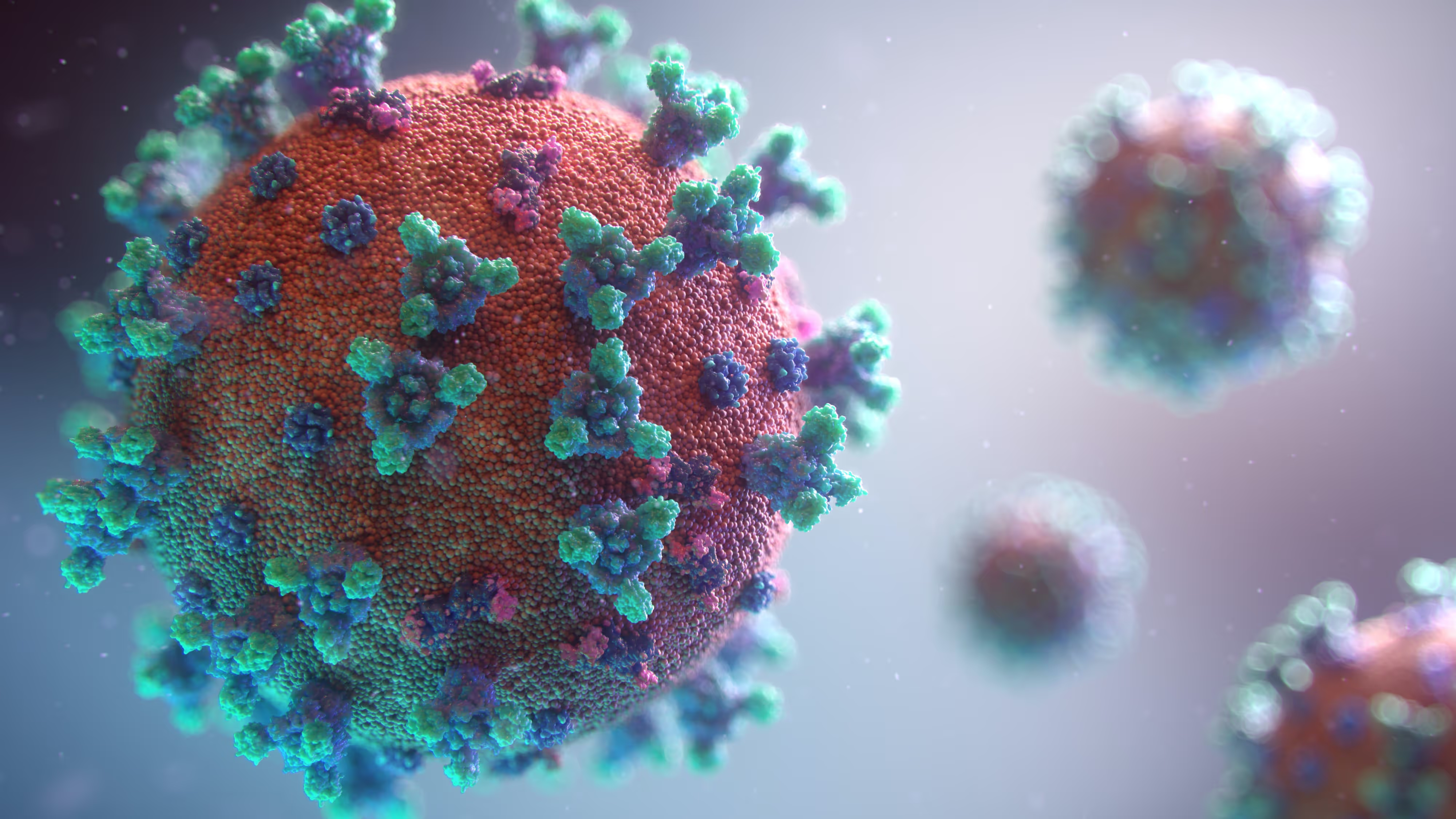
Covid-19 situation
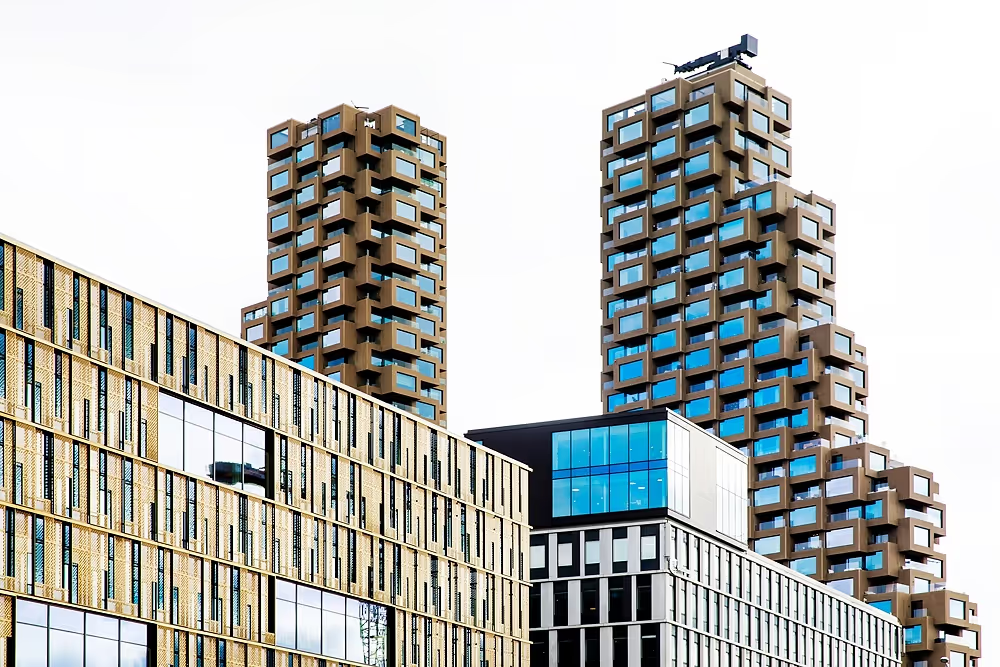
Innovation flourishes when different perspectives meet
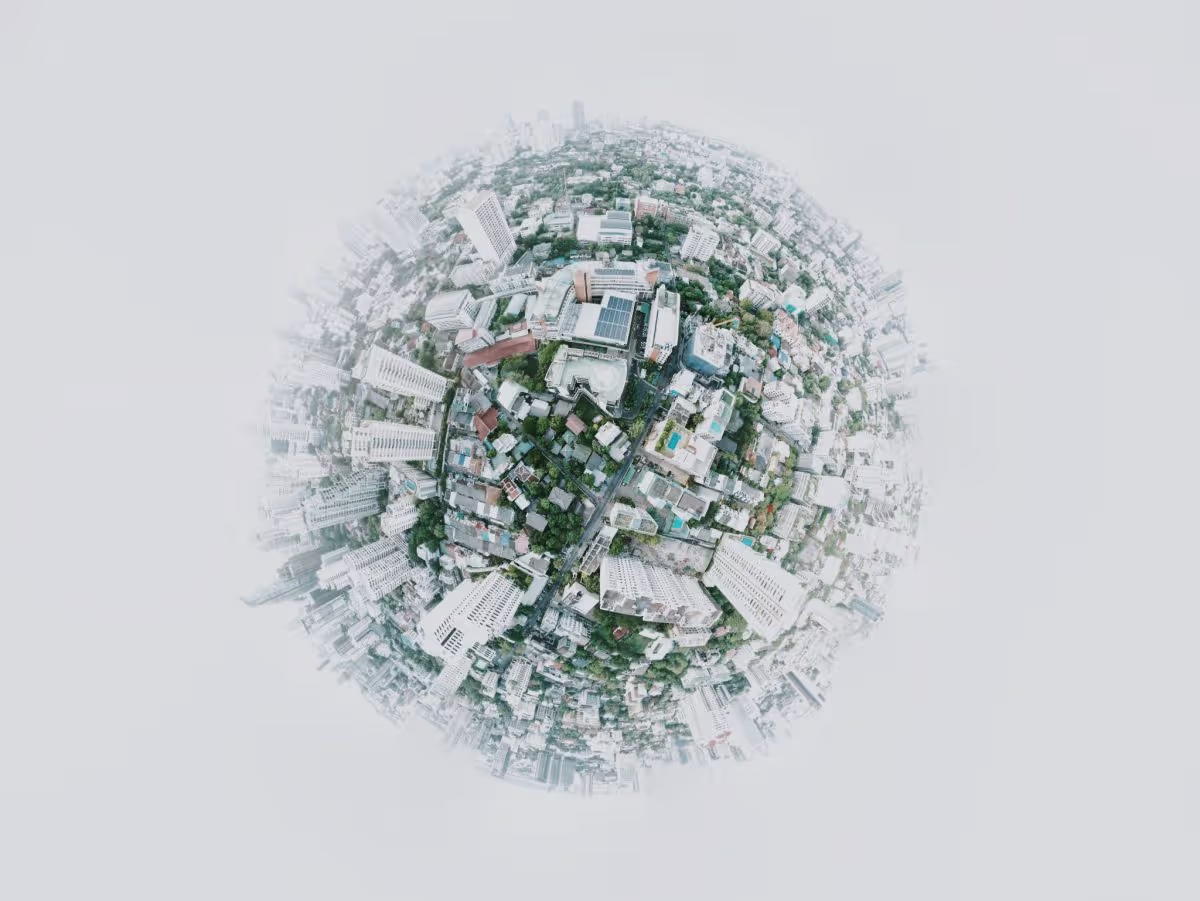
Exploring the solution to a global question
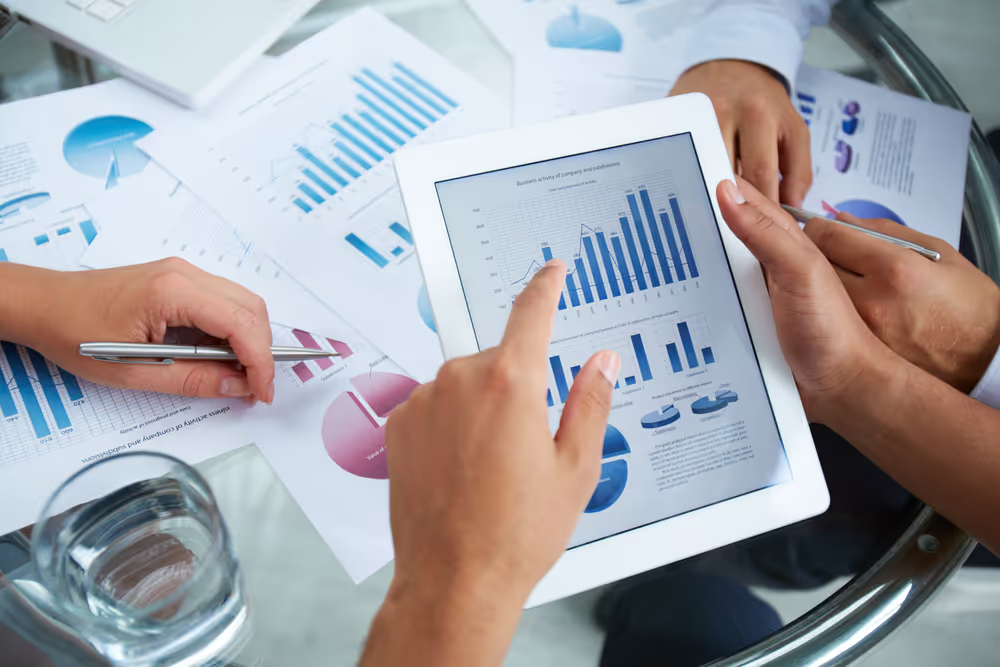
How live access to GxP data support supply chain best practices?
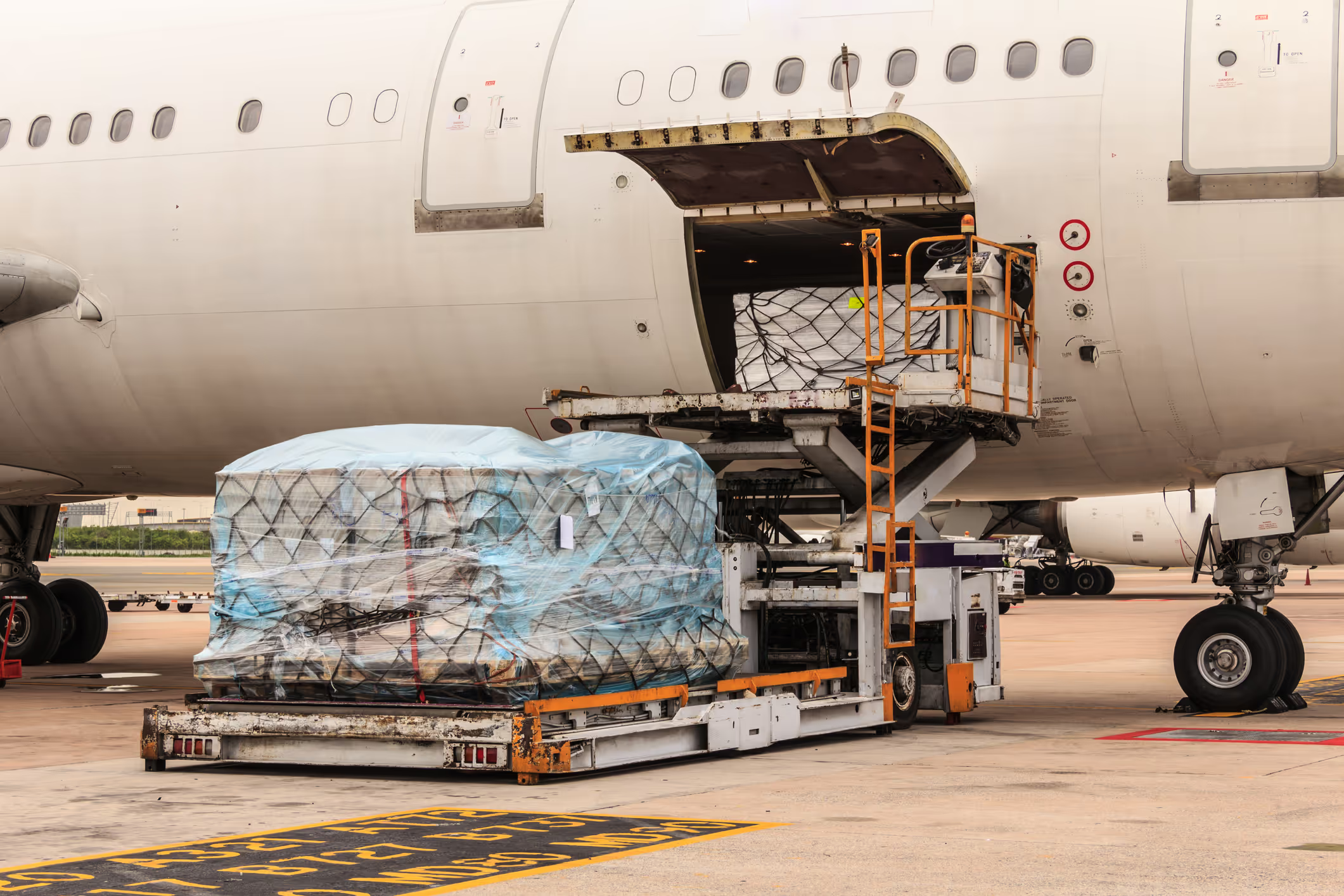
On time and in full, when it matters most
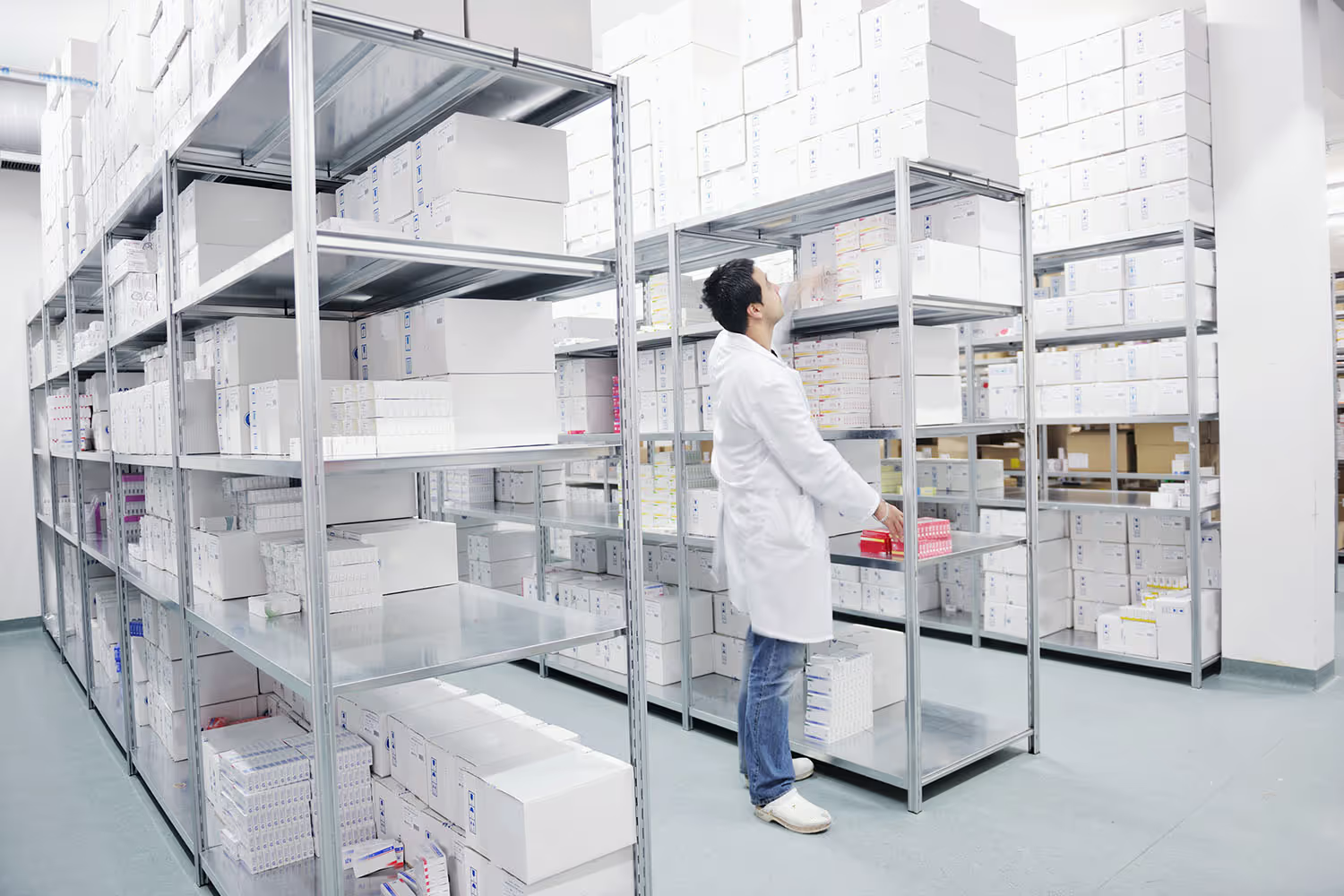
5 benefits of adopting digital temperature monitoring solutions
.avif)
Reducing excursion evaluation time from days to seconds
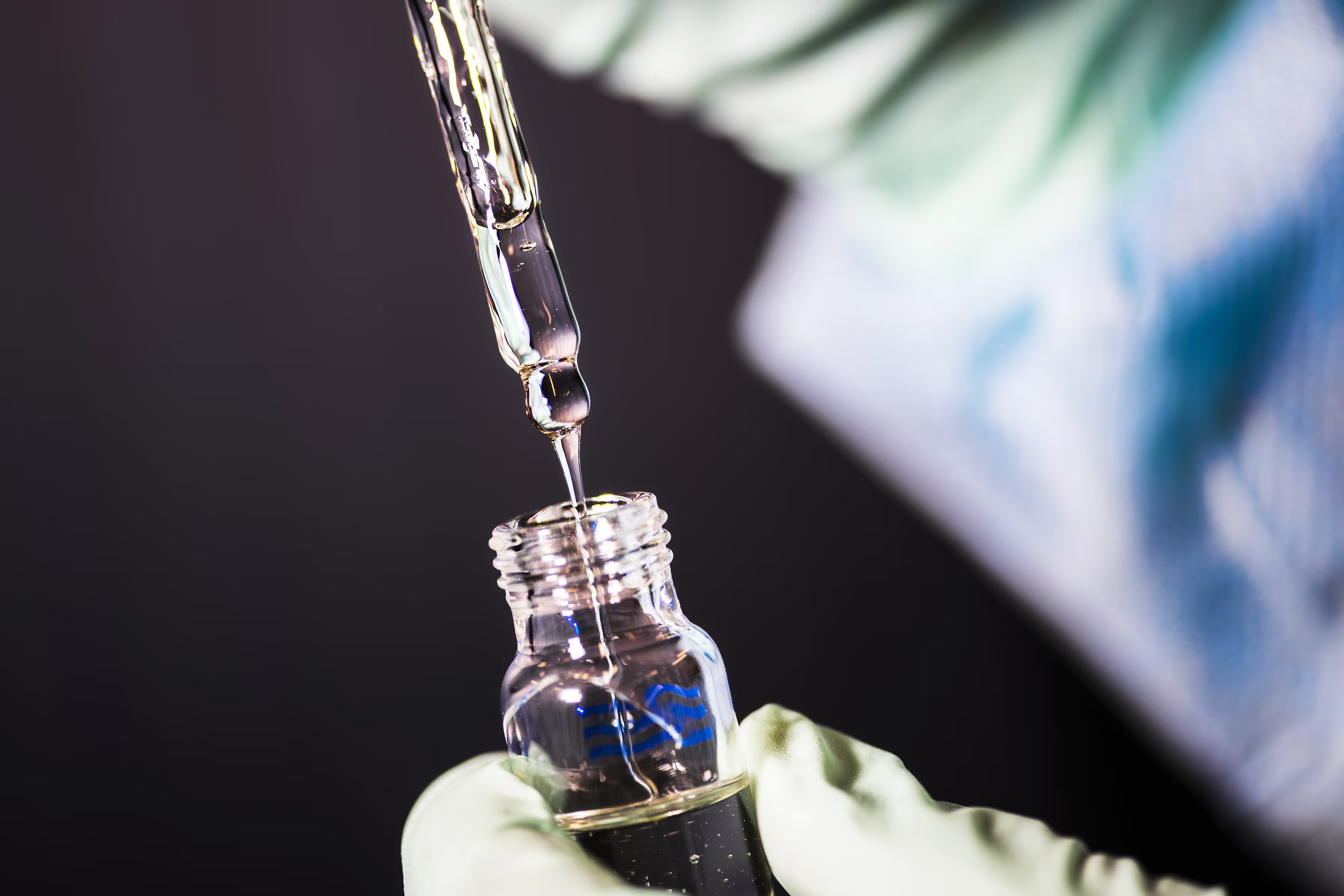
Making the pharma industry future-proof through supply chain digitalization
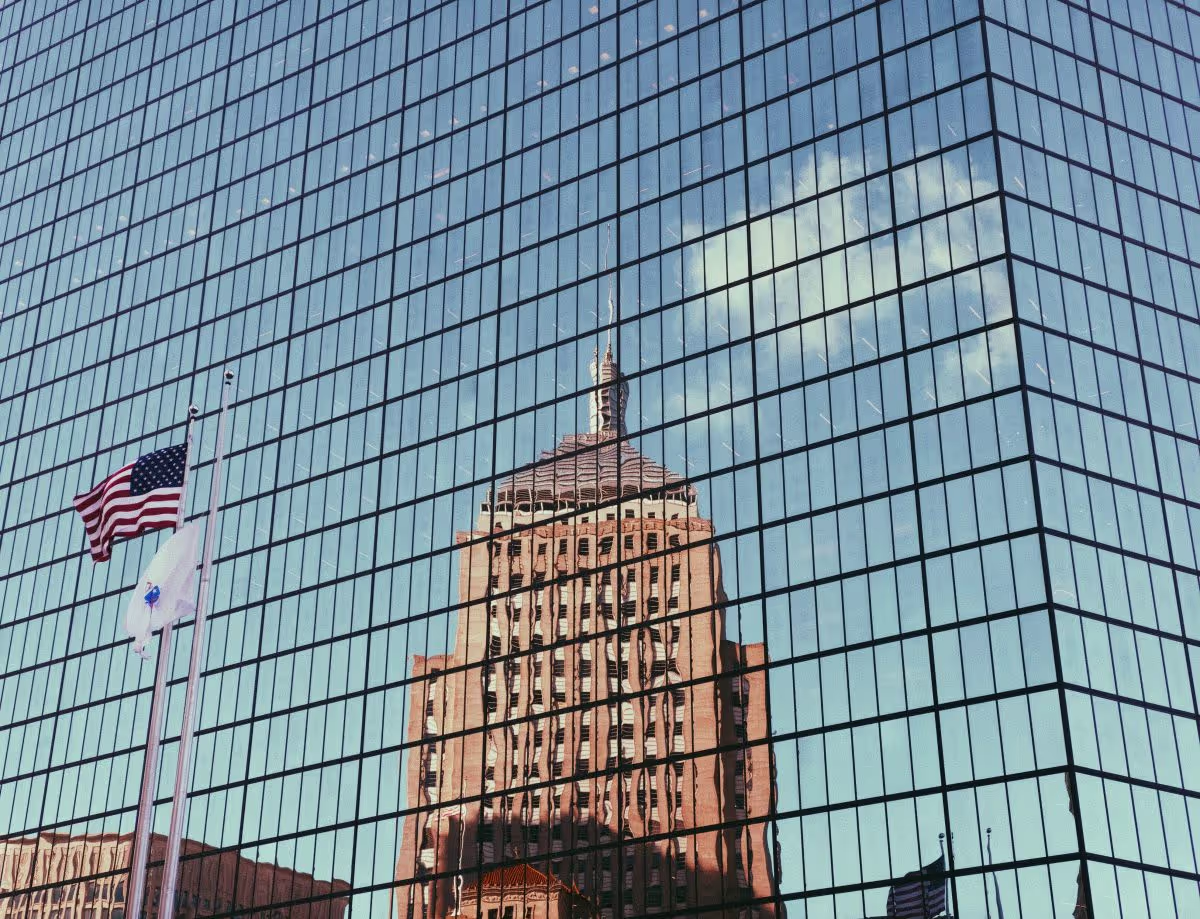
New opportunities on the horizon as TSS expands US operations
.avif)
On-demand webinar: A unified approach to clinical supply temperature management
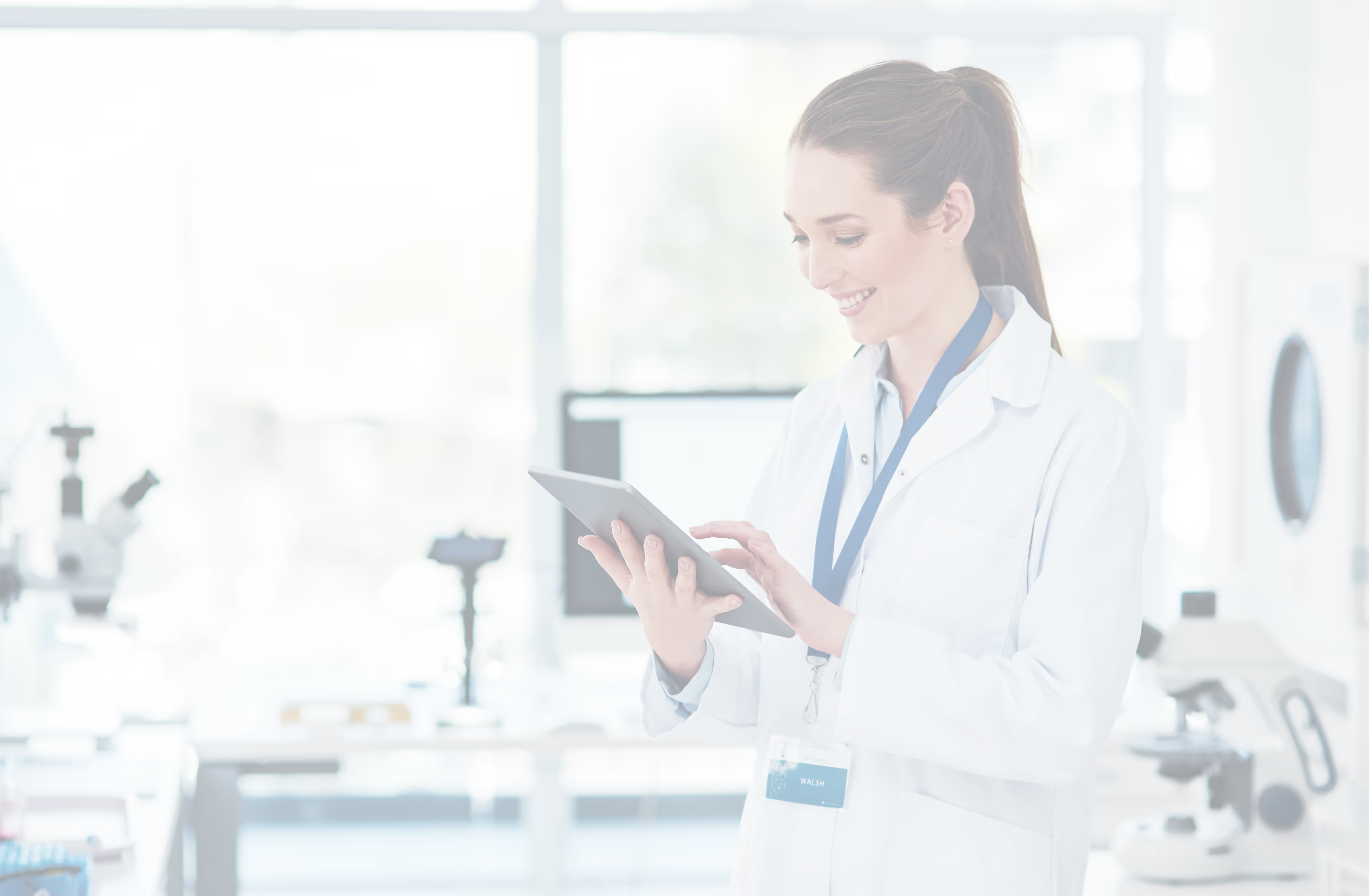
TSS Clinical Trials Digitalization User Forum 2021
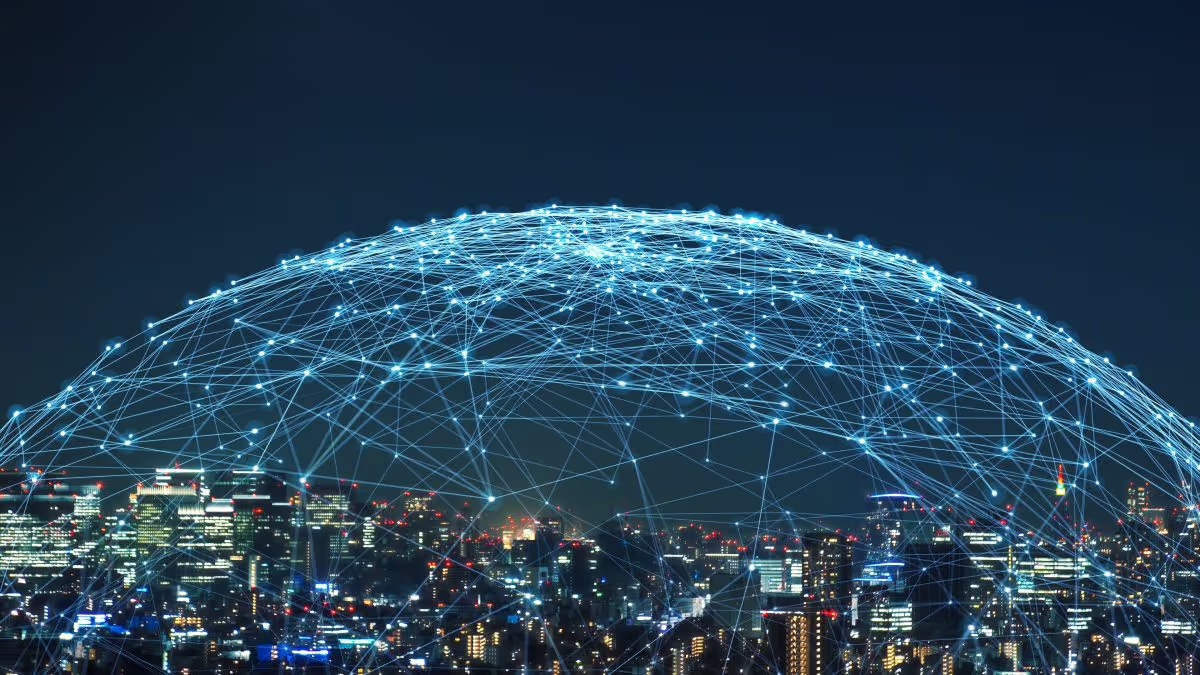
Which way is the wind blowing? The implications of cloud-based IoT on temperature monitoring in the life science supply chain
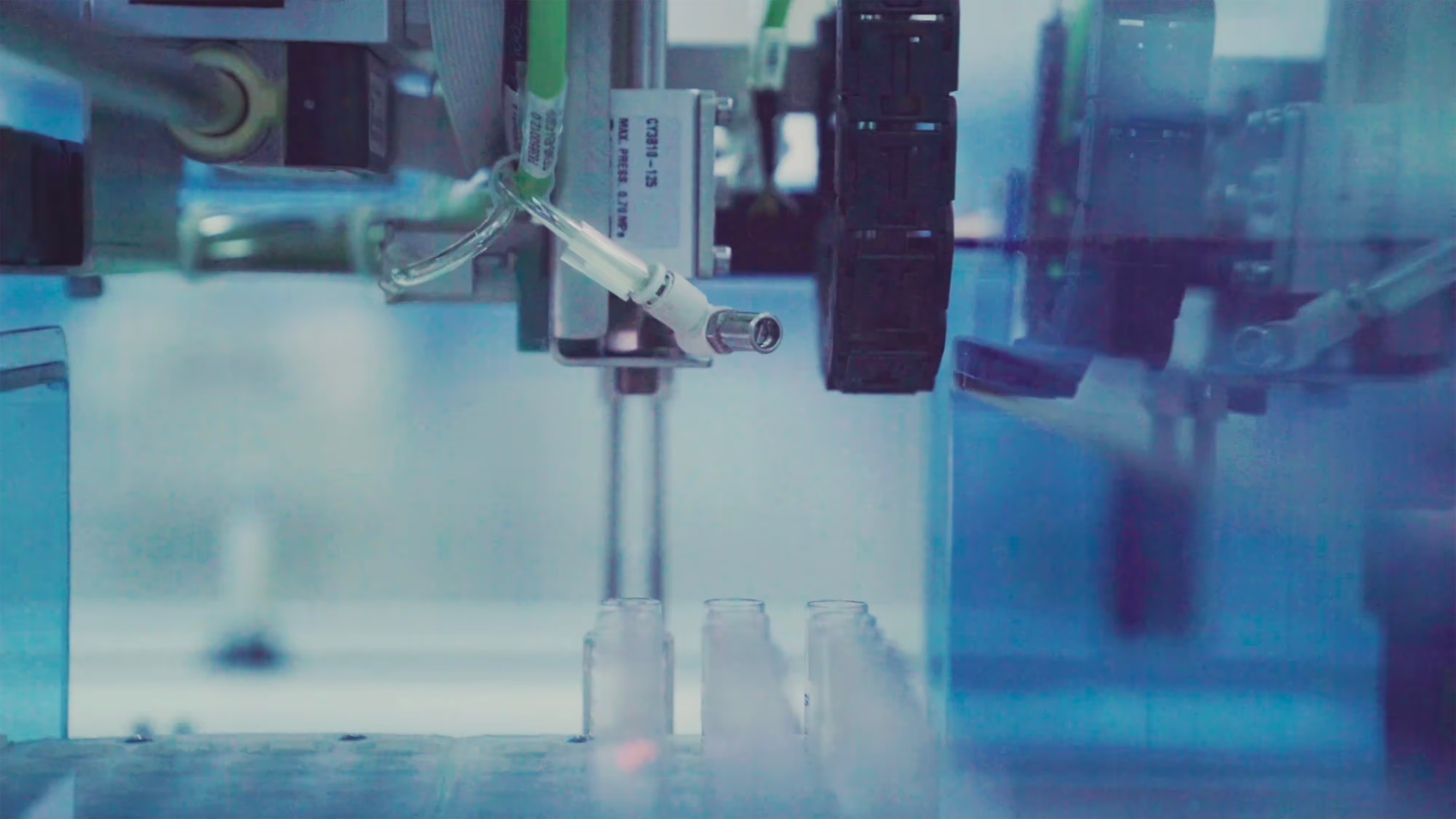
On-demand webinar: Monitoring multiple products with one temperature data logger
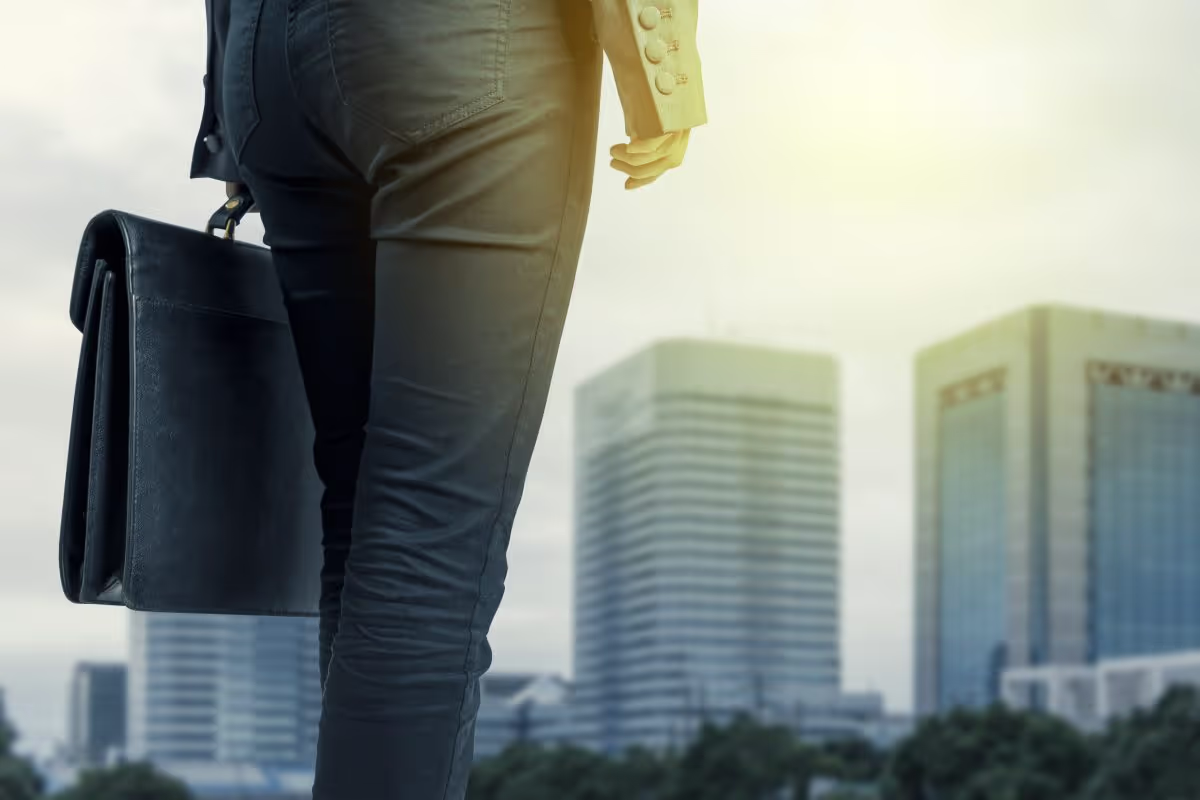
Women in executive positions: making a difference with International Women’s Day
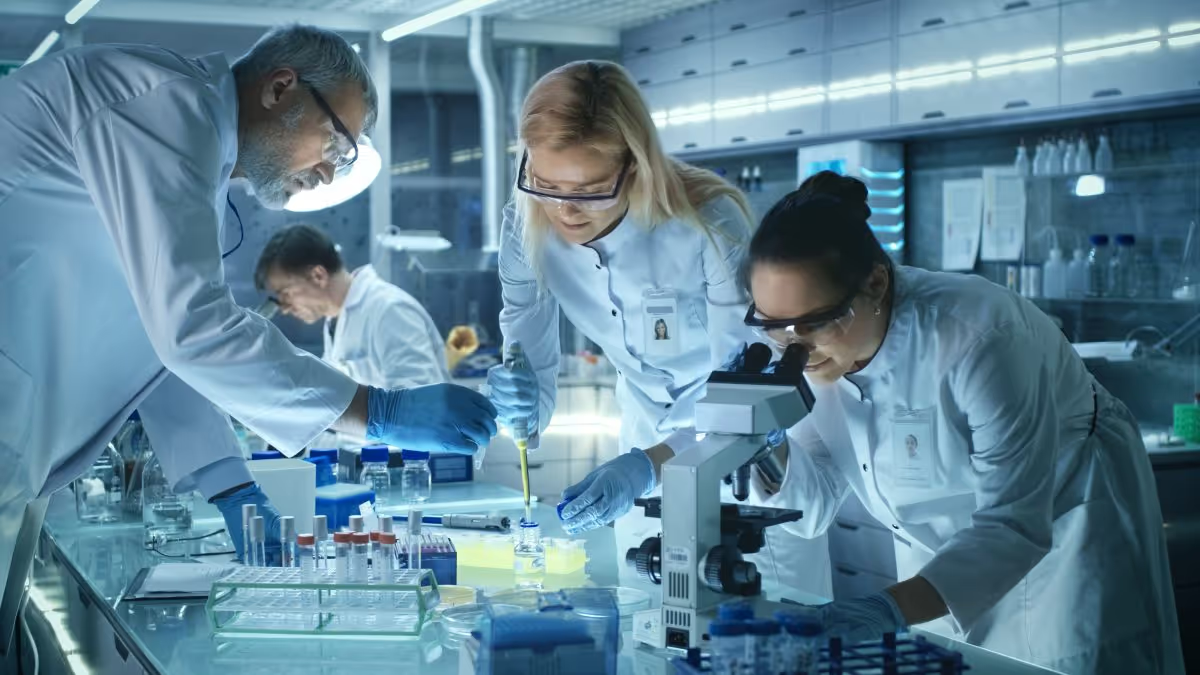
Automation is making temperature excursion management simpler and more efficient for clinical sites
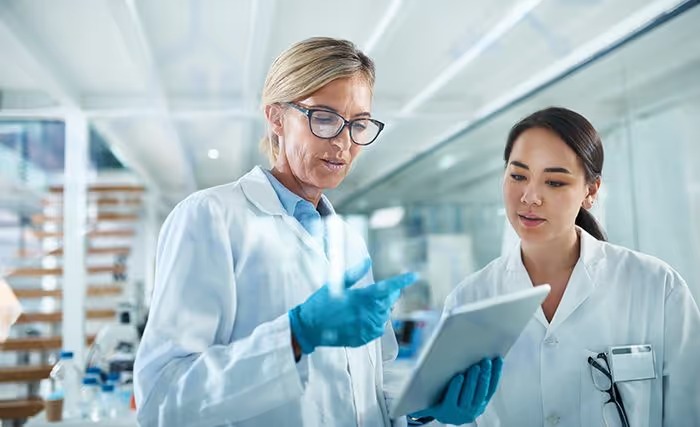
Mind the gap: the real-world impact of data gaps in clinical trials
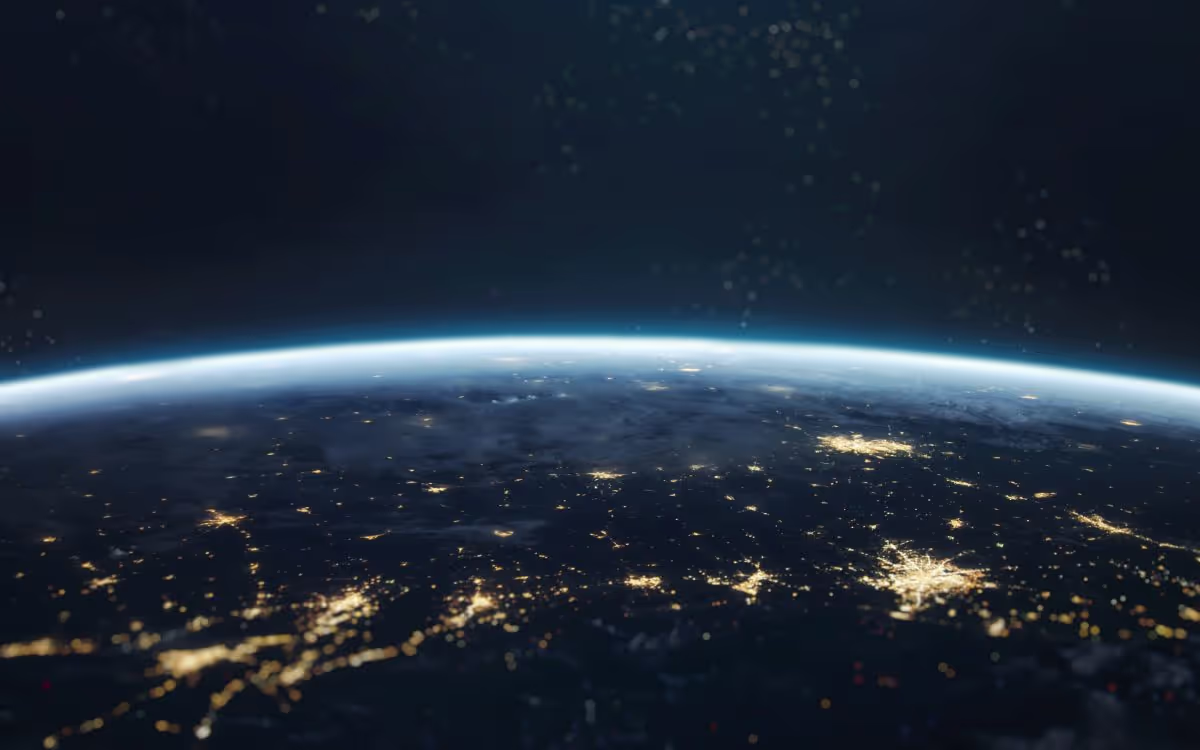
On-demand webinar: Introducing BLE technology for temperature monitoring
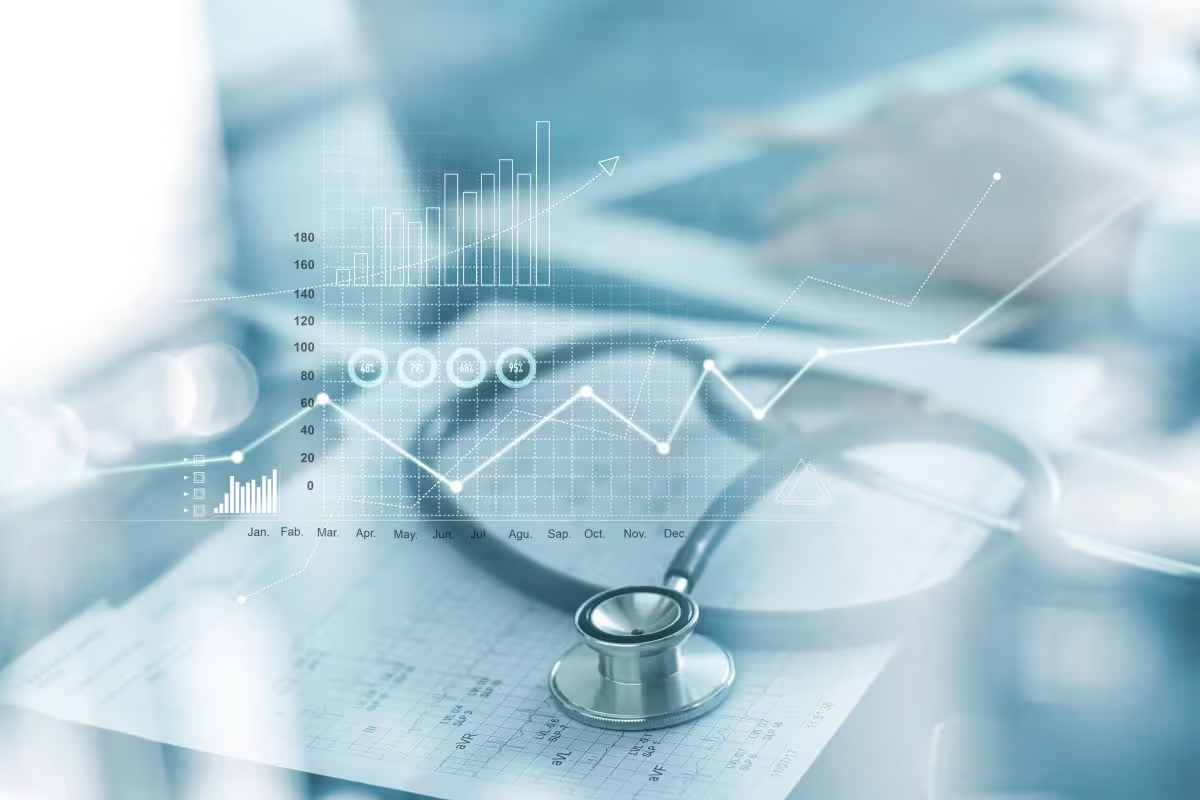
Visibility and automation: reducing disruption due to temperature excursions
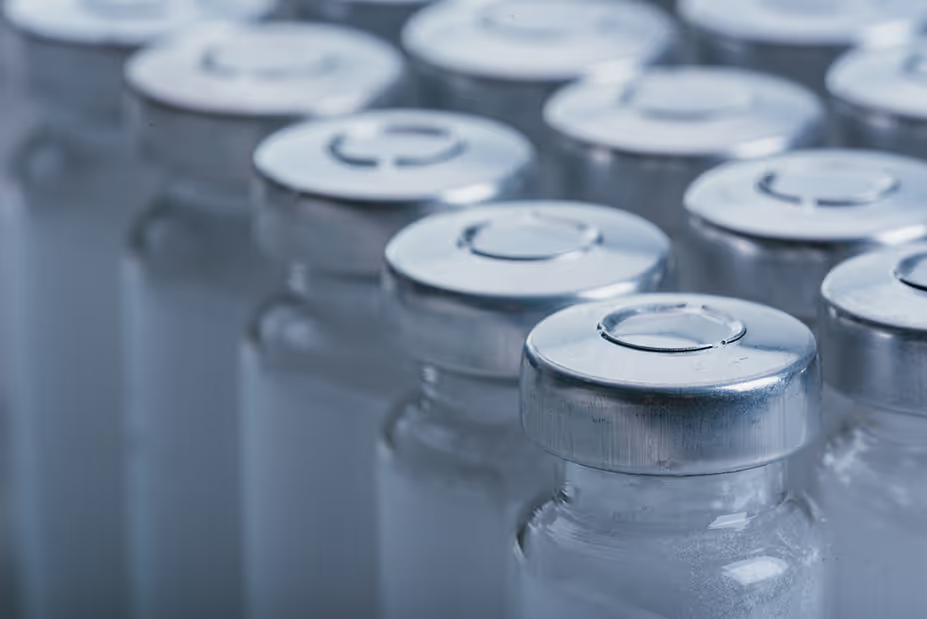
On-demand webinar: Automating the clinical supply chain

Three approaches for automating clinical supply chains
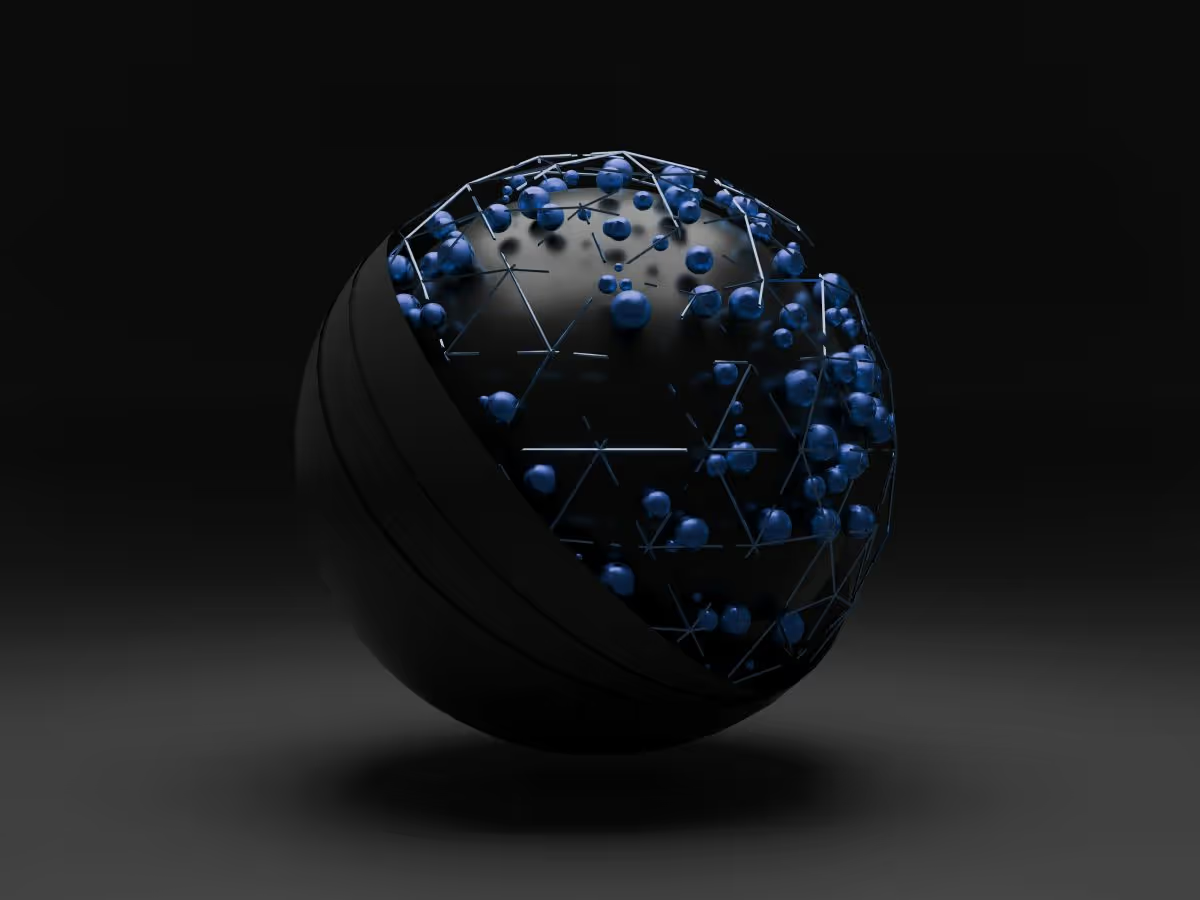
Data-driven supply chains: improving your excursion rate and temperature performance in 5 steps
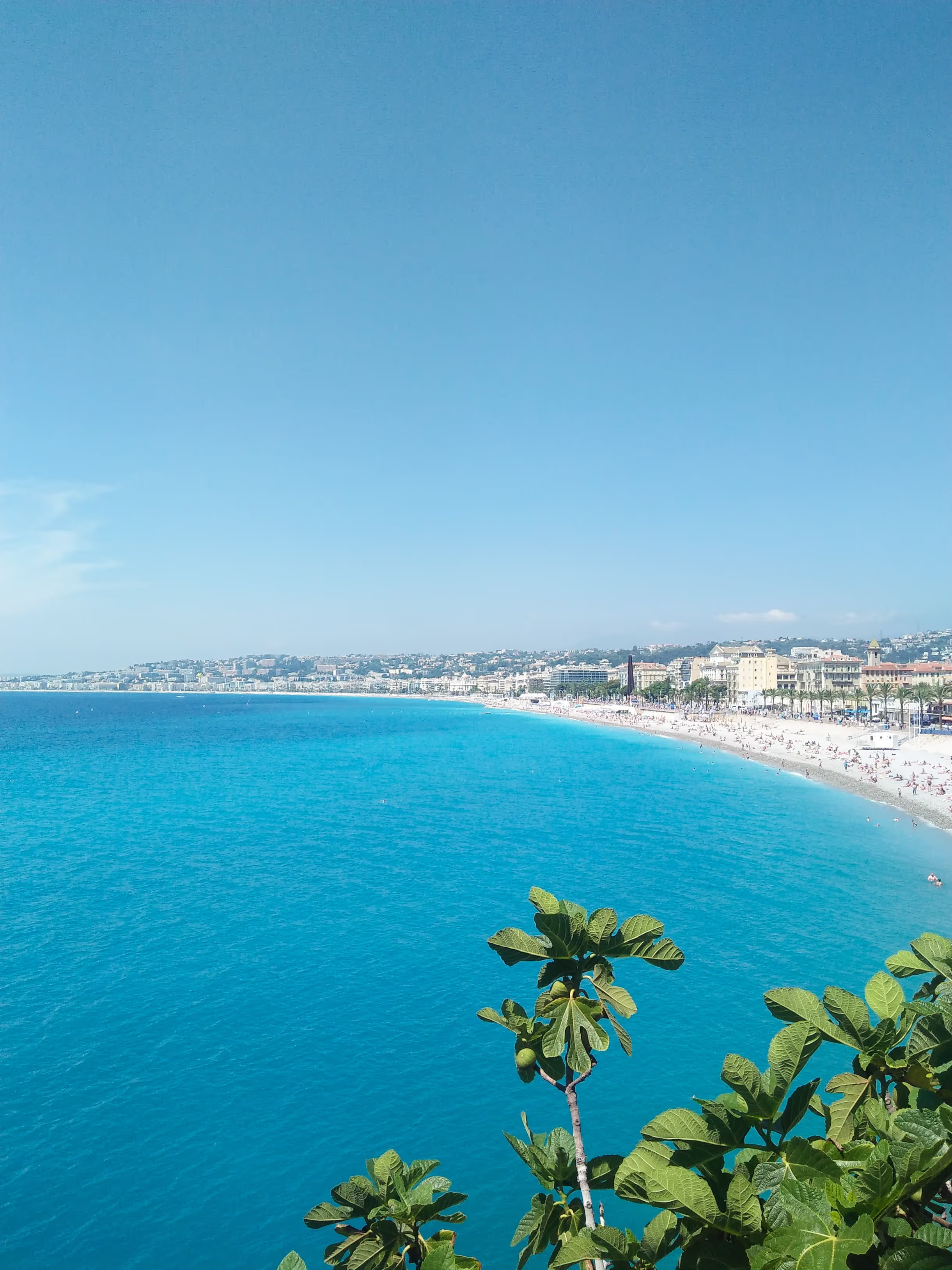
We’re attending LogiPharma 2022
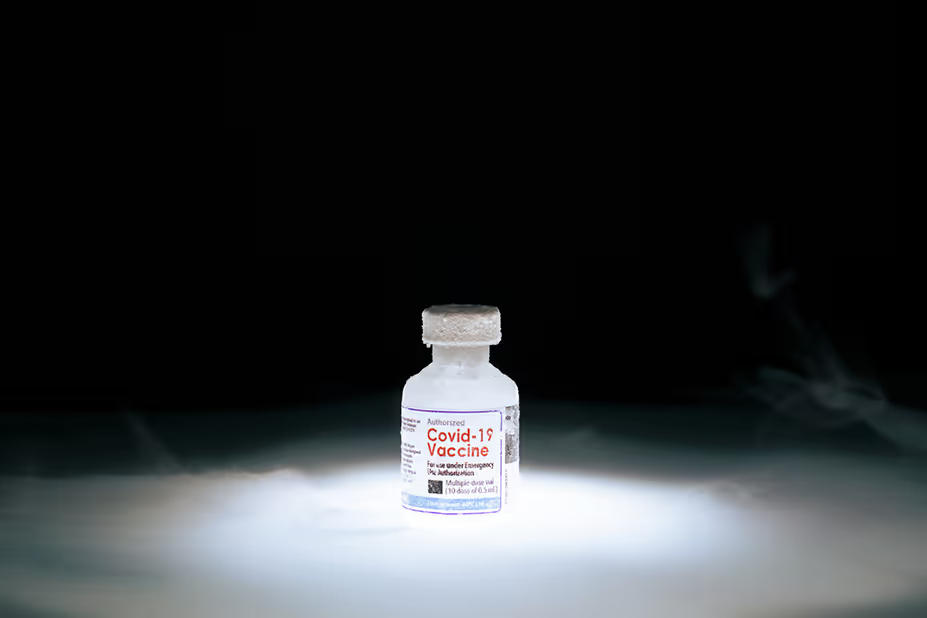
Could automating temperature excursion management hold the key to improving clinical supply processes?
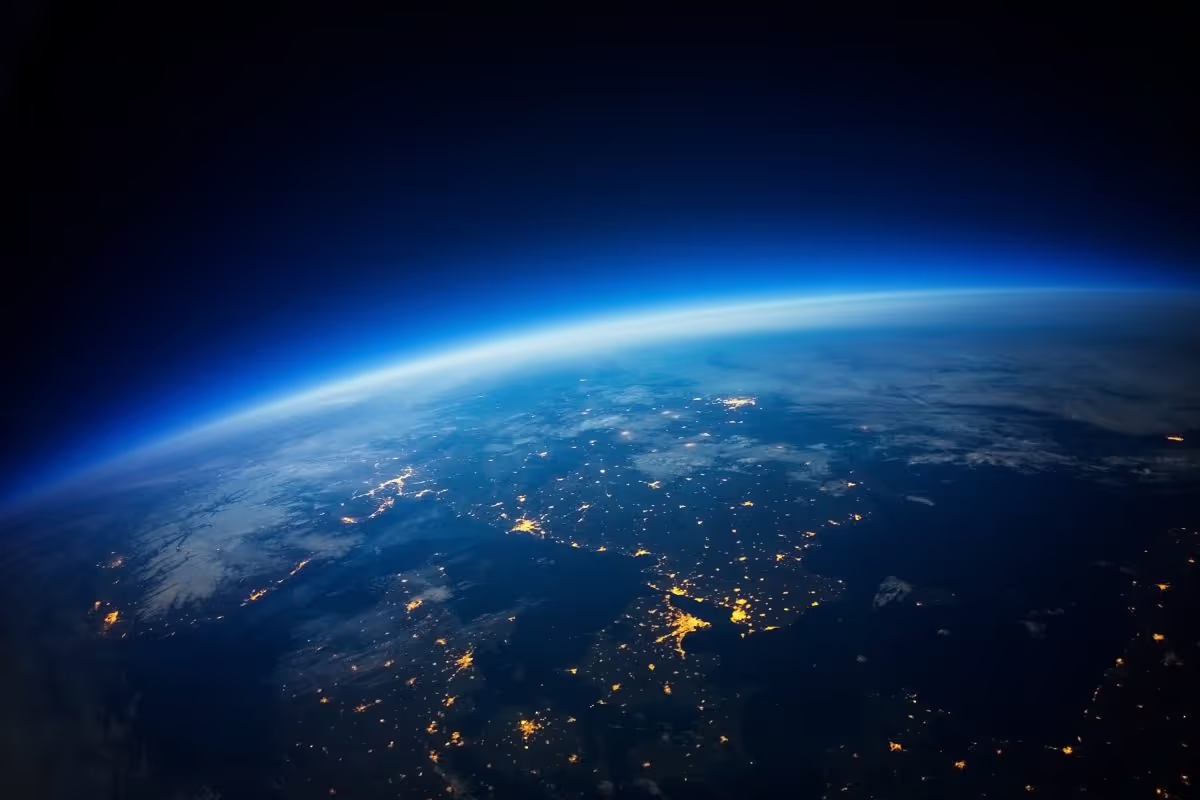
TSS launches innovative Bluetooth powered temperature monitoring solutions
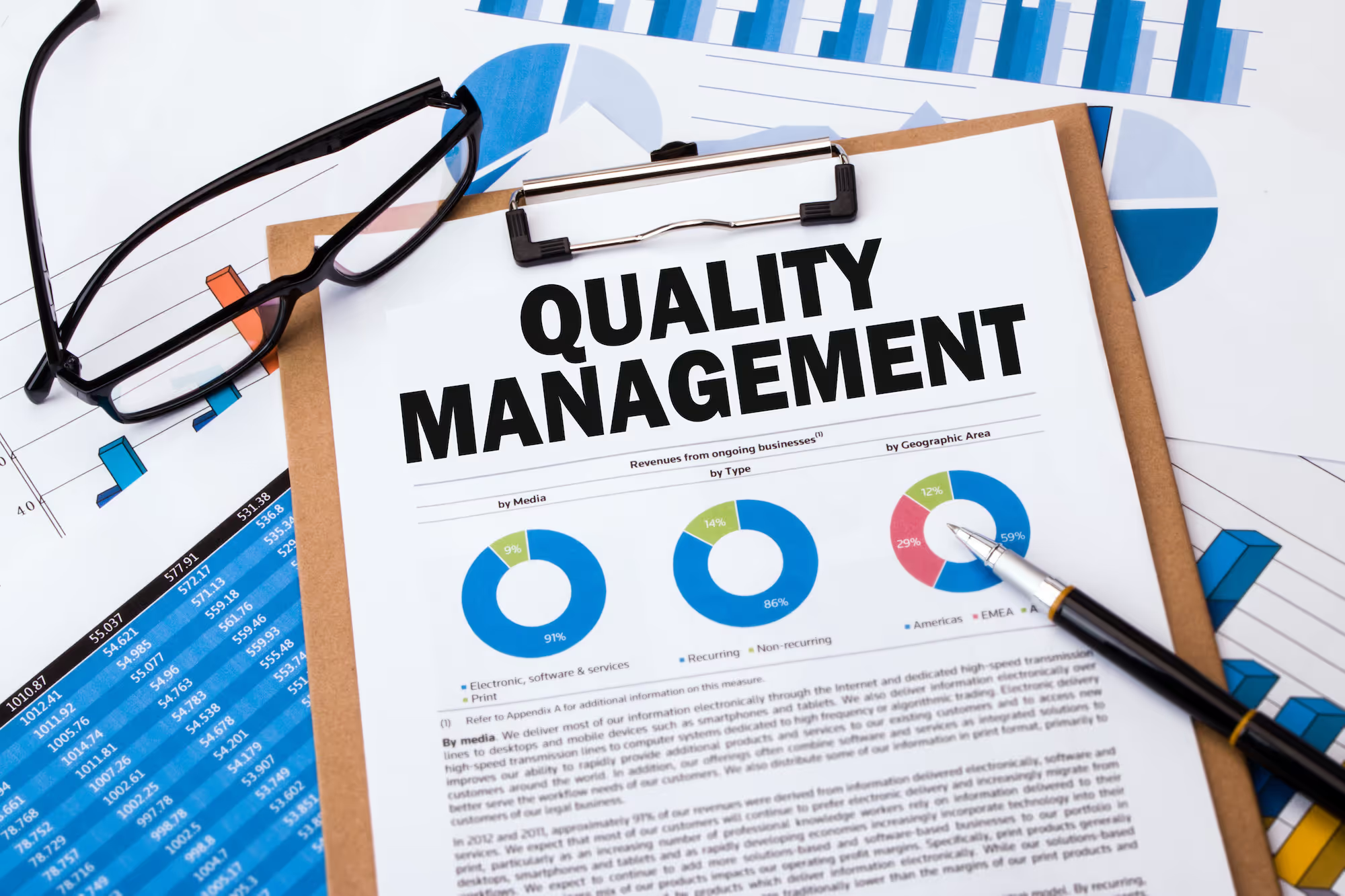
What is Quality?
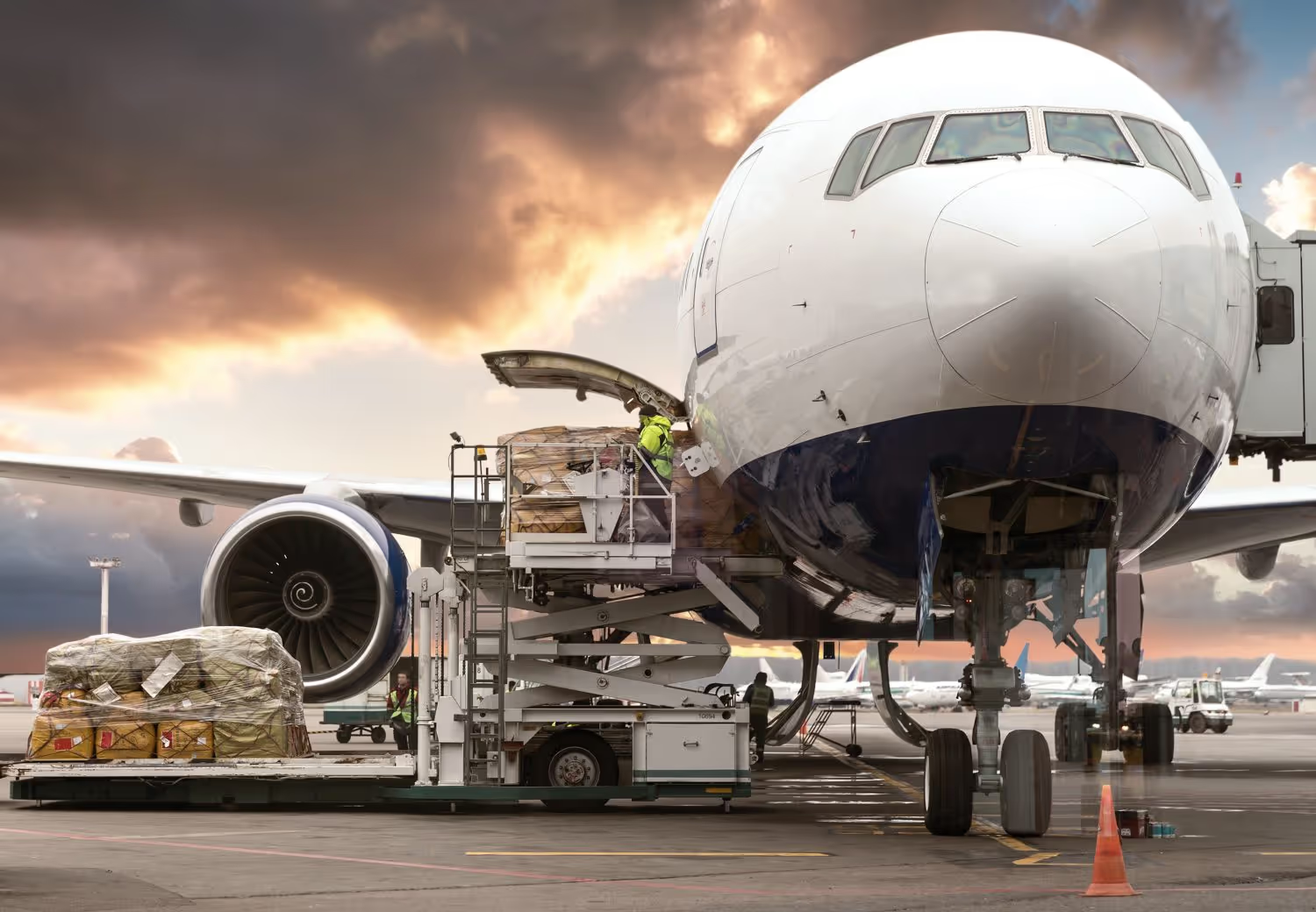